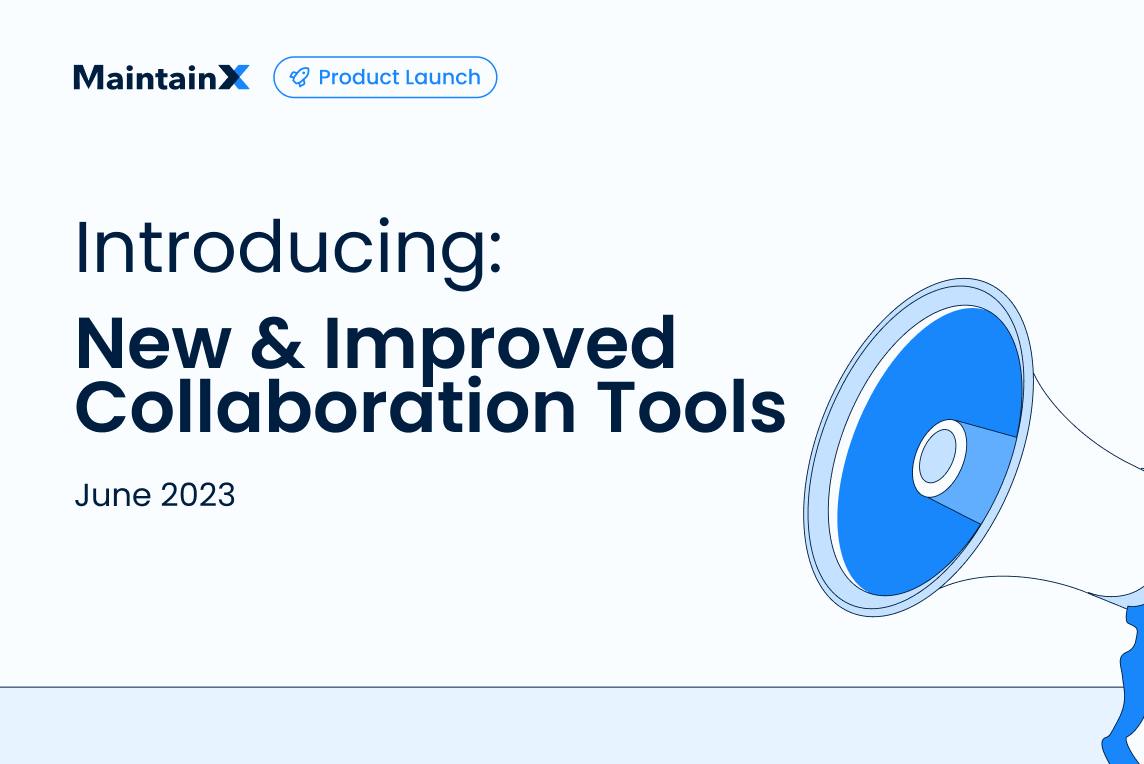
Digital collaboration has transformed the workplace in almost every sector, providing faster, more effective alternatives to phone calls and meetings.
Real-time information exchange is particularly critical to maintenance teams. Manufacturers and facilities face the risk of unexpected shutdowns every day, and they do so with an aging workforce and a shrinking pool of skilled workers.
McKinsey predicts digital collaboration boosts productivity by up to 30 percent for maintenance teams, partly by allowing factories to “better leverage their experts across a broader group of people to help train the less experienced workforce.”
But even maintenance managers using a CMMS and instant messaging software would agree that communication challenges remain a leading cause of delays and mistakes–which can be costly.
These challenges can occur for several reasons. When teams communicate across multiple systems, essential knowledge is scattered and can’t always be retrieved quickly enough. Digital tools also can lead to unnecessary interactions or notifications that can distract technicians from their most important tasks.
That’s why our philosophy at MaintainX is to streamline communication and bring it as close as possible to where the work is actually happening. MaintainX is already unique in the way it helps maintenance teams share information in real time and quickly retrieve historical records to get things done faster and safer.
