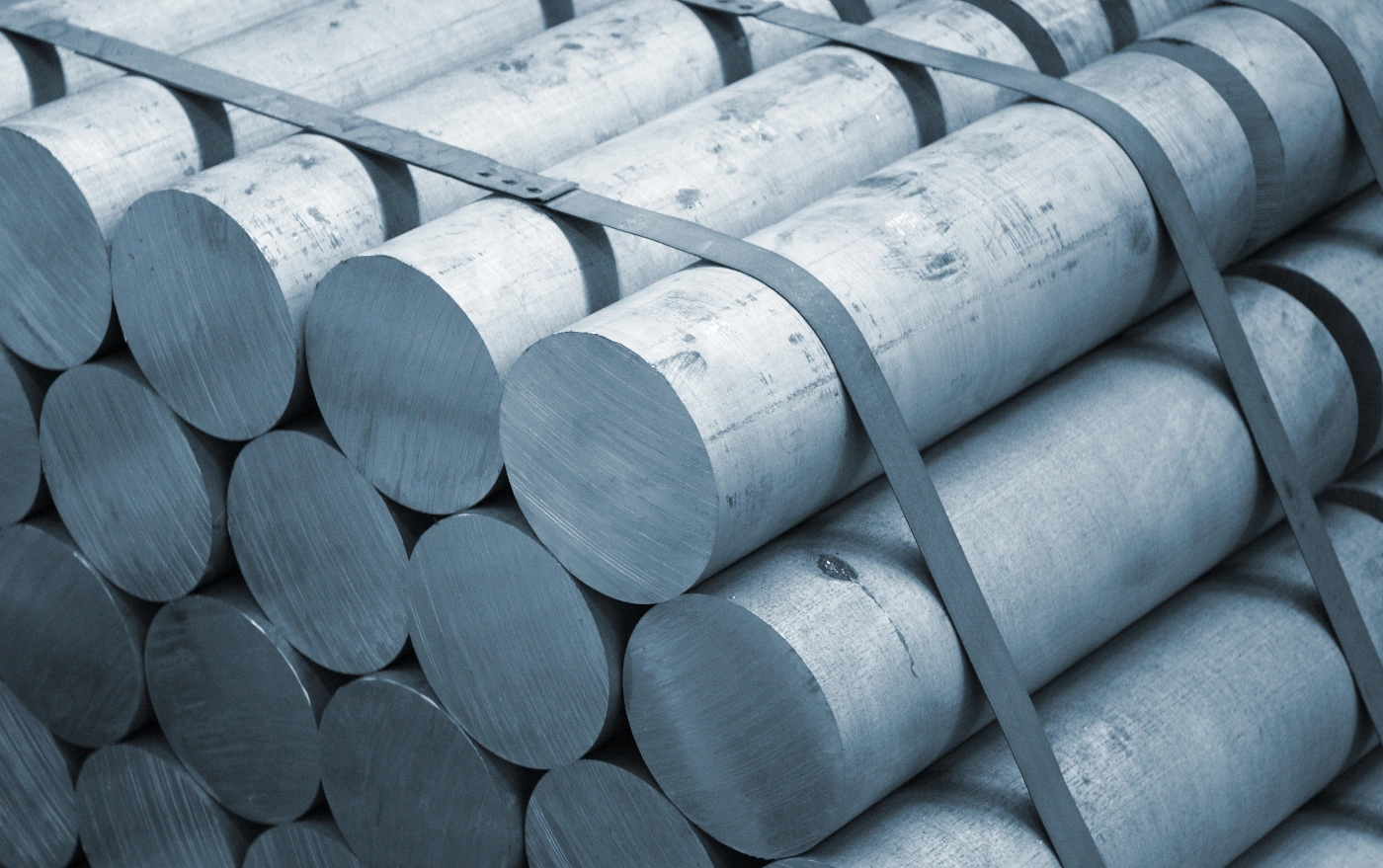
Material Requirements Planning is the process of identifying what materials and components manufacturing companies need to produce particular goods. It is a supply planning system that helps product manufacturers manage their supply chains, plan and map out necessary lead times, deliver finished products to customers quickly, and optimize their earnings.
Material requirements planning starts from knowing what your finished goods are supposed to be and works backward to plan production and inventory based on three main questions:
What Materials Do You Need?
