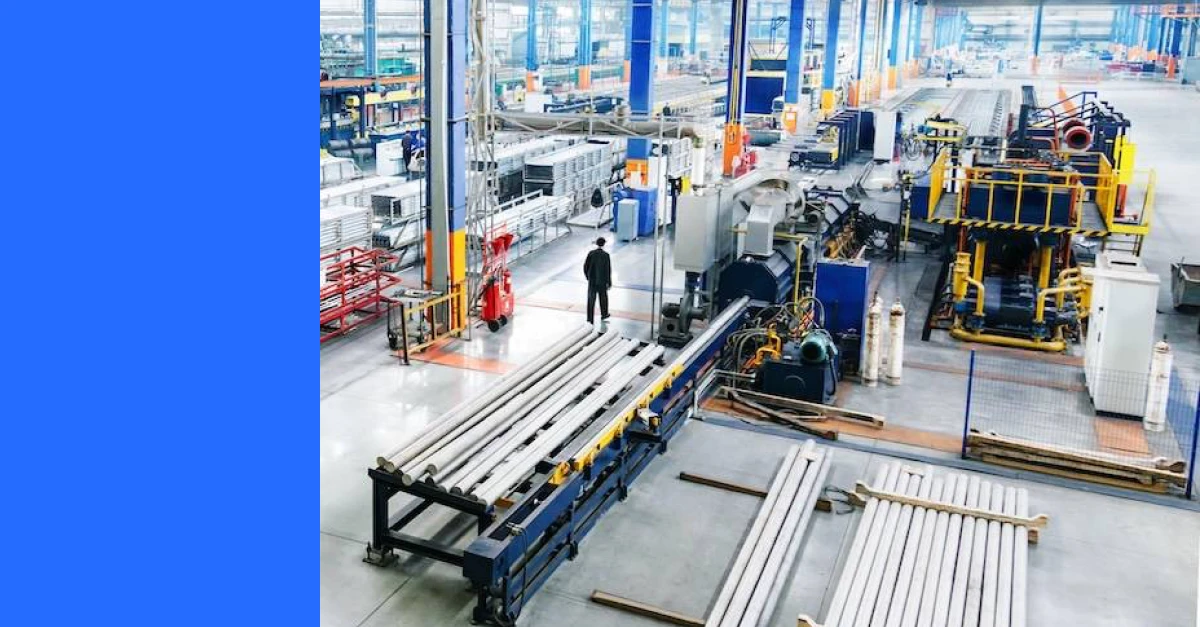
While downtime is dropping for most maintenance teams, it’s also becoming more expensive, which gives the battle against breakdowns even higher stakes. This is the story of four maintenance teams that answered this challenge and reduced downtime with MaintainX. It’s also a blueprint you can use to stop reactive maintenance in its tracks.
Before and After MaintainX: A Snapshot of Conquering Downtime
Interroll: A global manufacturer stuck with software that caused downtime
Interroll’s team was spending more time on workarounds to their maintenance software than using it. The system didn’t work on mobile devices, making it impossible for technicians to use it on the floor. Even when the software did work, it was frustrating to use. This caused work to be missed, downtime to increase, and response times to grow.
“[The team] was using other systems to make requests because it was quicker than finding a computer and navigating the system,” said Scott Quesenberry, Lean Engineer at Interroll.
The maintenance leaders decided it was time to change. When searching for a new platform, they prioritized ease of use, scalability, support, and customization. MaintainX checked all boxes, winning them over with its intuitive design, versatility, quick adoption (4 weeks!), and innovative roadmap.
“We wanted a partner that would grow with us and…provide continuous improvements that would help us optimize maintenance operations,” said Elisabetta Brunetti, Interroll’s Global IPS Director.
Once onboarded with MaintainX, Interroll centralized maintenance management, audit tracking, and reporting, allowing them to eliminate multiple tools. Techs were also able to report issues in real time with photos and videos, improving response times. The result was a 20% reduction in unplanned downtime, software savings of $10k, and a 250-hour decrease in admin work.
