
Imagine this: A production line hums along smoothly. Operators clean and check equipment between cycles to spot problems before they snowball. No scrambling. No surprises.
That’s what autonomous maintenance looks like.
It’s a concept born from the principles of total productive maintenance (TPM) that gives frontline operators the tools and ownership to handle routine upkeep. In this guide, we’ll look at the basics of autonomous maintenance, how it works, and how to use it at your facility.
Key takeaways
- Autonomous maintenance empowers operators to prevent breakdowns by handling routine tasks like cleaning, inspection, and lubricating equipment.
- To implement an autonomous maintenance program successfully, involve operators from the start and give them comprehensive training.
- CMMS acts as a central tool for autonomous maintenance. It allows you to track tasks, flag issues, and create accountability, making your autonomous program more efficient and data-driven.
What is autonomous maintenance?
Autonomous maintenance is a strategy that assigns the responsibility for baseline maintenance activities to the primary equipment user, the machine operator.
The primary users of an asset take center stage and drive the asset’s maintenance program. Advocates of this maintenance philosophy suggest it provides operators with greater ownership, pride, and control.
Machine operators perform basic maintenance activities such as lubrication, cleaning, and safety checks. This frees maintenance technicians to focus on more complex and demanding maintenance activities, such as those involved in a total productive maintenance (TPM) program.
Principles of autonomous maintenance
Here are autonomous maintenance principles that guide frontline operators in gradually taking more responsibility and care of their equipment:
- Prevention through proper operation: Operators must use equipment correctly to minimize wear and tear and reduce the likelihood of failures.
- Maintain equipment in “like new” condition: Operators must regularly clean, lubricate, and inspect equipment to bring it back to its optimal state and maintain it. This helps improve performance and longevity.
- Standardize maintenance tasks: To ensure consistency and efficiency across operations, you must develop clear, standardized procedures for maintenance tasks.
- Ownership: Operators must take responsibility for routine equipment maintenance. This fosters a sense of ownership and accountability.
- Continuous improvement: Encourage operators to improve maintenance skills and maintenance processes continually.
Autonomous maintenance vs. preventive maintenance
Autonomous and preventive maintenance (PM) are the main pillars of total productive maintenance. These maintenance strategies focus on improving asset uptime, increasing production efficiency, and enhancing bottom-line performance.
