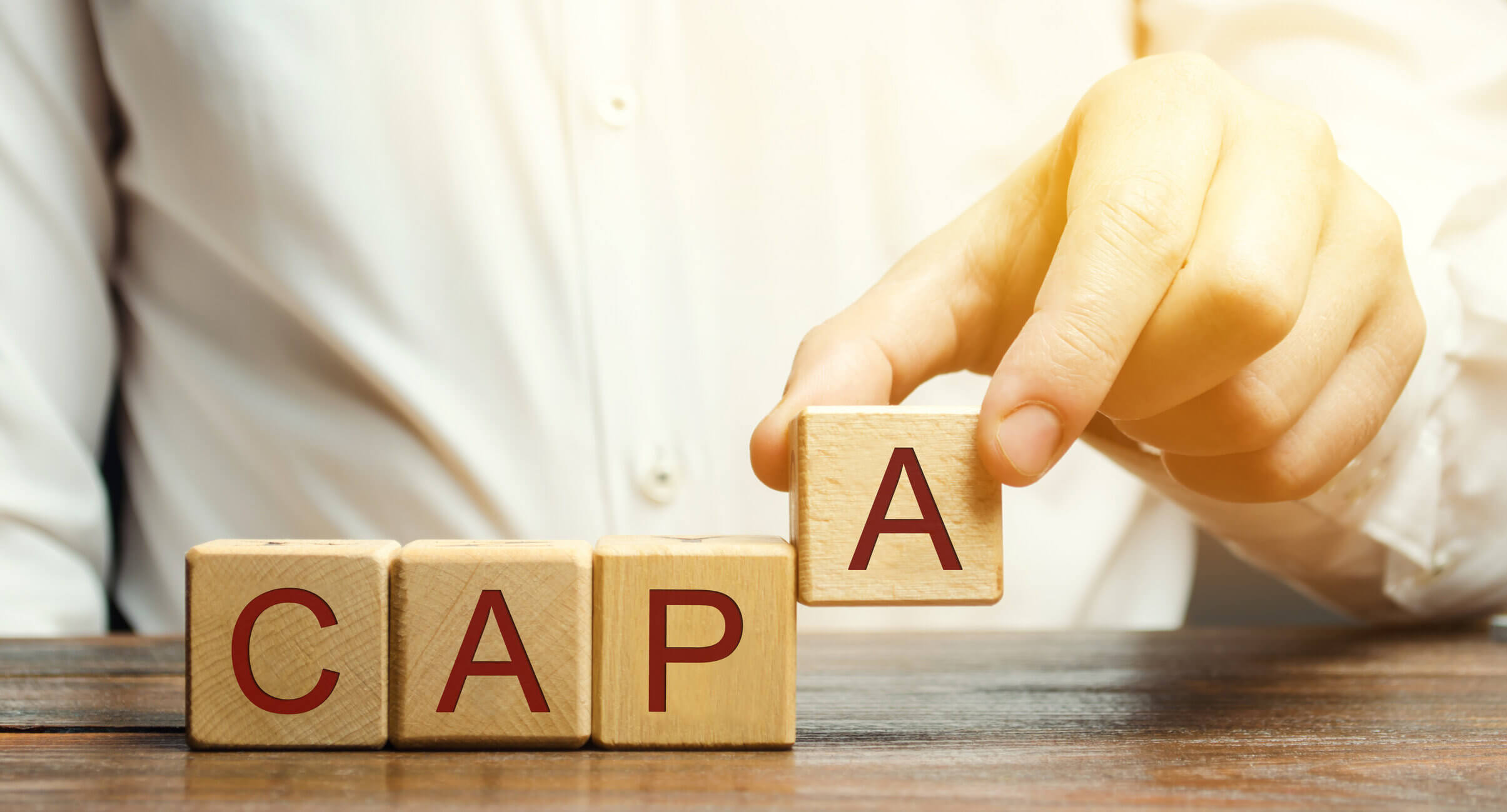
Corrective and Preventive Action (CAPA) refers to the steps your company can take to improve its processes and eliminate unwanted occurrences. These unwanted occurrences can be non-conformities (deviations from standard expectations) or any other undesirable situation. Examples of non-conformities include:
- Asset breakdowns
- Downtime
- Faulty products
- Supply chain interruptions
- Non-compliance with regulators
- Negative feedback
- Customer complaints
Corrective Action vs. Preventive Action
Corrective action aims to prevent issues from arising again, while preventive action seeks to prevent potential issues from coming up at all. In other words, you carry out preventive action to head off any failure, interruption, or undesirable event from happening in the first place.
