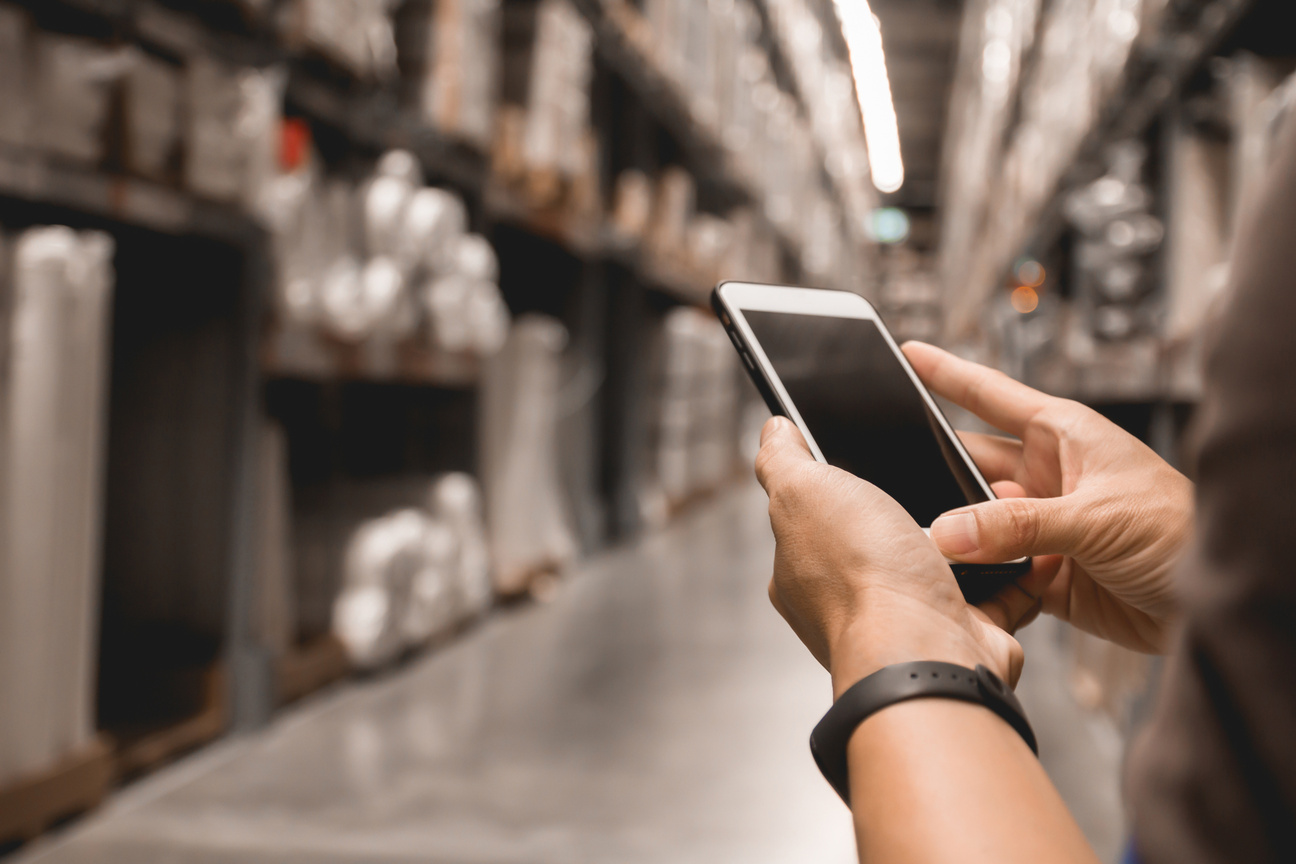
Are you spending too much time tracking down parts that may or may not be on the shelves? Is your downtime prolonged because you don’t have the parts you think you do and need to order them? If this sounds like you, it’s probably time to re-evaluate your inventory management practices and explore digitizing the process.
