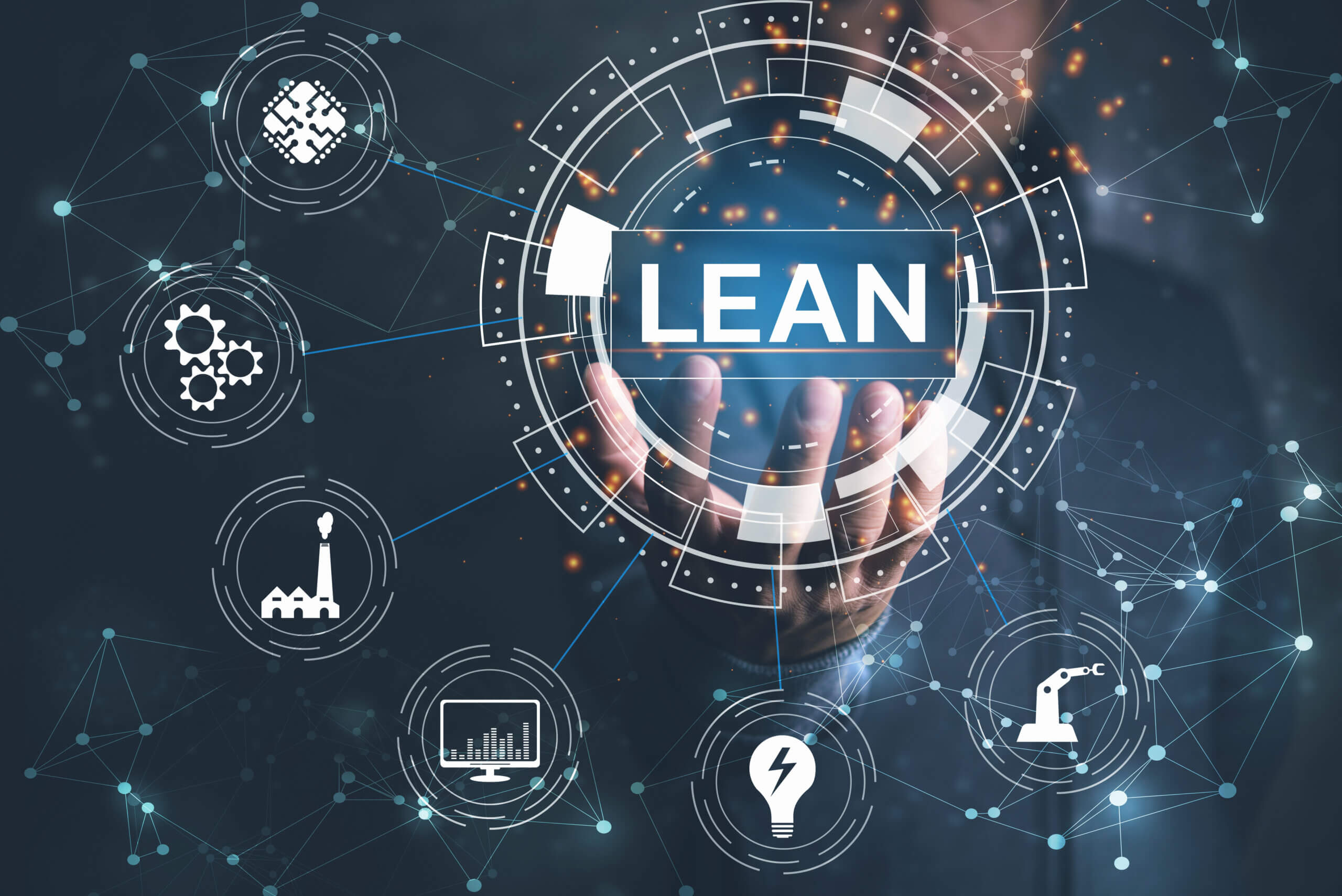
As a maintenance manager, running an efficient maintenance team is critical to success. In this post, we review six CMMS reports you can pull to demonstrate team efficiency, identify weaknesses in your assets, and develop a more robust preventative maintenance program.
Reports give you the data you need to build a more efficient and cost-effective maintenance team. The less you know about your team’s activities and which assets are causing you downtime, the harder it is to improve your team operations and manage your asset value. So, when used smartly, reporting can tell a lot of stories, like what worked this month, what project required the most time, and how a preventive maintenance plan cuts down on emergency parts costs.
The easiest way to extract these reports is from a maintenance management app like MaintainX. Once you’ve read more about reporting, you can try to build your own.
Key Performance Indicators Benchmarks
Benchmarks are certainly worth striving for. However, what can be more important is watching your trends over time. Are you improving in some areas and lagging in others? What do the KPIs help you figure out? And by using MaintainX filters, you can zero in on teams, assets, and effectiveness.