Corrective action meanwhile takes place after an unwanted occurrence of, say, equipment failure, negative feedback, or costly downtime. In essence, if you don’t work to prevent the bad stuff from happening in the first place, you may be faced with a problem that you need to correct after the fact.
Not to mention, even if you try to prevent any problems, issues do come up. So while creating a preventive action plan, you can also make plans to handle potential nonconformity.
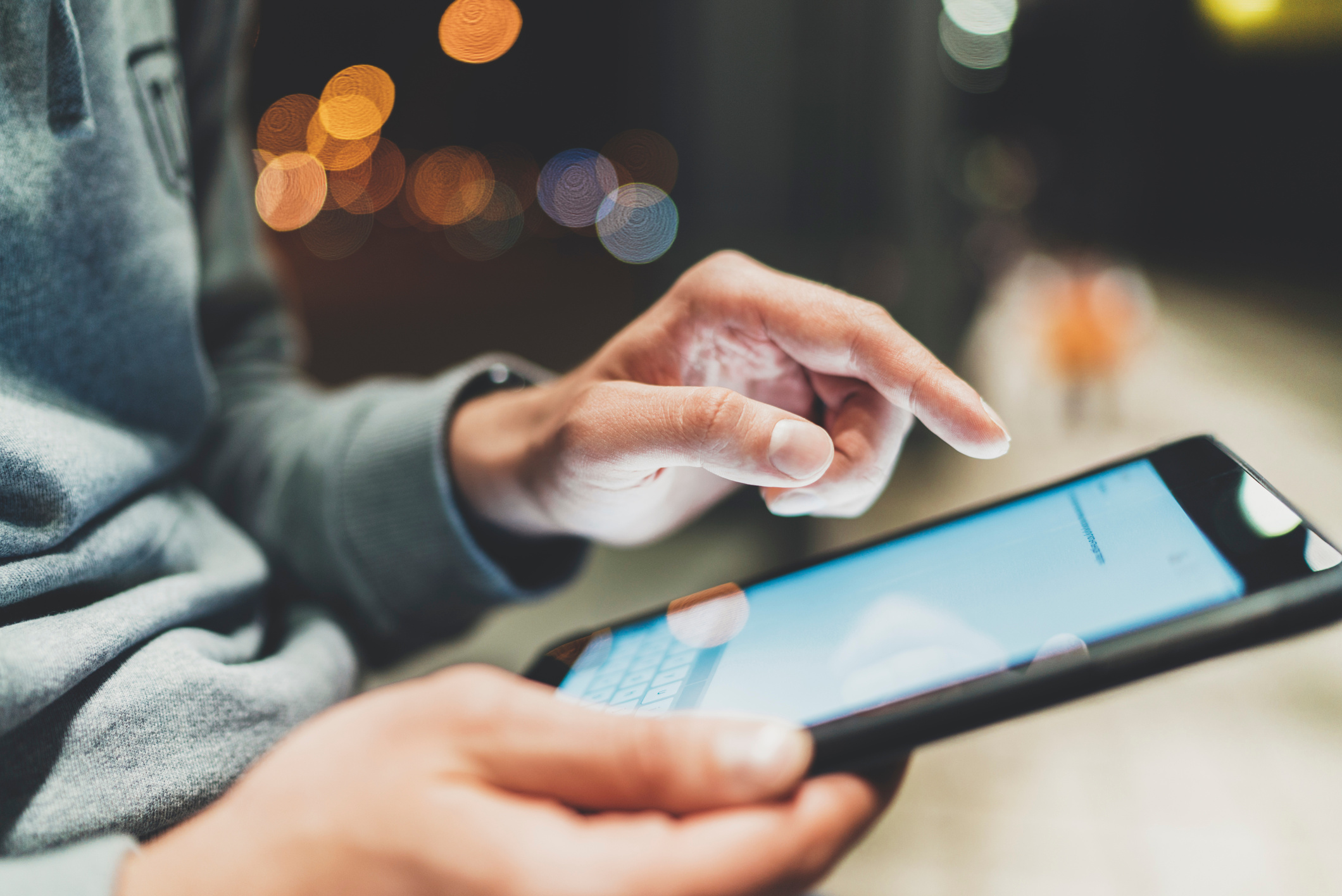
Why Bother with CAPA?