Preventive maintenance is planned maintenance performed according to the manufacturer’s recommendations or predetermined intervals. Instead of waiting for equipment to break down unexpectedly, preventive maintenance proactively calls for routine upkeep that prevents minor issues from becoming major shutdowns.
Autonomous maintenance adds a layer of efficiency to the practice. In autonomous maintenance, machine operators are primarily in charge of executing basic maintenance activities such as routine inspections, cleaning, and lubrication. Machine operators are equipped to make fundamental maintenance decisions without going through lengthy approval processes.
Here’s an overview of the differences between autonomous and preventive maintenance:
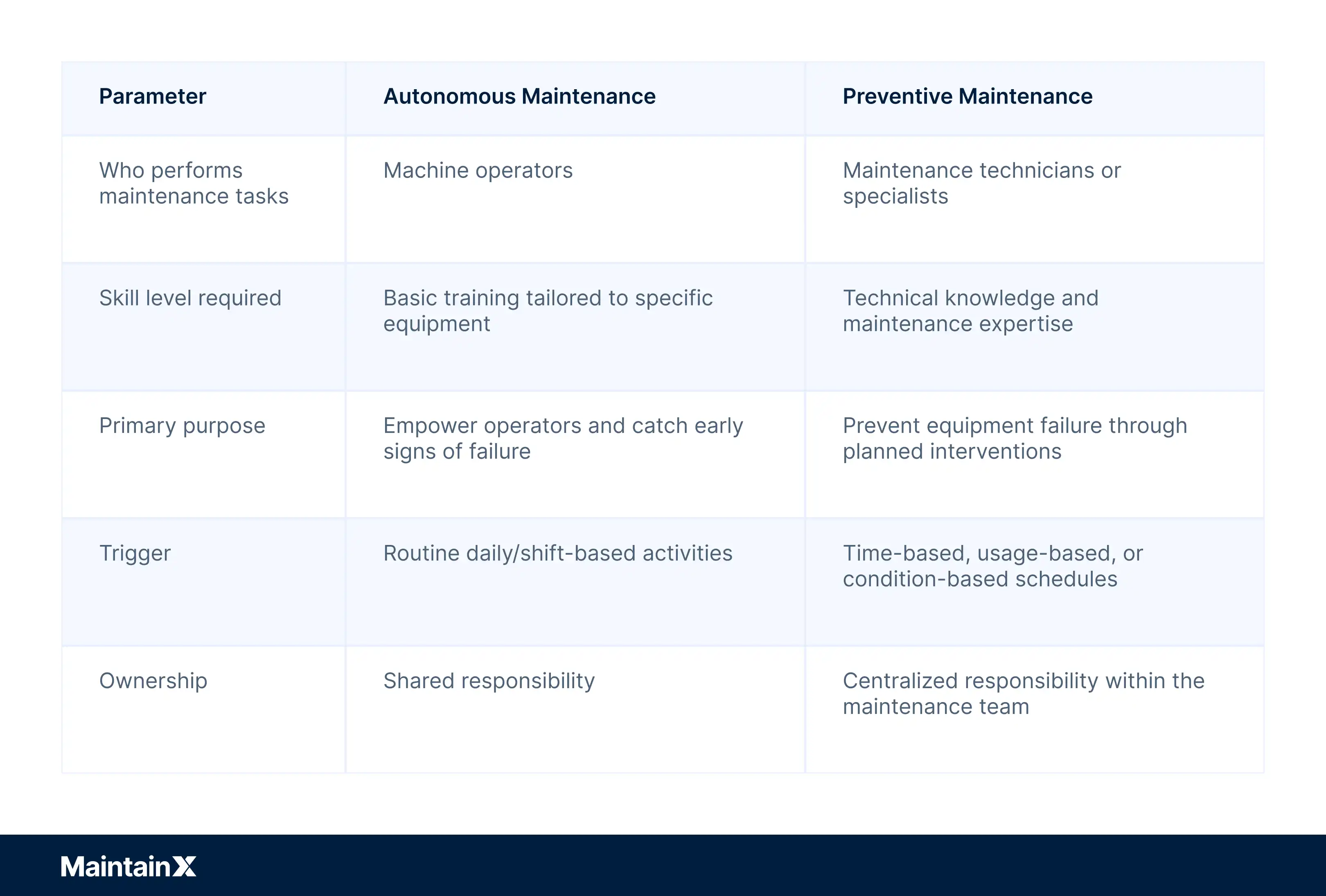
Benefits of autonomous maintenance
Autonomous maintenance and preventive maintenance complement one another. The benefits of adding an autonomous maintenance component to your PM program include:
- Increased equipment uptime: Autonomous maintenance empowers operators to catch issues early and fix them on the spot. This reduces the risk of sudden breakdowns and keeps machines more reliable.
- Lower maintenance costs: By reducing inefficiencies such as travel time and waiting for a technician's availability, you can take care of problems early on and at a lower cost. The more the machines deteriorate, the more maintenance costs you incur.
- Proper asset care: In large organizations, most maintenance operations focus on ensuring critical assets don’t experience major unplanned downtimes. Maintenance technicians and resources typically focus on big repairs. As a result, simple tasks like cleaning and lubrication can easily get overlooked until a problem arises. Autonomous maintenance ensures that someone always takes care of minor maintenance tasks properly and on time.
- Early problem detection: Autonomous maintenance lets you detect small problems in their initial stages before they become major concerns. Training machine operators to identify the early signs of equipment deterioration and malfunction lets them take corrective action to prevent a critical failure.
- More productive maintenance personnel: Autonomous maintenance frees up maintenance technicians to focus on more important, higher-level, and more complex tasks. They can plan their schedules better and refine their skills to address more critical issues, making them more productive overall.
- Improved employee engagement: Autonomous maintenance gives employees a greater sense of asset ownership and control.
- Improved overall safety: Assets under autonomous maintenance are constantly kept in good working condition, lowering the risk of accidents and injuries.
