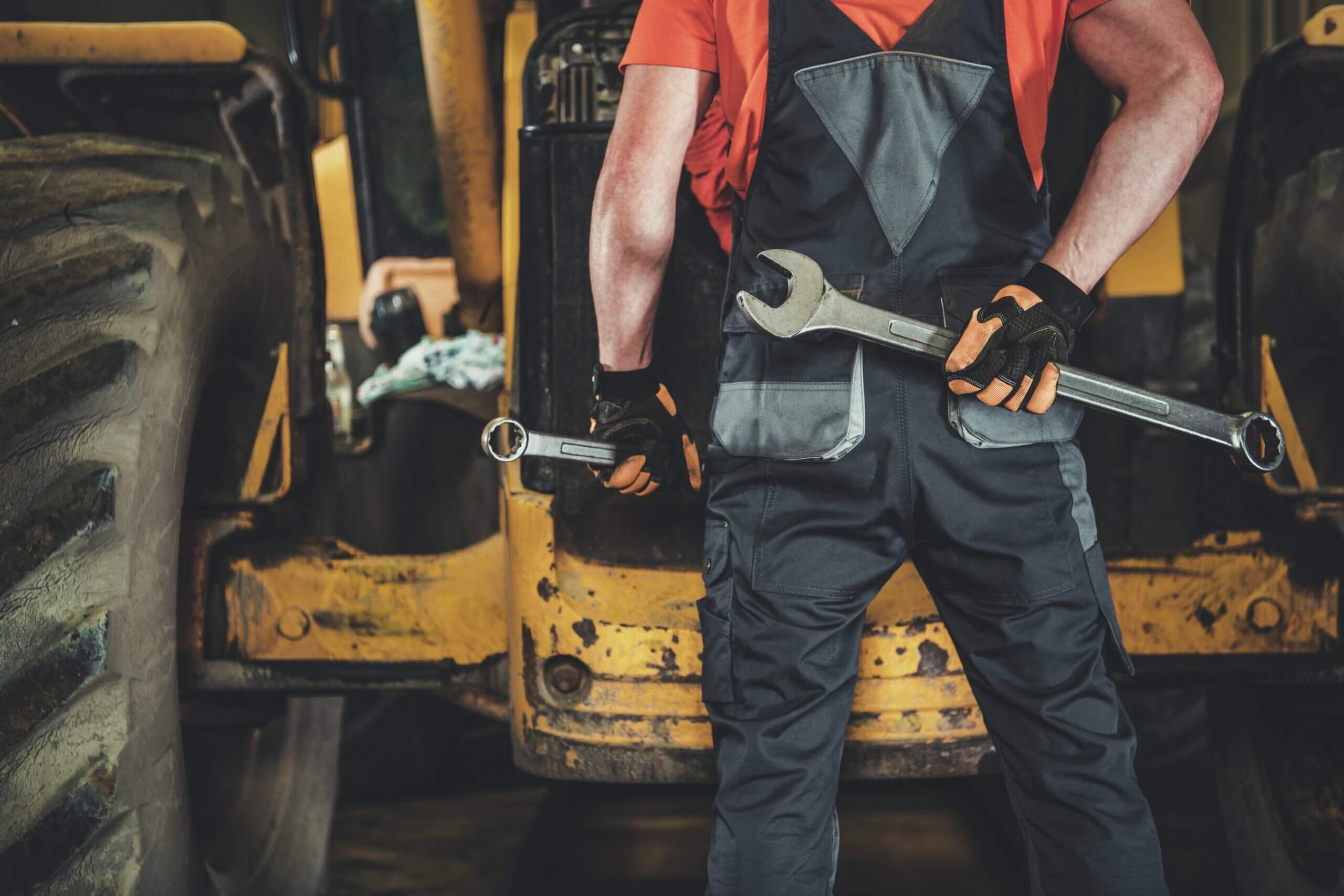
Choosing the right manufacturing maintenance plan is essential to help maintenance teams minimize costly equipment disruptions that halt production with little to no warning. The more highly automated the manufacturing facility, for example, the more critical efficiently preventing, diagnosing, and solving complex asset breakdowns becomes using work order management tools.
What is Manufacturing Maintenance?
Manufacturing maintenance is the process of maintaining and servicing the equipment and machinery used in manufacturing. Proper manufacturing maintenance reduces equipment downtime on assembly lines caused by preventable breakdowns, keeping factory production running efficiently.
Choosing the Right Manufacturing Maintenance Management Plan
Unfortunately, managers, maintenance supervisors, and operators often face several challenges when optimizing manufacturing maintenance programs, including the lack of process knowledge, historical data, time to complete required analyses, and top-management support.
