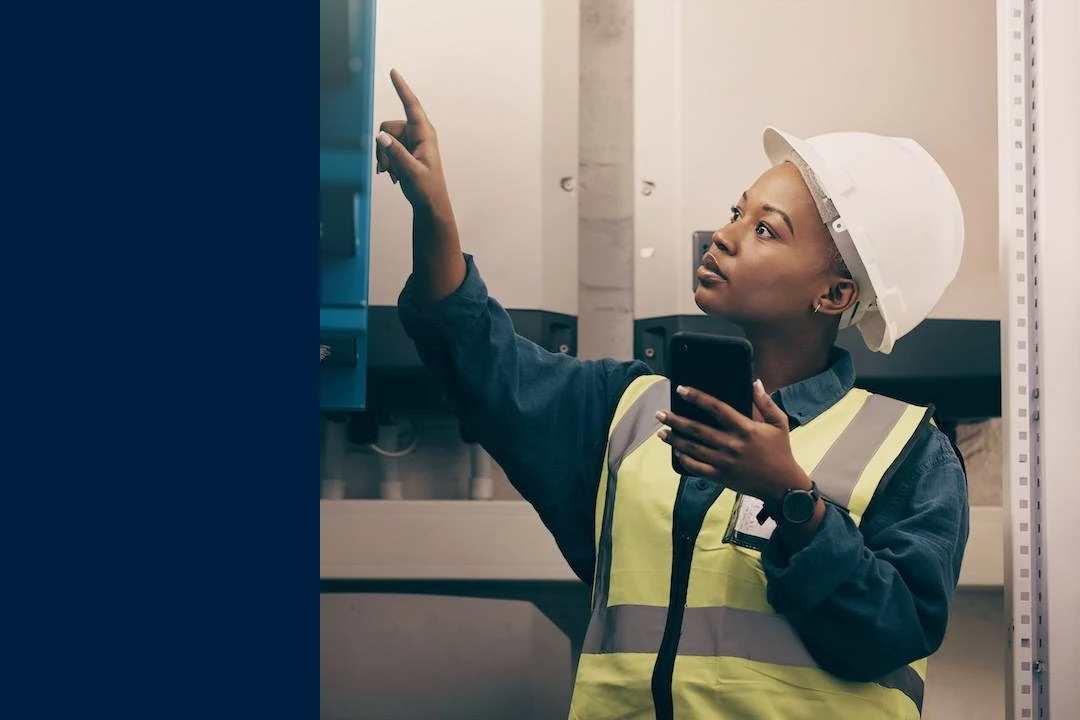
What if we told you the skilled labor shortage in manufacturing isn't just a crisis to manage, but a chance to transform your operations for the better?
For MaintainX’s 2025 State of Industrial Maintenance report, we surveyed 1,320 maintenance professionals across industries to gain a deeper understanding of the challenges they’re facing today. While we found that the skilled labor shortage is still a big problem, there are creative steps companies can take to overcome this hurdle.
In this post, we'll walk through our findings. Discover the factors fueling the skilled labor shortage, the risks of inaction, and, most importantly, concrete steps you can take to combat the shortage.
Why it matters: The real impact of the skilled labor shortage
The leaders we surveyed cited the skills gap as one of the top three challenges maintenance teams face today.
“There’s not as many young people coming into maintenance as there used to be years ago,” explains Woody Rogers, the Maintenance Supervisor at Cintas. “In some cases, we don’t even get a single application when a maintenance role opens up. And when we do get applications, they don’t always have the required skills.”
The problem is only going to get worse: According to a report by Deloitte and the Manufacturing Institute, 1.9 million jobs in manufacturing could remain unfilled by 2033 due to the skills gap. “As the older generations retire, it’s becoming challenging to replace that human capital,” says Justin Float, Fleet Maintenance Manager at Herlache Truck Lines. “The younger generations don’t grow up dreaming of becoming mechanics.”
But what does this actually mean for manufacturing? Let’s consider a few practical effects.
