A single machine breakdown in manufacturing can derail production and escalate costs in seconds. The costs from these disruptions add up over time. Just one hour of unplanned downtime may cost your facility as much as $25,000 on average; for larger organizations, this number can be as high as $500,000.
Total productive maintenance (TPM) prevents these setbacks with a proactive approach designed to keep every machine and tool performing at its peak. However, TPM is about more than upkeep. A well-thought-out TPM strategy is a foundation for operational efficiency that helps facilities reduce downtime, achieve production targets, and lower repair costs.
This guide unpacks TPM’s core principles, the eight-pillar framework, and TPM’s impact on overall equipment effectiveness (OEE). Read more to discover how TPM prevents costly equipment failures, optimizes productivity, and reinforces reliability across your entire production process.
TPM improves equipment effectiveness by involving all employees in maintenance tasks. For example, equipment operators and maintenance managers help with daily checks, simple repairs, and preventive actions rather than relying only on technicians.
TPM also uses planned maintenance schedules to address equipment needs before problems develop. By monitoring machine performance, your maintenance team can identify patterns and make small adjustments to improve speed, quality, and reliability. This proactive approach reduces equipment failures and helps maximize production output.
The result is consistent quality and fewer delays in production processes. These improvements will then significantly improve your overall equipment effectiveness (OEE).
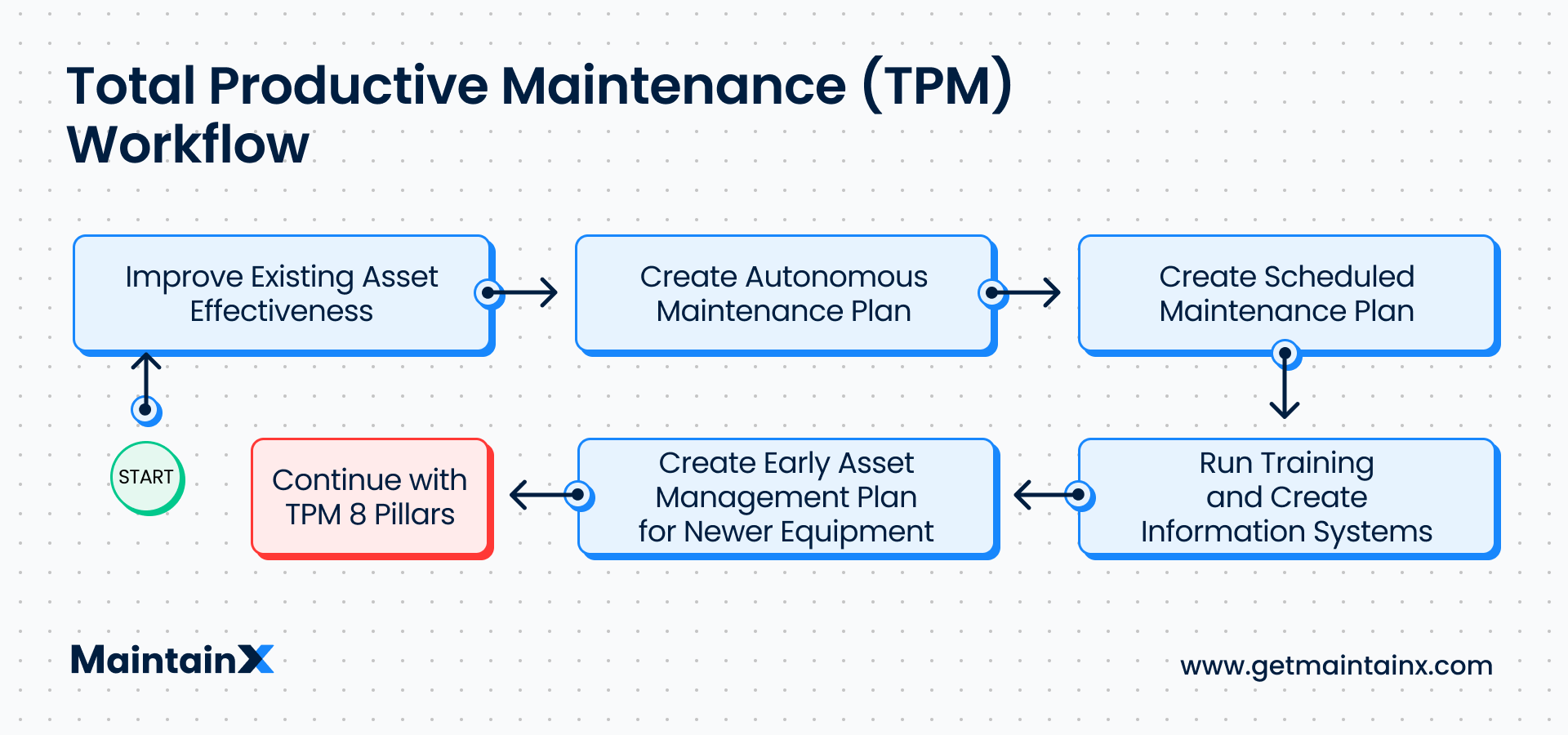
Core Concepts of TPM
Unlike reactive maintenance, which fixes problems after they happen, TPM aims to prevent issues before they occur. The three key ideas that drive this philosophy are as follows:
1. Proactive and preventive maintenance
TPM uses regular, planned maintenance activities to stop problems before they cause downtime. This approach helps equipment run more smoothly and reduces the risk of unplanned downtime or costly repairs.