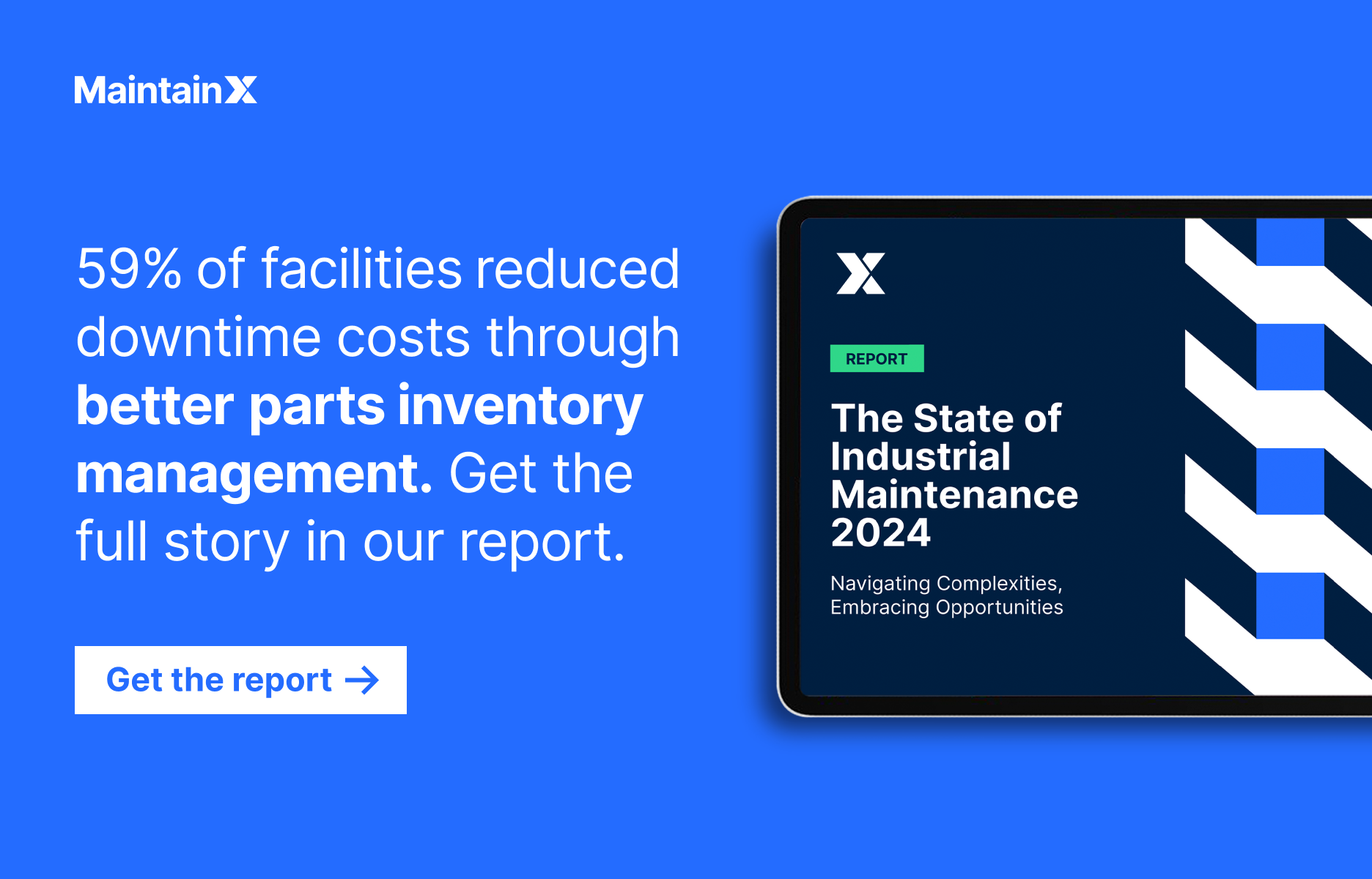
While your manual inventory protocols might be second nature to you, digitizing and automating your workflows can help you increase inventory visibility, avoid unnecessary stockouts, and decrease duplicate parts purchases. Here, we walk you through how to create a digital inventory management system using a computerized maintenance management system (CMMS).
Challenges facing manual parts inventory management
If you already have a manual parts inventory management system in place, going digital might seem like an unnecessary distraction. However, here are some of the critical risks you may face by sticking with a manual inventory approach.