- Enhanced team spirit: Autonomous maintenance eliminates the “we vs. them” attitude between operators and technicians. Instead, teams work together to improve asset uptime and availability.
The overall benefit of autonomous maintenance is that everyone in your organization collaborates to ensure that your assets are well taken care of. This allows you to maximize availability, safety, and overall equipment effectiveness (OEE) of assets.
How to execute autonomous maintenance
Reliable Plant outlines seven easy steps for implementing an autonomous maintenance program:
1. Increase operator knowledge
Machine operators are usually well-trained to operate machinery at optimal capacity. However, for the autonomous maintenance program to be successful, they need more in-depth knowledge of the machines.
They should know the technical details of the assets and their components, how they work, common issues, and how to troubleshoot problems. Here are the equipment-related skills machine operators need:
- Problem detection and troubleshooting
- Asset repair and restoration
- Optimal conditions and settings for asset operation
- Optimal condition maintenance
Implement an effective training schedule to teach these skills to your machine operators. Retrain them from time to time to refresh and upgrade their skills.
2. Carry out initial cleaning, inspection, and repairs
The next step is to perform initial machine cleaning and inspection. The goal at this stage is to ensure that the assets are in “almost new” condition. Involve the production, machine engineering, and maintenance teams.
Start by thoroughly cleaning the assets and the surrounding area.
Next, look for common signs of deterioration, such as:
- Loose bolts
- Leaks
- Cracks
- Contaminated fluids
- Accumulation of dirt and dust
- Limited asset functionality
You should also develop easy-to-follow standard operating procedures (SOPs) for inspections and other basic maintenance tasks.
3. Eliminate root causes of contamination
After performing the initial inspections and cleaning, deal with any identified problems to eliminate their primary causes.
This will ensure that assets don’t deteriorate again. You should also improve access to the assets so that machine operators can perform basic maintenance tasks. You can avoid recontamination of the equipment by:
- Ensuring everyone sticks to established cleaning and maintenance standards
- Putting in place quality machine covers and seals to avoid soiling
- Adhering to continuous inspections to ensure cleanliness
- Establishing orderliness within the facility
Ensure that you consider safety measures, too. Under OSHA regulations, you are responsible for providing a safe working environment for your employees.
4. Develop lubrication and inspection standards
Develop standards that clearly indicate which assets (and their components) require lubrication and inspection, the process of cleaning and lubrication, and whose responsibility this will be.
Operators can develop their own standards for non-critical assets. However, it’s important to involve experienced maintenance engineers when developing these standards for critical assets.
Document all standards and make them available to all primary users once they’re ready. Regularly review and update these standards as your equipment portfolio or operating conditions change.
5. Consistently monitor maintenance tasks
After initiating your autonomous maintenance program, keep tracking and monitoring tasks. See if you can find ways to improve the SOPs and eliminate any duplicate tasks.
Tracking is easier with a computerized maintenance management system (CMMS). For example, MaintainX gives you full and real-time visibility over all work orders and the ability to communicate with the assignee with a built-in chat feature. This allows you to quickly identify and resolve issues without visiting the factory floor.
6. Standardize visual maintenance
The next step is to use visual indicators to help operators understand equipment and labels. Clearly label valves and levers to indicate their opening and closing directions. You should also mark normal and safe operating values next to gauges and use sight glasses so operators know when machines reach dangerous operating levels.
7. Ensure continuous improvement
Autonomous maintenance isn’t a one-off task that ends when you hit your targets it’s a long-term commitment throughout an asset’s entire lifespan. To improve your maintenance program, regularly collect and analyze maintenance data for optimization.
A CMMS like MaintainX can help with this. You can also ask for feedback from machine operators, team leaders, and maintenance technicians to improve your autonomous maintenance program. The goal is to have a sustainable program that can serve you in the long term.
Best practices to successfully implement autonomous maintenance
Following these best practices will help you get the most out of your autonomous maintenance program.
Involve operators from the start
Engage operators early in the implementation process. Ask for their input, listen to their insights, and involve them in creating maintenance standards and routines. Operators are more likely to stick with the routine and take initiative when they feel ownership over the process.