The effective use of maintenance management software can ease these burdens.
What Is Planned Maintenance?
Planned maintenance is a management approach focused on minimizing equipment downtime and returning to uptime as soon as possible after a breakdown. As a basic form of preventive maintenance carried out “according to plan,” planned maintenance involves knowing ahead of time the spare parts, tools, services, and maintenance tasks needed to solve a problem.
Two Categories of Planned Maintenance
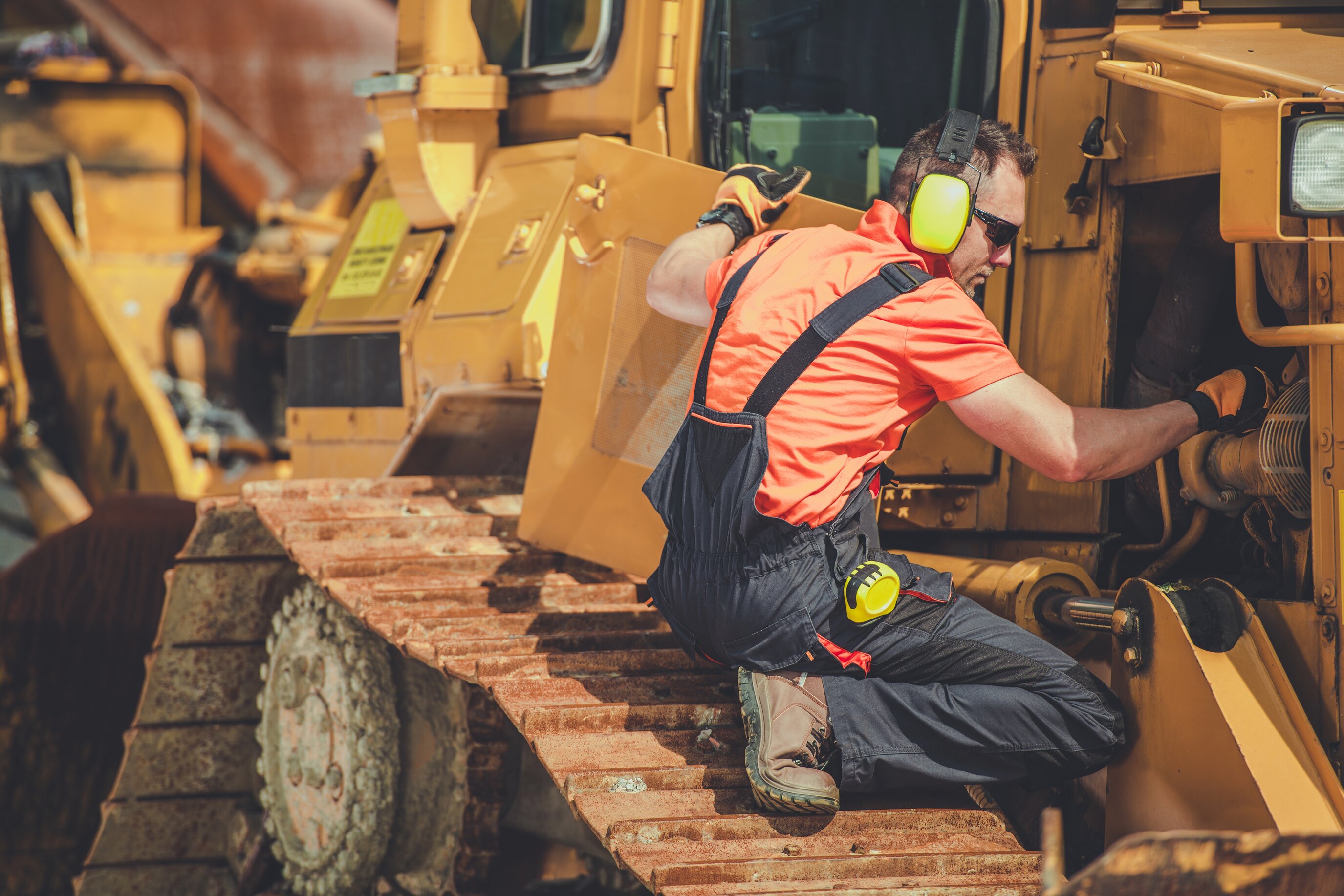
Preventive Maintenance: Planned preventive maintenance puts in place a maintenance schedule that takes care of problems before they occur. For instance, manufacturers often recommend servicing vehicles every 5,000 miles. This scheduled maintenance task helps vehicles run smoothly; forgo car upkeep for too long, and the car may stall at a dangerous or inconvenient time.
