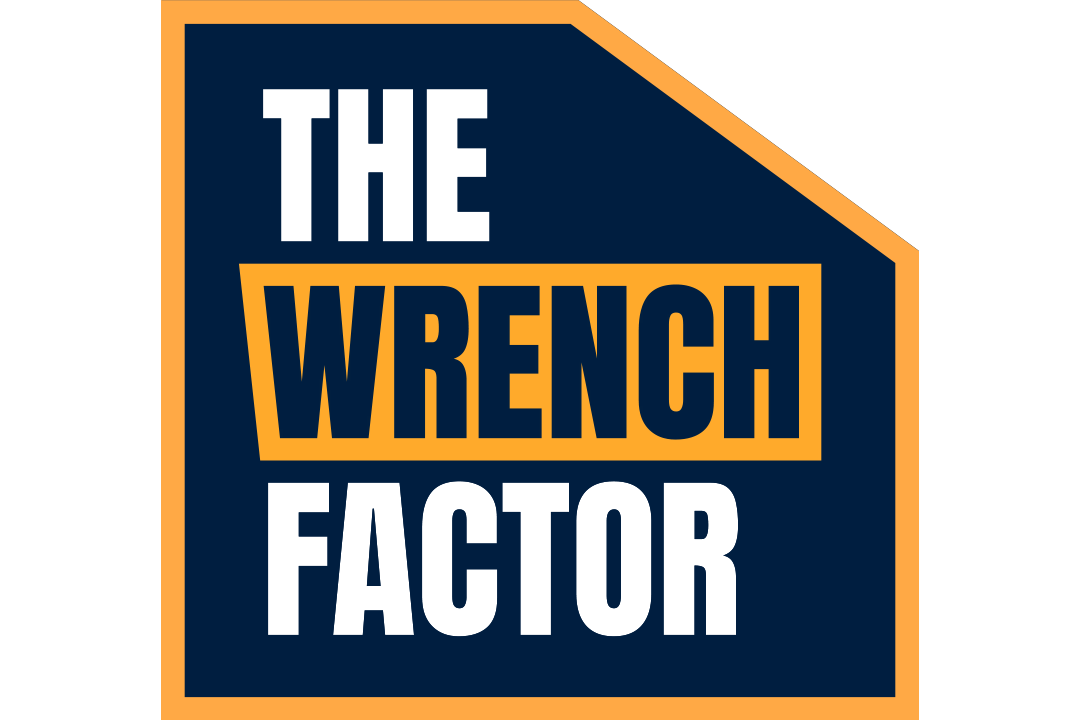
Wrench Factor is a series where we sit down with maintenance, reliability, and asset management experts to hear their stories and advice on the industry’s biggest topics.
The latest episode of Wrench Factor (watch below or listen here) explored 10 signs your maintenance program needs a tune-up. We’ll break down five of those signs in more detail and share some ways to tackle them.
Sign 1: No one knows how much downtime is costing the business
As the saying goes, “What gets measured gets managed.” This is especially true for downtime. Knowing the cost of downtime could be your ticket to optimizing your maintenance program and getting the resources you need to take it to the next level.
“There’s a big difference between feeling the pain of downtime…and being able to quantify that pain,” says Wrench Factor host Brit Bartolini.
“I was talking to someone the other day who’s starting to measure downtime using an Excel sheet, and it helped them see that it’s costing $15,000 a week.”
How to start calculating the cost of downtime
“The first thing to do is get the basics right,” says Tyler Hufstetler, head of partnerships at MaintainX.
“You need to get the downtime metrics, measure impact, then extrapolate that so you can justify and prioritize an investment in addressing that downtime.”
Here are a few more tips to help you calculate the cost of downtime:
- Start with a small number of machines to understand the variables, keep the tracking manageable, and create a formula that fits your operation.
- Shrink your scope further by beginning with unplanned downtime, which has a bigger impact on the business and will help you justify an investment in preventive maintenance.
- Prioritize your bad actor assets—the ones that have the most unplanned downtime.
- Note the factors that are making downtime cost more. For example, are out-of-stock parts leading to more downtime and higher inventory costs?
The metrics used to calculate downtime costs will differ between companies and even assets, but here are three core data points to consider:
Example of downtime calculation
Sign 2: Maintenance SOPs are kept in binders older than your interns
A stack of grease-smudged binders are a common sight at most facilities. But there are a lot of crucial insights in that pile that can make your team more efficient, which makes digitizing them critical.