Provide proper training and education
New operators join your company with varying skill levels. It’s unfair to assume they know how to spot a misaligned belt or when to lubricate a bearing. If you want autonomous maintenance to succeed, you must invest in training.
Take time to teach them how the equipment on the shop floor works, what to look for, and how to perform basic maintenance safely. Hands-on, role-specific training builds confidence and sets the foundation for successful implementation.
Use maintenance management tools
Autonomous maintenance generates a steady stream of records and data as operators perform cleaning routines, minor fixes, and inspections. If you don’t have the right tools in place to capture that data, it’s easy for things to fall through the cracks.
A CMMS comes in handy when you want to centralize maintenance data. It helps your team schedule tasks, track completion, and flag recurring issues. It also enables real-time communication between operators and technicians.
Instead of leaving sticky notes or hoping someone follows up, operators can log abnormalities directly into the CMMS. This creates a digital audit trail that improves accountability and speeds up resolutions.
Align with broader TPM and lean initiatives
Autonomous maintenance works best when you integrate it into your larger operational strategy. It's one of TPM's eight core pillars meant to complement planned maintenance, quality improvement, and focused equipment improvements. Similarly, when autonomous maintenance is tied to lean manufacturing, it reinforces values like waste reduction, employee empowerment, and continuous improvement.
Aligning autonomous maintenance with TPM and lean initiatives ensures that everyone from leadership to operators sees how their efforts contribute to plant-wide goals. These goals include improving overall equipment effectiveness (OEE), reducing downtime, and minimizing defects.
Monitor and measure performance continuously
You need to track the impact of autonomous maintenance to prove ROI and find ways to refine your autonomous maintenance processes. Monitor metrics like unplanned downtime, Mean Time Between Failures (MTBF), and work order completion rates.
Boost morale
Celebrate wins to boost motivation and morale. For example, if your teammate catches a worn belt before it snaps, recognize them on the team’s Slack channel. Continuous measurement and rewarding good work reinforce the culture of ownership and improvement, which is the foundation of autonomous maintenance.
Develop a successful autonomous maintenance program
A successful autonomous maintenance program requires input from everyone on the team. It requires significant upfront training effort, but the benefits are massive.
If you’re ready to begin taking steps to automate your efforts, start by investing in a CMMS. try MaintainX for free.
FAQs
What is the difference between autonomous and preventive maintenance?
Autonomous maintenance helps operators perform routine upkeep and detect early equipment issues. Preventive maintenance relies on scheduled interventions by specialists to prevent failures. AM is operator-driven and routine-based; PM is technician-driven and schedule-based.
What are the seven steps of autonomous maintenance?
The seven steps of autonomous maintenance are as follows:
- Training operators on equipment and troubleshooting
- Performing initial cleaning, inspection, and minor repairs
- Eliminating contamination and root causes of deterioration
- Setting lubrication and inspection standards
- Monitoring tasks and improving SOPs
- Standardizing visual maintenance cues
- Continuously collecting data and optimizing processes
What is the difference between autonomous maintenance and TPM?
Autonomous maintenance is an important component of total productive maintenance (TPM). AM focuses on operator-led routine care, while TPM is a broader strategy covering all aspects of equipment reliability and OEE improvement. In short: autonomous maintenance is one part; total productive maintenance is the full framework.
What are the disadvantages of autonomous maintenance?
Autonomous maintenance can require extensive operator training, may produce inconsistent results if not monitored, faces resistance to change, and cannot replace technical repairs. Ongoing oversight and support are essential.
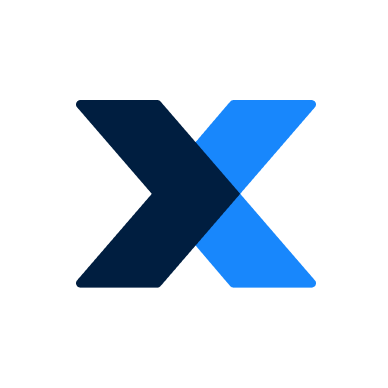
The MaintainX team is made up of maintenance and manufacturing experts. They’re here to share industry knowledge, explain product features, and help workers get more done with MaintainX!