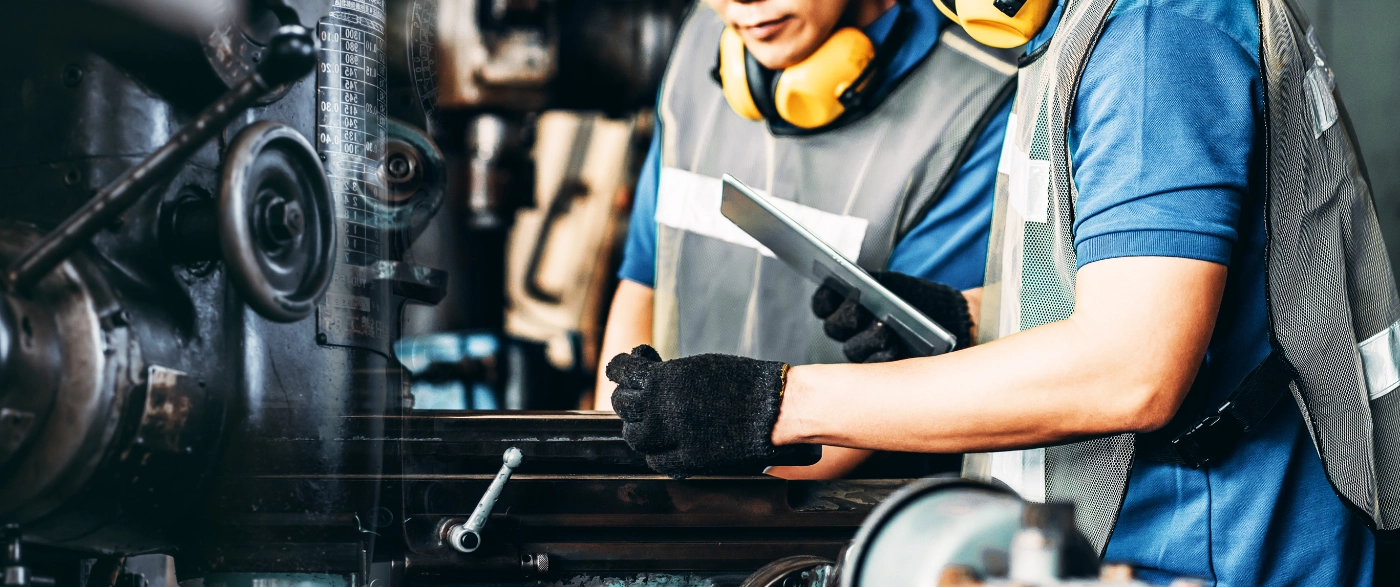
When it comes to equipment maintenance, the person closest to the work knows the work best.
Employees who spend a lot of time operating a particular machine or using a specific asset, build a level of familiarity that business owners can tap into to streamline their maintenance procedures.
This concept, known as operator care, places the initial responsibility for identifying problems and caring for assets on the equipment operator. Many asset management and maintenance tasks can be quickly picked up on and handled directly by the operator, allowing minor issues to be solved in real-time.
If a potential issue has been raised that the operator can’t rectify, your regular maintenance providers can move it and investigate more thoroughly.
This approach is also called operator-driven reliability–a strategy that simplifies maintenance workflows and increases predictive maintenance programs' efficiency.
However, this approach can soon become unstructured and difficult to monitor without the right systems in place. Operator care software can help you smoothly integrate operator-driven reliability into your organization, providing a structured platform to manage autonomous maintenance carried out by your team of capable machine operators.