“Now, requests are submitted within two or three minutes, get approved, and are assigned to a maintenance team,” said Scott, “which helped improve downtime and reaction time by 20%.”
Future Foam: A Foam Manufacturer Missing Works Orders, Parts, and Targets
Future Foam’s maintenance team was constantly in reactive mode. They had no visibility into at-risk machines, real-time work order data, and parts availability. Without a centralized system, preventive maintenance was missed, breakdowns piled up, and emergency orders became routine.
“[In one example] we had a machine overdue for maintenance, and two weeks later, it went down because we didn’t have the work order data,” said Ernie Plemmons, Equipment and Supply Manager at Future Foam.
The team needed a way to stay ahead of problems and chose MaintainX to do that. They used MaintainX to create centralized asset histories, preventive maintenance schedules, and inventory tracking. Its mobile app allowed techs to access SOPs and work orders from the floor, while the reporting tool provided insights to improve efficiency and procurement across sites.
“I can now look at future work orders and anticipate our needs weeks in advance,” said Ernie.
Future Foam has adopted MaintainX at 22 sites to manage over 19,000 work orders. Reactive maintenance is down 35%, costly emergency parts orders are nearly eliminated, and auditors now receive maintenance logs with just a few clicks.
“It’s a completely new environment,” said Ernie. “There’s no scrambling for paperwork. I can make sure we have the parts we need. It’s a huge help.”
Tosca: A Plastics Manufacturer Drowning in Paper Work Orders and Downtime
Tosca’s maintenance team had a CMMS that was so difficult to use, they were forced to print, sort, and hand out paper work orders every day. Not only did this slow technicians, it also led to lost work orders, inconsistent tracking, and a gap in KPIs. The result was persistent downtime and no way to find the root cause. Plus, it made audits and reporting painful to prepare for.
“An Excel file would have been better than that system,” said Lily Burkett, Tosca’s Process Engineer.
Tosca knew it needed a solution that was easy to use, mobile-friendly, and scalable across facilities. MaintainX was the obvious choice. The platform allowed frontline workers to create and complete work orders in seconds. It also helped managers see real-time data on maintenance performance and quickly prepare for audits. Plus, every site could tailor standard processes to its PM schedules.
“Once I saw how easy it was for people to use MaintainX, there was no question [it was the right choice],” said Scott Schneider, Director of Engineering.
Since launching MaintainX at 16 Tosca facilities, OEE has jumped from 55% to 80%, audit prep takes minutes instead of days, and sites can self-manage issues instead of needing corporate intervention.
“[With MaintainX], our plants have the data and resources to do the work themselves,” said Lily. “They’re very excited about it.”
Redimix: A Concrete Producer with Rising Downtime and Contractor Costs
Redimix was managing maintenance with paper notes, spreadsheets, and verbal updates. Work was missed, breakdowns skyrocketed, and critical parts were in short supply, causing contractor costs to spiral. Worse yet, asset and repair histories were locked in the heads of team members and standardized documentation was almost nonexistent.
“There's nothing worse than having something go down and not having the part on hand to fix it,” said Greg Wortman, Operations Manager at Redimix.
The team searched for technician-friendly maintenance software that could permanently solve its problems. They knew they needed centralized SOPs, parts data, vendor relationships, and maintenance history. MaintainX delivered. The team built out standardized training, automated preventive maintenance schedules, and gained real-time access to inventory levels.
“As long as you know how to take a picture on an iPhone and type in a Word document, you can use MaintainX,” said Greg. “The scheduling feature was a massive win.”
Redimix has completed 1,800+ work orders since adopting MaintainX. This helped the team reduce downtime, winter maintenance costs 66%, and total spend 53.9%. It also gave the company insights to stay ahead of problems and boost uptime across plants.
“We’ve done more maintenance than ever before with a significant cost reduction,” said Greg. “And if I want to pull the data up on my phone, I can look at those dashboards with the click of a button.”