According to Reliable Plant:
We encourage you to share insights with management and customers. While there are many reasons to share your data, accountability and transparency are crucial aspects of any business. Transparency can boost your ability to work with teams across your organization, giving them access to where your effort is being spent, your biggest challenges, and where you’ve experienced your most significant successes in the last few weeks and months. These reports will help you assess asset and team performance. All of which can be found in maintenance software such as MaintainX.
“We found that while 74% of firms say they want to be “data-driven,” only 29% say they are good at connecting analytics to action. That is the problem.”
Forrester
CMMS Report #1: Created vs. Completed Work Orders
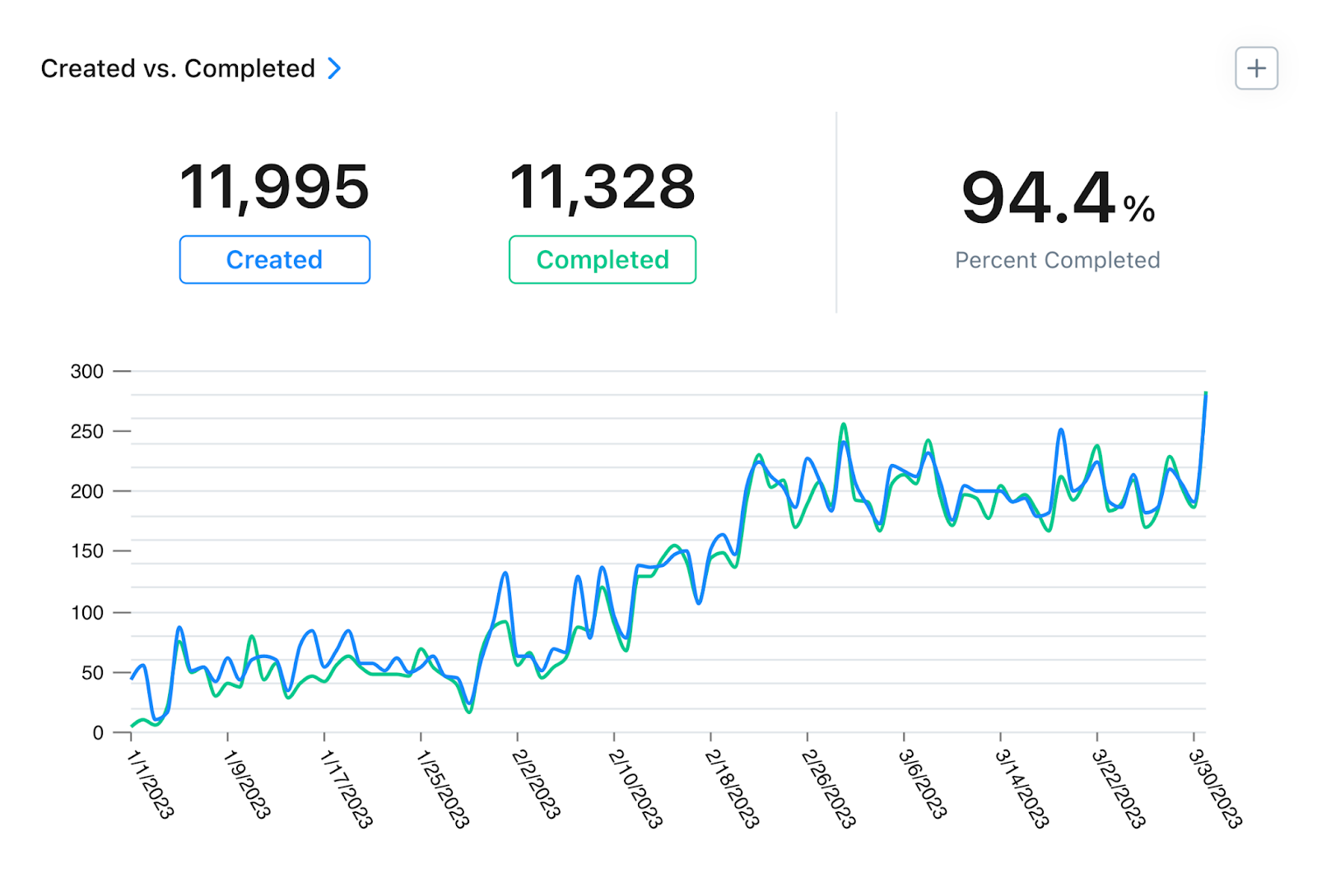
The Created vs. Completed report helps you assess schedule compliance, another way to monitor a team’s performance and productivity.
