How Aparto Student Housing Manages COVID-19 Sanitation Inspections
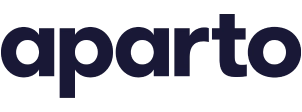
Headquartered in Clinton, Wisconsin, the company currently operates 38 facilities and offices in Wisconsin, Illinois, Kansas, Nebraska, New Jersey, New York, and Ohio. The DeLong Co. is the #1 U.S. exporter of containerized agricultural products, according to the 2021 Journal of Commerce export rankings. The company ranked #4 overall in total U.S. container exports for the same year.
The DeLong grain division is an industry leader in container exports and offers an extensive commercial grain and food-grade program. The grain division operates grain handling and storage facilities in Wisconsin, Illinois, Kansas, Nebraska, Michigan, New Jersey, and New York locations. The commercial grain business buys, stores, and sells corn, soybeans, and wheat from local farmers and ships these grains to various domestic millers and livestock feeders across the United States. In addition to its grain division, for the last 30 years, DeLco Transport has provided transportation solutions, offering vans, hoppers, dumpers, and tankers.
Prior to choosing MaintainX as its computerized maintenance management system (CMMS), DeLong was, as Sean Farrell, DeLong project manager, said, “basically all paper.” With paper binders and work orders clamped to clipboards, “We'd have to carry the work orders through the facility with us, or just leave them in the office and then have to go and fill them out later when we were done with our tasks.”
DeLong wanted its maintenance management more unified across the organization. Pat DeLong, who oversees DeLong’s massive grain operations, reported, “We used to do a lot of paper. Recordkeeping was messy. We didn't know if it was up to date or not, with no good way to have it live or have good checks and balances.” DeLong wanted to standardize how it records its standard procedures and daily tasks, among a host of other maintenance activities.
Furthermore, they needed to keep the standardization simple so that, Pat DeLong explained, “We could easily audit all of our maintenance.”
DeLong had two requirements for CMMS adoption: simplicity and useability.
After finding MaintainX in the App Store, “We compared it against several other similar systems,” Farrell said.
“What really stood out is MaintainX’s simplicity. We didn’t need to modify it. We started using it Day One.”
—Sean Farrell, DeLong Project Manager
DeLong also needed to make sure that its employees would easily take up whatever digital solution they chose. DeLong said, “We can't expect them to go from paper to something online that's more difficult than the system they currently use.” After integrating MaintainX into its maintenance program, Farrell recalled, “Our guys had a good experience. They love it because of its simplicity.”
In addition to simplicity, DeLong needed for the CMMS they chose to have excellent customer support. “We wanted to make sure that we have somebody to call if there's a problem,” Farrell said. “If there's any issue at all, they can pick up a phone, dial a number, and get an answer.”
Regarding the actual transition to MaintainX, DeLong said, “I've had experiences with other maintenance programs, where the initial setup was overwhelming. MaintainX is easy to use. It's just like writing it on a piece of paper, but you're doing it on the phone or on your computer. And it's traceable, that's what I really like.”
As Farrell said, “It’s made it so much easier to do this than it used to be. Before, I had to come up to the office, print out my lockout permit, my bin entry permit, my oxygen readings. Now, everything is on my phone.”
DeLong started using MaintainX as a maintenance tool but now also considers it a management tool for its employees. “You can track the progress of your guys, making sure that they're on top of what they're supposed to be doing that day. It’s just made it a ton easier.”
After implementing MaintainX in just one location in early 2020, DeLong has brought on board 30 locations (with more than 450 sub-locations) as of March 2021. Even better, in the same two years, DeLong has created almost 35,000 work orders and is tracking close to 3600 procedures. The company has integrated more than 325 meters and more than 1400 assets. Notably, it took only about three months for DeLong to reach 100% preventive maintenance coverage on all its assets across all accounts. In other words, 100% of its assets have at least one repeatable work order assigned to them.
Compared to hardcopy paperwork, Farrell appreciated how smoothly its maintenance management runs through MaintainX. “I really liked the way it flowed when we first started. You don't have to think about anything anymore.” He appreciates how he can get real-time access to what’s going on in the moment and next week.
That takes us to the Reporting module—another important MaintainX feature for DeLong. “Reporting is the best part of it. It’s simplified, what we can look at, how I can pull information. It’s much quicker and more accurate,” Pat DeLong explained.
The DeLong Co., Inc. is a multigenerational, family-owned business that provides innovative, value-based solutions in today’s dynamic environment. Since 1913, when brothers William and Jesse DeLong went into the grain business, the DeLong family has been committed to serving the agricultural community of southern Wisconsin. The company generates its revenue in six divisions: Agronomy, Grain, Exports, Seed, Wholesale Distribution, and Transportation.
Get more done with MaintainX