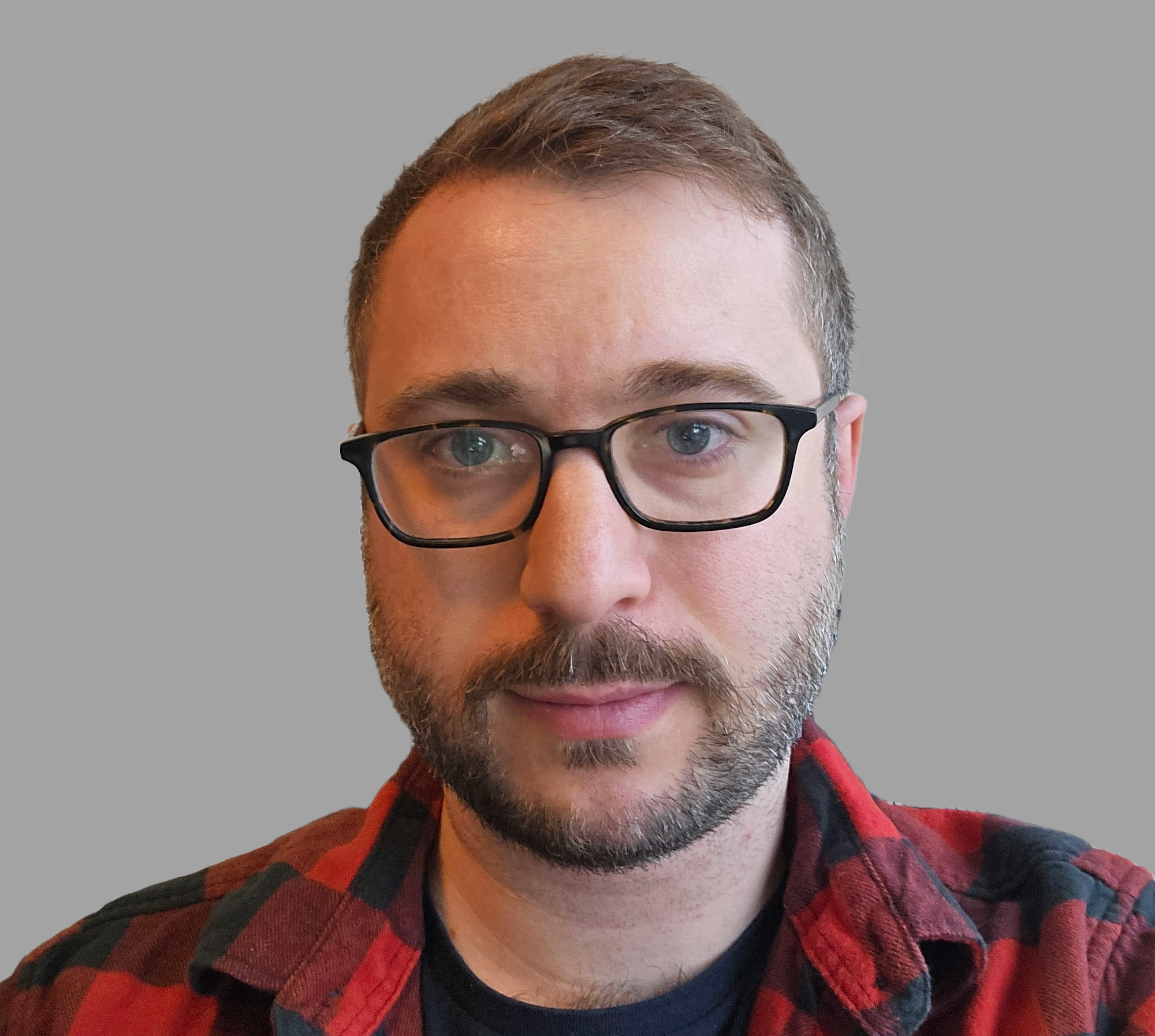
Marc Cousineau is the Senior Content Marketing Manager at MaintainX. Marc has over a decade of experience telling stories for technology brands, including more than five years writing about the maintenance and asset management industry.