Planned Unscheduled Maintenance: This approach entails undertaking manufacturing maintenance activities after a failure has occurred, even though a recovery plan is in place to deal with this eventuality. Once again, the goal is to return the equipment back to operation as soon as possible without jeopardizing safety. In addition, planned unscheduled maintenance helps minimize maintenance costs by avoiding last-minute rush orders for replacement parts. For example, a vehicle owner may purchase a spare battery in the event the current one dies.
What Is Planned Maintenance Optimization (PMO)?
Planned maintenance optimization (PMO) refers to a set of organizational methods used to improve existing maintenance management strategies. PMO analyzes asset failure history and ongoing preventive maintenance (PM) routines to improve outcomes. The analysis involves reviewing existing manufacturing maintenance tasks, eliminating unnecessary work processes, and adding missing assignments to maintenance schedules.
Planned Maintenance Optimization is ideal for organizations that:
- Experience manufacturing equipment downtime, excessive stock inventory, and underutilized workers
- Have yet to perform objective evaluations of PM workloads
- Do not have clearly defined maintenance goals
PMO analysis begins with assessing known asset failures and maintenance tasks that workers are already performing. Organizations then modify existing routines to develop new maintenance schedules and frequencies based on asset failure history. This approach is different from RCM, which analyzes every failure mode on a given piece of equipment.
Phases of Planned Maintenance Optimization
Data Collection: Organizations need reliable high-quality data to begin optimizing their maintenance strategies. They should consistently collect data on equipment performance, especially on asset failure. Tools such as IoT-based meters and computerized maintenance management systems (CMMS) make it easier for organizations to organize accurate equipment data and wear-and-tear statistics and to identify behavioral patterns.
Analysis, Review, and Recommendations: After collecting data for a few months, organizations should take a closer look at the key performance indicators (KPIs) for their most critical assets. Factors that determine how critical assets are to plant operations include Mean Time between Failures (MTBF), Mean Time to Repair (MTTR), and the average cost of asset repair. Next, compare this information to existing PM routines to align with MTBF and MTTR data points. This review will determine if the failure points fall within acceptable tolerances set by manufacturing industry standards and equipment manufacturers. Substantial deviations indicate a need for improvement. Operational managers can recommend modifying existing PM tasks. The review should lead to optimizing maintenance schedules and frequencies and to addressing inefficient or missing maintenance activities.
Commitment to Implementing Data-Backed Improvements: Managers should delegate recommended adjustments to manufacturing maintenance technicians who can appropriately perform tasks. Workers should continually monitor the progress of required actions.
