.png)
In an environment shaped by labor shortages, rising costs, and aging infrastructure, maintenance teams are increasingly expected to do more with less.
At MaintainX, our goal isn’t just to help your team keep up. We’re building tools to help you lead the pack.
That’s why we’re proud to share that MaintainX was just named the Verdantix Green Quadrant: Industrial Computerized Management Systems (CMMS) Software 2025, scoring above the median in 9 of the report’s 12 categories.
This ranking demonstrates how MaintainX is bringing teams into the next era of maintenance. Read on to see what our innovations mean for your operations.
Key Takeaways:
- MaintainX’s AI-driven capabilities like smart procedure generation and anomaly detection are making preventive and predictive maintenance more achievable for manufacturers.
- We’re streamlining the complex process of digitizing operations with a user-friendly, enterprise-grade platform.

Designed for Frontline Workers First
The future of maintenance is mobile.
Our goal has always been to build software that actually works the way maintenance teams need it to. We’ve seen how a mobile-first platform that’s intuitive to use and scale helps our customers work better, faster, and smarter, no matter their skill level.
Verdantix saw this in MaintainX and celebrated us for our technician-centric design. By prioritizing features that can be used offline, in the field, and in real time, we’re bringing maintenance teams the tools they need to thrive in today’s fast-paced environment.
MaintainX’s mobile-first design made it easy for the Redimix team to embrace the new technology. “I spend a lot of my time on the desktop, but all my plant superintendents and the maintenance techs are on the mobile app. I wanted a system that they could use,” Greg Wortman, Redimix’s operations manager, explains. “As long as you know how to take a picture on an iPhone and how to type in a Word document, you can use MaintainX.”
Optimizing Maintenance With Best-in-Class AI Tools
Verdantix recognized MaintainX for bringing AI to frontline workers, calling our AI integration “best-in-class.”
AI technology can lead to cost savings by surfacing information that facilitates proactive maintenance strategies—which is especially important as the cost of unplanned downtime rises.
MaintainX’s AI capabilities help maintenance teams:
- Interpret asset data and generate asset failure summaries
- Quickly build out standardized procedures
- Reduce unplanned downtime by identifying equipment issues and solving problems faster
Our in-app, AI-powered assistant, MaintainX CoPilot, is trained on your manuals, your past work orders, and the way your team gets work done. It captures and transforms institutional knowledge into instant guidance that every technician on your team can access anytime and anywhere. Technicians can snap a photo of a problem and get repair steps. Or record a voice memo to auto-generate a work summary.
As the skilled labor shortage looms, tools that help your team gather and share knowledge are critical to future-proofing your operations. And when technicians can do the tedious parts of their jobs more efficiently, they have more time to tackle bigger problems.
“We’ve used AI to help with our lockout tagout procedures. For example, to change a bandsaw blade, we needed to lock out the motor. The first thing MaintainX CoPilot said was to shut off the breaker, which verified our thinking. To go through the entire manual to find that information would have been pretty hard, but CoPilot showed us exactly where to find it.” Jeremiah Dotson, facility maintenance manager at Amfab Steel
Simplifying Digital Transformation
For manufacturers moving away from paper-based workflows, software that combines ease-of-use and enterprise-grade functionality is key. MaintainX helps teams take their first steps to digitize their operations, and then continues to help them evolve by supporting more advanced strategies.
Maintenance leaders managing multi-site operations find that MaintainX is ideal for their needs. Verdantix scored MaintainX well for our pre-built asset library and centralized procedure library, which helps teams standardize maintenance practices across facilities.
These features, combined with strong AI-driven anomaly detection tools, position MaintainX customers to see long-term results.
Within less than a year of using MaintainX, Titan America reduced unplanned maintenance by over 30%. The company digitized more than 150 procedures and integrated over 800 assets into the platform, enhancing real-time visibility and decision-making across operations.
More on How MaintainX Stacks Up
Want to learn more about today’s trends for CMMS platforms? See how MaintainX is leading the way for modern maintenance in the full Verdantix report.
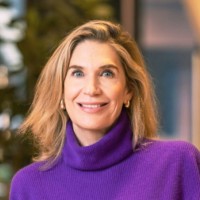
Head of Corporate Communications