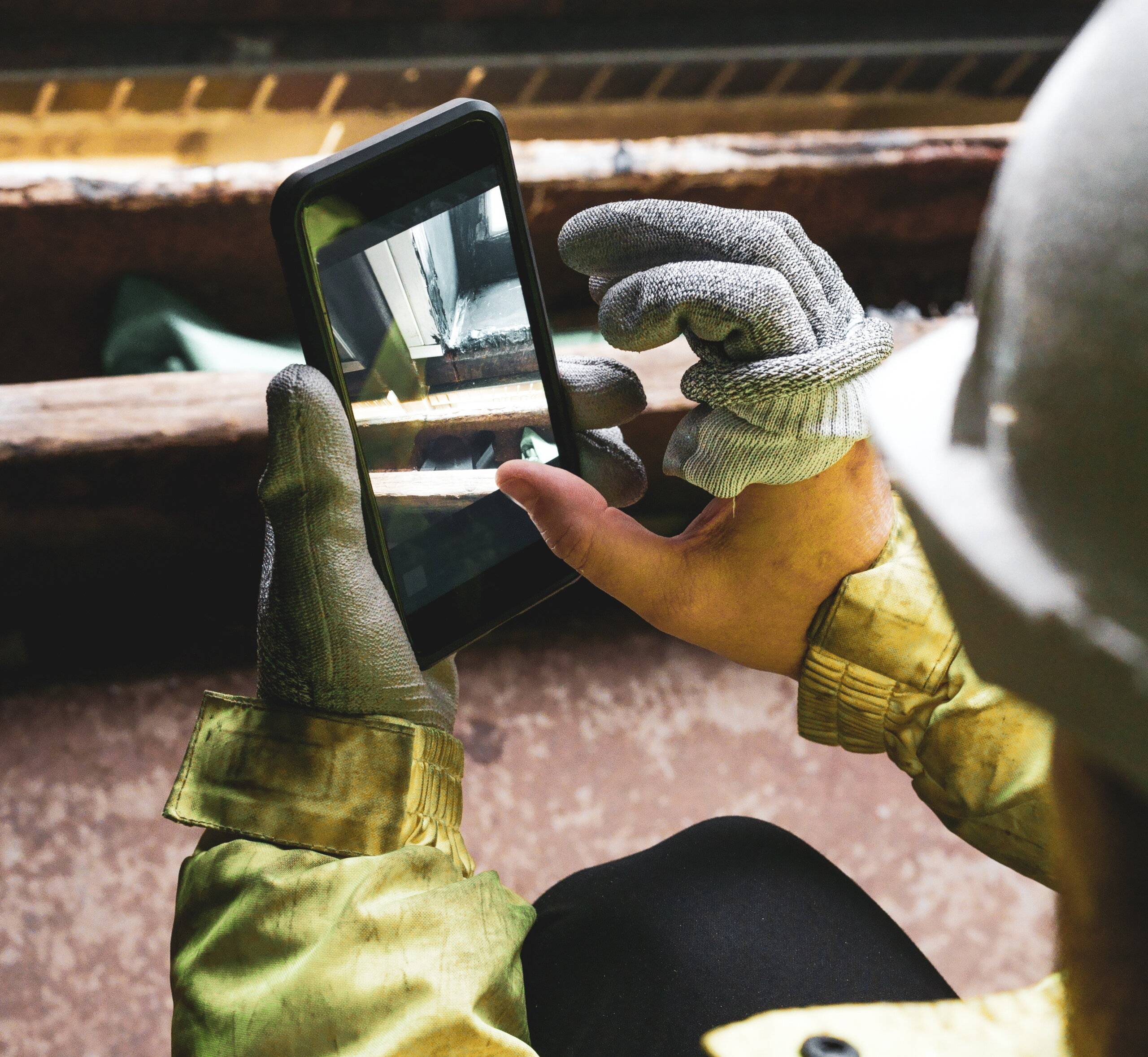
Unplanned downtime can significantly disrupt business operations, leading to lost revenue, increased operational costs, and potential damage to client relationships. In fact, studies show that unplanned downtime costs Fortune Global 500 companies approximately $1.5 trillion annually.
Cutting downtime is key to keeping operations smooth, lowering costs, and boosting productivity. And you don’t have to be a Fortune 500 company to feel the effects—on average, downtime costs organizations $25,000 per hour.
This guide breaks down the differences between planned and unplanned downtime, gives you practical tips to handle both, and highlights key metrics to track equipment performance. Learn how to save time, work smarter, and improve your processes.