Maintenance programs become optimized through their consistent commitment to data collection and analysis and by readjusting programs accordingly over time.
How to Optimize a Planned Maintenance Program
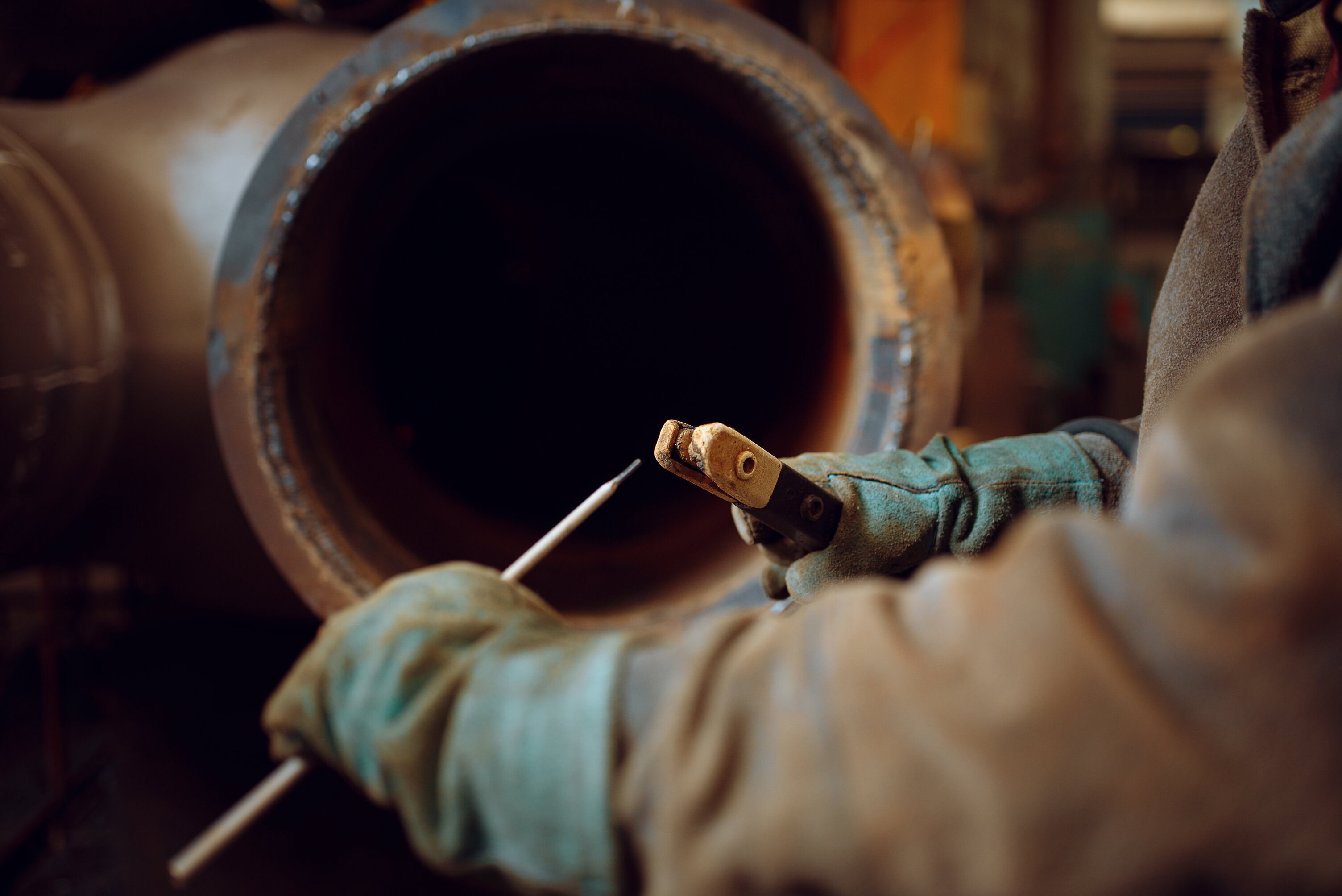
Generally, organizations take one of two initial approaches to maintenance management optimization:
1. Seek feedback from technicians responsible for performing maintenance tasks: While this approach is logical—these workers interact with pieces of equipment day in and day out—it does not provide reliable and consistent information. In addition, personal bias and forgetfulness sometimes skew qualitative data. Therefore, we recommend the second approach.
2. Use the 6:1 Rule: This more objective approach dictates that organizations find a corrective maintenance task in every six PM tasks performed. This method provides organizations with a starting point to fine-tune preventive maintenance processes and programs.
With either approach, we recommend analyzing existing PM tasks periodically to optimize their frequency, priority, and quality continually.
Planned maintenance optimization (PMO) is the first step on the journey to continuous manufacturing maintenance departmental improvements. PMO frees resources, minimizes reactive maintenance, and creates more organized asset management systems leading to better decision-making. However, PMO processes do not occur overnight. Effective implementation takes time, resources, and user-friendly CMMS software.
What Is Corrective Maintenance?
We can divide corrective maintenance management into two parent classes: Unscheduled (immediate) corrective maintenance and planned (deferred) corrective maintenance:
- Unscheduled Corrective Maintenance refers to repair actions taken immediately after an asset fails. These failures are critical and need corrective action immediately.
- Planned Corrective Maintenance refers to needed repairs that you can defer to a later date. Deferrals can be due to a limited budget, time, or staff. In addition, the repairs may require more advanced technical maintenance, which the company may need to outsource.
From here, planned corrective maintenance is sometimes broken down into two groups:
- Run-to-Failure Maintenance: In this case, an asset is permitted to run until it breaks down, at which point it is repaired or replaced. This strategy is only suitable for redundant systems and non-critical assets that are easily repairable and replaceable.
- Preventive Maintenance (as part of Condition-Based Maintenance): Equipment problems are identified during preventive and condition-based maintenance inspections.
Corrective maintenance requires companies to invest in sufficient labor and resources to handle equipment problems when they arise. Organizations can avoid significant unplanned downtimes—and extend asset life spans—by pairing unplanned and planned repair actions with realistic preventive maintenance programs.
What Is Breakdown Maintenance?
