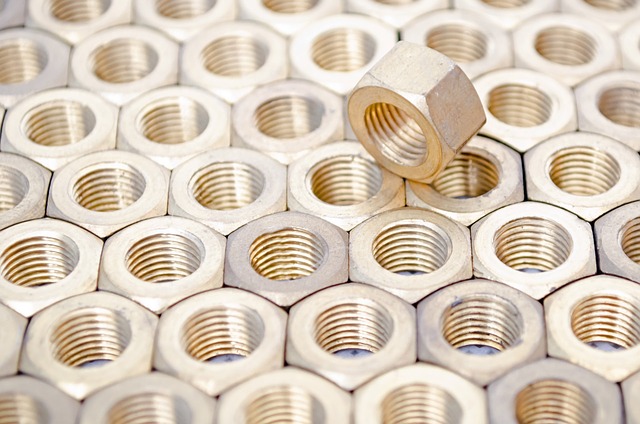
Materials inspections are similar to taking a flight on an airplane. The ideal scenario for both is an uneventful outcome—they are both means to a greater end. If an issue arises, it creates a series of headaches for all parties involved. While we can’t prevent issues with your next flight (at least until every airline uses MaintainX!), we can help streamline your materials inspections and build a repeatable process to success.
Whether your team conducts Materials Inspections for ISO compliance or to maintain internal quality standards, this article will help you get started and provide tips on best practices to help you improve.
What is A Material Inspection?
A material inspection is the process of examining and evaluating the physical and chemical properties of a material to ensure it meets specific standards, specifications, or product quality. This process is commonly employed for quality assurance in a number of industries such as manufacturing, construction, aerospace, automotive, and more.
For those who don’t have regulatory reasons to conduct materials inspections, you may be wondering why it’s worth the hassle. The simple answer is that it will help your team deliver the best results to your customers.
Regardless of your industry, it’s increasingly becoming more important to perform a quality audit on your suppliers. Even markets like Amazon are dealing with increased rates of fraud on items that were previously very trustworthy to bypass an inspection upon receipt. Based on the type of materials you are bringing in, you may find it useful to build a few unique materials inspection checklists on what is important to check.
It is also important to be aware of industry-specific guidelines. For example, the auto industry has a QS-9000 Certification. Anyone in the auto-industry supply chain who receives materials or parts that have previously been certified might be able to run these audits less frequently.
However, if you fall into the majority, your company likely buys most supplies from uncertified sources and will want to perform random inspections to ensure your supply chain doesn’t cost your business.
Why Material Inspections Are Necessary
There are several situations where you want to be sure to carry out material inspections.
Foreign Suppliers
Chances are some of your suppliers are foreign. Many foreign countries simply don’t have the same standards we have in North America.
Assuming the raw materials you source from these countries will meet the type of quality standards you have could be a grave mistake. If your organization is in the habit of renegotiating your cost down (and really, who isn’t trying to do that), you may set yourself up for a situation in which the supplier can’t afford to provide you with the best quality materials or parts.
If you end up paying the price with unsatisfied customers, material inspections might be worth the time after all. A bit of a vicious cycle, right?
