
It’s true that preventive maintenance is the way to go when developing an asset management strategy. A robust preventive maintenance program will save money on maintenance costs, increase efficiency, and reduce unplanned downtime.
And those aren’t even all the benefits. However, it can be a mistake to focus entirely on preventive maintenance activities. While planning to prevent and avoid breakdowns, you also need to be prepared for unplanned breakdowns and equipment failures. This is where a corrective maintenance plan comes in.
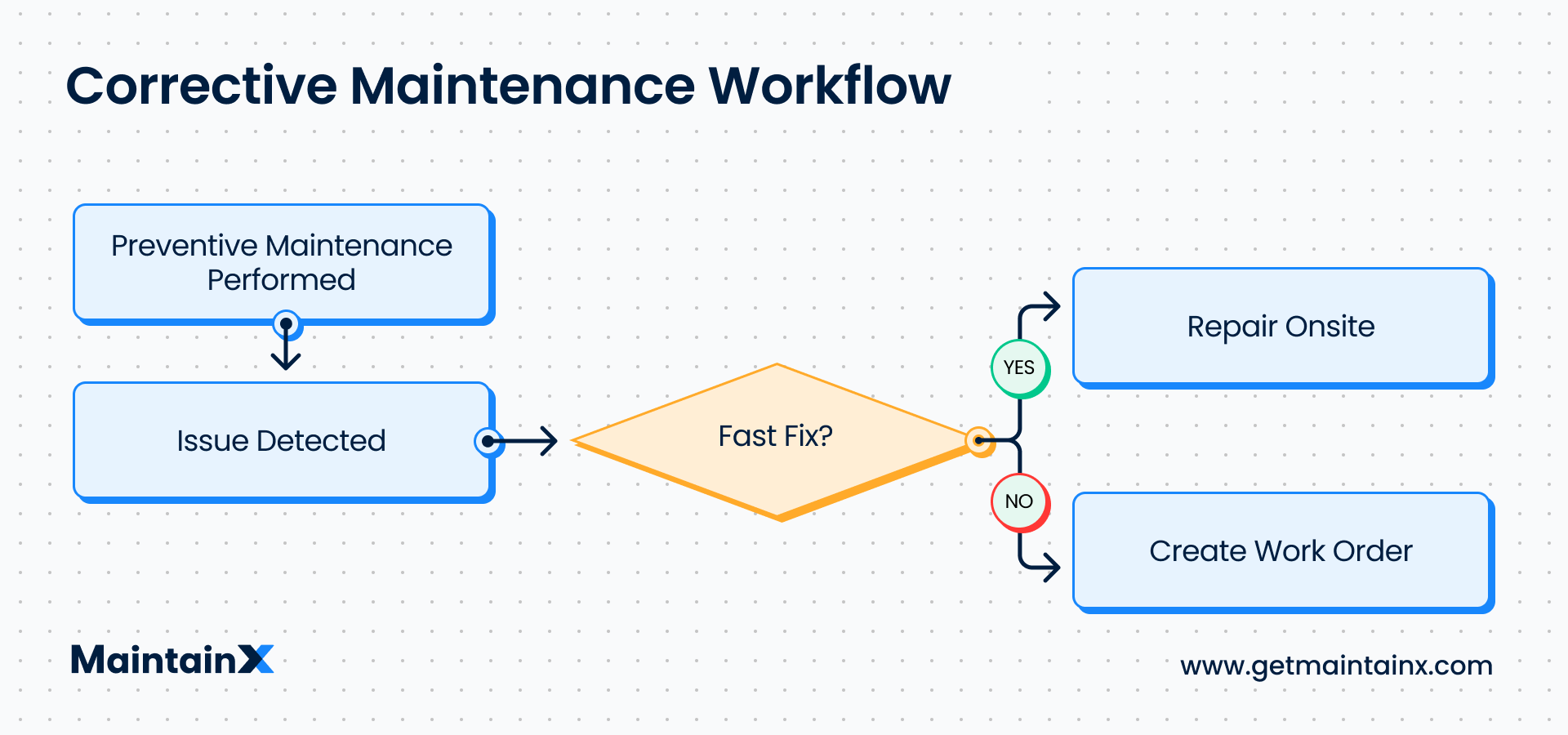
Asset Management Strategy and Corrective Maintenance
Asset Management Strategy is an organization’s approach to keeping its machinery and assets running correctly. As we stated above, maintenance management should ideally focus most efforts on preventive maintenance.