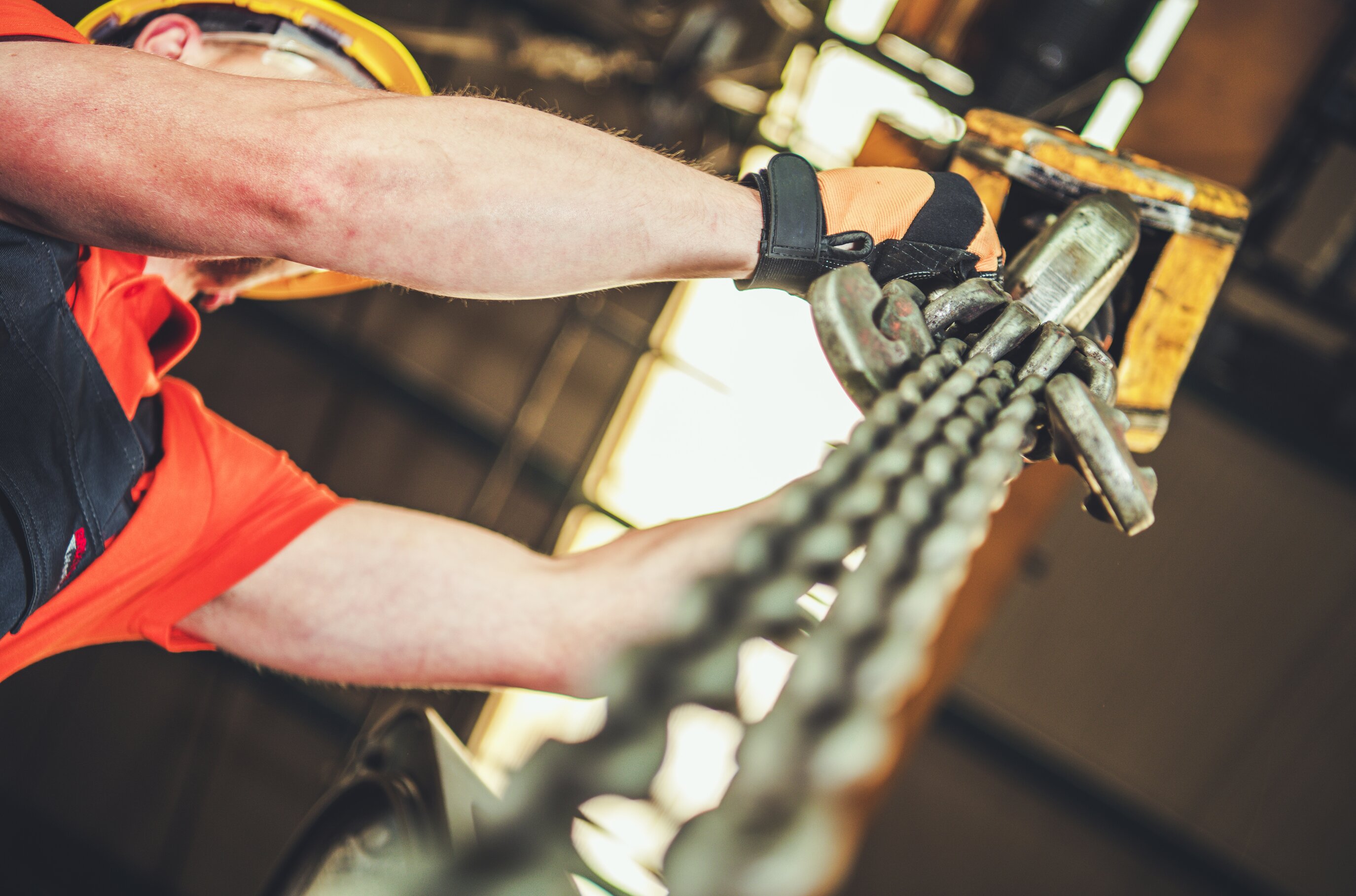
Breakdown maintenance management is the continuous use of a part, machine, unit, or device until it breaks down and needs to be repaired or replaced. It is often referred to as reactive or corrective maintenance.
Because breakdown maintenance is not scheduled in advance, companies need to be able to redirect resources toward repairs every time a piece of equipment breaks down. Ideally, when breakdown maintenance is necessary, manufacturing maintenance systems should be able to remedy the situation without coming to a complete halt. Of course, there is never a convenient time for downtime. Fixing inconvenient equipment malfunctions is an inevitable part of asset management. However, breakdown maintenance can and should be minimized through strategic planning.
Types of Breakdown Maintenance
The key to managing an effective breakdown maintenance strategy is implementing efficient stock and inventory management procedures. In addition, management teams need to monitor asset manufacturer’s guidelines and parts inventories, and backlog history to determine which equipment parts should always be in stock for emergencies. The two main types of breakdown maintenance include:
Run-to-Failure Maintenance
This type of maintenance refers to equipment failure that is expected to happen. Run-to-failure maintenance means an organization is prepared for a machine to stop working at some point in the near future. Assets ideal for run-to-failure maintenance include those that are:
- Easy to replace and
- Do not jeopardize operational systems or personal safety.