Schedule compliance is one way to illustrate how successful maintenance teams are in completing preventive maintenance (PM) tasks as planned. Maintenance experts consider the world-class standard for the measure to be 90 percent.
This key performance indicator (KPI), also referred to as PM compliance, compares actual work order completion dates to suggested completion dates. Periodically calculating schedule compliance is an excellent way to gauge overall maintenance productivity effectiveness.
Managers often schedule PM activities to be completed weekly, monthly, or annually. However, PM intervals can also vary according to the manufacturer’s recommendations, work environments, and equipment usage metrics. The key to running a successful PM program is creating a formal process to track, review, and investigate maintenance KPIs regularly.
Running a Successful PM Program
If a team’s scheduled compliance is falling below 90 percent, you may need to:
- Increase training
- Increase headcount
- Identify assets that may need to be on preventive maintenance.
Once you identify these weaknesses in your operations, make the moves necessary to improve your created vs. completed ratio. Every maintenance work order has a lifecycle with three main phases–creation, completion, and recording. We can break these down into six steps:
- Identify task,
- Request work order,
- Schedule work order,
- Assign and complete work order,
- Document and close work order, and
- Analyze work order for improvements.
Understanding each step and having a solid work order process ensures tasks don’t get stuck in one phase and end up backlogged.
CMMS Report #2: Reactive vs. Repeatable Work Orders
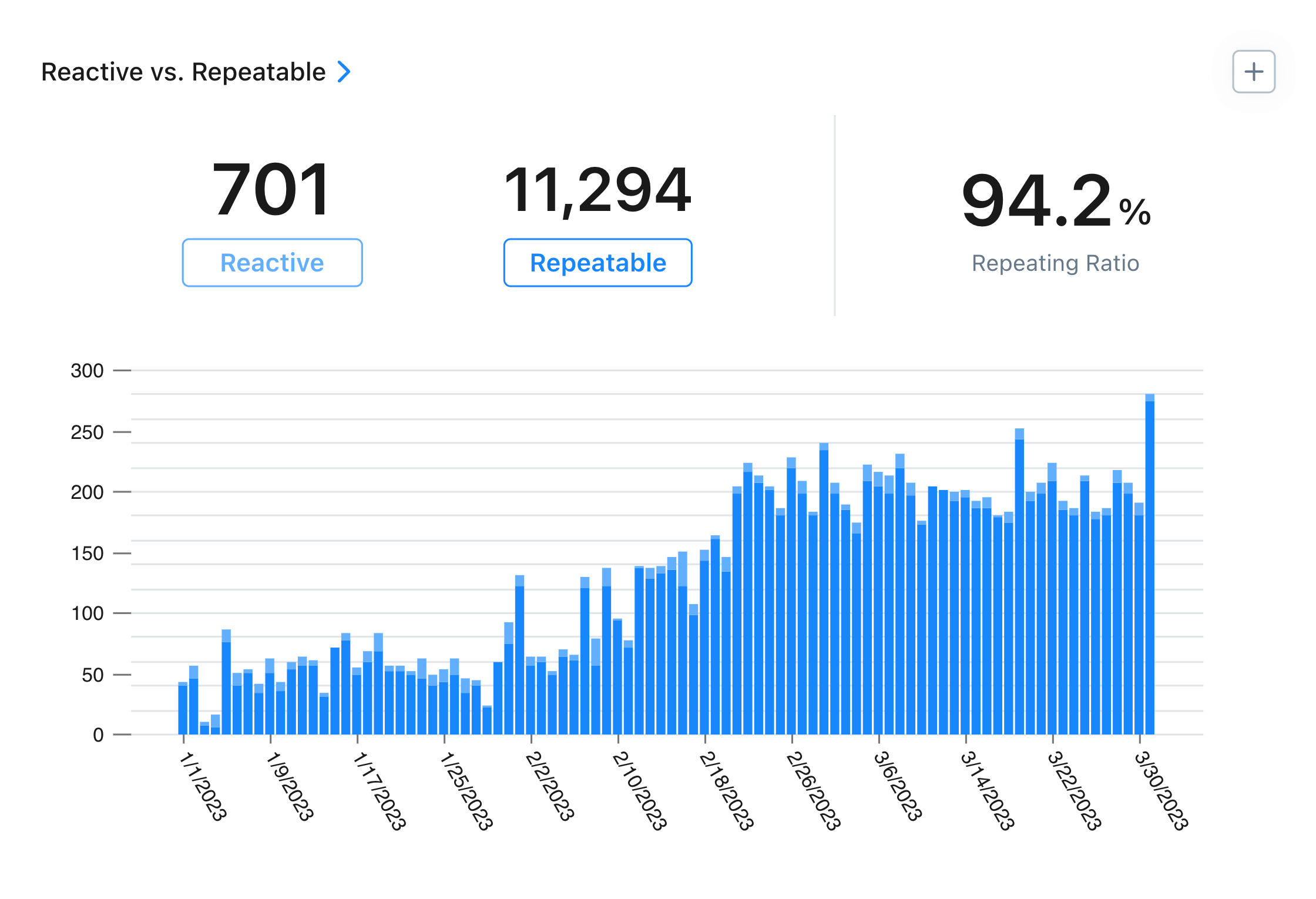
You don’t want equipment downtime. One of the best ways to avoid it is preventive maintenance. You know this, all maintenance managers know this, but it’s hard to know where to start. If you’re looking to develop a preventive maintenance program, read our guide, “What Is Preventive Maintenance? The Beginner’s Guide to Running PMs.”