CAPA includes rules, regulations, processes, procedures, and systems that companies and teams apply internally to prevent unwanted occurrences. However, in some cases, CAPA goes beyond a company’s decision to improve itself, and external regulators require it.
For example, in the USA, the Food and Drug Agency (FDA) requires medical device companies to establish a CAPA plan within their Quality Management System (QMS). A company’s failure to address a non-conformity by recording and carrying out a root cause analysis can lead to regulators naming its medical devices substandard. CAPA must also comply with International Standards Organization in ISO 9000 and ISO 9001.
What Is the CAPA Process?
Your CAPA process is a function of your specific team and organization. When designing the process, start by putting together a team involving quality assurance workers, senior management, and floor staff.
The work of you and your team is to take into account your unique production circumstances and regulatory requirements. Then, create an action plan to address potential problems. This action plan may prove crucial for regulatory audits and inspections.
The Eight Disciplines (8D)approach is one method for structuring a CAPA plan for your business. It was developed at Ford Motor Company and used to approach and to resolve problems, typically employed by quality engineers or other professionals.
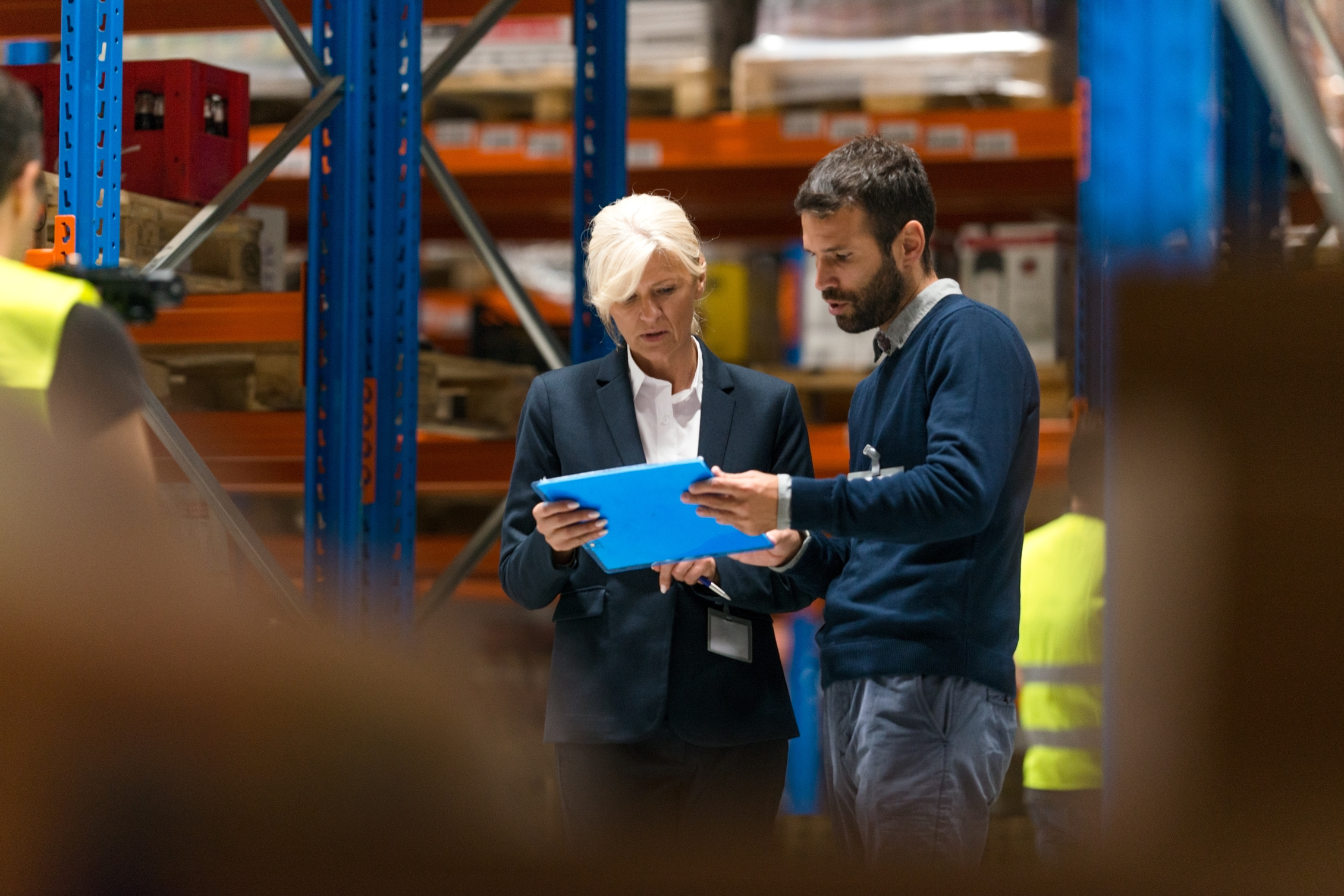
The Eight Disciplines
The eight disciplines model is a problem-solving approach aimed at process control and continuous improvement. According to the American Society for Quality (ASQ), “The purpose of the 8D methodology is to identify, correct, and eliminate recurring problems, making it useful in product and process improvement.”
The eight disciplines are actually nine today, now including an initial planning stage. The disciplines are:
D0: Plan
Here, you plan to solve the problem and determine the prerequisites. This stage also involves preparing your approach to respond to emergencies.
D1: Use a Team
You’ll need to put together a team of different workers with knowledge of your products and processes.
D2: Define and Describe the Problem
Here, you’ll need to specify the problem in concrete and quantifiable terms. For example, you want to answer the who, what, when, where, why, how, and how many for the problem. Tools you can use here include the 5 Whys, Affinity Diagrams, and Fishbone diagrams.