Inaccuracy and data entry errors
As conscientious as your technicians may be, it’s impossible to eliminate the potential for human error. Simple mistakes like putting an entry in the wrong column or adding an extra zero to a number can mean the difference between having the required parts on hand to conduct maintenance and extending your downtime while waiting to acquire the parts.
Lack of real-time visibility
Relying on manual data entry means waiting for someone to physically update your inventory records whenever a change occurs. This process denies you real-time and up-to-the-minute information about your spare part levels, makes it harder to order replacement parts on time, and puts you at risk of stockouts, resulting in missed sales opportunities.
Limited accessibility and collaboration
Traditional inventory methods like log books and spreadsheets can restrict who has access to inventory data, especially if you’re depending on manual records located in a single place. This is even more of a problem if you oversee multiple locations or facilities and your records are spread across sites. In addition, parts inventory management often requires collaboration between maintenance and procurement teams to decide what parts to obtain, when to obtain them, and in what quantities. A lack of easy access to the data can slow down decision-making and the approval process
Increased costs
When faced with inefficient inventory management systems and fears of supply chain disruptions, one apparent solution is to overstock parts so you always have them on hand. However, this approach is inefficient as it increases carrying and storage costs, eating into financial resources you can deploy elsewhere.
If any of these problems ring true, below we outline how a digital inventory management system can help.
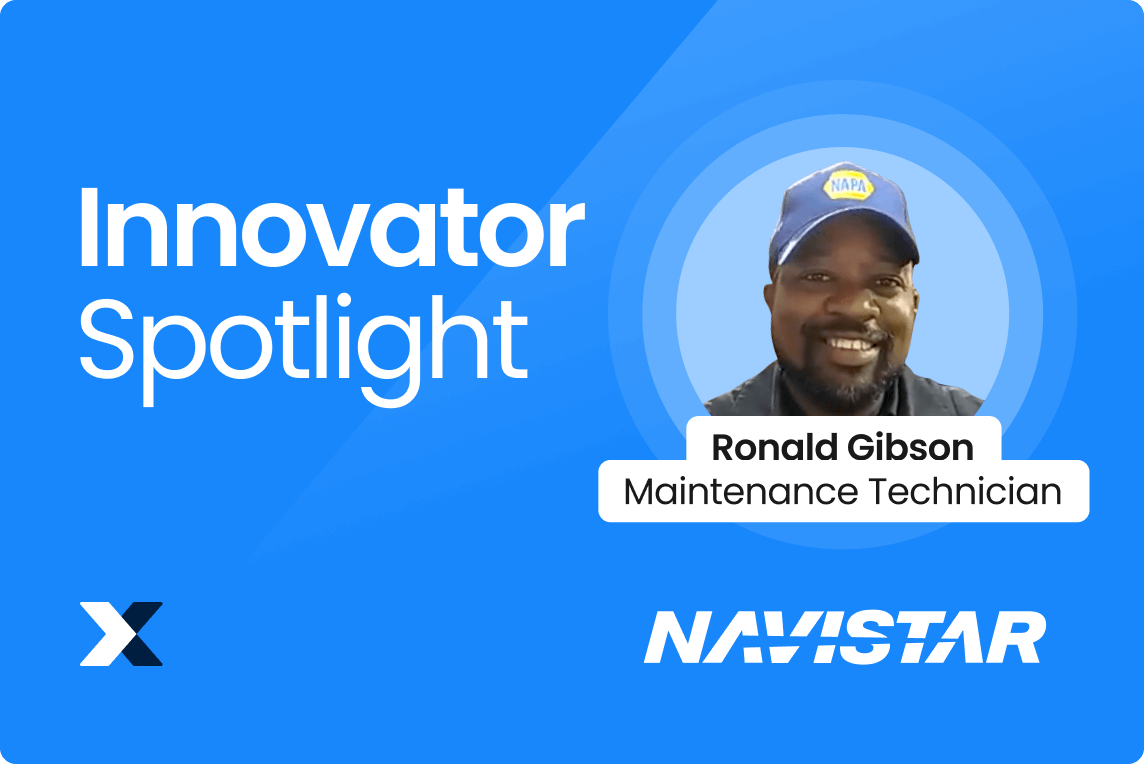
Click here to read how Maintenance Technician Ronald Gibson digitized and automated Navistar's parts inventory.
