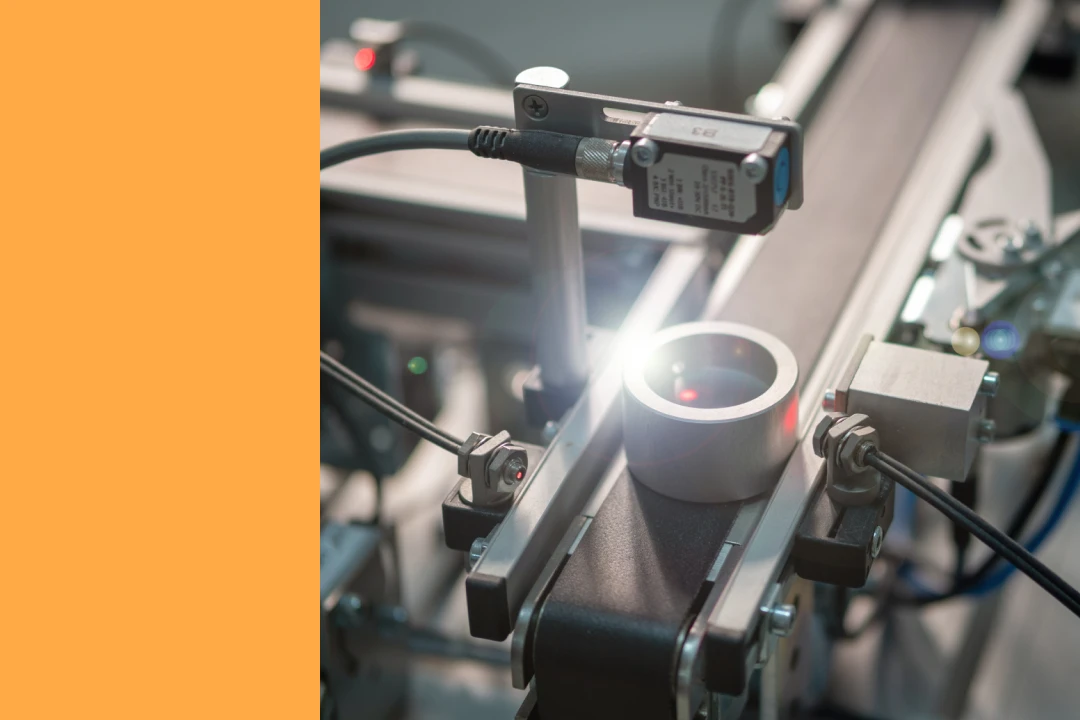
Most industrial leaders strive to be more proactive and data-driven. But getting there can feel overwhelming, especially if your teams spend much of the day firefighting.
Maintenance maturity depends on the quality of your data, how effectively you use it, and the processes and culture that support it.
The most mature companies not only gather equipment data—they turn it into actionable insights that empower technicians and help managers make decisions.
If you don’t keep good records today, or your asset data is buried in a filing cabinet or spreadsheet, your maintenance strategy is likely costing you more than it needs to.
There’s not necessarily a quick fix. But understanding where your team stands today and what steps to take next will help you build a smarter, more efficient operation.
You’ll also have a better sense of how to take advantage of the various technologies and strategies available to you.
The Five Stages of Maintenance Maturity
A maintenance maturity model developed in 1999 by Winston Ledet still serves as a roadmap for modernizing maintenance practices.
There are some slight variations of this model, but generally companies progress through these five levels:
- Reactive Maintenance – Fixing equipment only when it fails. This approach can be costlier due to unplanned downtime and emergency repairs.
- Preventive Maintenance (PM) – Scheduling maintenance at regular time or usage intervals to reduce more costly unexpected failures.
- Condition-Based Maintenance (CbM) – Using real-time machine data to monitor asset health and trigger maintenance when needed.
- Predictive Maintenance (PdM) – Leveraging data analytics and machine learning to forecast failures before they happen.
- Prescriptive Maintenance – Recommending repair actions and scheduling them automatically based on historical work and asset data.