In such instances, the cost of repairing the asset “on the fly” is less than the associated costs of preventive maintenance. Therefore, run-to-failure maintenance should be reserved for inexpensive or unimportant parts and machinery.
Emergency Maintenance
Teams conduct emergency maintenance when an essential piece of equipment stops working unexpectedly and we need to replace it immediately.
We tend to associate emergency breakdowns with expensive costs, financial losses, and safety hazards. In addition, because we must conduct these equipment repairs ASAP, companies tend to overspend on the expedited shipping of needed parts, outsourced technician assistance, and overtime costs.
What Are Maintenance Standards?
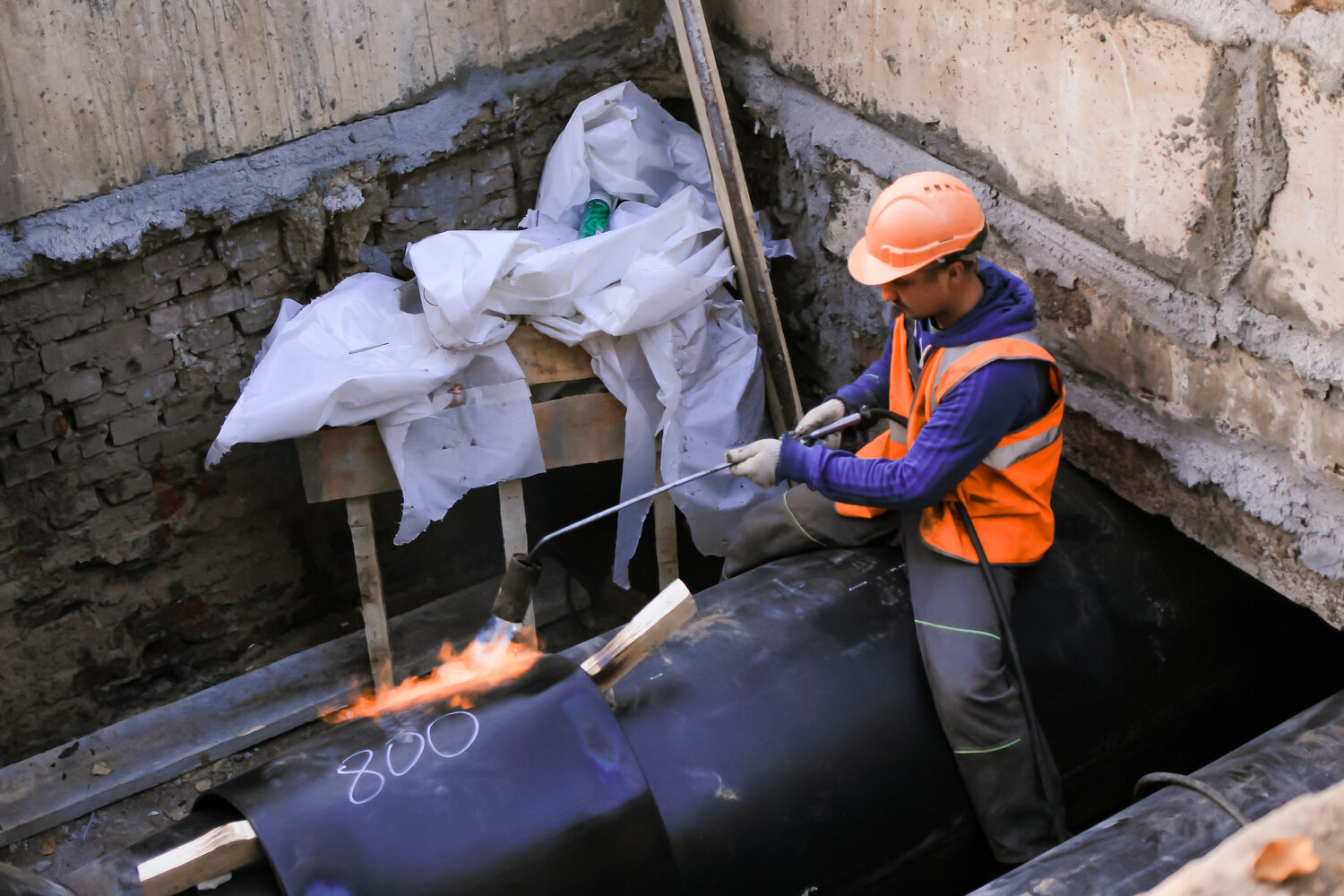
Maintenance standards are established criteria for performing maintenance tasks such as cleaning, repairs, parts replacement, lubrication, and maintenance data collection. Stakeholders in the maintenance industry establish standards for various reasons, including reduced safety risks, increased asset reliability, and enhanced efficiency.