From regular checks and scheduled tune-ups to parts replacement guided by predictive maintenance, you want to make sure you don’t wait until your assets break down before you pay attention to them. But what happens when they do break down?
Asset failure is, in some cases, inevitable. Therefore, when planning your maintenance work, you should combine types of maintenance plans. (Preventive, run-to-failure, and condition-based maintenance, to name a few.)
Corrective maintenance (or reactive maintenance) refers to maintenance tasks carried out after equipment failure. For example, is a piece of equipment out of oil? Does a fan belt need to be replaced? These and many more maintenance actions make up corrective maintenance.
Or, to put it more simply: while preventive maintenance stops things from breaking down, corrective maintenance fixes them after they break.
Benefits of Corrective Maintenance
Even if all your equipment is already on preventive maintenance plans, a detailed corrective maintenance plan should be part of your broader asset management strategy. Here are just a few of the reasons why.
Saves Money
One primary reason for leaning on preventive maintenance strategies is that they can save money and improve profitability. However, this doesn’t mean corrective maintenance strategies won’t save you money.
If an asset gets to the stage of needing corrective maintenance, you’ll likely be spending more than if it never broke down. But an excellent corrective maintenance plan can ensure your repairs are as cost-effective as possible.
Suppose you’ve thought ahead about how to handle specific breakdowns or failures with particular assets. In this case, you won’t be subject to haphazard spending that can come with emergency maintenance. But, of course, your corrective maintenance plan needs to be robust. For example, you need to know which spare parts you might need to replace and stock up on them beforehand. This will save you on expedited parts replacement costs.
Saves Time
When you need to carry out corrective maintenance, you’re losing production time. But a good strategy will help reduce your asset downtime and save you time figuring out what needs fixing.
Instead of maintenance teams getting stumped when faced with a breakdown and then just beginning to figure out how to solve the problem, they can simply refer to the corrective maintenance plan already in place. As a result, your team members will know what actions to take on different types of assets, and you’ll resume production more quickly.
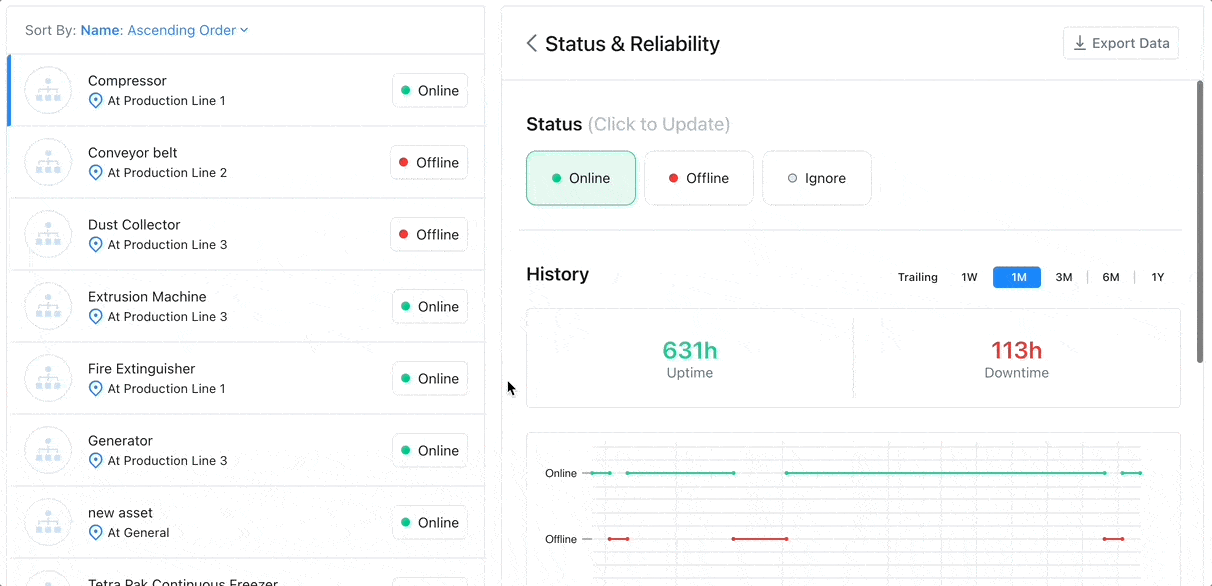
Saves Assets
No matter how effective your proactive maintenance is and how robust your reactive maintenance is, some assets will be beyond repair at some point. Reduced asset performance due to wear and tear is inevitable in the business.