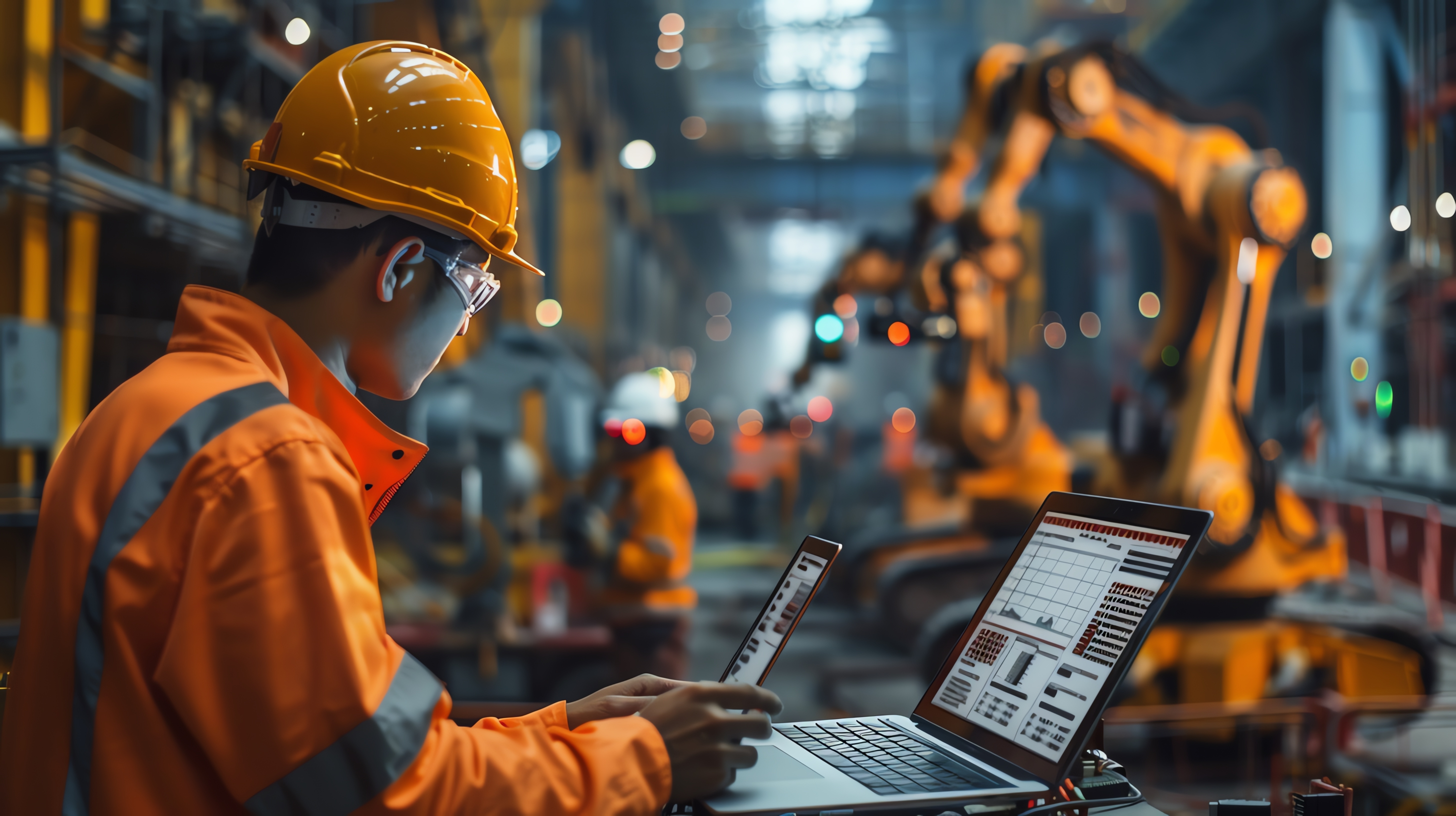
Why Maintenance Maturity Matters
The further a company progresses in maintenance maturity, the lower its costs and downtime. The U.S. Department of Energy found that shifting from reactive to preventive maintenance can cut maintenance costs by up to 18%, while PdM can deliver an additional 12% in savings.
By adopting smarter maintenance strategies, companies can improve equipment reliability, enhance safety, and optimize labor and resources. Mature companies deploy a mix of these strategies, depending on the criticality of the machine.
Practical Steps to Improve Maintenance Maturity
Every team is at a different stage of maturity, but here’s how you can start moving forward:
- If your team is mostly reactive: Start by prioritizing maintenance requests for your most critical assets, and implementing OEM-recommended PM schedules. Capturing work order and asset data in a CMMS will help lay the groundwork for more advanced strategies.
- If you’re doing some preventive maintenance: Standardize workflows using digital procedures to ensure consistency and track maintenance trends in your CMMS. Connect condition and usage data from your most critical machines to help optimize these schedules.
- If you’re using condition-based maintenance: Automate work order triggers based on sensor data to act on abnormal conditions faster. If you have rotating assets, start monitoring vibrations to catch faults as early as possible and detect potential future failures.
- If you’ve implemented predictive maintenance: Streamline workflows for your frontline teams to improve data quality and enrich predictive insights. AI assistants can help teams act on those insights faster by recommending repair actions.
The Path to Smarter Maintenance
Achieving maintenance maturity isn’t about jumping straight to AI and automation—it’s about building a solid foundation of standardized processes and high-quality data. By focusing on continuous improvement and measured progress, companies can develop a more resilient and cost-effective maintenance strategy.
Want to dive deeper? Read the full article in Plant Engineering.
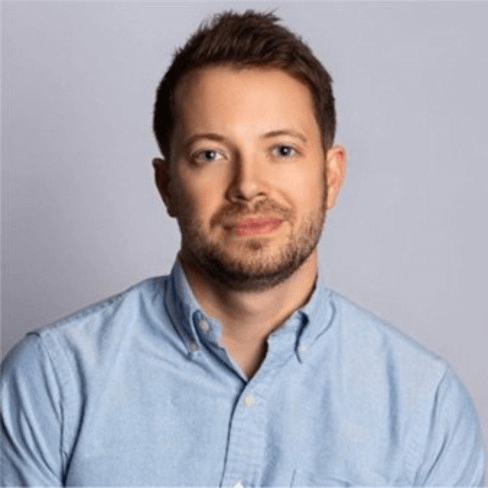
Colin Strachan is a Senior Product Marketing Manager at MaintainX, with a background in journalism and almost a decade of experience in SaaS marketing. In the past few years, he has worked with some of the world’s largest enterprises to adopt software that empowers their employees to work more effectively.