2. Employee involvement at all levels
TPM requires input and action from everyone, not just your key maintenance personnel. All employees actively participate in routine inspections, cleaning, and basic maintenance to keep equipment in the best possible condition. By involving everyone, TPM promotes shared responsibility and pride in maintaining high standards.
3. Zero loss
TPM sets a target goal of "zero losses." This target includes zero breakdowns, zero defects, and zero accidents. By working together to prevent these major losses, your team can keep your machinery in prime operating condition for longer.
Eight pillars of a Total Productive Maintenance Program
The eight pillars of TPM build on the core concepts by outlining specific strategies to achieve the key goals specified by the core concepts. Collectively, these pillars encourage proactive strategies that prevent breakdowns, reduce waste, and increase productivity. Each pillar also plays a role in ensuring equipment reliability, safety, and continuous operational improvement.
Here is an overview of each of the eight pillars:
1. Autonomous maintenance
Machine operators take care of basic upkeep on their own equipment. That means operators are responsible for cleaning, inspecting, and performing simple maintenance tasks, such as lubricating moving parts or tightening loose bolts. They should not have to contact your maintenance personnel for these specific issues. Autonomous maintenance helps operators become more familiar with their machines and increases the likelihood that emerging issues will be caught well ahead of a breakdown.
2. Planned maintenance
Planned maintenance involves scheduling regular checkups and repairs to keep machines running smoothly. Planning these maintenance activities can prevent unexpected breakdowns and reduce the risk of costly downtime. This process often requires the expertise of a specialized technician to accurately assess equipment needs and perform necessary maintenance tasks.
3. Quality maintenance
The quality maintenance pillar focuses on preventing potential product defects due to mechanical errors. Employees on your production line closely monitor target equipment during production to watch for anything that might affect product quality. They then may perform minor adjustments or inform maintenance technicians of any major issues if found.
4. Focused improvement
Focused improvement involves identifying specific challenges that hinder productivity and efficiency based on the combined opinions of a cross-functional team. For example, production staff identify bottlenecks, and quality assurance specialists check that results meet standards. Typically, the goal is to incrementally identify and resolve small problems to achieve large-scale improvements over time.
5. Early equipment management
Early equipment management means using insights from past operational and maintenance tasks to guide the setup and design of new equipment. Engineers and maintenance teams can install or build simpler and more dependable machines by applying lessons learned. A CMMS makes it easier to access and understand this data. That’s because these tools help you organize maintenance records, track equipment performance, and highlight trends, making it simpler to analyze past issues to improve future plans.
6. Education and training
With proper training, workers learn how their equipment works, how to make minor repairs, and how to spot potential issues. This knowledge allows them to help keep machines in good condition and improve overall equipment performance.
7. Safety, health, and environment
This pillar focuses on creating a safe, healthy, and environmentally friendly workspace. It includes safety measures, health guidelines, and environmental protections to reduce accidents, minimize health risks, and ensure that operations don’t harm the environment.
8. TPM in administrative departments
One of the core principles of TPM is the involvement of all employees. This philosophy extends to your administrative teams. Administrative functions like scheduling, inventory management, and documentation all contribute to the success of your TPM program. Administration's involvement in TPM means that materials arrive as needed and records stay accurate.
Importance of Overall Equipment Effectiveness (OEE) in the TPM Process
Overall equipment effectiveness (OEE) measures how well a machine or system works compared to its full potential. OEE is important in the TPM process because it highlights if equipment is not being used to its full capacity. High OEE means that equipment operates efficiently, runs reliably, and produces high-quality output—all indicators of TPM success.
The formula to calculate OEE is:
For example, suppose a machine operates 8 hours a day with 30 minutes of downtime, runs at 90% of its maximum speed, and produces 98% of items within quality standards. In this case, you would calculate OEE by finding availability as 7.5 hours / 8 hours = 93.75%, performance (90%), and quality (98%). Multiplying these (93.75% x 90% x 98%) gives an OEE of 82.7%.