And today, we’re excited to announce that we’ve doubled down on digital collaboration with a package of new features to help your team respond faster to change and reduce your mean-time-to-repair (MTTR).
This includes:
- Request Routing: Improve response times by allowing requests to be assigned to specific teams.
- @Mentions: Grab the attention of other users faster by tagging them in Work Order comments and instant messages.
- Improved Notification Controls: Stay focused on the most important updates by controlling when and where notifications are sent.
Streamline Communication from Request to Resolution
We know that delays can happen, from when a person first identifies an issue to when a tech resolves the issue to when the resolution is communicated back to the person who reported it.
Without an efficient process to manage maintenance requests, requests can sit around for hours or even days before they’re picked up and actioned. As a result, supervisors can get bombarded with irrelevant requests, and requesters can be left in the dark as to why their request isn’t being fulfilled.
MaintainX’s new Request Routing allows requests to be assigned to specific teams, accelerating the approval process. Approvers are notified when a request has been assigned to their team and can quickly distinguish these requests from others they’ve submitted. Request Routing helps supervisors focus on the requests that matter to them, while minimizing distractions.
With Request Routing, requesters receive automatic notifications when their request is declined, minimizing back-and-forth and helping to reduce frustration.
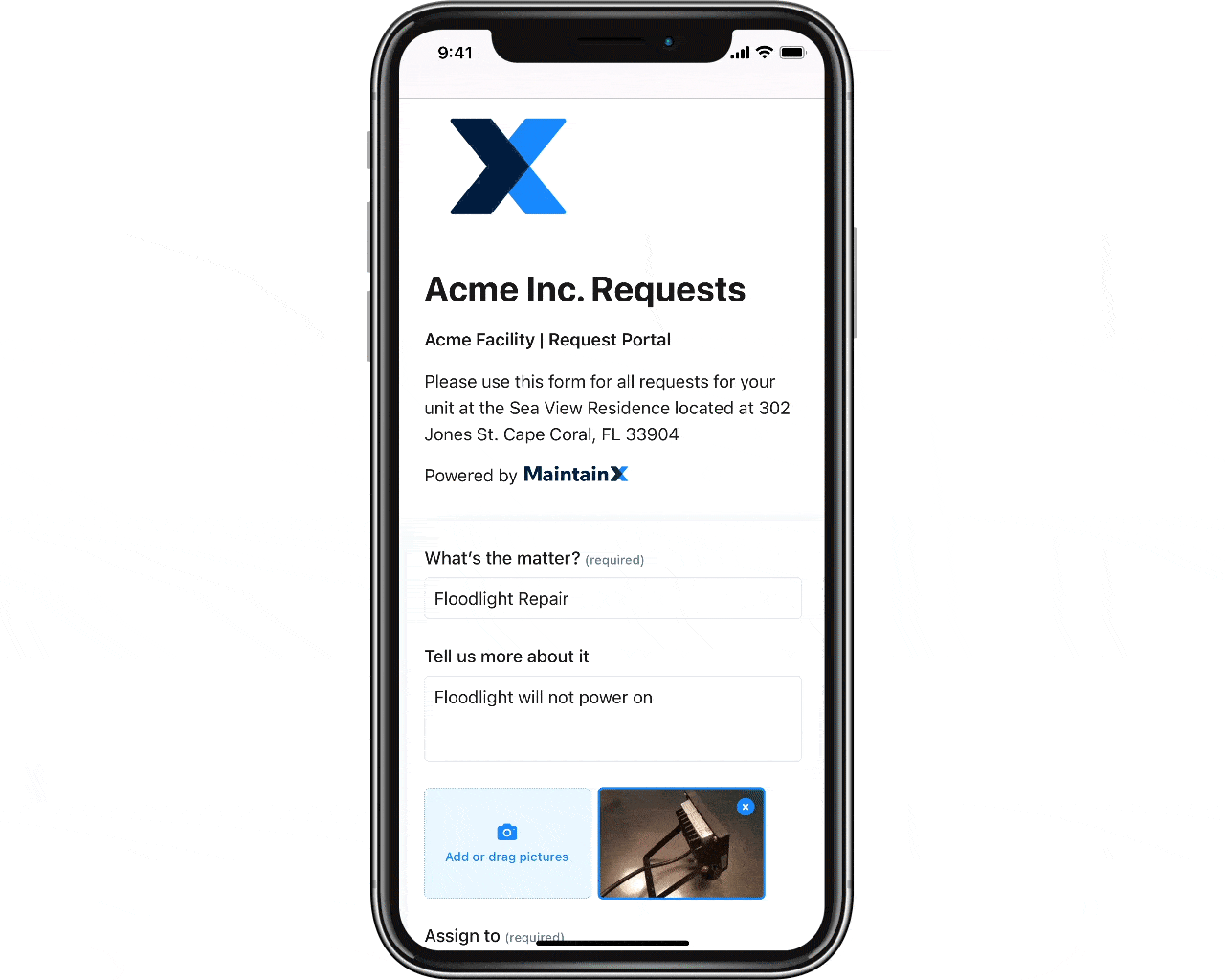
Grab the Attention of Coworkers Faster with @Mentions
When time is short, email and voicemail messages simply don’t deliver answers quickly enough. And on chaotic days, it can be challenging to keep track of updates even within MaintainX.