This involves looking at customer demand and sales forecasts and understanding the raw materials and components necessary to meet them. With this in mind, you can identify the materials you need to procure by looking at what you already have. This type of demand forecasting involves taking stock of present inventory, comparing it to the list of needed raw materials and tools, and itemizing what you need to stock up on.
What Quantity of Materials Do You Need?
This is a question of volume. How much production do you want to undertake? Your answer to this will be a function of market conditions. What kind of demand exists for your products? Your production capacity will also factor into your answer here. Do you need to produce specific amounts before breaking even? And can the market accommodate those volumes?
By When Do You Need Materials?
Or rather, when does the market need it? Beyond planning for raw materials, knowing customer expectations will help you schedule production properly so you never fall short of demands. You’ll need to account for all resources you need for the manufacturing process, including labor and machinery. You want the production process to continue without delay, so your schedule should identify what assets are needed and when and ensure any scheduling conflicts are resolved beforehand.
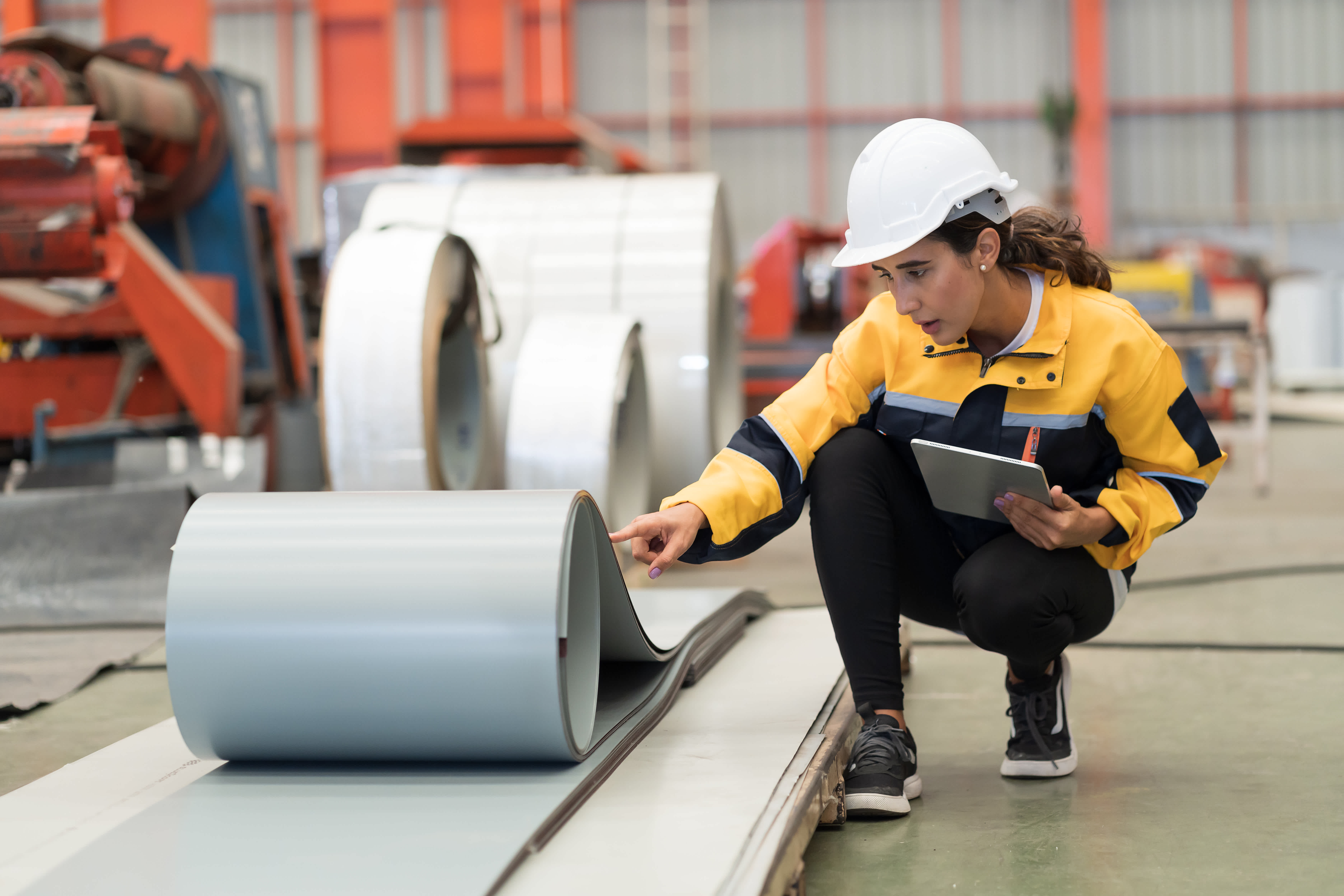
What Are the Benefits of MRP?