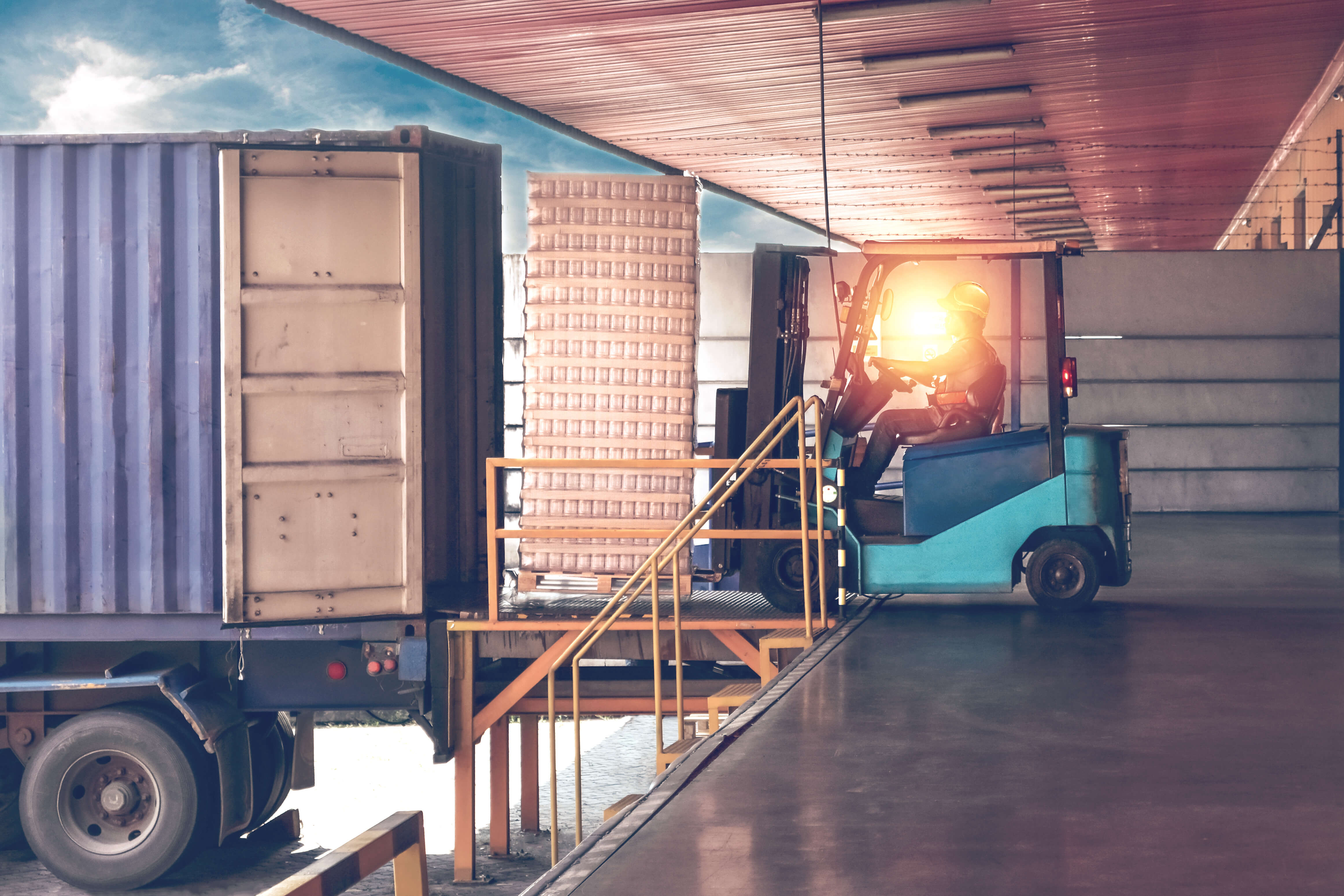
Quality Fade
Quality fade, sometimes also called quality creep, is something most of us have faced, at least as consumers. We purchase a product that we’ve been buying for years only to find that it doesn’t quite hold up and perform the way it used to.
This is because the manufacturer is either knowingly cutting costs or has received substandard materials and hasn’t been doing its own proper materials inspections.
While quality fade is known to be a problem with material sourced internationally, it is increasing domestically as well.
Over time there is a very subtle but progressive degeneration of quality. If your company isn’t diligent about materials’ quality management, you could miss this slow-moving trend toward substandard materials.
The Costs
Make no mistake. There will be costs involved when you implement a materials inspection strategy. Time put into effective inspection protocols and then the time required to perform them isn’t free.
However, the money you ultimately save could far outweigh your initial outlay in setting up and implementing your inspection strategy. For example, the Jesse Garant Metrology Center points out that the aerospace industry saves $1,000 for every $1 it spends inspecting for material defects before materials make it to the production stage. It’s not hard to imagine how even years of non-incidents with inspections can be offset by catching an issue that prevents a large-scale disaster.