Benefits of a digital inventory management system
Managing your parts inventory with a digital system can help you get the following benefits.
Improved preventive maintenance workflows
It defeats the entire purpose of preventive maintenance when planned maintenance work stalls because critical parts are unavailable. A digital parts inventory system that gives you adequate and real-time data ensures that you are aware when stock levels are low. For example, a CMMS with automated low-quantity alerts informs you when you need to reorder necessary parts, ensuring you get them on time and eliminating the risk of your planned maintenance activities suffering delays.
Faster responses to emergency repairs
Even if your preventive maintenance workflows proceed without any hitches, some level of reactive maintenance is inevitable. In such cases, you want to minimize the unplanned downtime by performing repairs as quickly as possible. The last thing you want is to prolong your downtime waiting for the necessary parts. If you select a CMMS with a robust purchase orders module, parts falling below set thresholds can trigger purchase orders with saved vendors. As such, you can replenish your inventory well in advance to ensure you always have critical parts on hand.
Data-driven decision-making
By maintaining real-time inventory records, you can gain greater insight into your parts usage. With a CMMS, for example, you can analyze your data to find your most frequently replaced parts and how they factor into equipment malfunctions.
Enhanced demand forecasting
With a CMMS, as soon as there is a change in inventory levels, workers can use their digital devices to instantly update the records, even from within a specific work order. This helps ensure you maintain real-time data and analytics for predicting inventory needs.
Improved stock level optimization
By maintaining real-time inventory records and with automatic purchase orders, a CMMS can ensure you order replacement parts on time.
Better collaboration
Using a CMMS offers you access to inventory records from wherever you are. As such, you can coordinate operations across different departments that need to collaborate on maintenance work.
Lower expenses
With tighter control over your inventory, you can eliminate the fear of stockouts and avoid the temptation to overstock. As a result, you can prevent increased carrying and storage costs caused by overstocking. In addition, having parts on hand improves planned maintenance workflows, resulting in fewer repeated repairs and wasted resources.
Ready to start working towards these benefits? Let’s look at how to create and implement a digital inventory management system for your team.
Create a digital inventory management system
STEP 1: Prepare and organize your inventory data
Carry out the following actions to ensure your data is well organized and ready for your new system.
Perform an inventory audit
Begin by conducting a comprehensive audit of your current inventory. Categorize and record your most critical or most used parts, assigning and documenting unique identifiers to each one. Once finished with these parts, add other parts to the inventory using the same system of unique identifiers. Make room in your identifier system to scale up as your inventory needs grow.
Conduct physical verification
The next step is to physically verify the data’s accuracy. Conduct a physical count of inventory items to be sure their descriptions, conditions, and locations match your records. In preparation for your new digital system, create unique QR codes for each item and affix them to each item or location to track usage. Alternatively, if you are already using a CMMS with a robust parts inventory module, the CMMS may be able to create QR codes for you.