What's the difference between planned downtime vs. unplanned downtime?
Put simply, planned downtime is scheduled in advance, while unplanned downtime happens unexpectedly.
Planned downtime is actually a good thing. It lets teams prep, gather tools, and follow a plan to finish tasks with minimal disruption. The challenge is scheduling planned downtime at the right time and getting the right parts or people ready. Delays can extend downtime and throw off operations.
Unplanned downtime pops up out of nowhere and is more disruptive since it halts operations and needs a quick fix.
There are a lot of reasons why unplanned downtime happens. According to the State of Industrial Maintenance Report, aging equipment is the most common cause of unplanned downtime (29%), followed by equipment failure (22%) and operator mistakes (12%). Also, 65.7% of managers report that they experience more downtime when they have a labor shortage.
The importance of reducing unplanned downtime events
Minimizing downtime is crucial because it directly improves productivity and reduces costs. When equipment fails, everything stops, leading to lost time and pricey repairs. Broken machines can also create safety risks. These disruptions push back deadlines and force teams to drop planned tasks to handle emergencies. That’s why even a small amount of unplanned downtime can derail workflows and sink thousands of dollars.
What’s interesting is that, even with fewer incidents, the State of Industrial Maintenance Report found that 29.4% of facilities say that each unplanned downtime event costs more than it did in the past. Several factors are causing unplanned maintenance to cost more. Put simply, emergency maintenance requires more resources than planned maintenance.
According to the report, this increase in cost is linked to:
- Rising parts and shipping costs (72%)
- Higher labor costs (48%)
- Wear and tear on critical equipment (40.6%)
Also, frequent unexpected downtime puts more strain on equipment, which can lead to more breakdowns and shorten the lifespan of machinery.
Strategies to reduce downtime
The best ways to reduce downtime depend on whether your goal is to reduce the risk of unplanned downtime events or shorten the length of planned downtime. Here are some strategies to help you effectively reduce downtime in both situations.
Strategies to reduce unplanned downtime
1. Implement predictive maintenance
Predictive maintenance involves using tools like meters, sensors, and counters to track equipment usage and conditions in real-time. Monitoring indicators such as cycles, temperature, and vibration help predict when maintenance is necessary. This approach reduces the frequency of unexpected failures and prevents excessive, unnecessary maintenance.
For example, ColdTrack cut downtime by 70% by tracking cycle counts and monitoring equipment through MaintainX.
2. Conduct proactive equipment assessments
Schedule regular assessments to check for early signs of wear or fatigue in key components. Fixing small issues now prevents bigger problems later. These inspections are also a way for your team to detect which assets are getting too old to do their jobs. Maintenance helps, but at the end of the day, our report found that simply replacing aging equipment will reduce downtime 43% of the time.
3. Optimize maintenance scheduling based on historical data
Look at your past performance and downtime records to help yourself schedule maintenance work at the best times for your facility. Use the data to fine-tune the schedule so you’re not overdoing it or skipping any needed inspections. The State of Industrial Maintenance Report found that being proactive about your maintenance tasks leads to a 65% reduction in unplanned downtime.
Strategies to minimize planned downtime
1. Schedule equipment downtime during low-impact periods
Scheduling maintenance during off-peak hours allows operations to continue with minimal disruption. By targeting periods of lower demand, your maintenance team can perform necessary updates or repairs without significantly losing production time.
2. Use rolling updates and staggered maintenance
Stagger work so parts of your operation can keep running. This method helps you avoid full operational shutdowns and lets your teams work on one area at a time. This time gives your team more space to conduct a more detailed assessment of each area.
3. Invest in redundant systems
Redundant systems give you a backup to use when your main equipment needs maintenance. They keep your work going without stopping, even if important machines are offline. For example, a factory might set up an extra conveyor belt that kicks in while the main one is getting fixed. This way, production doesn’t slow down for maintenance.
Key Performance Indicators for downtime
Using key indicators to track downtime helps your company understand performance, streamline maintenance activities, and make informed maintenance decisions. You can consistently monitor these indicators to improve productivity, reduce costs, and avoid downtime.
Here are three key performance indicators often used for tracking downtime:
Mean time between failures (MTBF)
Mean time between failures (MTBF) measures how long equipment typically operates before breaking down. This metric is a reliability indicator that shows whether equipment can run for extended periods without interruption.