Clearly, a material inspection is imperative to the quality-control process.
Certified Off-Site Material Testing
Since material testing is a critical step, you should note that in some cases, it’s not feasible or reliable to have certain materials tested in-house. For example, is your facility ready for, and do your local employees have the training to do, a complete analysis of chemical components? This could include testing for trace contamination and the process of identifying unknown substances.
If your answer to this is “no,” then you need to have your materials checked and tested at a certified lab that can handle the job.
So understand that there will be circumstances when third-party material inspection services are necessary.
The method you use to test and inspect can and may vary by product, but inspections will help you verify that your incoming components and materials meet the requirements of your final product.
Methods of component or material testing include:
- Chemical analysis
- Testing physical properties and measurements
- Testing mechanical properties
- Regulatory testing
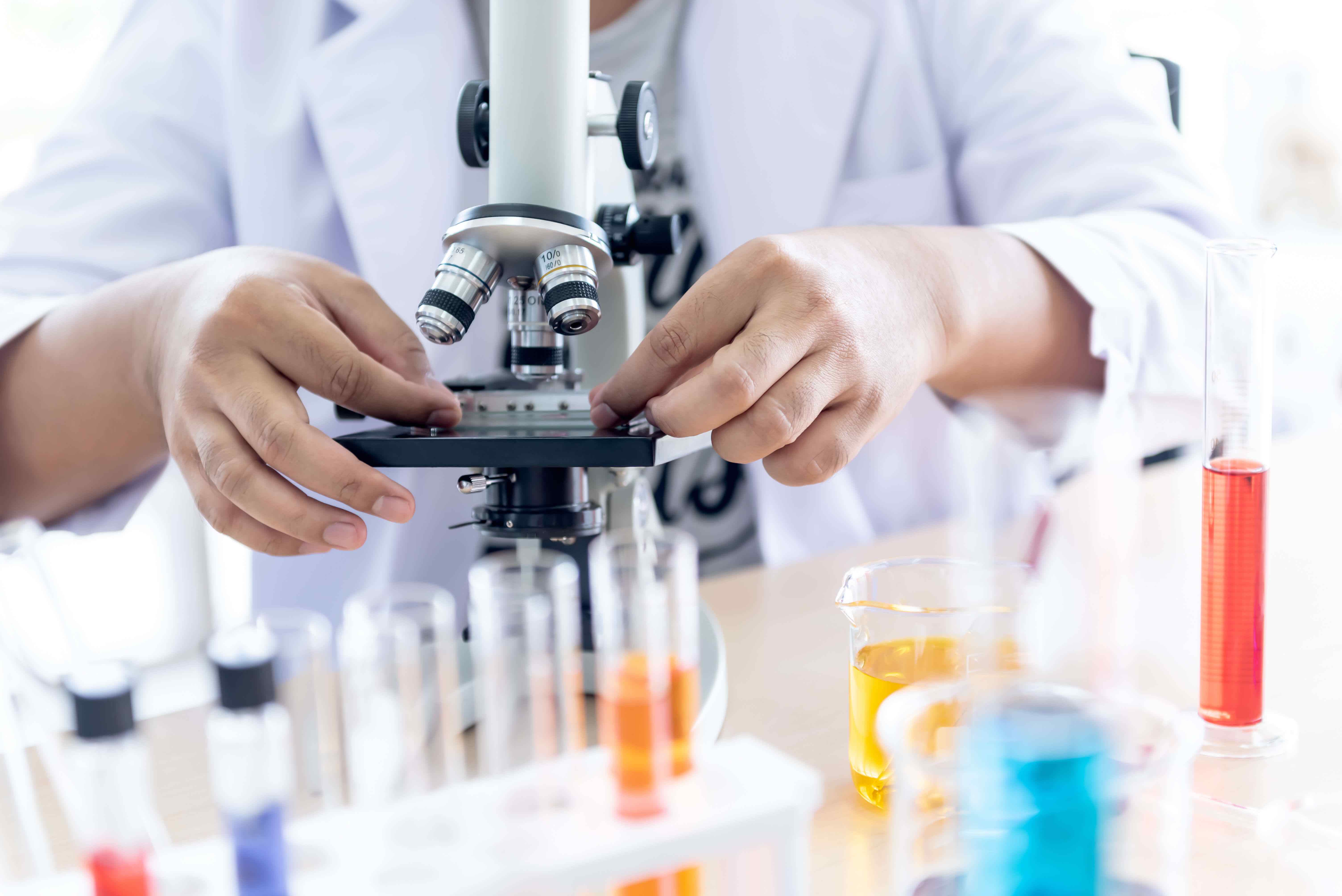
Material Inspection Procedure
1. Pre-Inspection Steps
You may have heard people refer to materials inspection as an inbound or receiving inspection because some steps occur before the actual inspection.