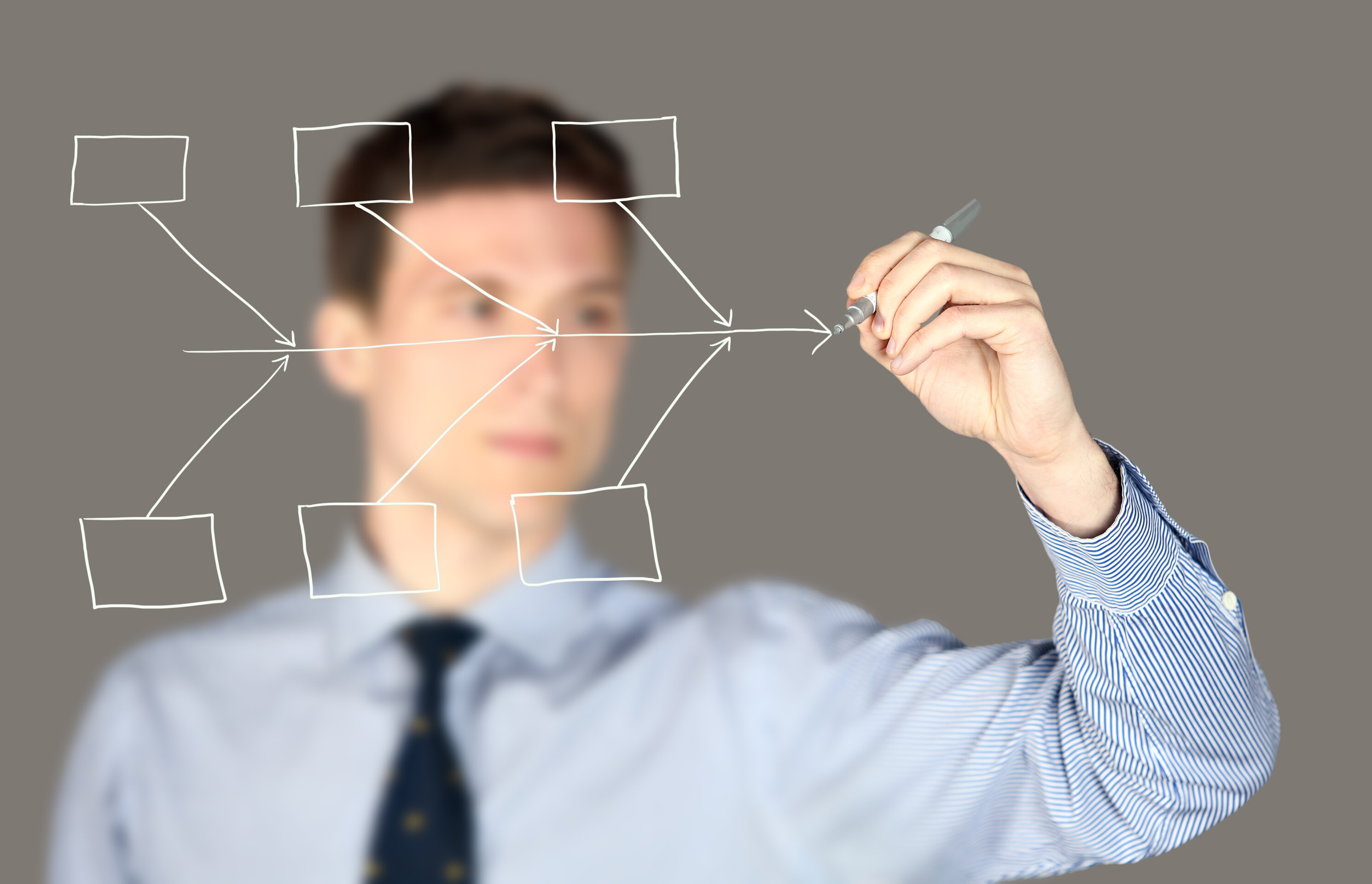
D3: Develop an Interim Containment Plan
Addressing the root cause of the problem may take some time to think about. So give yourself the time it takes to develop a plan to keep the problem from the customer for the time being.
D4: Determine, Identify, and Verify Root Causes and Escape Points
Here, you need to figure out why the problem happened. Take a close look to work out the cause of the nonconformity. Also, determine why the problem escaped your attention before. Importantly, when determining the cause of a problem, teams need to rely on verifiable evidence and not guesses, no matter how strong the guesses.
D5: Choose and Verify Permanent Corrections for Problems
Plan on what corrections to make. This stage involves significant risk-based thinking. To avoid wasting time, you need to verify that the corrective actions will lead to customer satisfaction.
Using pre-production diagrams is a good idea here. This way, you’ll have the quantitative assurance that the correction you want to implement is the right one. You’ll also want to carry out a risk analysis or a Failure Mode and Effects Analysis (FMEA) on the corrective actions you’ve devised.