Companies of all sizes establish their own internal standard operating procedures (SOPs) to ensure smooth operations and maintenance. Additionally, industry institutions, such as the International Organization for Standardization (ISO), publish official industrial maintenance standards as recommended best practices. Maintenance departments use these standards as guidelines to develop, implement, and correct maintenance team strategies.
The implementation of maintenance management standards takes into account:
- Organizational operating plans and budgets
- Environmental laws, OSHA mandates, and other regulatory requirements
- Terms and conditions of facility and asset insurance policies
- Terms and conditions of operations and maintenance agreements
The maintenance industry depends on standards to maintain safe, efficient, and reliable operations. The above list of standards is not exhaustive but does include the most commonly used standards. Keep in mind, however, that maintenance standards are constantly evolving. As organizational maintenance needs and data mediums change, teams must continually adapt their approaches. Such flexibility enables maintenance departments to determine which standards are most applicable to their unique needs.
What Is Maintenance Management?
Unplanned downtime negatively affects organizations in many different ways, including unexpected repair costs (e.g., employee overtime, spare parts, and outsourced specialists), delayed shipments, customer dissatisfaction, and lost revenue. However, we also frequently associate maintenance management with a range of difficulties.
We define maintenance management as prioritizing, strategizing, and delegating maintenance-related objectives with the goal of maintaining company assets. It involves tracking, controlling, and maximizing equipment lifespans to increase organizational profitability, increase efficiency, and reduce downtime.
Maintenance Management vs. Enterprise Asset Management
We often use the terms maintenance management and enterprise asset management (EAM) interchangeably. However, there are key differences.
Maintenance management is a holistic approach to managing facility operations. Manufacturing maintenance covers asset and equipment maintenance and encompasses labor, parts inventory, and safety procedures.
Asset management primarily focuses on optimizing asset performance relative to output. Asset management programs monitor equipment efficiencies and the asset lifecycle to facilitate capital decisions and provide depreciation estimates to accounting teams. While some asset management systems incorporate maintenance schedules, they do not do great with work orders. As a result, they tend to be more dependent on an administrator to manage the data entry.
What Are Maintenance Strategies?
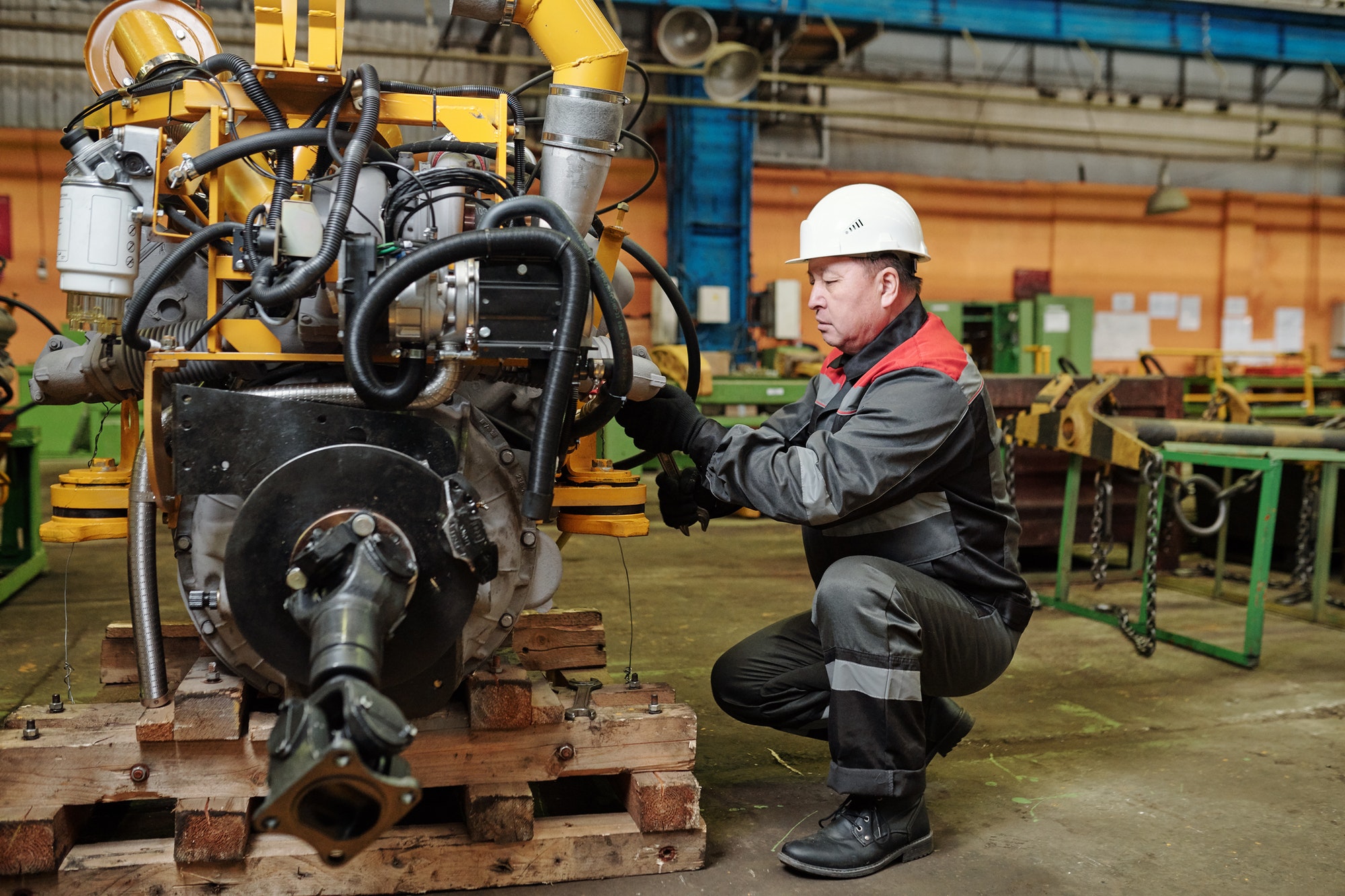
A maintenance strategy is a systematic approach that companies use to maintain their assets in prime working condition. It involves maintenance checks, data analysis—for example, KPIs and metrics, failure rates, performance, and costs—and the repair or replacement of faulty equipment. High-level manufacturing plant maintenance programs typically mix several different maintenance strategies based on the needs of individual equipment.