The whole point of MRP is to ensure a smooth production cycle that meets customers’ demands. More specifically, let’s break down some benefits of material requirements planning.
- Improve Your Inventory Management: Planning beforehand helps you manage your inventory optimally. You’ll be able to avoid shortages or stockouts and ensure you always have the goods you need for production. You’ll also eliminate waste that could occur from buying materials that are not necessary. Not to mention saving on the costs that excess inventory storage would require.
- Always Meet Demand: Effective supply chain management helps make sure you meet customer demand. This helps create a loyal customer base that trusts you will consistently deliver when you say you will. This data can also inform the pricing of your finished goods as you work toward profitability.
- Optimize Production Costs: When you schedule your production properly, you can avoid delays and disruptions. This means that any extra costs from disruptions can be eliminated.Also, proper production planning helps ensure no assets are overloaded because you’re rushing to meet demand and deadlines. Good capacity planning will help prevent breakdowns from overused assets, potentially extending the useful life of your machinery and reducing your maintenance costs.
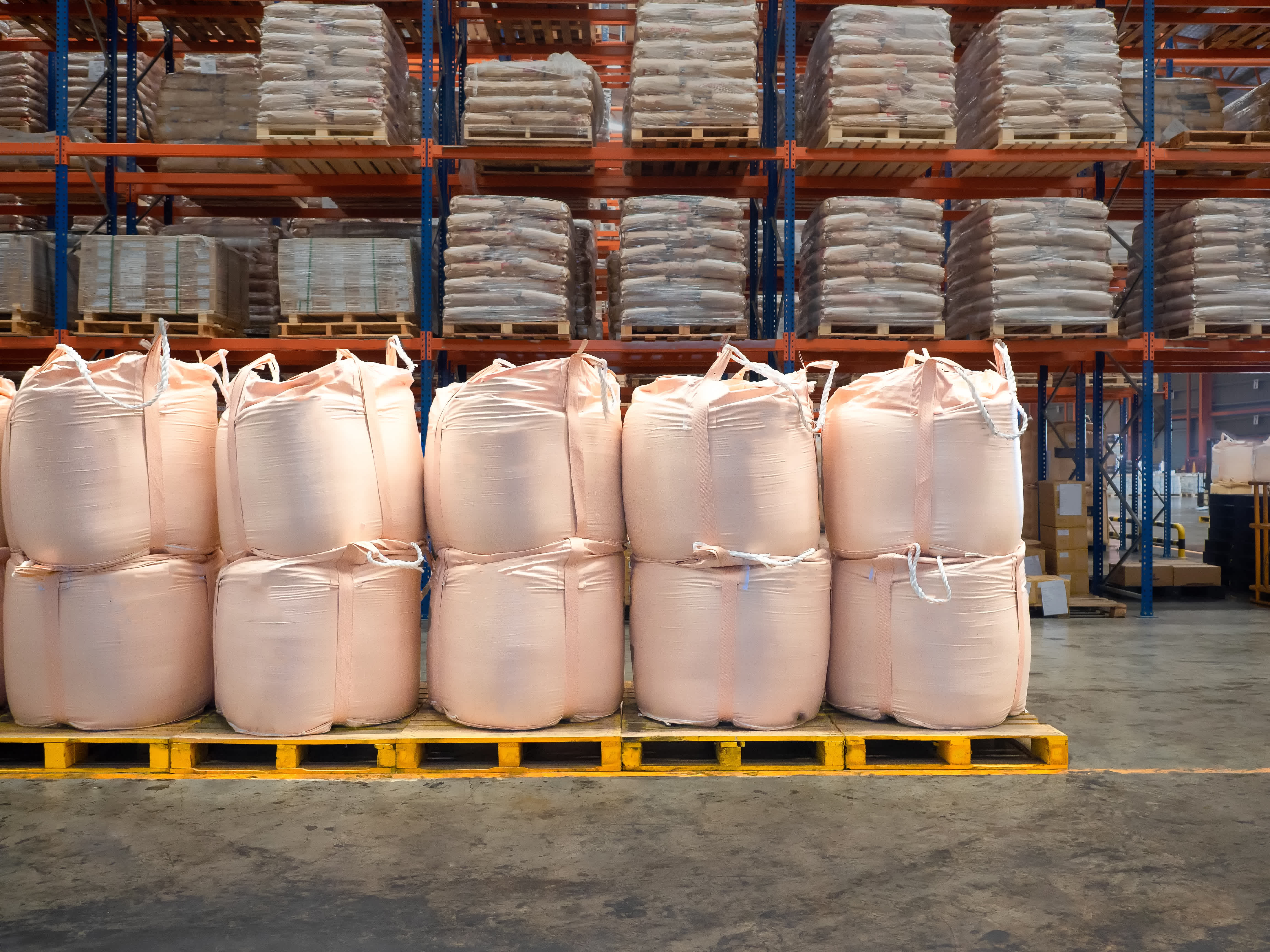
Are There Any Drawbacks to MRP?
Challenges facing the use of an MRP system include the following:
Can Be Expensive to Implement
It requires managing many moving parts and, as such, can be costly in practice. MRP software can also be costly sometimes. However, a CMMS software solution can be a more cost-effective alternative to help manage some parts of your material requirements planning systems. MaintainX is one example.
Not the Most Flexible System
As much as planning helps you save money, making drastic changes to those plans can become even more costly. Getting the most out of an MRP production schedule involves sticking to the plan as much as possible. As such, it isn’t the best option if your production cycles are prone to emergencies or disruptions.
Requires Highly Accurate Data
You need accurate data on demand and sales forecasting to benefit the most from an MRP. Your other inputs should be accurate as well. Want to learn more about MRP inputs? Keep reading.
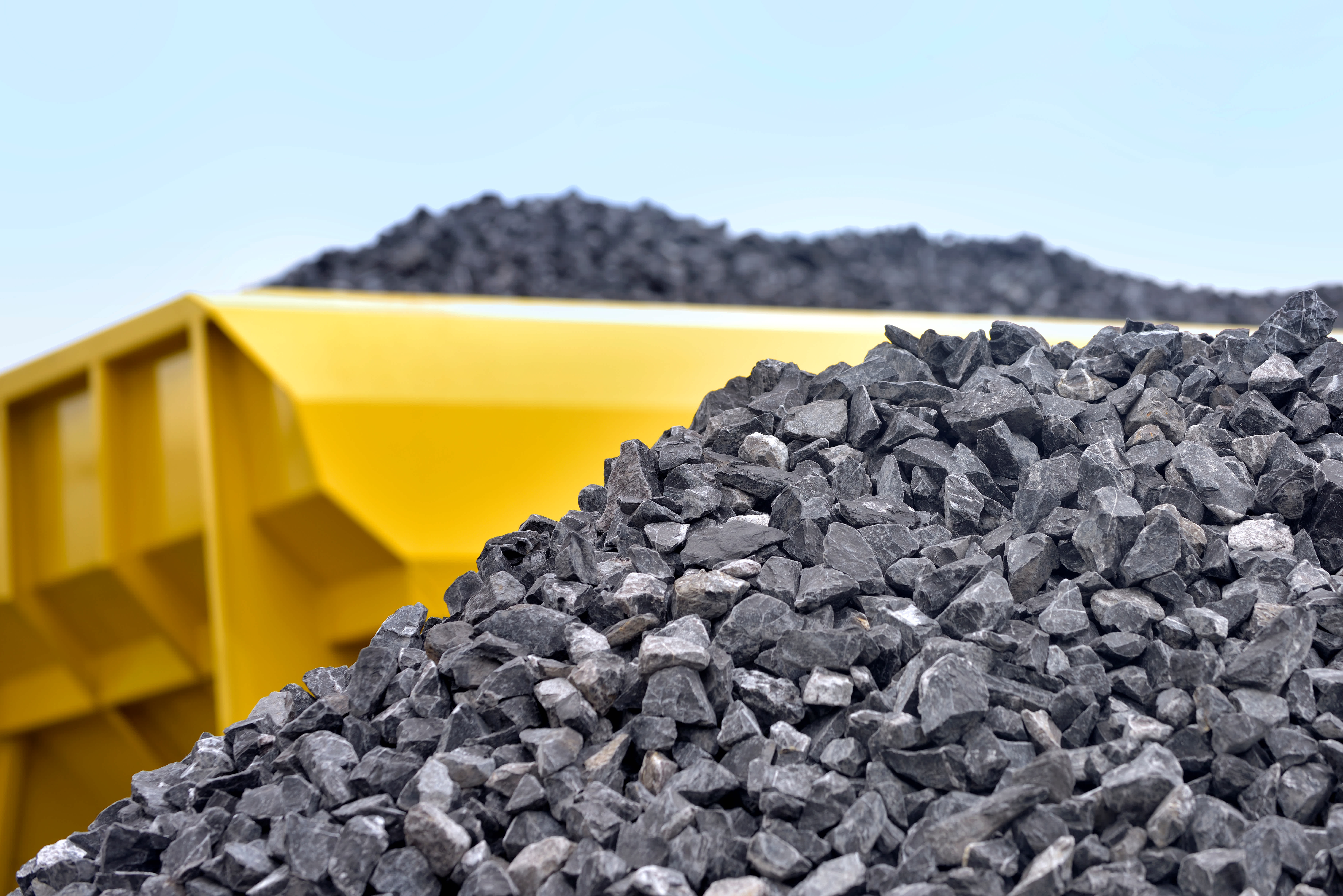
What Are MRP Inputs?
To create a successful MRP system, you need to have solid data to work with. Some of these include:
- Demand: This includes customer orders and sales forecasts. Look at the overall market and consider the conditions for your product. Also, look at your historical sales data. Are sales growing or dwindling? This will help you identify the most accurate figures to enter in your MRP.
- Bill of Materials: This lists all the materials required for the products. Knowing the products you will make and the volume, you can identify the materials needed and check your inventory for them.
- Inventory: You’ll need a clear view of your inventory levels across all your facilities and projects. A CMMS is a good idea for creating an inventory management system, as you’ll get a bird’s eye, real-time view of your inventory. MaintainX, for example, allows you to keep track of what you have.With this, you’ll know what you need to get. You can also create and assign purchase orders in MaintainX. Once you identify what materials you need, you can create purchase orders and assign them to staff immediately without leaving the app. You can then monitor the orders in real time.
- Master Production Schedule: This schedule considers the materials available and when, the staff available and when, and the assets available and when.
MRP Inventory Management
According to the Corporate Finance Institute, when it comes to MRP inventory management, the three primary objectives are:
- Ensuring raw materials are readily available for production, and products are readily available for delivery to consumers,
- Storing the lowest number of raw materials and finished product levels, and
- Expertly organizing manufacturing, delivery schedules, and purchasing activities.
A robust CMMS can do all of this with automated scheduling, real-time inventory reporting, and efficient maintenance and manufacturing teams.