Once you’re running a robust preventive maintenance plan, be sure to report out on its success to show the development of your team. Such a report shows how your team is becoming more efficient and effective. The Reactive VS. Repeatable report displays Work Orders based on reactive and repeatable work orders.
This Repeatable vs. Reactive KPI (or Planned Maintenance Percentage (PMP) ) measures whether your organization is stuck in a culture of reactive maintenance or is moving toward world-class or high-performance maintenance. This transition is essential because reactive work costs four-six times more than planned and scheduled work.
Planned Maintenance Percentage (PMP)
PMP is an indicator that compares the amount of maintenance time used towards planned maintenance tasks against the total amount of maintenance hours in a given time period (weeks, months, years). Monitoring the Repeatable to Reactive ratio allows maintenance teams to better understand how their maintenance plans are working out and to improve their strengths while targeting their weaknesses.
Managers should shoot for 20-30 percent of completed work to be reactive, reduce downtime, and increase asset lifespan.
“Industry standards suggest aiming for a ratio of 80% or better of repeatable Work Orders to reactive Work Orders to increase efficiency.”
SMRP
If you have way more reactive vs. repeatable work orders, dive into the report and filter reactive work orders by asset. This will help you identify your problem assets that need to be put on preventive maintenance plans. Reactive maintenance serves only one purpose—to address problems when they arise. Equipment malfunctions, setbacks, and failures trigger maintenance activities.
Check out:
CMMS Report #3: Time vs. Cost
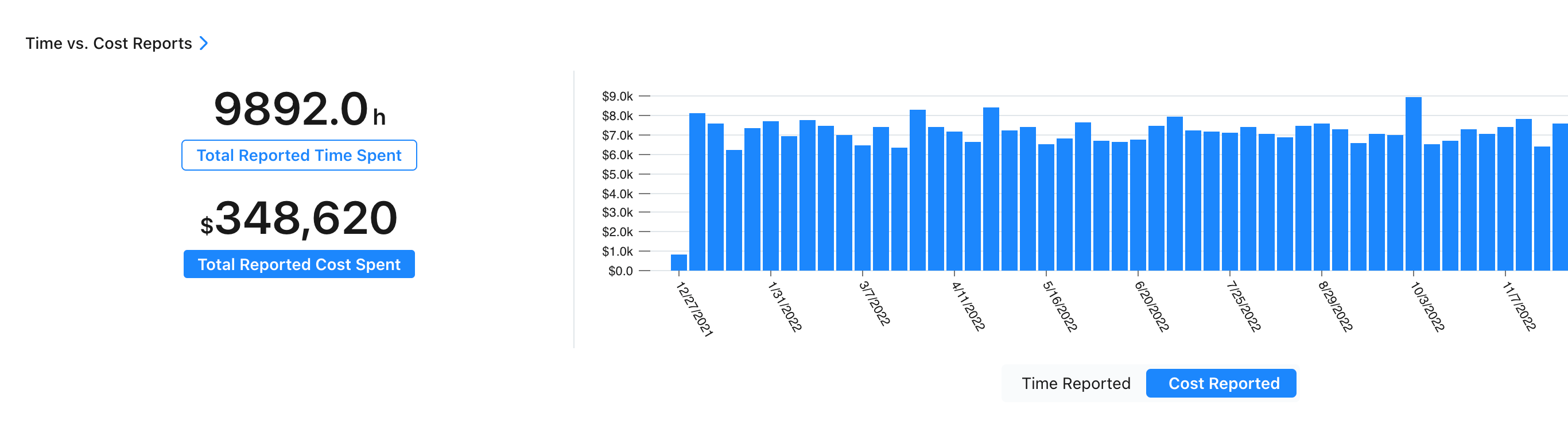
Time and Cost Tracking features are widely requested by our customers across industries and use cases.
