Western’s Smokehouse Increases On-Time Delivery with MaintainX
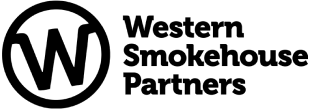
Cintas Corporation, a Fortune 500 company, is a leader in providing specialized services to businesses of all types and sizes, helping them get Ready for the Workday™ with confidence. With a heritage deeply rooted in efficiency, innovation, and excellence, Cintas has been recognized as one of Fortune's World's Most Admired Companies and is committed to safety and reliability in all its operations. In 2023, Cintas achieved the lowest safety incident rate in its history and was named one of Forbes' America's Best Large Employers, reflecting its dedication to its employee-partners and sustainable business practices
Cintas, in support of its commitment to excellence, recognized the need for a more robust and agile maintenance management system to support its expanding operations. In a strategic move, Cintas partnered with MaintainX to embark on a transformative journey, integrating cutting-edge technology to streamline operations, improve efficiency, and foster a culture of continuous improvement.
Their digital transformation journey was ambitious, targeting a swift and seamless integration of MaintainX across 200 sites in less than 3 months! The initiative was driven by a clear vision: empower employees with tools that will make their daily routines more efficient and lay a robust data foundation for future advancements.
Cintas implemented its first CMMS roughly 10 years ago. Their legacy system was unable to support its continued growth and addition of new sites. Cintas needed to modernize its maintenance management to match its operational scale and complexity.
The company needed a solution that could seamlessly integrate with its existing systems, support industrial maintenance reliability best practices, and be rapidly deployed across its vast network without disrupting daily operations. The solution needed to not only enhance operational efficiency but also embody Cintas's core values of safety and reliability.
MaintainX emerged as the ideal partner for Cintas, offering a mobile-first platform that accelerated the adoption of digital technologies across the workforce. The platform's robust features, including preventive maintenance, AI-powered predictive maintenance, and IoT integrations, empowered Cintas to uphold best practices in industrial maintenance reliability. With MaintainX, Cintas drove an increase in revenue by increasing asset availability, reducing downtime, and ensuring on-time delivery.
The decision to partner with MaintainX was not made lightly. Cintas conducted a comprehensive evaluation to confirm MaintainX could handle its scale and easily be adopted by the frontline team. Feedback from frontline partners was overwhelmingly positive, with many noting the intuitive design and mobile accessibility.
Eric Ayanegui, Senior Director of Operations Engineering, recalls: “I remember where I was. It was a Friday, after work, like 6 p.m., when I took a phone call from my engineering manager. He had just finished an in-depth review of MaintainX. He was literally bouncing off of the walls through the phone as far as his excitement of the potential, the breakthrough and all the different possibilities and the features that this new software would have versus the one that we were using.”
This successful evaluation and testing was crucial in confirming MaintainX as the right choice to support Cintas' digital transformation goals.
As the rollout began, user adoption became paramount. Cintas and MaintainX worked closely to ensure that training and support were readily available to facilitate a smooth transition for employees at all levels of technical proficiency. The platform's user-friendly interface and similarity to consumer applications played a significant role in its rapid adoption across the workforce. This integrated approach minimized disruptions to daily workflows and encouraged employees to embrace the new system, with each site going from users signing into MaintainX to completing all site PMs in less than 14 days.
Cintas successfully implemented MaintainX across 200 sites in just 9 weeks. The rapid deployment was a testament to the platform's scalability and the effectiveness of the partnership between Cintas and MaintainX. The platform's mobile-first design facilitated quick setup and immediate use without extensive hardware installations.
Within the first month, frontline partners reported significant improvements in their daily routines, from reduced paperwork and easier access to maintenance records to more efficient scheduling and task management. This frontline success highlighted the value of digital transformation and how technology can directly contribute to increased productivity and job satisfaction.
With MaintainX, Cintas drove unparalleled operational efficiency. The platform's advanced asset management and IoT integrations offered real-time visibility into frontline operations and asset health, enabling proactive maintenance, better decision-making, and efficient resource allocation. "The user experience is so much easier... we have instantaneous access to the data," remarked Eric Ayanegui, Senior Director of Operations Engineering, highlighting the platform's impact on decision-making and operational agility.
Cintas' partnership with MaintainX laid the foundation for a future-proof data management strategy. The platform's AI features and smart workflows streamlined maintenance scheduling, ensuring right-first-time execution of PMs. For example, MaintainX’s AI anomaly detection feature has already helped flag inconsistent reporting tactics across Cintas’ sites. This not only minimizes the risk of human error but also addresses the challenges posed by labor shortages by enabling less-experienced partners to perform at higher standards.
MaintainX has significantly improved job satisfaction and productivity among Cintas’ frontline partners. The platform's user-friendly interface made it accessible and easy to use, allowing employees to focus on high-value tasks. "It makes me feel like the company cares about improving our day-to-day routine," shared Pat Eling, a Maintenance Supervisor. By automating tedious tasks and streamlining workflows, MaintainX has enabled employees to contribute more effectively to the company's success.
MaintainX's global standardization features and procedure library have been instrumental in enabling Cintas to enforce maintenance standards with digital instructions and mandatory steps. "We now have the ability to enforce maintenance standards with digital instructions and mandatory steps," said Eric Ayanegui, Senior Director of Operations Engineering. This capability is crucial for maintaining compliance with stricter regulations and ESG laws, reducing safety incidents, and avoiding regulatory fines.
The adoption of work request QR codes has revolutionized the submission and tracking of maintenance requests within Cintas. Eric Ayanegui, Senior Director of Operations Engineering, highlighted the impact of this feature: "We're leveraging QR codes now, anybody can grab their phone and create a work request without being part of maintenance." This innovation has improved record-keeping with an automated digital audit trail and ensured that equipment issues are resolved quickly and to standards.
The efficiency gains from implementing MaintainX have been substantial. Tyler, a maintenance technician at Cintas, observed, "You might get an extra hour or two a day... over a week, that's 10 hours." The platform's mobile maintenance and digital work orders have optimized workforce scheduling, reduced duplicate work, and automated monotonous tasks, freeing up valuable time for employees to focus on more critical tasks.
Pat Eling, Maintenance Supervisor, shared his experience with the time savings: "I feel like I'm on the computer less. Before I used to have to go through and close out work orders, I had to open up requests. And now we've taken that to where the techs can open their own requests. They're closing their own work orders, and that has taken a lot of time off my day... It enables me to walk around, look at the equipment, look at processes to see if I can improve them. And it just really frees me up to be more visual in my planning versus sitting in an office stuck behind a computer.”
The partnership between MaintainX and Cintas has set a new benchmark for digital transformation in the industry. By deploying MaintainX across 200 sites in just 9 weeks, Cintas has streamlined its operations and strengthened its commitment to safety, reliability, and continuous improvement.
Mark Bolen, VP of Quality and Engineering, succinctly captures the essence of this groundbreaking initiative: "MaintainX aligns with our objectives and values. From day one, they've been able to keep pace with us here at Cintas, which is very hard to do. MaintainX is innovative and nimble and they provide an intuitive solution to help take your reliability program to the next level. With our partnership, we're building a data foundation that we can take advantage of for many years to come."
This initiative demonstrates the significant value that the right technology partnership can bring to large-scale operations. The Cintas-MaintainX partnership serves as a blueprint for enterprises navigating the complexities of digital transformation, and highlights the transformative power of digital technologies in enhancing maintenance management and operational efficiency.
Get more done with MaintainX