However, losing assets to natural wear and tear is better than losing them to poor repairs. The last thing you want is to fix a broken-down asset only for it to break down again later, eventually reducing your equipment’s useful life or lifecycle. You want solutions that last, not stop-gap approaches.
Consider a situation where your regular technician isn’t available. Because you need to get production back up as quickly as possible, you seek help from someone who isn’t as skilled or knowledgeable about your particular equipment. Sure, you might get your asset up and running now, but in the long run, repeated failures from poor service will cost more than the production loss.
An excellent corrective maintenance plan helps you avoid short-term solutions that don’t last. You’ll be able to implement lasting asset maintenance solutions, especially for your critical assets.
“The bedrock of a successful digital transformation is user adoption, as you’ll only get the benefits of the solution if a critical mass of users is leveraging it. To design a great user experience that yields high adoption, it’s critical to improve upon your processes as you digitize.”
Forbes
Empowers Your Staff
The last thing anyone on your team wants is to be responsible for interrupting the production line. When you have essential assets at risk of failure, it’s not uncommon to find staff trying not to interfere with the delicate balance.
While conscientiousness isn’t a bad trait, you don’t want your staff to lack conviction. Establishing for your employees how to take corrective action will help improve their confidence. In addition, they will know what to do if something goes wrong.
“By understanding the different pain points experienced by frontline personnel, maintenance planners, and plant managers, implementation teams can better design the new, digitally enabled processes to address longstanding problems.”
McKinsey
Implementing Corrective Maintenance with a CMMS
A computerized maintenance management system is a powerful tool for optimizing corrective maintenance. The right CMMS software can help you in the following ways:
Digitized and Automated SOPs
If you want to save time and prevent errors in your maintenance activities, one place to start is by establishing your standard operating procedures. Standardizing your maintenance processes ensures that your technicians know what to do and how.
Standard operating procedures empower your teams, onboard new workers, and provide step-by-step instructions for those who may need to jump in when a machine goes down.
Use computerized maintenance management software like MaintainX to give your staff real-time access to SOPs.
Root Cause Analysis
After all this planning, you want to ensure your corrective maintenance work is practical and effective. Imagine your technicians working hard to fix breakdowns, only for those breakdowns to recur in a matter of days or weeks. This is where root cause analysis comes in.