“Tribal knowledge is absolute gold,” says Chris Morrissette, a Senior Enterprise Account Director at MaintainX, “but if it’s not captured somewhere, it’s literally going to walk out the door.”
“The teams I work with are starting to see this as a business risk, especially with the shortage of skilled labor and the time it takes to get new hires up to speed.”
How to start updating your SOPs
Digitizing SOPs is just one part of modernizing your processes, as Chris explains.
“It’s not just about standardizing your processes…but how you distribute them, and more importantly, how you pull old processes away.”
Here are seven steps that will help you swap that stack of binders for something more efficient:
1. Start with high-impact procedures: Identify 5-10 of the most common SOPs to start so you can avoid disrupting your team, overcommitting to a large project, and taking a step backwards.
2. Work with experienced technicians to digitize the SOPs: Sit down with technicians that are most experienced with your selected SOPs and build out the SOPs digitally in real-time.
3. Use mobile friendly tools: Make sure the tools used to digitize and access SOPs are mobile friendly, like QR codes on machines that link to SOPs, so they’re easily accessible on the plant floor.
4. Run a test with select technicians: Have technicians access and follow the SOPs to understand if the process works or doesn’t. Get feedback and use it to adjust the process.
5. Phase out outdated SOPs: After working out the bugs, start scaling your new SOP process. Plan to transition all at once so workers aren’t switching between the old and new ways.
6. Track usage and flag gaps: Track which SOPs are being used, which aren’t, and where new ones are needed. Adjust and fill in gaps over time.
7. Reinforce and celebrate what’s working: Dedicate five minutes of team meetings to review a new SOP, answer questions, gather feedback, and recognize the team for adopting new processes.
Sign 3: Your last big maintenance project failed and no one wants to try again
A failed project is one of the biggest obstacles to improving a maintenance program.
“Nothing hurts your reputation in an organization more than when you have an initiative roll out and it fails,” says Chris. “You only get so many of these opportunities.”
If the company has been burned by a project in the past (even if it wasn’t yours), it can be an uphill battle to gain back the trust needed to move maintenance forward.
How to get buy-in for a big maintenance project
The best way to sell an idea is using data to show it has big upside and little risk. Here are five ways to get that data by starting small with a project and gathering proof of concept to build your case:
- One facility: Launch a pilot at one facility before tackling a multi-site rollout.
- One asset/asset group: Experiment on a single asset or asset group, preferably one with less impact on production if something goes wrong.
- One technician/team/shift: Start with one employee or team to build champions and gain a deeper understanding of the best ways to drive change.
- One process: Update a single process to find out the possible side effects of change and how it’s received by your team.
- One maintenance type: Isolate one maintenance type to chart success and identify potential problems with fewer risks and disruptions.
Sign 4: Maintenance is only called when something breaks
Eliminating reactive maintenance often requires a cultural shift that extends beyond the maintenance team.
“[Solving this issue] means a total change in the mindset and commitment of leadership,” says Tyler.
“It’s about getting the right talent and building the right tech stack to support them, which can only be done with support from leadership.”
Connecting maintenance metrics to business impact can drive change at the highest levels of the organization and shift maintenance from reactive to preventive.
How to connect maintenance work to business impact
The foundation of executive reporting is understanding the key priorities of business leaders and tying them to maintenance work. These priorities often fall into five categories:
Sign 5: You have big gaps in your maintenance data
The right data is essential to making incremental improvements that allow your maintenance team to embrace more sophisticated tools and techniques, like AI.
“Everyone is thinking about AI right now,” says Brit, “but the data they’re collecting is only on paper, and everyone knows AI is only as good as the data put into it.”
Finding ways to improve data quality should be high on the priority list of every maintenance leader looking to make their operations more efficient.
How to collect better maintenance data
Chris has two pieces of advice for maintenance teams looking to improve their data.
The first is to start small.
“Start with your critical lines or assets,” says Chris. “Develop PMs, and collect data you can build on.”
This advice can also be applied to cleaning data and building reports. It’s easier to nail the process of collecting, cleaning, and analyzing data on a small scale so you can quickly make an impact.
The second piece of advice is to make it as simple as possible to log maintenance data.
“[Documenting work] has to be very simple,” says Chris. “If it takes…15 minutes to document something, it’ll never be documented. And if it’s not documented, you’re losing the data.”