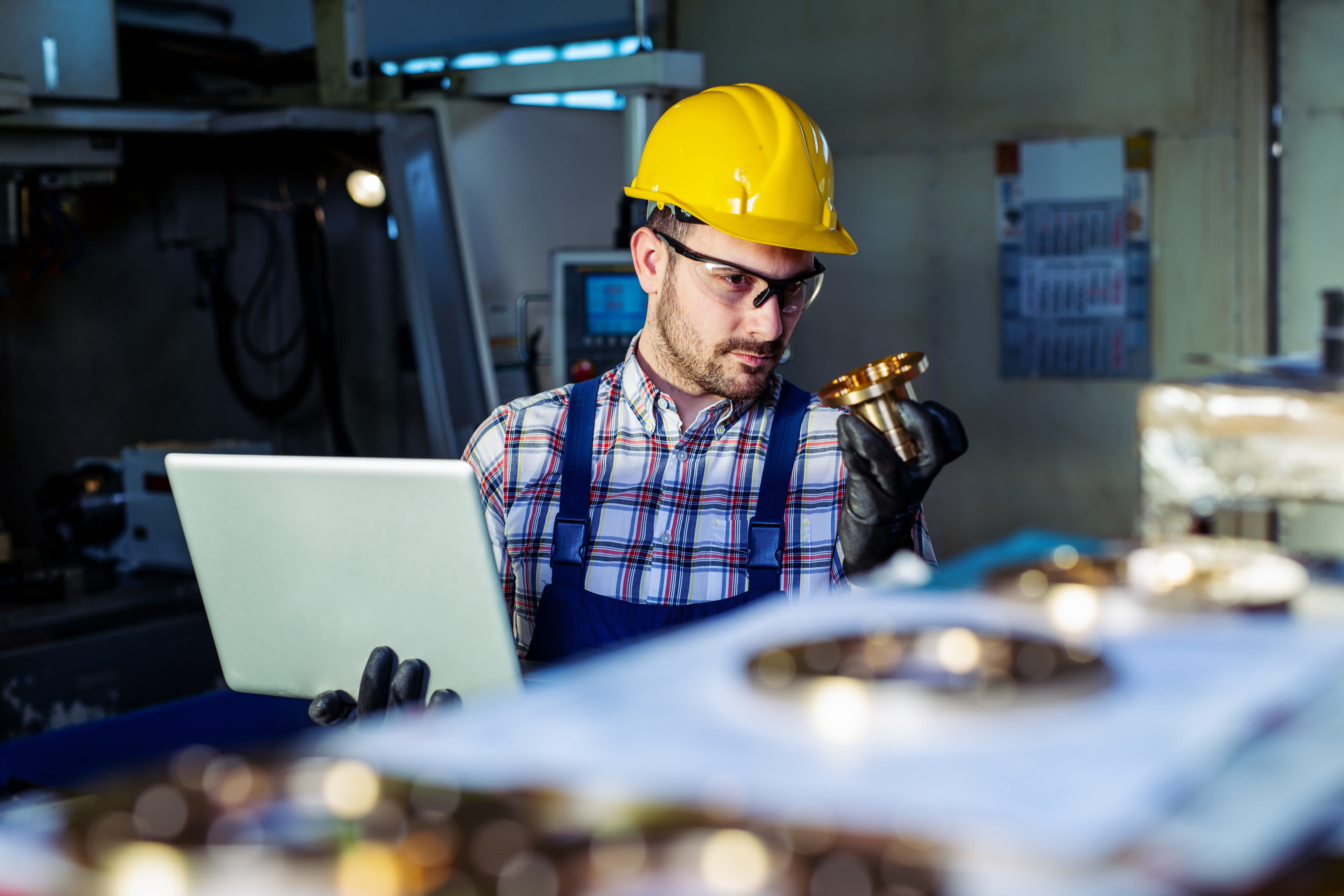
What Operator Asset Care Looks Like
Permitting machine operators to carry out maintenance tasks is the main idea behind operator asset care. This independent maintenance strategy shifts traditional workflows to employees who know the equipment instead of having maintenance technicians called in for basic jobs like lubrication.
Operator care always starts with the proper use of an asset. Running equipment according to the manufacturer's instructions and intended operating parameters will help extend the asset's life and optimize uptime.
Good ongoing asset management is the other side of the coin. By helping to keep the asset in good working order and staying on top of minor issues before they become big problems, operators can help the business mitigate costly downtime.
In an autonomous maintenance program, employees that operate the asset as part of their day-to-day role drive the care of that asset. This gives these individuals greater ownership and control – and when operators can perform basic maintenance activities such as lubrication, cleaning, and safety checks, maintenance costs can be significantly lowered.
Unnecessary downtime is also reduced, as specialist staff don’t need to be called in for simple maintenance procedures.
Skilled repair technicians also gain more time to focus on difficult or complex maintenance activities and can respond more quickly to emergency breakdowns.