An effective maintenance strategy:
- Reduces downtime and guarantees high equipment availability
- Keeps maintenance and operational costs low and predictable
- Optimizes facility performance and production line processes
- Maintains a high level of safety
- Improves customer satisfaction
- Extends equipment life
To choose the right maintenance strategy, you will need to assess existing organizational data, such as asset performance/criticality, uptime/availability, maintenance costs, and failure rates. Once you have “the big picture” of your organization’s current maintenance and operational structure, we recommend reviewing the types of maintenance strategies before conducting a criticality analysis.
Maintenance Management Software
Use a Computerized Maintenance Management System (CMMS) to track your progress, analyze KPIs, and generate meaningful data reports. SaaS products offer different CMMS features and customization that vary based on the company and pricing plan. Benchmark data on your facility’s performance before changing strategies. Your most useful KPIs will most likely be:
- Equipment Performance
- Mean Time between Failure (MTBF)
- Mean Time to Repair (MTTR)
- Maintenance Costs
- Maintenance Program Used
Benchmark data for both individual assets and collective asset holdings. This preliminary work will enable you to draw meaningful conclusions from your new KPIs post-launch. Review your strategy’s performance frequently and prioritize realistic improvements achievable in the short to medium term.
CMMS maintenance solutions are a cost-efficient and easy way to streamline your operations and improve maintenance efficiency. CMMS help companies:
- Shift from reactive to proactive maintenance
- Optimize maintenance schedules
- Handle both recurring tasks and urgent issues on time
- Reduce maintenance costs and supply-chain lag time
- Improve the visibility of immediate, mid-term, and long-term maintenance needs
MaintainX and Maintenance Management
MaintainX is one of the top-rated maintenance management software solutions on the market. This modern CMMS boasts robust maintenance management functionality with real-time chat functionality, a world-class global procedures library, and excellent support.
User-friendly maintenance management software can make the difference between constantly running behind schedule and fixing urgent issues, and making the most out of your maintenance resources in the most efficient way possible.
The right maintenance strategy will be different for each business and for each asset. There is no one-size-fits-all solution. Choosing user-friendly software makes maintenance care much easier for everyone involved. We invite you to check out MaintainX today. If our reviews are any indication, you will not be disappointed.
FAQs
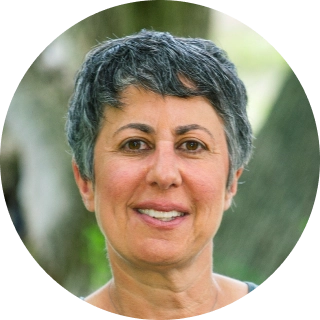
Caroline Eisner is a writer and editor with experience across the profit and nonprofit sectors, government, education, and financial organizations. She has held leadership positions in K16 institutions and has led large-scale digital projects, interactive websites, and a business writing consultancy.