Audit your processes to make them less complicated. For instance, something as simple as organizing failure codes in your CMMS by frequency instead of alphabetical or numerical order can increase the likelihood technicians select the right code and not ‘other.’
“Adoption drives data,” says Chris, “and data drives insight.”
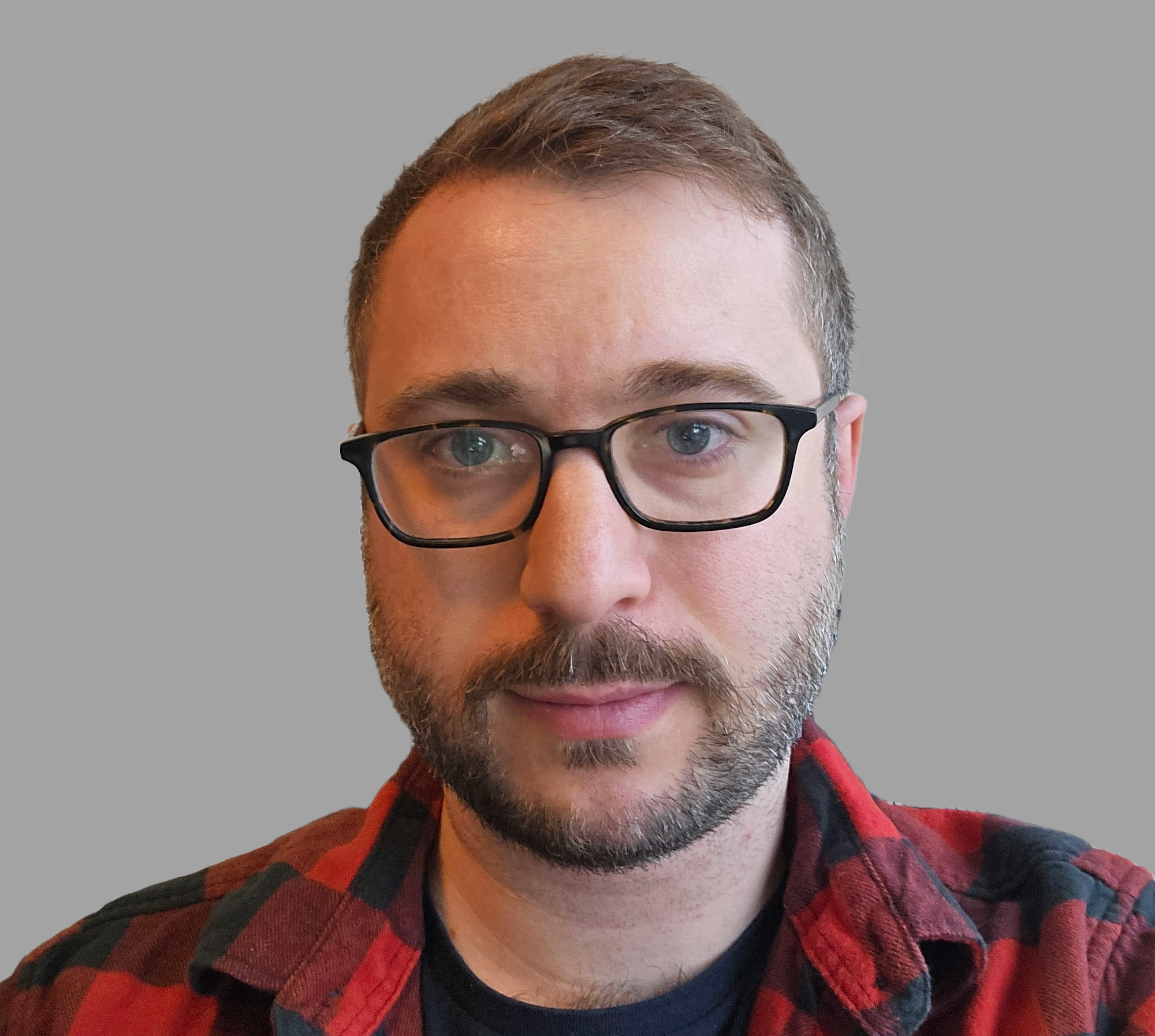
Marc Cousineau is the Senior Content Marketing Manager at MaintainX. Marc has over a decade of experience telling stories for technology brands, including more than five years writing about the maintenance and asset management industry.