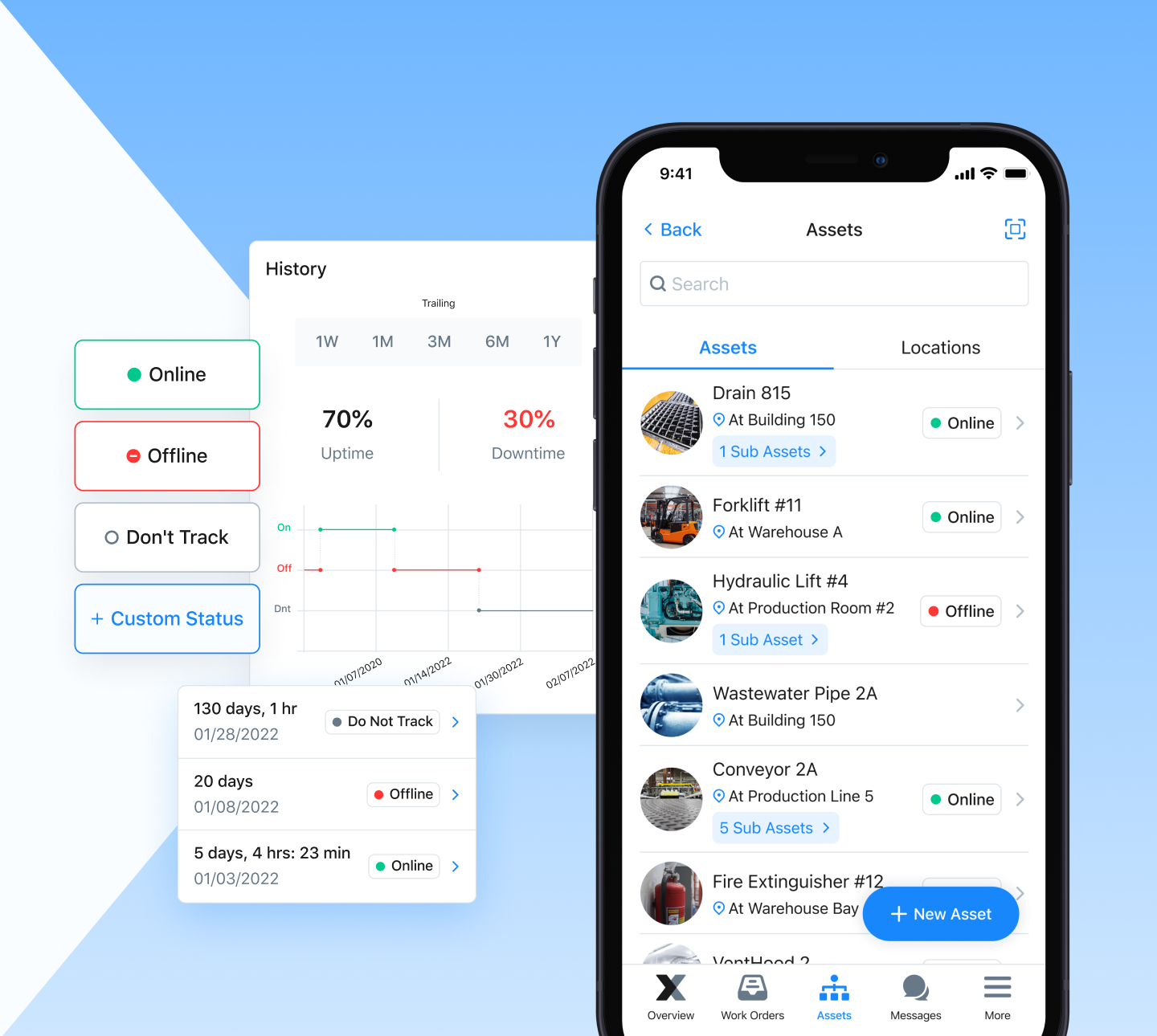
Bringing Tech to the Table
An operator care program requires a fresh approach to preventive maintenance, with technology playing a pivotal role in keeping everyone on track.
- Operators need a simple, user-friendly way to conduct their regular checks and record any maintenance tasks they have carried out
- Skilled maintenance technicians need to access records of the everyday maintenance tasks that the operator has been handling
- Maintenance managers need to ensure both operators and maintenance crews work in tandem to meet safety requirements and adequately maintain equipment
- Business owners and management teams need high-level dashboards to oversee maintenance costs, plan staffing requirements, and view metrics that influence Total Productive Maintenance programs.
With different stakeholders needing different information from their operator care software, it makes sense to ensure everyone’s needs are met when comparing platforms.