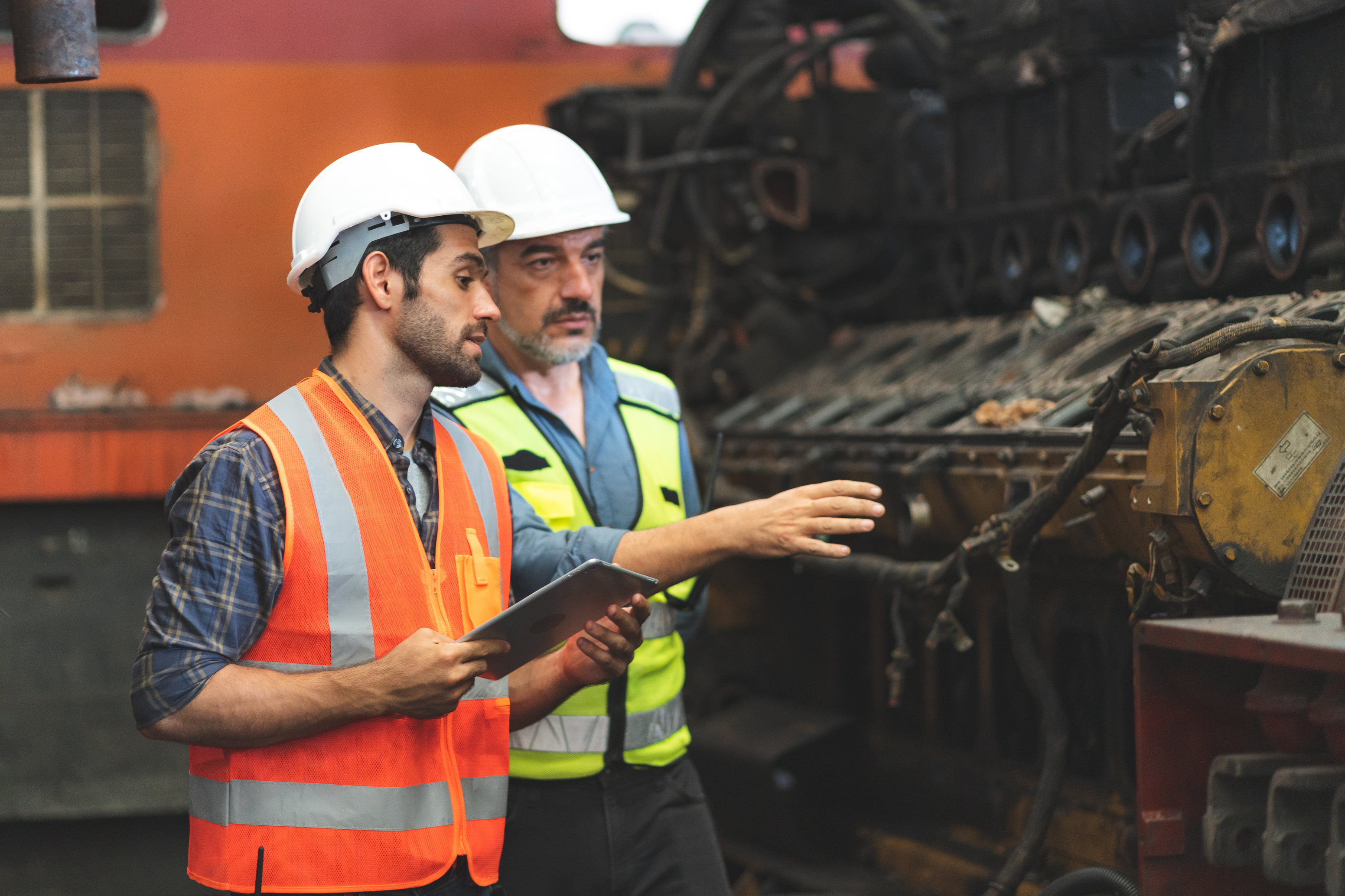
D6: Implement and Validate Corrective Actions
Carry out the corrective maintenance process. By this point, you should have created a detailed implementation plan and communicated this plan to all stakeholders. After implementing your corrections, use empirical measurements to verify the results. By empirical evidence, we mean measurements or data collected through direct observation., You need to see it to believe it, in other words.
D7: Take Steps to Prevent Recurrence
When you’ve completed the changes and verified your results, put the whole process through a management review. Through this, you can define your preventive action process and modify your management systems.
Organize your operations systems and quality systems to ensure you don’t have to deal with this particular nonconformity again. Also, define your risk management process for whenever you need to make changes in the future.
D8: Congratulate Your Team
Be sure to give your team members positive feedback on the process. Recognize the achievement of the team as a whole and any specific individuals who were all in. Finally, document any lessons learned and archive (and digitize) them for future reference.