Time and Cost Tracking can be surprisingly complex. So we’ve designed our Time vs. Cost Report to be a key feature to help you drive actionable improvements. These insights identify resource-intensive assets and equipment, identify organizational bottlenecks, and inform capital planning decisions.
Time and Cost reports are crucial because advanced budgeting and capital decisions should integrate labor and inventory costs. With these statistics, you can make intelligent decisions about equipment, spending, the cost of your employees versus the cost of outside techs, and more.
We know that way too often the cost of repairs can get lost. Here, you can keep track of time spent and the cost of that labor. You can make capital expenditure decisions based on which Assets cost the most to maintain. And you can evaluate the allocation of time and resources of teams, individual team members, and outside techs.
Tracking Time and Cost
With Reporting filters, you can track time and cost by:
- Due Date
- Location
- Priority
- Vendor
- Part
- Asset
- Asset Type
- Assigned To
- Procedure Flags
- Requested By
- Status
- Category, and more
In short, Time and Cost Tracking enables your team to track:
- Wrench, Inspection, and Work Order Time by Team, User, Asset, and Location;
- The Cost of Wrench, Inspection, and Work Order Time by Team, User, Asset, and Location; and
- Total Work Order Cost, including Parts, Assets, Labor, and any other costs that go into completing work orders.
CMMS Report #4: Completed with Inspection Check Work Orders
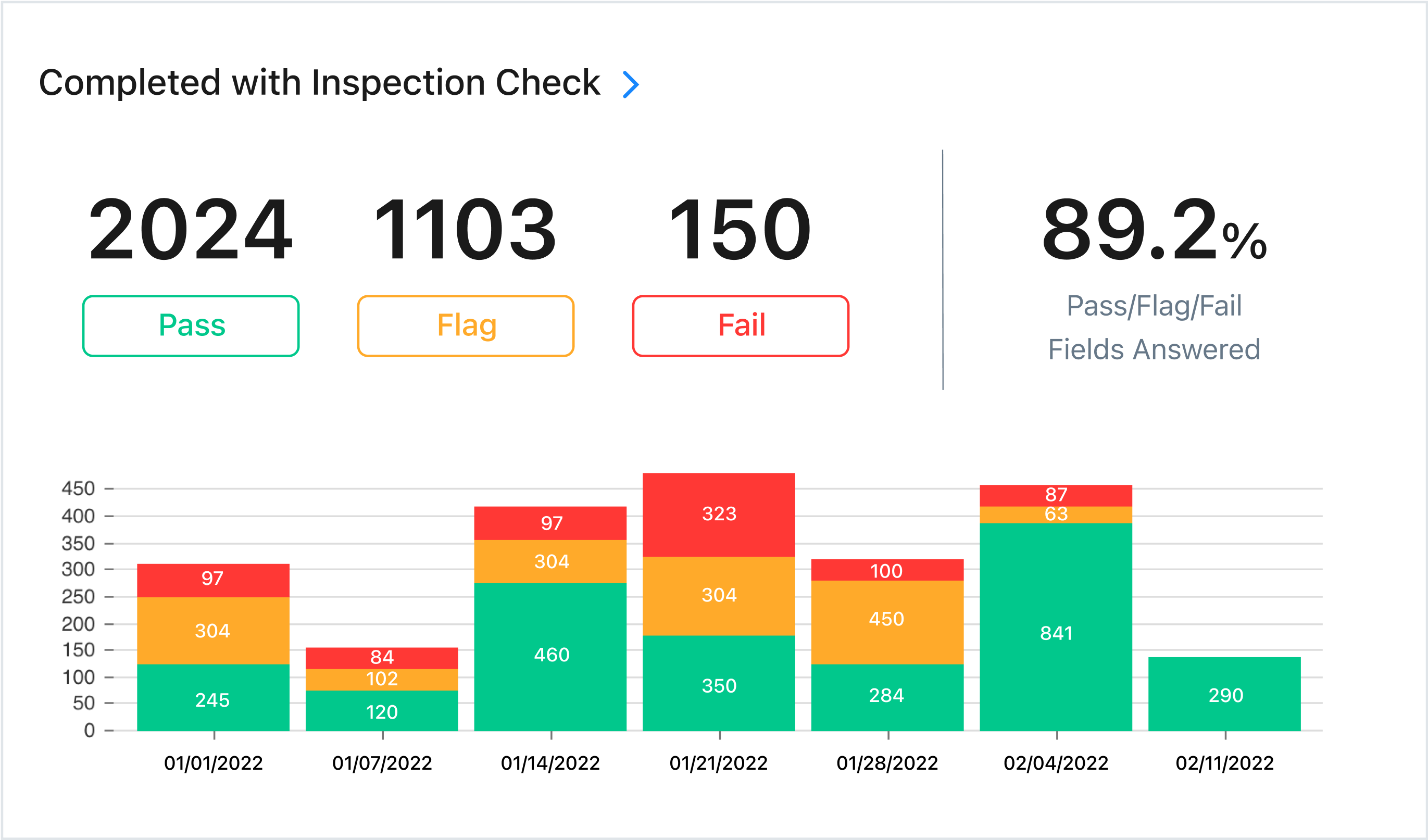
This Dashboard identifies how many of your Inspection Checks have been Passed, Flagged, or Failed in your chosen reporting period. Our Global Procedure Library houses inspection and safety procedures across industries and equipment.