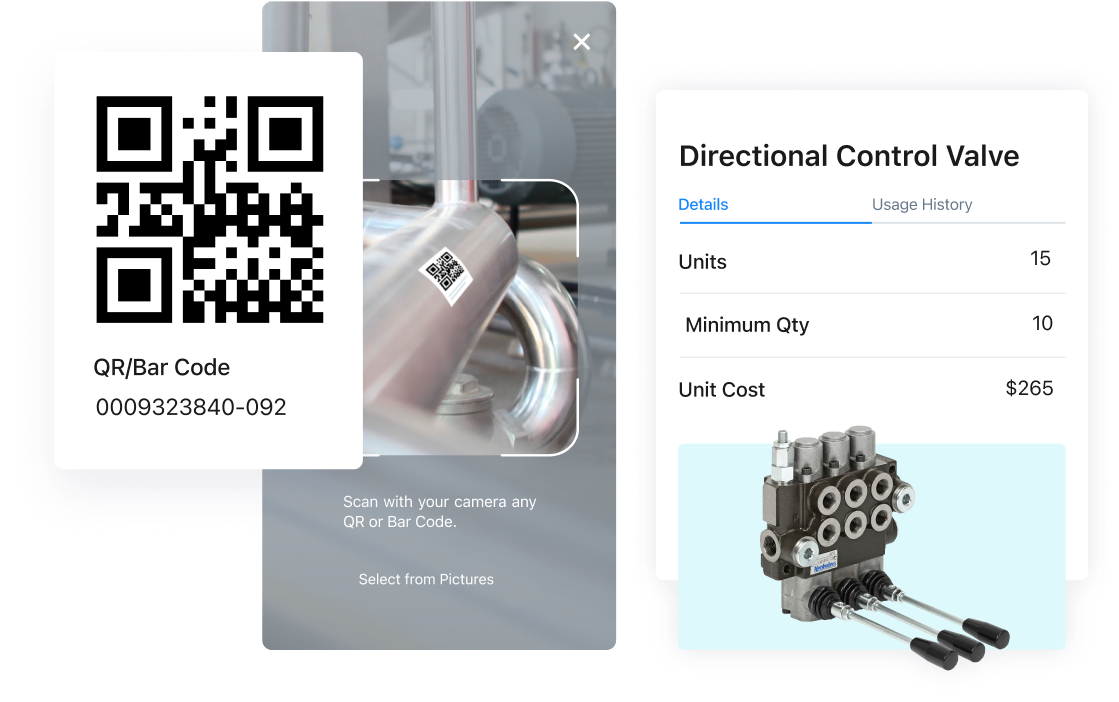
Confirm digitization readiness
Done verifying your data? Convert cleaned and standardized inventory data to a digital format suitable for import into the digital inventory system. The inventory system will typically use CSV or Excel formats.
STEP 2: Select the right digital inventory management system to house the data
The next step is to find the digital solution for your needs. Remember, automation involves using technology to perform tasks with minimal human intervention, so you want to look for features that reduce the need for your oversight.
Select the digital solution
With your data in order, explore the range of digital inventory management options available. Crucial features to consider are barcode and QR code scanning, integration capabilities with existing business software, mobile functionality, and real-time parts tracking. User-friendliness is also a vital element, so be sure to carry along and seek the input of frontline workers who will be engaging with the new system.
Weigh the return on investment (ROI) of a system focused solely on inventory management vs. a full-suite work order management system with inventory management features. For example, with a computerized maintenance management system (CMMS) offering features like low inventory alerts, parts histories, and inventory reporting, you get the benefits of a robust inventory management system alongside other maintenance management features like work order scheduling, real-time updates, and in some cases, AI-powered maintenance operations like SOP generation. Consider the cost of these options and research customer reviews to decide which vendors to approach.
Remember, the digital platform that best fits your needs is the one that both you and your teams will consistently use. You're not just transitioning your company’s inventory records to a digital format but leveraging this change to create an improved maintenance culture across your team.
STEP 3: Set up the digital inventory management system
Okay, now that you have the required data in hand and the right system in place, the next step is to import that data into the CMMS.
1. Carry out a test import with a small subset of your already converted parts data. Map your data fields to the corresponding fields in the digital inventory system, adjusting as necessary to fit the required formats. Troubleshoot any issues with your service provider.
2. Once you’ve verified that the system runs fine and imports your data accurately, proceed with the full import. Then, check again for accuracy.
STEP 4: Build the necessary workflows to automate inventory management
After importing your parts data into the CMMS, define and create your workflows for managing the inventory. In addition to using QR codes and barcodes that workers can scan to access assets quickly, you can create work orders with direct links to the parts needed to complete the work.
With a robust digital inventory system, other features to use in automating your parts management include:
Automatic reordering
With the right CMMS, you can create automated low-quantity alerts and triggers to purchase orders for stock.