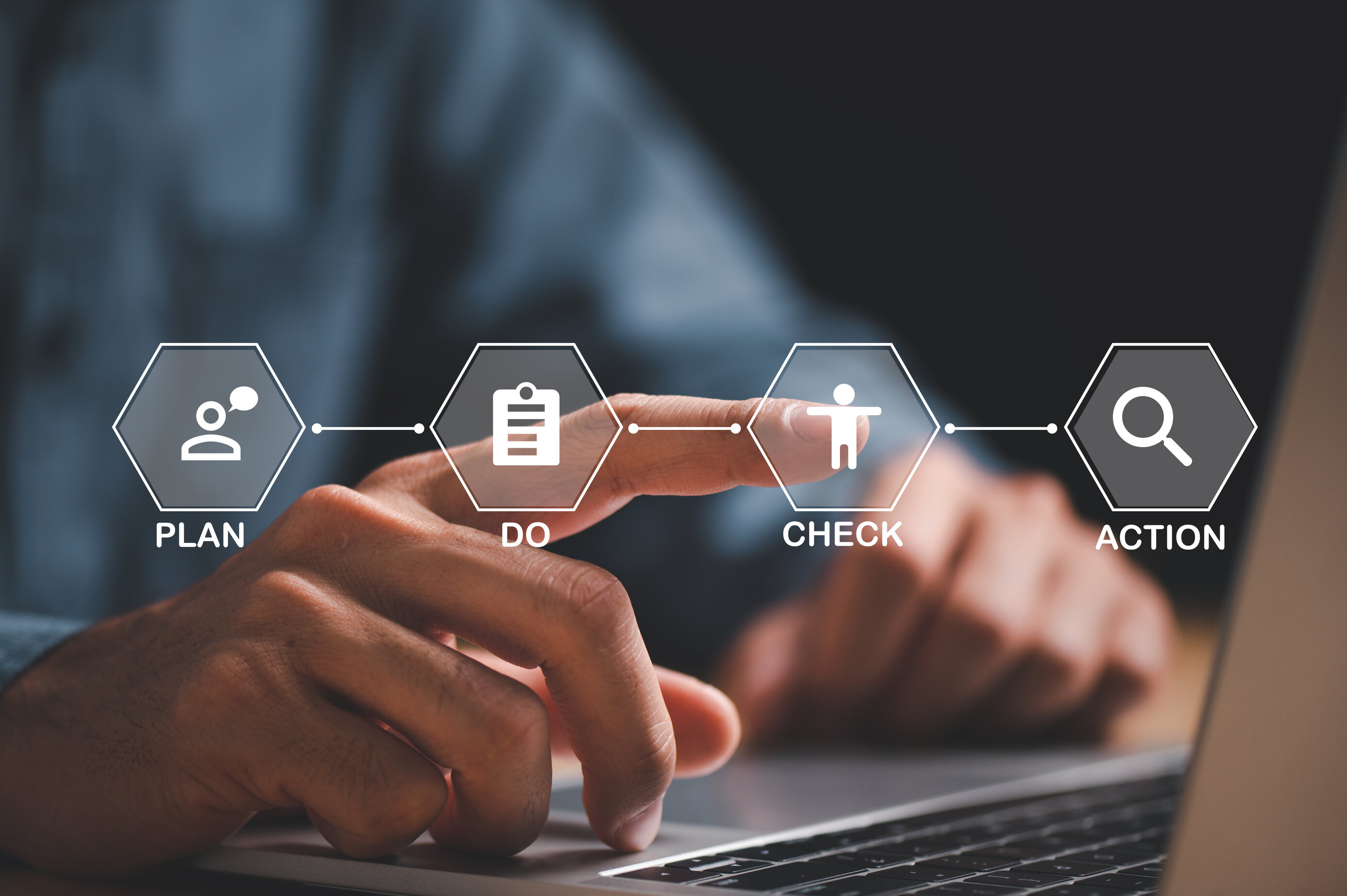
Or, Try PDCA
Another approach to corrective and preventive action is the PDCA cycle. The PDCA model is an essential part of the lean manufacturing philosophy and well-known concepts like Lean Six Sigma and Kaizen.
PDCA stands for Plan-Do-Check-Act. The model is made up of the following stages:
Plan
In this planning stage, you form a team to determine your current and intended future state. Proper planning prevents poor performance, so it’s worth giving this step the time and energy it deserves. Here you determine the baseline, plan what resources are needed, and consider how you will measure success.
Do
This stage involves testing out the solutions in a small-scale pilot form. The stage may take time because it can involve changes to production or maintenance processes or training staff on new work practices.
Check
After implementing the solution, carry out a follow-up effects analysis to make sure it works. You’ll find out if your early planning worked in the check phase. Did you reach your expected goal? What challenges did you encounter along the way? Finally, compare your results with the current business-as-usual process.