To help technicians connect faster with key people and information, we’ve introduced @Mentions on Work Order comments and instant messages. This allows you to tag other MaintainX users in your message, notifying them immediately of something you want to ask them or bring to their attention.
@Mentions can be used to get information for something urgent or when you just want a coworker to be aware of something. Just hit the @ key in a comment or message, or you can select another MaintainX user to notify.
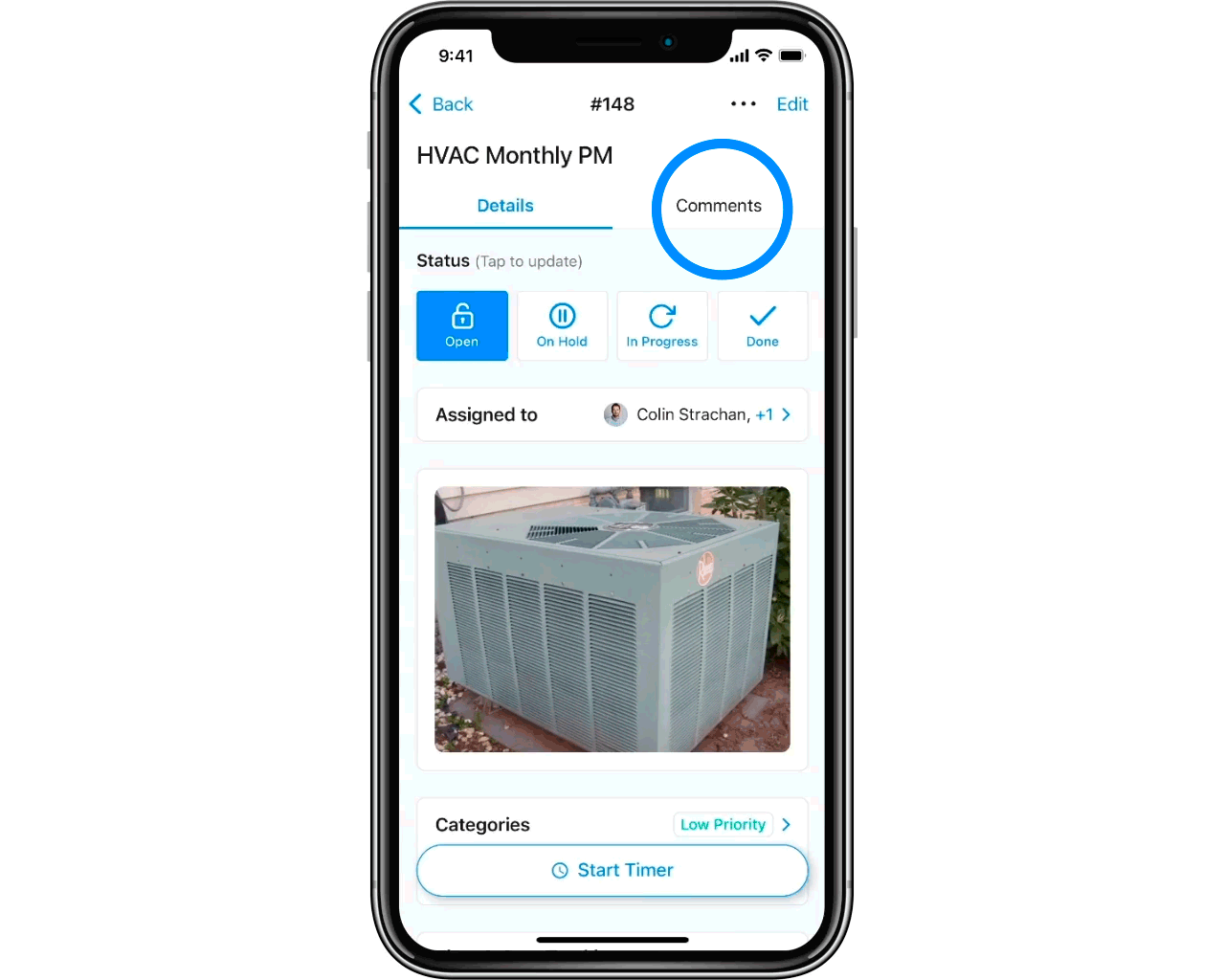
Stay Focused with Improved Notification Controls
Keeping supervisors and technicians in the loop is a balancing act. They need to be aware of developments that matter to them, but they should also be protected from information overload, which can cause distraction and fatigue.
And so, to complement these new methods of sharing updates with coworkers, we’ve also introduced new controls over which notifications you receive and where.