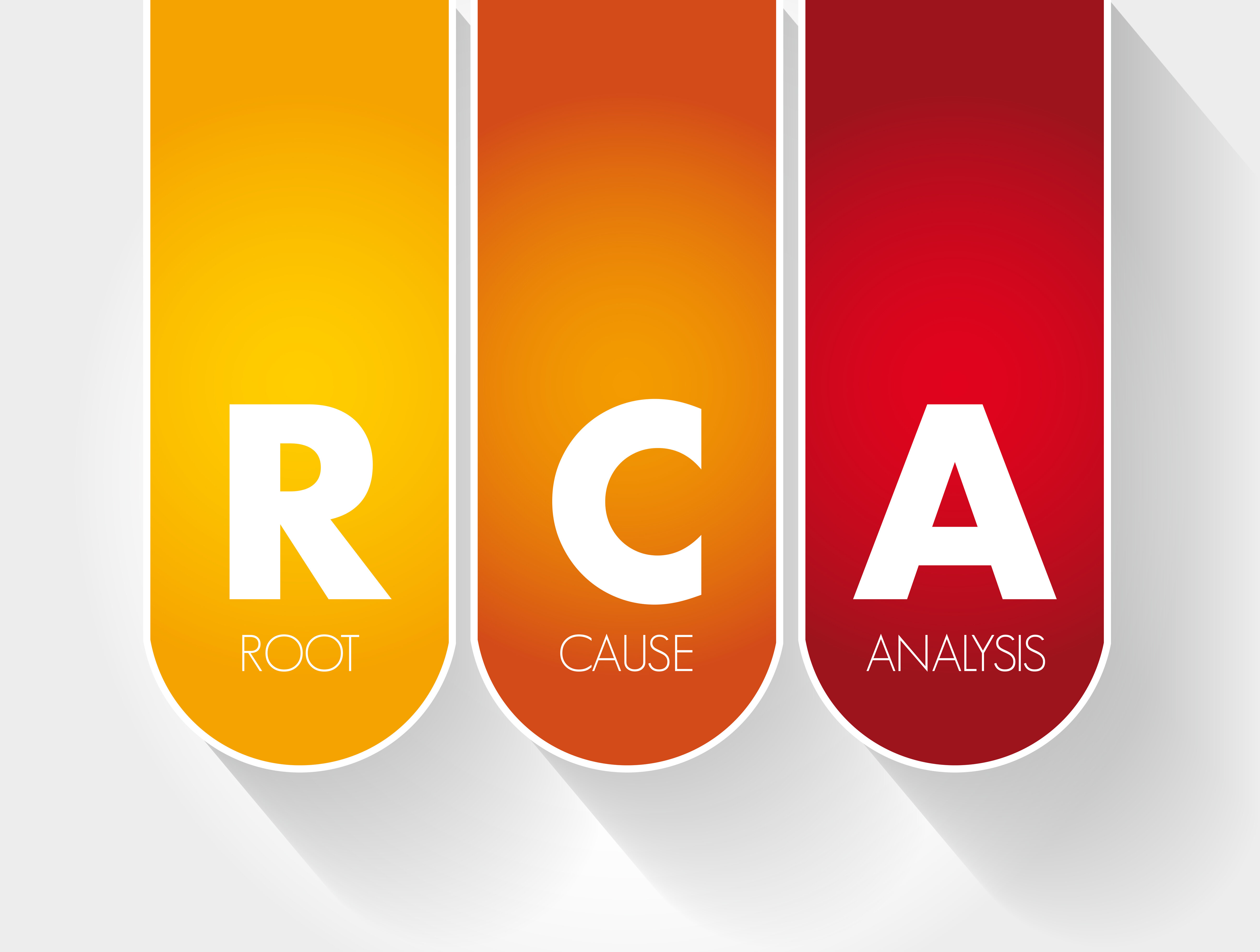
Instead of simply addressing symptoms, root cause analysis aims to get at the heart of problems with assets and machinery. Taking a deep dive into the root cause of equipment issues can help you know exactly where to target your corrective maintenance efforts for maximum results. As a result, you’ll save time and effort and improve your assets’ lifespan when you ensure they’re correctly repaired and put on a preventive maintenance plan.
Instant Communication
Despite having a plan and workflows ready to go in case of unplanned downtime, you can still be hit with surprises. For example, technicians might have to deal with unclear instructions, unavailable tools, poor parts inventory management, and other problems.
In cases like this, you want your team members to have access to each other. MaintainX is the first work order software with chat and allows real-time, instant communication via our mobile and web apps. As a result, staff can communicate quickly, seek clarification, brainstorm solutions, and share real-time updates.
