Ahlstrom Reduced MTTR by 90% through Centralized Tribal Knowledge
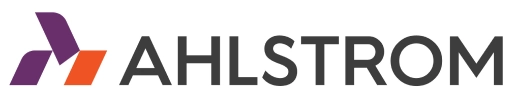
Titan America, the organization’s U.S. subsidiary, has developed a track record for connecting communities, generating economic prosperity, and improving stakeholder quality of life since its establishment in 2000. Titan America remains committed to upholding its parent company’s deeply rooted commitment to foster customer-focused decision-making that emphasizes teamwork.
Senior Reliability Manager Jorge Pinzon has worked in the cement and lime industries for more than 20 years. In 2018, Titan America hired Pinzon with a simple request: help us build a reliability-centered maintenance (RCM) program in our Florida plant leading to measurable O&M savings.
Despite the longevity of the RCM framework, a surprising 85 percent of recommended improvements are never implemented in companies. Though reasons exist for the lackluster industry average, the primary causes are a) ineffective systems for capturing, analyzing, and acting upon collected data and b) a lack of organizational support.
“I believe this 100 percent—when you talk about reliability, there has to be a commitment from all stakeholders within the organization,” Pinzon said. “Often, maintenance technicians and managers find themselves without the tools or budget to make it happen.”
One of the reasons Pinzon joined Titan America was the company’s commitment to continuous improvement. Upon starting, Pinzon quickly analyzed the plant’s critical equipment failures via root cause analysis, partnered with its engineers to develop solutions for repetitive failures, and implemented a new preventive maintenance program. His primary focus? Putting systems in place to ensure every RCM initiative came full circle in a timely fashion. Though company leadership was pleased with his initial changes, Pinzon wasn’t completely satisfied—he knew Titan was still leaving money on the table; he just wasn’t sure how much. With executive approval, Jorge began evaluating computerized maintenance management system (CMMS) options to streamline inspection data entry, data analysis, PM scheduling, and budgetary planning.
Based on his experience, Pinzon knew that successful RCM programs and user-friendly CMMS platforms go hand in hand. Program victory hinges on maintaining accessible data, the ability to make sense of that data, and the willingness of maintenance technicians to cooperate with initiatives.
Pinzon soon found the seamless data integration he was seeking in MaintainX. He liked that the user-friendly CMMS was compatible with desktops, tablets, and smartphones. Ground-floor technicians can easily follow digitized inspection checklists from their mobile devices, enter work order data in real-time, and reach Pinzon via instant messaging within seconds.
"I have five inspectors working on a problem right now, collecting data, and all I hear is how much easier, faster, and more user-friendly MaintainX is compared to what they did before,” Pinzon said. “A year ago, our plant inspectors had to go into the field and write each report by hand before converting the data into Excel files. Not only was this time-consuming, but I didn’t always have immediate access to the information during meetings.”
Prior to MaintainX, Titan America was losing production due to unplanned downtime being a 'major problem.' Jorge and his team at Titan needed to be able to understand and quickly identify trends of recurring problems, and be able to make changes in real-time. He needed real-time visibility into the root cause of bag failures. As a result of using MaintainX for less than a year, Jorge and his team eliminated unplanned downtime by over 30%.
Pinzon also uses MaintainX’s dashboard to track, analyze, and generate inspection reports; evaluate Mean-Time-to-Repair (MTTR) to inform budgetary decisions; and stay on top of in-progress work orders.
Jorge emphasized that MaintainX’s API capabilities enable his workflows to empower Titan’s teams that rely on their ERP system to be up-to-date and accurate in making decisions. When workers input data into MaintainX, it immediately populates Titan’s Domo dashboards and ERP system. This automated integration saves the maintenance department from hours of redundant data-entry work or in some cases, data not being recorded at all.
Beyond becoming a “thinking organization” and taking the time to understand why individual equipment failures happen, Pinzon emphasized the importance of having the right tools in place:
“To make information available at the right time is critical to our success,” he said. “A supported reliability community, with flowing, real-time information, and collaborative brainstorming sessions with department leaders are essential elements of RCM program success. However, if your team’s proposed actions only remain on a beautiful sheet of paper, forget it—it’s not going to happen.”
Today, Titan tracks 2,700+ meters across 800+ assets using MaintainX. Jorge’s team has digitized more than 150 procedures including inspections and safety checklists.
The company’s leadership has been so impressed with the plant’s measurable improvements since implementing MaintainX that they are now deploying the software across Titan’s subsidiary organizations.
The company’s upper management loves the increased transparency enabled by MaintainX. Now, executives maintain a bird’s eye view of what’s happening on the plant floor in real time.
Jorge can now manage:
Get more done with MaintainX