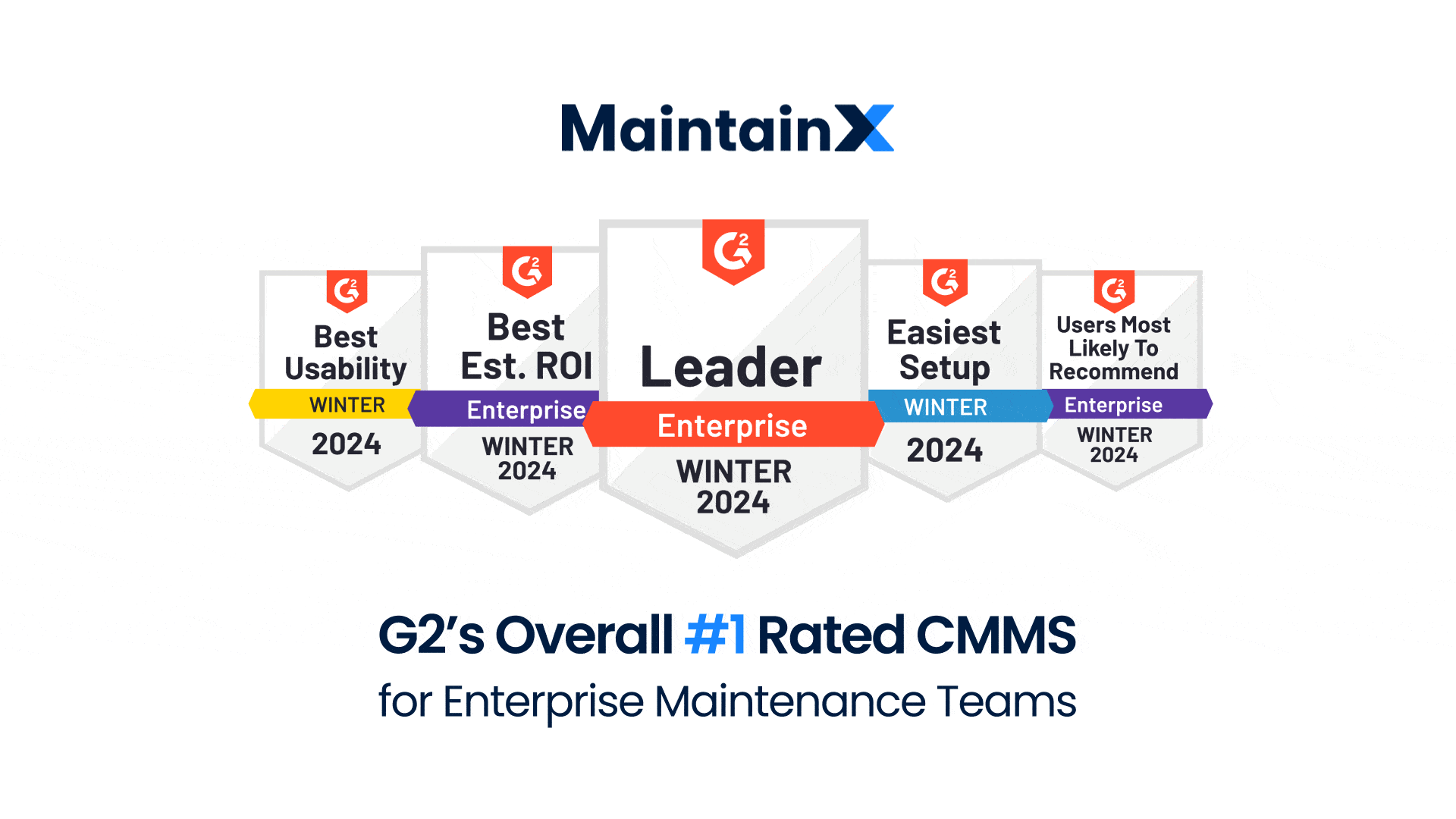
Manage Your Material Requirements Planning with MaintainX
MaintainX CMMS can help manage your manufacturing resource planning in conjunction with your MRP software. MaintainX helps streamline your workflows, production management, maintenance operations, manufacturing operations, and overall business processes. MaintainX can help simplify the following:
- Inventory Control: Keep an eye on stock levels with MaintainX’s inventory tracking
- Procurement: Create automatic purchase orders based on inventory records
- Work orders: Use the mobile app to create work orders and get real-time updates from the shop floor
- Routing: Here, we are referring to all different kinds of routing. In MaintainX, you can manage fleet routing, subassemblies of which products are finished where, and reorder points along the production line.
MaintainX integrates with ERP software (enterprise resource planning) integration to take things a step further. MaintainX provides REST APIs and integrations that pull real-time data directly into ERP systems. Even more, check out our partnership with SAP.
If you want to take your manufacturing business to the next level, try MaintainX today.
FAQs
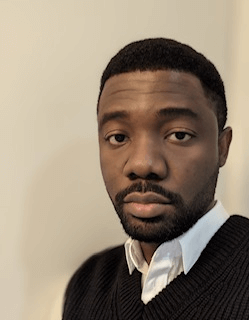
Lekan Olanrewaju is a content writer with years of experience in media and content creation. He has held positions at various media organizations, working with and leading teams at print magazines, digital publications, and television productions.