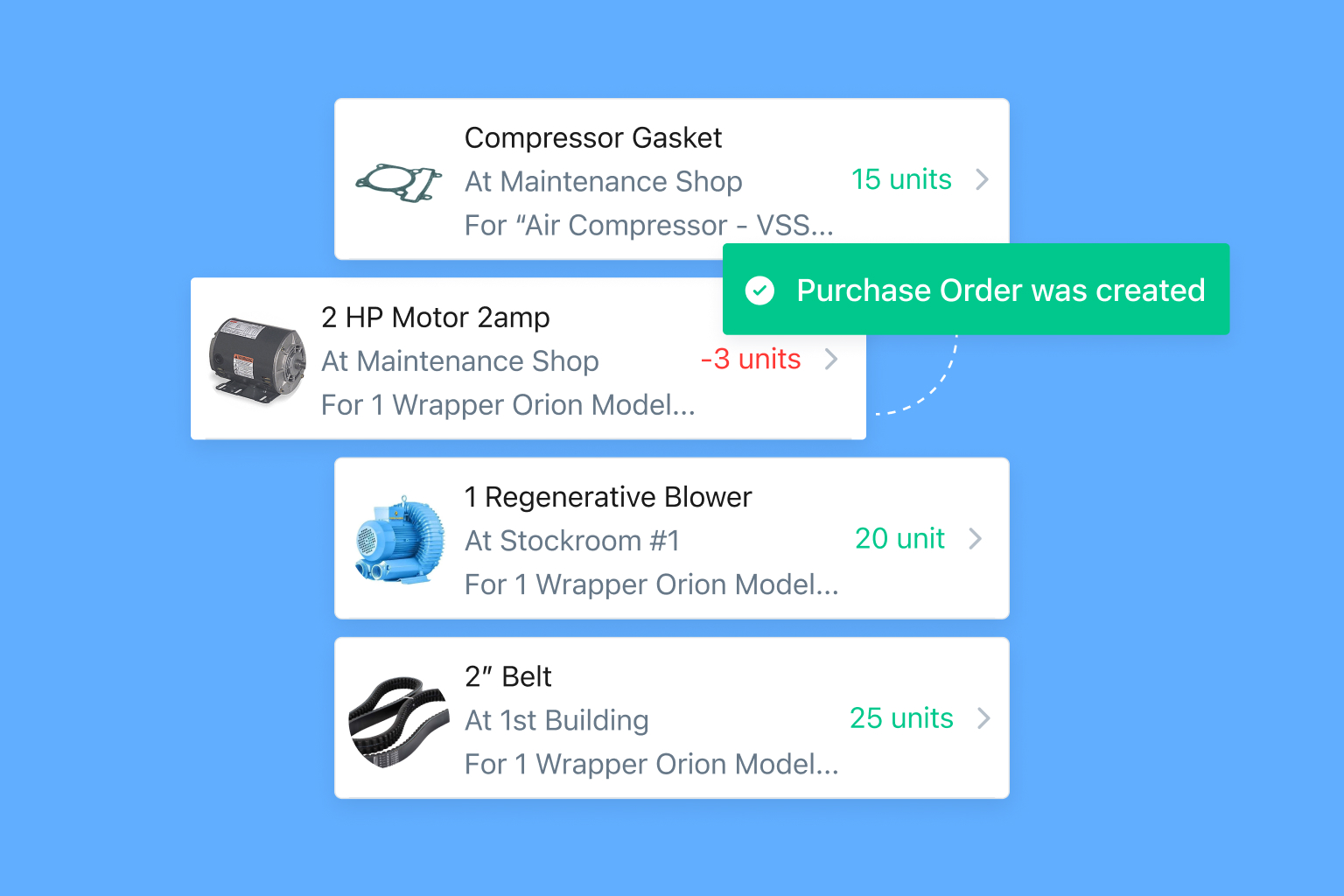
For example, to set a Minimum Quantity Trigger in MaintainX for a specific part in your inventory, navigate to the Parts Inventory tab and select the part to trigger an alert. Select “Edit Part” from the menu next to the “Restock” option. Scroll to the “Minimum in Stock” field and set the minimum quantity for the selected part. Click “Update” to save your trigger. You will now receive an alert when stock levels approach the defined minimum threshold.