Your notification settings in MaintainX now allow you to control which Work Order updates you’re notified about and whether the notification should be sent by email or just within the MaintainX app. In addition, you can now control the notifications you receive as instant messages.
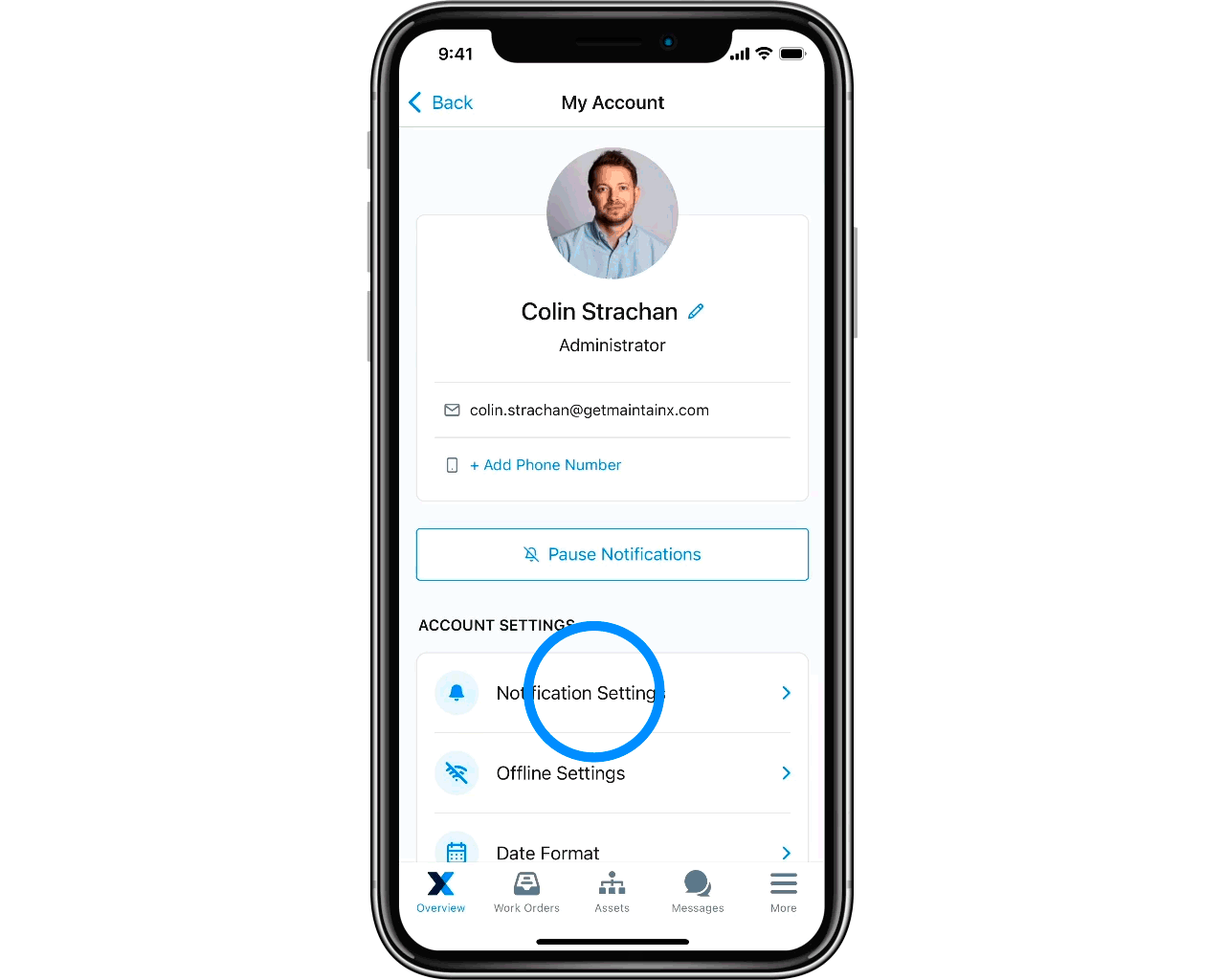
Foster Better Communication, Collaboration, and Team Engagement
MaintainX enables maintenance teams to react faster on the shop floor. Our customers also report happier and more engaged workers, thanks to the transparency and connectivity that MaintainX brings to frontline teams.
Keen to know more about how MaintainX drives down mean-time-to-repair (MTTR) by fostering better team collaboration? Book a demo today, and we’ll show you.
FAQs
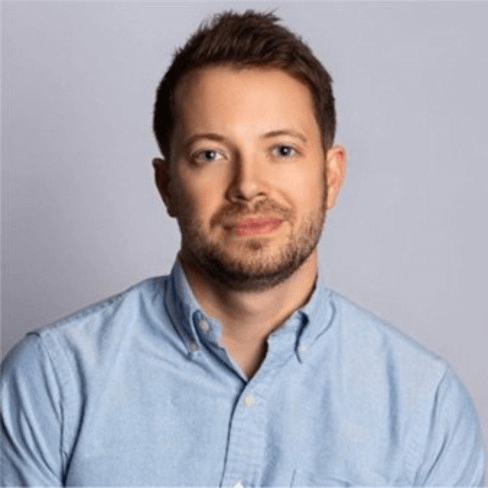
Colin Strachan is a Senior Product Marketing Manager at MaintainX, with a background in journalism and almost a decade of experience in SaaS marketing. In the past few years, he has worked with some of the world’s largest enterprises to adopt software that empowers their employees to work more effectively.