The formula for MTBF is as follows:
MTBF = total operating time/number of equipment failures
For example, if a machine operates for 10,000 hours and experiences 5 breakdowns, MTBF would be 2,000 hours. A higher MTBF value means fewer breakdowns over time, while a lower MTBF may indicate potential issues that need attention to improve performance.
Mean time to repair (MTTR)
Mean time to repair (MTTR) tracks the average time to repair equipment after a failure occurs. Lowering MTTR helps reduce downtime and keeps production schedules on time.
The formula for MTTR is as follows:
MTTR = overall downtime/number of repairs
For instance, if a piece of manufacturing equipment experiences 5 breakdowns with a total repair time of 300 hours, the MTTR would be 60 hours.
The Cottrell Organization’s 22 McDonald’s locations used MTTR to help their operations. With the MaintainX platform, they achieved an impressive reduction in MTTR: from 400 hours to just 60 hours in four months.
MaintainX helped them eliminate the need for spreadsheets and emails. This allowed the Cottrell team to track work requirements in real-time and complete over 90% of work orders across all 22 locations within 10 months.
Overall equipment effectiveness (OEE)
Overall equipment effectiveness (OEE) is a comprehensive indicator that shows how effectively equipment operates based on three factors: availability, performance, and quality. OEE reveals the percentage of time equipment is productive and is calculated using this formula:
OEE = Availability × Performance × Quality
Here is what each factor in the OEE formula represents.
- Availability: Percentage of scheduled time that equipment is available to operate.
- Performance: Speed at which equipment operates compared to its maximum possible speed.
- Quality: Proportion of good output versus total output produced.
For example, if equipment operates with 90% availability, 95% performance, and 98% quality, the OEE would be 83.79% (0.90 × 0.95 × 0.98). A high OEE score indicates that the equipment is used effectively, with minimal downtime and high-quality output.
Optimize your maintenance processes with MaintainX
Using a computerized maintenance management system (CMMS) makes cutting downtime easier. MaintainX simplifies work orders, tracks data, and helps you plan better. Our tool also uses AI and IoT features to assist with your predictive maintenance strategy.
Learn more about what we can do for you today.
FAQs on Reducing Downtime
How can preventive maintenance strategies be optimized to minimize unplanned downtime?
Optimize preventive maintenance by scheduling regular inspections, using data analytics to predict equipment needs, and training staff to spot early signs of wear. Monitoring tools should also be used to alert teams before issues become critical. This approach keeps equipment in good shape and reduces your risk of unexpected breakdowns.
What role does predictive maintenance play in forecasting equipment failures before they occur?
Predictive maintenance uses real-time sensor data and historical performance to identify patterns that signal potential equipment failure. By analyzing this data, you can forecast issues before they happen and proactively plan maintenance schedules accordingly, reducing machine downtime.
How does effective tracking and analysis of downtime events contribute to improved production line efficiency?
Effective tracking and analysis of each downtime event helps your team identify the root cause of recurring issues that lead to machine downtime. Understanding these patterns allows you to address specific problems, make targeted improvements, and adjust schedules or processes as needed.
Why is maintaining an efficient spare parts inventory crucial for reducing machine downtime?
Maintaining an efficient spare parts inventory ensures that replacement parts are available when needed. Having the right parts ready avoids delays and speeds up maintenance work. As a result, you can reduce the length of time that planned machine downtime lasts. Plus, you’ll save money when you don’t have to rush order items. In fact, the State of Industrial Maintenance Report found that 58.9% of facility managers say that better inventory management helped lower their costs.
How can real-time monitoring be leveraged to prevent unexpected equipment failures?
Real-time monitoring tracks equipment performance continuously and immediately detects unusual patterns or signs of wear. You will then receive an alert as soon as potential issues are detected. So, you can solve the emerging issue before it leads to an unplanned machine downtime event.
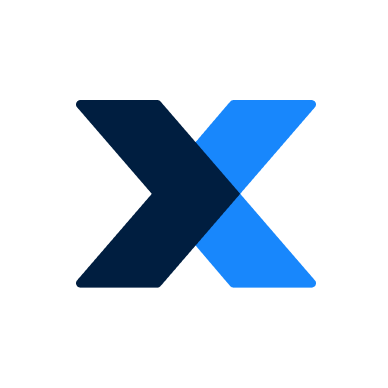
The MaintainX team is made up of maintenance and manufacturing experts. They’re here to share industry knowledge, explain product features, and help workers get more done with MaintainX!