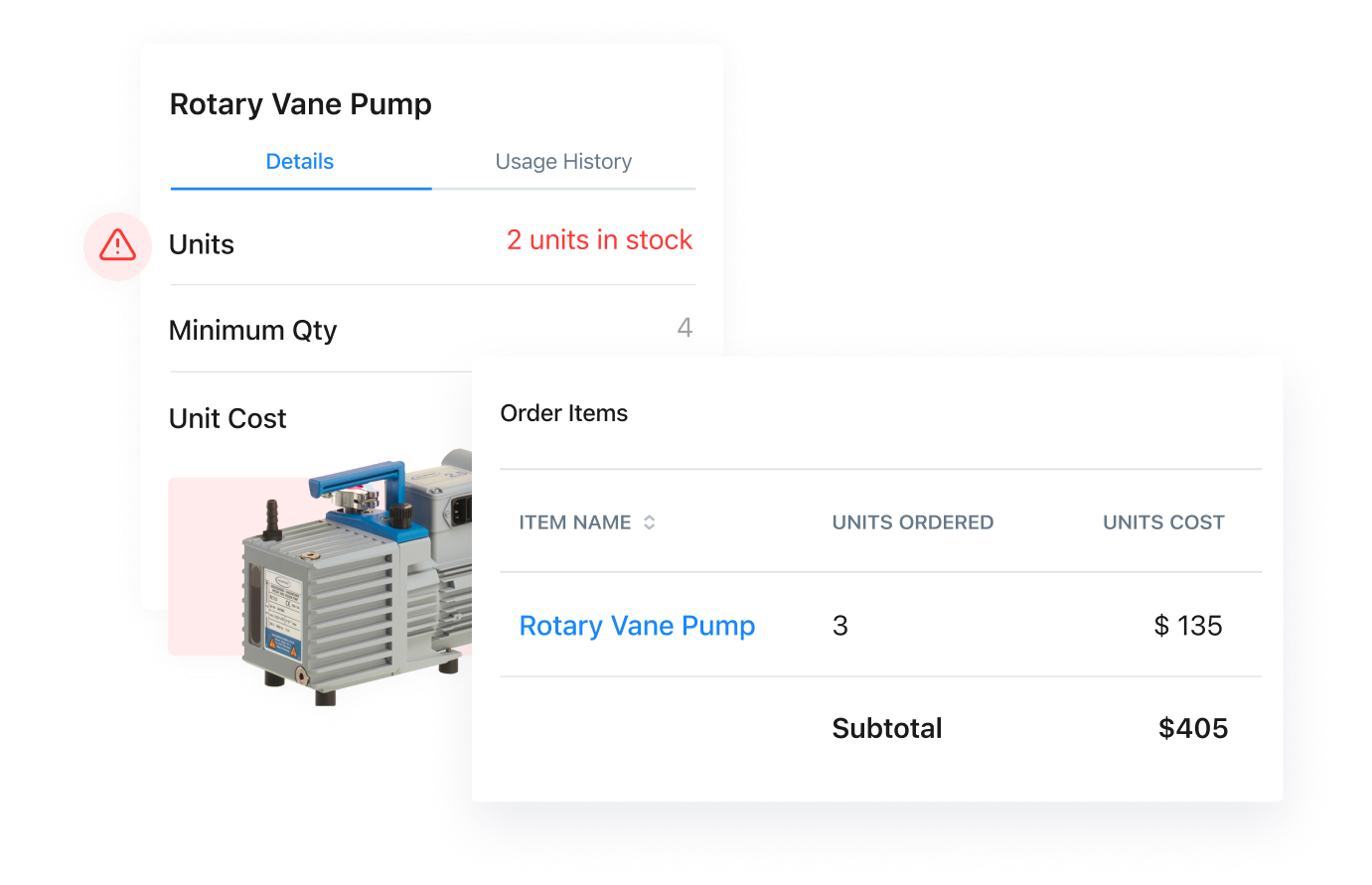
Real-time updates
This feature automatically updates inventory levels as team members use, move, or replace parts.
To restock a part in MaintainX, go to the Parts Inventory tab and select the part that needs restocking. Click “Restock” and adjust the part quantity by either increasing or decreasing the quantity as needed. Be sure to input the restock unit cost for accurate financial tracking. You can attach any relevant pictures or files for further clarification or recordkeeping purposes. To complete the process, review your entries, confirm the restock, and save the updated inventory information to keep everything up to date.