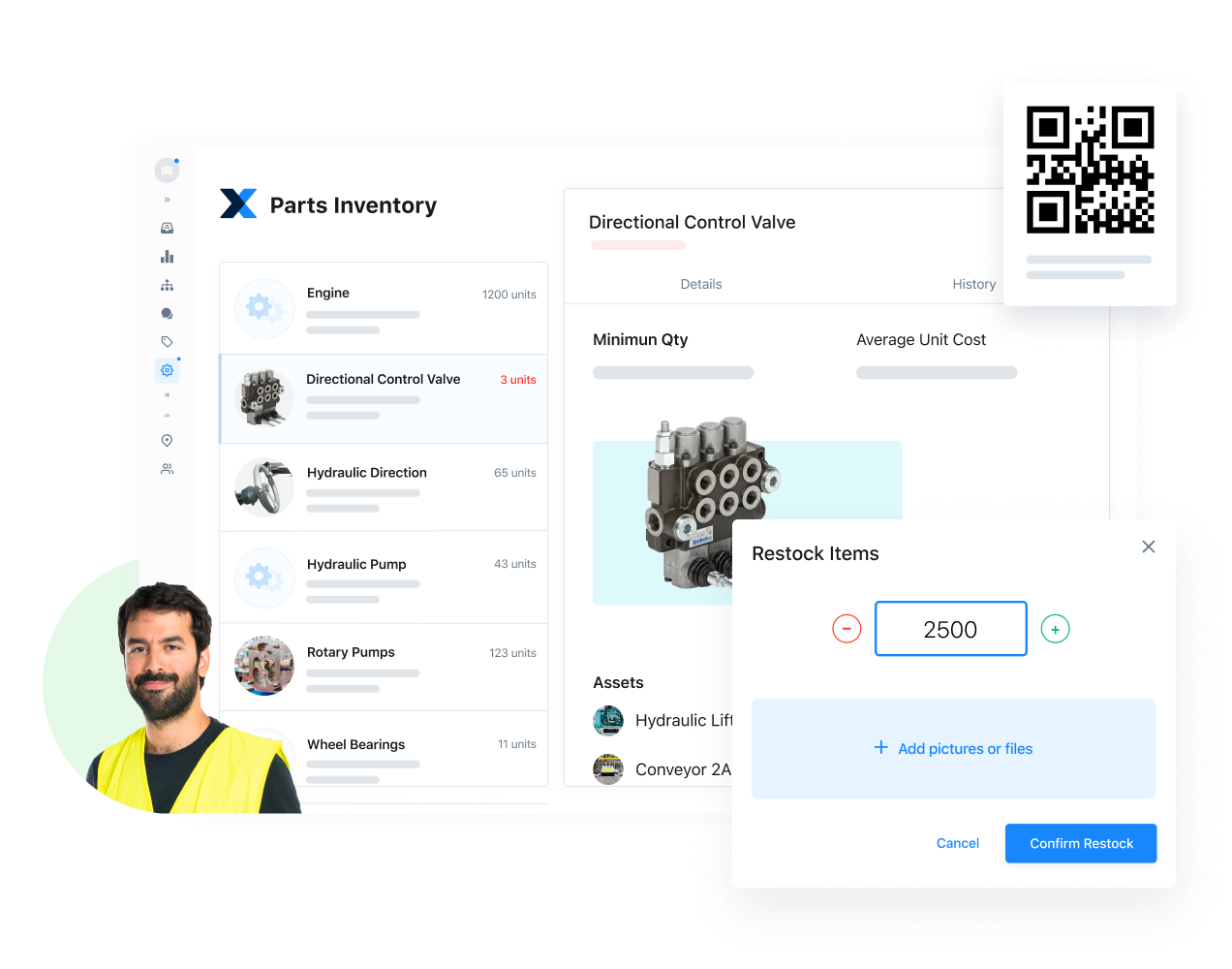
How a CMMS Supports Autonomous Maintenance Programs
The best way to approach an autonomous maintenance management program is to start by developing standard operating procedures for completing tasks. This can be done using Computerized Maintenance Management Software (CMMS) like MaintainX, which works on all devices and OS, including Google, Apple, and Microsoft.
Once you have standard operating procedures in place, maintenance managers can allocate tasks to individuals or teams at intervals that make sense for each asset. Your CMMS can be integrated with IoT sensors on equipment, automatically triggering maintenance work orders for operators. Linking the software with your CRM also offers additional automation capability to help maintenance crews plan and carry out complex maintenance tasks.
And, because a CMMS also collects real-time and historical data, management teams can review past performance and identify cost-saving opportunities or possible improvements to the company’s maintenance program.