Your receiving department will have its own inspection procedure that will include things like verifying and recording the quantity received, the referencing purchase order number, and whether or not the material order is complete.
2. Photos
It’s a very good idea to capture photos or videos upon receipt of the materials. An easy way to do this is to use a tool such as MaintainX that enables you to capture photos, tag them, and store them within each inspection form.
3. Review Project Specifications
This is a critical step, and it needs to be performed before you start your physical inspection. You need to know the set specifications of your project in order to know if the materials you received fall within tolerances. Receiving a part or component—whether it’s a piece of metal or a liquid chemical—that falls outside of agreed-upon standards should never pass inspection.
Once you know the project’s specifications required of the materials, you can confirm whether they comply with the requirements of the contract and purchase order.
4. Physical Condition of Material
Create a sampling process where you randomly pull materials and check their physical condition. How this is handled will clearly depend on the material, and it doesn’t necessarily mean you have to eyeball every single piece that was delivered.
Apply a set criterion, which, if it isn’t met, means the shipment isn’t fit for production.
5. Make and Manufacturer
This is a fairly simple step. Confirm that what you received is from the confirmed manufacturer or trademark holder.
6. Certifications
If the materials you are receiving should meet specified standards or material certifications—for example, UL or CSA—make sure they are appropriately marked.
7. Storage Requirements
Assuming your materials have passed inspection, check for any special storage requirements. If so, materials should be marked or tagged appropriately.
It may even be wise to include a final photo requirement to show the materials in the place where they need to be—if a shipment of refrigerated produce arrives cold, but sits in receiving for 24 hours before being stored properly, this defeats the purpose of the whole inspection.
The Importance of Material Testing
Whether your product is bound for an end consumer or another manufacturer in the supply chain, it’s critical to test the materials coming in so the product you ship out meets quality and safety standards.
A materials inspection report will help to catch defects before production starts. And remember, a business with quality material inspections is a business that grows.
Let MaintainX Manage Your Inspections
If you have all of your quality control processes in place, inspections won’t be something to fear. Instead, you’ll want to put the test results right up on your office wall for everyone to see.
Consider integrating a CMMS to ensure your business operates efficiently–even within a highly regulated environment. A robust CMMS like MaintainX can help streamline your entire manufacturing and maintenance cycles. The choice is yours. You can view customer inspections—or any inspection—as an opportunity to confirm that all is well.
FAQs
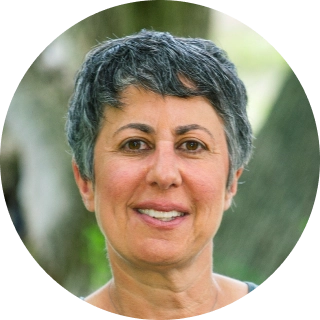
Caroline Eisner is a writer and editor with experience across the profit and nonprofit sectors, government, education, and financial organizations. She has held leadership positions in K16 institutions and has led large-scale digital projects, interactive websites, and a business writing consultancy.