Six losses that a TPM program prevents
A TPM program prevents losses that disrupt productivity, product quality, and equipment operation. By addressing these losses, TPM keeps processes efficient. Here are the six key losses that TPM can help you avoid:
1. Breakdown losses
Breakdown losses occur when machines suddenly fail and need repairs. TPM prevents these issues by scheduling regular maintenance and closely monitoring equipment health. By fixing small issues, like loose parts or worn bearings, TPM stops them from turning into serious breakdowns.
2. Setup and adjustment losses
Setup and adjustment losses happen when machines take too long to prepare for production, often due to time spent switching between products or adjusting machine settings. TPM tackles this challenge by creating efficient setup routines, training staff on exact steps, and encouraging consistent settings.
3. Idling and minor stoppage losses
Idling and minor stoppage losses refer to brief pauses in machine operation that don’t require major repairs but still halt production for a short time. Although each stoppage might last only a few seconds or minutes, it adds up over time and reduces overall productivity. TPM addresses these losses by helping you identify common causes of these short pauses and training operators on how to fix them on the spot.
4. Reduced speed losses
Reduced speed losses occur when machines operate below their top speed due to aging parts, poor lubrication, or improper settings. TPM prevents this problem by enforcing routine maintenance and fine-tuning that keeps machines running optimally.
5. Quality defects and rework
Sometimes, products don't meet quality standards due to poor machine calibration or worn-out parts. TPM reduces this risk by ensuring machines are consistently calibrated, cleaned, and equipped with high-quality parts. This way, machines consistently produce quality items, which reduces waste and saves time by minimizing the need to redo work.
6. Startup losses
Startup losses occur when machines waste time and materials during warm-ups or initial runs. TPM reduces these instances by setting up standard routines for smoother startups and training operators to identify early issues. As a result, startup times are shorter, and machines reach full production sooner.
How to implement TPM
There are four essential steps to implementing total productive maintenance at your facility. Following these steps will help ensure a smooth program rollout and reduce the risk of disruptions to your operational efficiency during your transition.
1. Preparation phase
Start by defining what you want to achieve with TPM. Defining your objectives will provide key guidelines to set the foundation for the rest of your TPM implementation process. Identify key department members, such as maintenance supervisors, production managers, and quality assurance specialists, to form a TPM team. Then, provide guidelines to ensure everyone on your TPM team understands their role in the process.
This phase should also include gathering baseline data on current equipment performance and maintenance history to measure improvement over time. Leveraging a CMMS to streamline data collection and ensure accurate tracking can make this phase easier.
Key Tips for Success:
- Hold a kickoff meeting to clarify roles and communicate the team's initial goals.
- Document current maintenance processes for reference and comparison if they’re not already in your CMMS.
- Assign team leaders to facilitate smooth communication across departments.
- Plan for any initial costs, such as training or equipment, to avoid surprises later.
2. Introduction phase
In the introduction phase, you introduce TPM concepts to everyone in your facility and build a sense of purpose around the program. Start by hosting training sessions to explain TPM goals, the eight pillars, and how everyone contributes to achieving success. Ensure you clearly explain how TPM directly impacts their roles and benefits them, such as by improving work efficiency or reducing equipment downtime.
A good way to start is by selecting a pilot area to apply initial TPM strategies. This helps iron out any issues before a facility-wide rollout and demonstrates the impact this new program could have.
Key Tips for Success:
- Organize interactive sessions where employees can ask questions and get hands-on demonstrations.
- Create visual materials like posters or signs that explain TPM processes clearly.
- Set realistic expectations for the pilot area and adjust based on initial feedback.
- Highlight how their efforts contribute to your organization’s broader TPM goals.
3. Implement the eight pillars
During this phase, apply each of the eight TPM pillars throughout your facility. Begin with manageable goals and address one pillar at a time to avoid overwhelming your team. You should also track pillar implementation progress so your team sees the results of their effort.
Key Tips for Success:
- Encourage employees to record observations about equipment performance in your CMMS for continuous insights.
- Assign mentors for each pillar to provide guidance and answer questions as new practices are adopted.
- Implement a simple feedback system so employees can suggest adjustments as needed and feel like they’re part of the process.
- Set short-term and long-term goals for each pillar to maintain steady progress.
4. Consolidation phase
The consolidation phase is when TPM becomes a routine part of operations. Regularly scheduled reviews with the team help identify challenges, improve strategies, and keep TPM at the forefront of daily activities. Continue to provide training to keep employee skills up to date. Training also helps maintain the momentum gained in earlier phases.
Key Tips for Success:
- Hold monthly employee check-ins to maintain momentum and address emerging issues.
- Use data visualization to show progress and make adjustments more transparent.
- Celebrate individual and team milestones to keep motivation high.
- Integrate TPM metrics into performance reviews to reinforce commitment to the program.