Act
After drawing conclusions from the data and deciding that the new approach will be successful, it’s time to act. Remember, the plan-do-check-act cycle is an iterative process. You may need to start over with a new plan if you haven’t found a satisfactory solution.
Regardless of the outcome, the information you have extracted from the testing process can be recorded and applied to your continuous improvement processes, bringing you back to the beginning of the PDCA cycle.
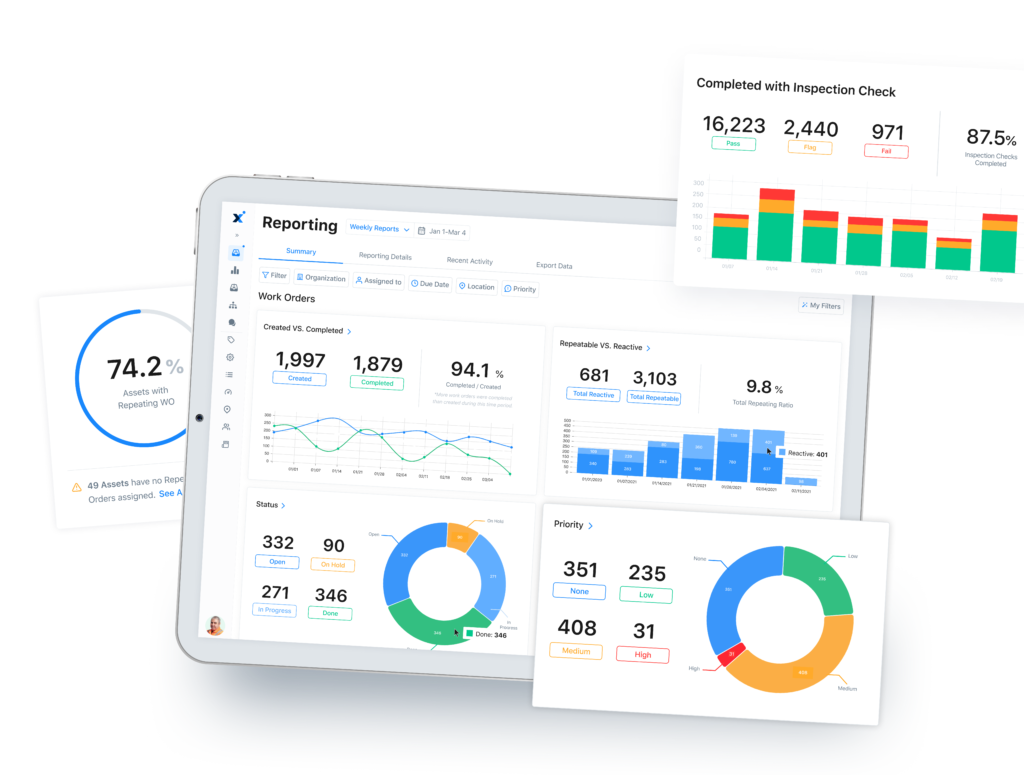
Use a CMMS to Optimize Your CAPA
A computerized maintenance management system (CMMS) is a software tool that can help you with your corrective and preventive actions. A robust CMMS helps organizations manage maintenance activities and equipment more effectively and can provide you with a range of benefits for preventive maintenance.
First, the right CMMS will provide a centralized digital platform for managing your corrective and preventive actions. Whether you apply PDCA, the Eight Disciplines, or some modified version of either, a good CMMS will help you streamline your activities.
MaintainX, for example, can automate your preventive activities and provide real-time tracking for your work orders and activities. Not only will this keep you in compliance with regulations, but you’ll also see reduced downtime and an improved bottom line.
FAQs
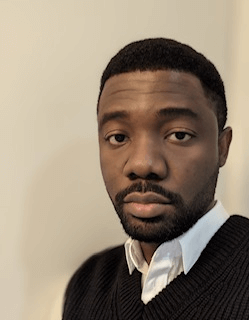
Lekan Olanrewaju is a content writer with years of experience in media and content creation. He has held positions at various media organizations, working with and leading teams at print magazines, digital publications, and television productions.