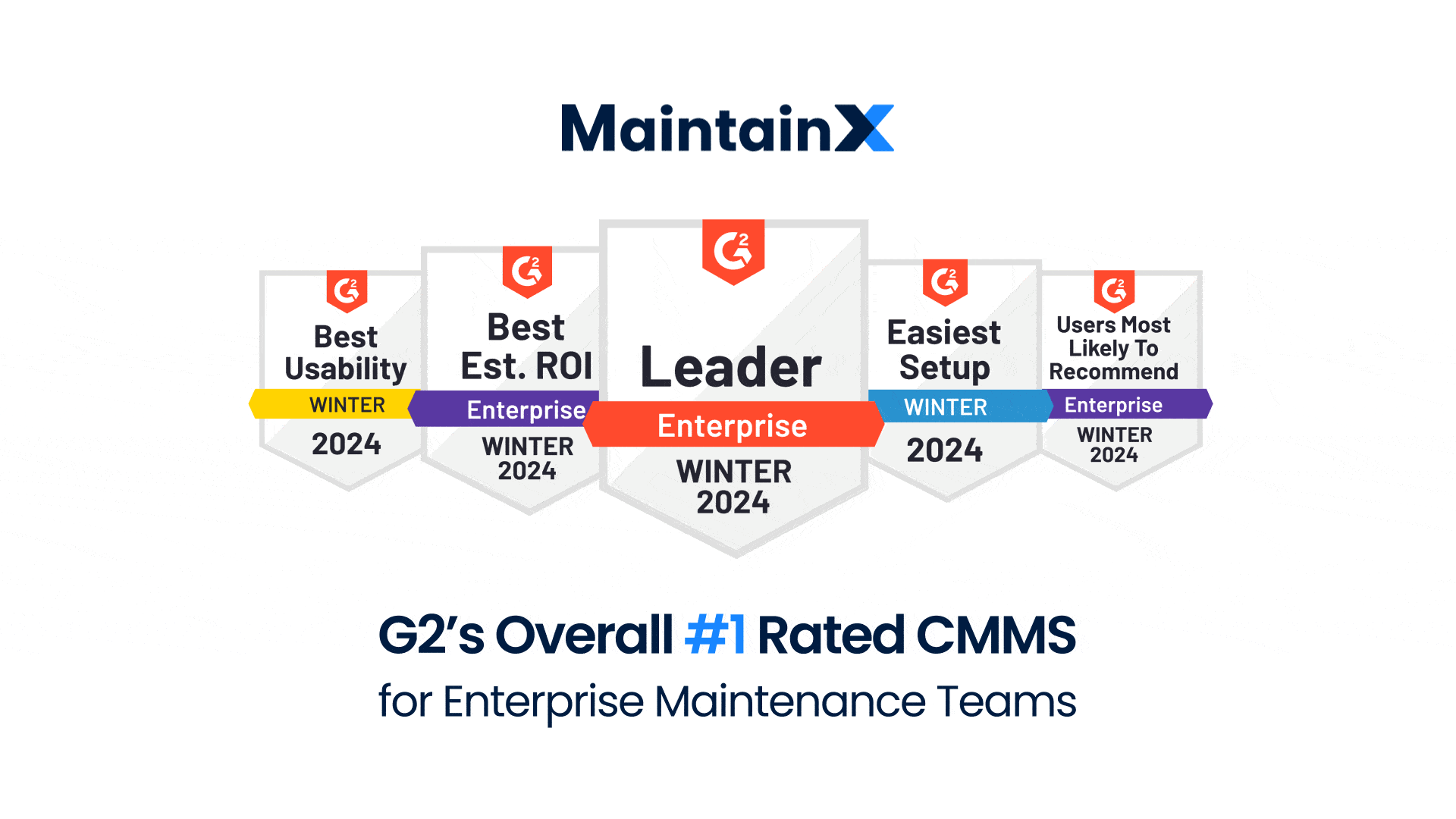
Optimizing Your Corrective Maintenance with MaintainX
MaintainX CMMS has powerful features to help you streamline your corrective maintenance. From automated and repeatable work orders to reporting dashboards that help you visualize data, there’s a reason MaintainX was rated the #1 CMMS in G2’s Winter 2023 report. Try MaintainX today!
FAQs
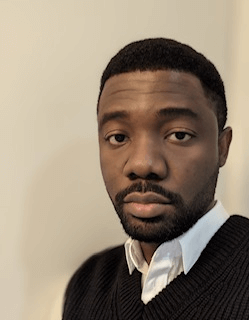
Lekan Olanrewaju is a content writer with years of experience in media and content creation. He has held positions at various media organizations, working with and leading teams at print magazines, digital publications, and television productions.