This dashboard provides vital information to identify inspection trends and the root causes of failures, downtime, and possible safety hazards. Any flags or failures indicate it’s time to address an issue.
This dashboard also serves as an essential audit history of safety and compliance. Inspection Check work orders can include standard operating procedures that walk through common inspection checks. The MaintainX Procedure Library can store this information to attach to other work orders when needed.
For example, a manager can create and assign reactive work order procedures during an emergency from the spot of the breakdown, eliminating the time needed to get back to the office and assign a team.
Also, you can attach safety procedures for a particular asset to the work order. Once the machine is back up, technicians using the digital work order can upload pictures, automatically storing this data in the cloud. With a CMMS, technicians have complete visibility over repair and maintenance history.
Check out our Support article: check out Reporting Summary: Completed with Inspection Check.
CMMS Report #5: On Time vs. Overdue Work Orders
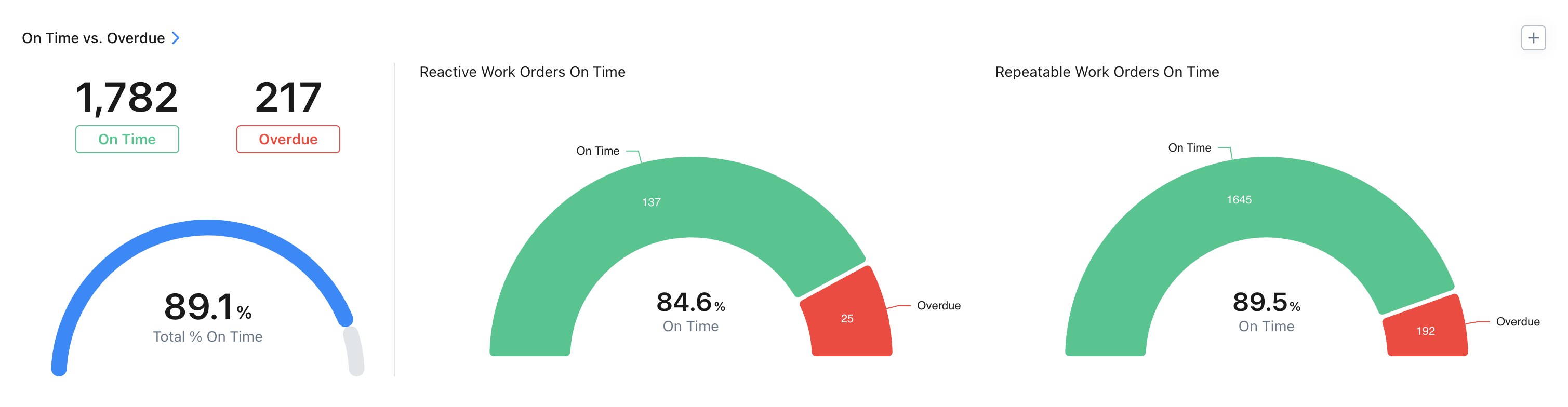
The On Time vs. Overdue Report details Work Orders completed on time or overdue, breaking them down further by Reactive and Repeating Work Orders.
This report shows that your teams are on time and meeting scheduled deadlines when it comes to completing Work Orders (by the due date set in the Work Order). The dashboard also highlights how many Reactive Work Orders don’t have a due date assigned at all. This may or may not be a problem for specific Work Orders, but generally speaking, we think it’s a good idea to add dates to provide your team structure (i.e., the date by which tasks must be completed).
These stats can help you understand a team’s historical bandwidth and efficiency. For example, is it always the same assets or teams that have overdue Work Orders, even if they are able to complete them? Likewise, the data helps you justify additional headcounts and evaluate the efficiency of those assigned to get work done by the deadline. This is especially important when maintenance depends on schedule compliance.