Benefits of Implementing a Total Productive Maintenance Program
Total Productive Maintenance (TPM) offers clear advantages for manufacturing, including higher productivity, reduced downtime, and lower maintenance costs. Here are five ways TPM can benefit your operations:
1. Improved equipment reliability and availability
TPM increases equipment reliability and uptime by focusing on proactive and preventive maintenance tasks. It encourages teams to inspect, clean, and maintain machines before issues arise, reducing unexpected breakdowns and keeping machines running smoothly.
For Wauseon Machine, implementing TPM with the help of MaintainX led to a 6% improvement in their OEE over 16 months. MaintainX provided valuable features like meter-based scheduling that helped Wauseon’s team perform maintenance precisely when needed.
2. Reduced maintenance costs
TPM reduces maintenance costs by promoting routine, low-cost maintenance actions instead of waiting for major repairs. By identifying small issues early, your facility can avoid costly repairs and extend the lifespan of equipment.
3. Increased productivity and efficiency
TPM helps your team reduce downtime and improve equipment efficiency, which boosts productivity. With TPM methods like quick setups, regular inspections, and streamlined processes, machines operate longer without interruptions. Therefore, employees can complete tasks faster and with fewer delays.
4. Enhanced product quality
Having a regular maintenance schedule improves product quality by ensuring equipment runs at optimal conditions. Machines in good working order produce fewer defects, which leads to consistently higher-quality products and better customer satisfaction.
5. Improved safety and employee morale
TPM improves safety by emphasizing maintenance tasks that prevent equipment-related hazards. Safe, well-maintained machines reduce the risk of accidents, and employees can work confidently without worrying about malfunctioning equipment.
Common challenges in implementing TPM
Change is never easy, so you may face some challenges while implementing a TPM program. Common issues include employees' resistance to change, limited resources, and a lack of immediate results. These challenges can make establishing TPM as a consistent practice across your facility difficult, but there are ways to mitigate them.
How to address resistance to change
Employees may feel unsure about new procedures or prefer familiar routines. To overcome this, communicate clearly and involve team members in planning. By explaining the benefits of TPM and addressing concerns directly, you can build trust and encourage acceptance.
Build support through training and resources
For TPM to succeed, teams need specific training on maintenance procedures and regular access to necessary tools and equipment. Ongoing training helps employees feel confident in using TPM methods effectively. Also, providing resources like maintenance scheduling software and condition-monitoring devices supports TPM by allowing employees to perform tasks accurately and consistently.
The Future of TPM
Total productive maintenance (TPM) is changing rapidly as Industry 4.0 technologies become more common in manufacturing. TPM processes often include advanced tools like artificial intelligence (AI) and the Internet of Things (IoT) to make equipment monitoring more accurate and efficient.
For instance, predictive maintenance is a big trend. This strategy allows maintenance staff to quickly track emerging equipment issues and respond almost immediately. IoT sensors are attached to machinery, and AI tools analyze data to predict when equipment maintenance is needed.
With predictive maintenance, you no longer need to rely on routine inspections or wait for failure before fixing equipment. Instead, you can schedule maintenance based on real-time data.
Choose MaintainX to enhance your TPM process
TPM can transform the way you handle maintenance. Adopting or enhancing your TPM practices can prevent costly breakdowns, minimize downtime, and improve equipment performance. However, you will also need the right tools to help you maintain continuous improvement.
MaintainX provides those tools. Our CMMS will support your TPM efforts by providing a single platform to manage assets and track work history, inventory, and more. From a single, easy-to-use dashboard, you can oversee all aspects of maintenance in one place. Keeping every detail organized and accessible on one platform improves your workflow and team coordination.
FAQs About Total Productive Maintenance (TPM)
A TPM program differs from traditional maintenance practices because it involves all employees in your maintenance process. Traditionally, maintenance personnel are the only ones involved in routine maintenance. TPM emphasizes preventive and proactive maintenance techniques, whereas other strategies may be more reactive.
Operators' role in TPM is to actively participate in maintaining their equipment. Their involvement helps spot issues early, prevent breakdowns, and keep machines running smoothly.
Yes, you can implement TPM in small-scale operations by adapting its principles to fit your resources. Starting with basic steps like operator-led maintenance and focusing on routine checks helps improve equipment reliability.
It typically takes three to six months to see results from TPM implementation. However, the full benefits of your TPM program may not be fully realized until after a year of consistent practice. It's important not to give up on your program if you don't see results immediately, as realizing its full potential takes time.
Common challenges in implementing TPM are employees' resistance to change, limited resources, and a lack of immediate results. These factors can hinder efforts to establish TPM as a regular practice across a facility.
These challenges can be overcome by:
- Explaining the benefits of TPM and involving team members in the planning process to address concerns and encourage acceptance.
- Offering specific training on TPM methods and ensuring your employees have access to all of the essential tools, equipment, and software they need to confidently support consistent TPM practices.
- Emphasizing that TPM’s benefits will develop over time to help manage expectations and maintain motivation.
See MaintainX in action