1. Reduced operational efficiency
Without enough staff, organizations will struggle to maintain their equipment and systems. Imagine a facility where multiple assets go down at once without enough qualified maintenance technicians to fix them. They’ll end up with delayed repairs and a maintenance backlog, especially if some of these machines are critical. This can create a ripple effect, like missed production deadlines or slower fulfillment times. Ultimately, the facility will have to deal with revenue losses and unhappy customers.
2. Compromised safety
It’s not just the extended downtime that’s a problem. Having limited labor means increasing the workload of the staff you do have. If such technicians get overworked, the quality of their work will suffer. This may result in equipment failures, safety hazards, or even production shutdowns. These issues can further decrease productivity and create costly disruptions.
3. Stifled innovation
A lack of skilled workers hinders a company’s ability to innovate and adopt new technologies. For example, imagine a factory looking to implement predictive maintenance with IoT sensors and advanced software. Without experienced personnel who understand the equipment and technology, the facility will struggle. This can leave the company at a competitive disadvantage—especially compared to rivals who are better equipped to implement advanced solutions.
How to tackle the skilled labor shortage
To overcome the skilled labor shortage, manufacturers must rethink how they acquire and develop talent. Rather than viewing it as an impossible challenge, companies can turn it into an opportunity. Here are some targeted strategies.
Enhance training programs
Without a steady pipeline of new staff, you need to ensure your existing workers gain the necessary skills to stay ahead. Investing in robust, frequent training is one of the most effective ways to do this. Think of this as an opportunity to elevate your team's skills beyond the status quo. Because your existing team already understands your processes, you can drive innovation from within. This proactive approach doesn’t just fill skill gaps—it transforms your workforce into a competitive advantage.
Provide on-the-job mentorship
Companies can also address the evolving labor landscape by developing internal pipelines of skilled technicians. Instead of relying entirely on an external pipeline, you can foster learning environments where experienced professionals mentor new recruits. Some teams—like Cintas—are already putting this into practice. “We want to play an active role in developing the skilled workforce we need to meet the evolving needs of our organization,” says Woody Rogers.
Invest in tools that boost efficiency
Dealing with a labor shortage means you must optimize efficiency for the staff you do have. One key step is to enhance their productivity by automating and streamlining tedious maintenance processes. Implementing modern technology, such as AI-powered tools or a Computerized Maintenance Management System (CMMS), can significantly reduce manual tasks and improve workflow efficiency.
A CMMS frees up valuable time for your technicians by automating routine maintenance scheduling, tracking work orders, and managing inventory. This lets your team concentrate on what they do best: keeping operations running smoothly and efficiently while minimizing downtime.
Build a future-ready workforce
The ongoing labor shortage makes one thing clear: Companies must become more proactive and think outside the box to ensure a steady talent pipeline. Investing in training and cultivating talent from within will help your team stay competitive and motivated.
Think of these steps not simply as one-off actions but as fundamental parts of your business strategy as you move forward. When managers invest in upskilling and creative solutions, they not only build a stronger, more capable team but also ensure the company is prepared to meet tomorrow’s demands.
Get creative and proactively seek solutions, and you’ll set yourself on the path to creating a more robust, resilient workforce.
Want more insights? Download the report today
The State of Industrial Maintenance report contains new approaches to tackling today's most critical challenges from maintenance, repair, and operations (MRO) professionals. Download the full report to see the trends shaping industrial maintenance in 2025 and beyond.
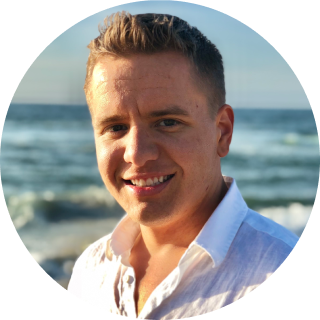
Nick Haase is a co-founder for MaintainX and is responsible for designing and leading the go-to-market strategies. He is a subject-matter expert in emerging CMMS technologies.