CMMS Report #6: Time to Complete Work Orders
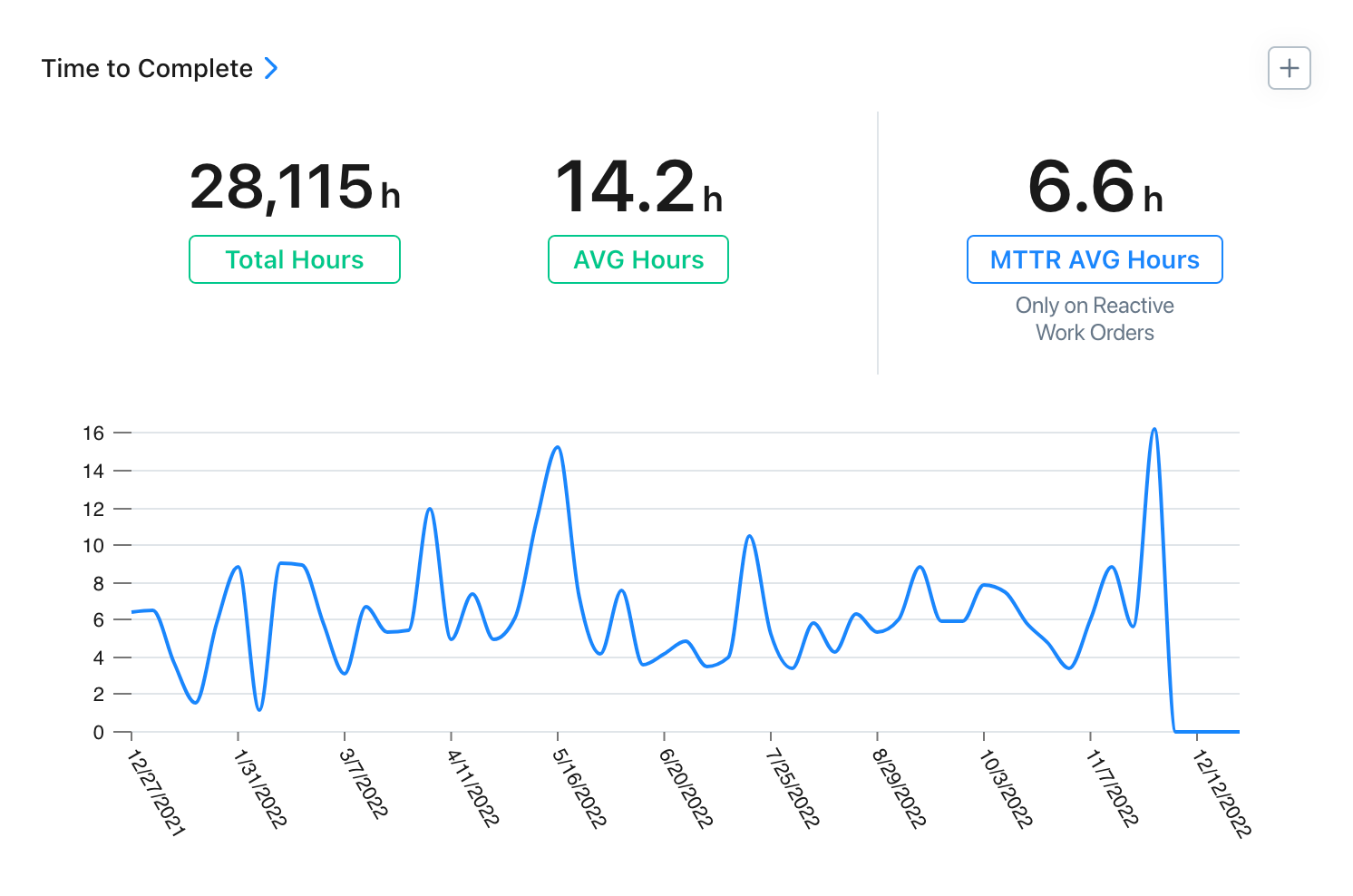
The Time to Complete Report provides a baseline that your department can use to measure asset efficiency and equipment value. It’s a valuable productivity benchmark for organizations seeking to reduce expensive and prolonged repair times.
Time to Complete shows how long it takes your team to complete Work Orders, displaying the total and average number of hours spent on reactive and repeatable Work Orders and the average MTTR hours on reactive Work Orders. The hours are based on the creation and/or start date of Work Orders.
Mean Time to Repair
Mean Time to Repair (MTTR) refers to the average time maintenance teams spend diagnosing, fixing, and recovering failed pieces of equipment. MTTR is a baseline that maintenance departments use to improve asset efficiency, minimize unplanned downtimes, boost bottom lines, and assess equipment value.