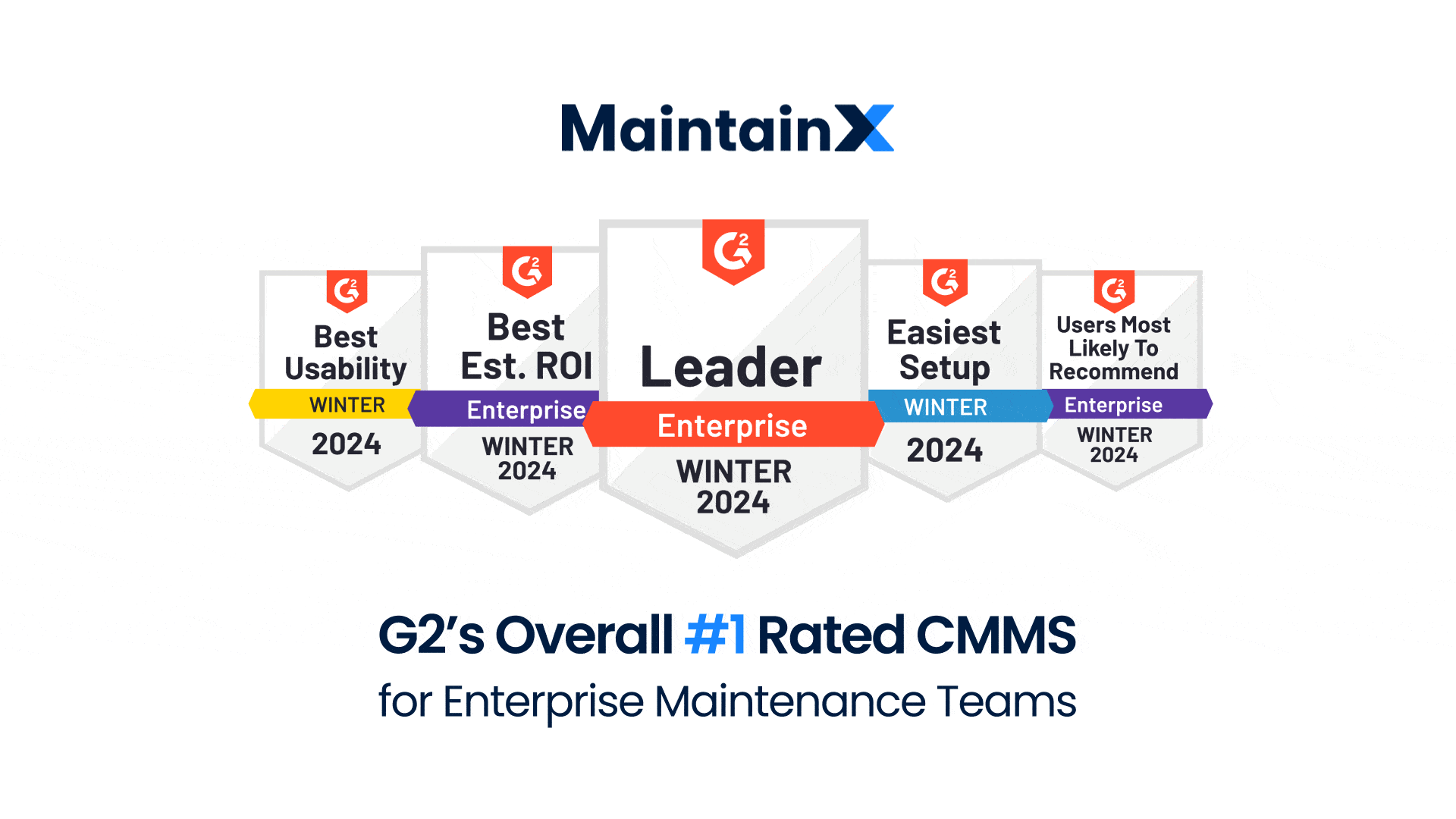
MaintainX: The CMMS Anyone Can Use
MaintainX CMMS is suitable for a wide range of industries. For example, it can help manufacturers maintain critical equipment, help assisted living businesses maintain their facilities, and help food & beverage outlets stay on top of daily cleaning and maintenance.
Shift simple maintenance into the hands of your capable operators by getting started with MaintainX today.
It’s free to download and will help your operator-driven reliability program run smoothly and efficiently.
FAQs
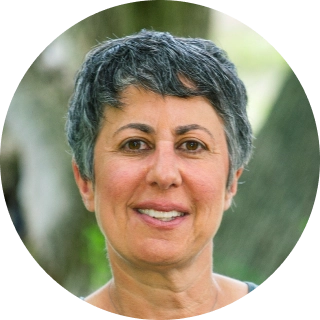
Caroline Eisner is a writer and editor with experience across the profit and nonprofit sectors, government, education, and financial organizations. She has held leadership positions in K16 institutions and has led large-scale digital projects, interactive websites, and a business writing consultancy.