With Time to Complete analytics, you can evaluate the quality and effectiveness of your maintenance procedures. For example, equipment breakdowns often translate to extended repair times, technician overtime, outsourced contractor fees, and lost production schedules. Use Time to Complete to find the sources of these expenses and determine where to direct your attention. For example, an asset may need an upgrade. Or, a tech needs additional training to complete an SOP more efficiently.
Mean Time to Repair (MTTR) is calculated by tracking the total amount of time an asset undergoes recovery after downtime, then dividing it by the number of times the asset in question has failed within a given time.
MTTR = Total Maintenance Time / # of Repairs
For example, if an organization spends 50 hours total on unplanned maintenance for an asset that broke down eight times in one year, the asset’s MTTR is 6.25 hours. The calculation would be: 50 hours / 8 = 6.25
Ultimately, delving deeper into “the whys” behind high Time-to-Complete metrics will help your maintenance teams increase uptime, enhance efficiency, and decrease unnecessary costs.
Got CMMS Reports: Now What?
Titan American and MaintainX
Looking at reports is one thing, but realistically, you want them to be easy enough to use regularly and for the data input to be easy enough for your team to enter accurate work order data for you to pull into reports. Miguel explains it perfectly:
Watch: Titan America and MaintainX
From the video:
“Look at the four pillars you have in the maintenance department. And look at what the weakest links in the chain are. You’ll say you’re using SAP and Maximo, and you have all the inspections saved in your program. Okay, but how often do you process that data? How quickly is that data available for your decisions? A week? 24 hours? A month? When we remember? When there’s a failure? When you go back and realize that the inspection never happened? You just weren’t able to visualize that data, but with MaintainX, you can go right now and see the complete operation.”
With MaintainX, you can see all these reports and manipulate them in an easy-to-access dashboard to share with the people that matter.
Watch our webinar on Reporting 101 to learn how to access these reports for your team.
Make MaintainX Reporting Part of Your Routine
Once you have your reports with data, you can organize them into a dashboard that you and your team can refer to daily.
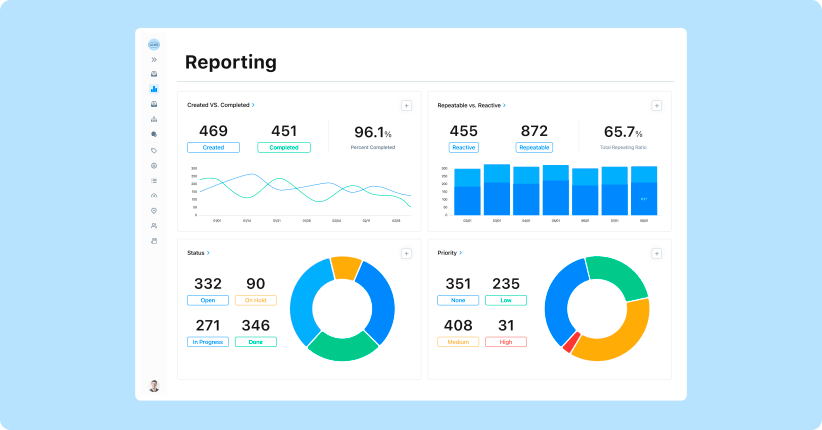
Access to the right data in real time is a huge benefit, especially if you use it to improve your processes and workflows. At MaintainX, our mission is to transform the way you manage your equipment and facilities.
As a result, we keep building for the long term, pushing innovation in mobile workflows, real-time analytics, and open APIs. Check out these posts:
- Improve Production with Enhanced Reporting
- Optimize Your Preventive Maintenance with Manufacturing Analytics
Check out our Support Articles on using our advanced filters to fine tune your reports:
FAQs
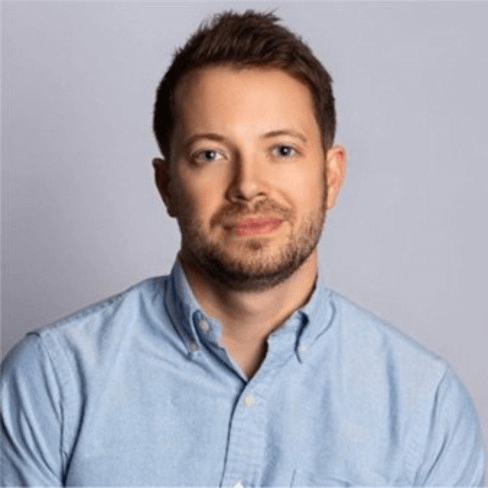
Colin Strachan is a Senior Product Marketing Manager at MaintainX, with a background in journalism and almost a decade of experience in SaaS marketing. In the past few years, he has worked with some of the world’s largest enterprises to adopt software that empowers their employees to work more effectively.