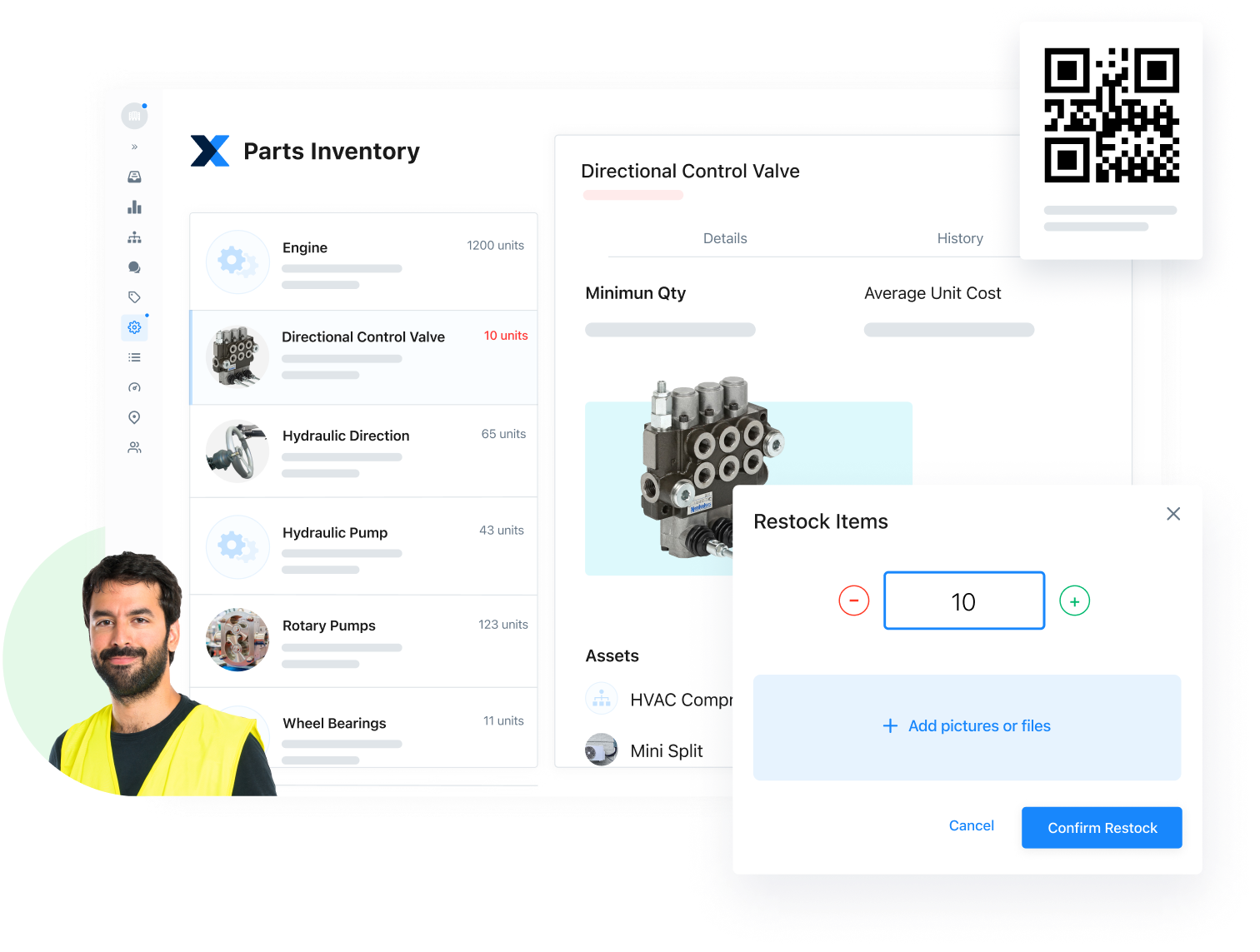
Throughout the above steps, take care to carry along your frontline workers, communicating necessary information about the coming changes. With all the essential components set up, it’s time to provide hands-on training to ensure they will get the most out of the system.
STEP 5: Training and user adoption
Change management is a significant element when introducing any new system to the workplace. Be proactive in training your teams to understand the specific systems you introduce and the broader inventory management practices you implement. Take particular time to educate your workers on the following:
- System navigation: If you’ve selected an intuitive and user-friendly solution, then your team members shouldn’t have much trouble here. Regardless, ensure they understand the meanings of all relevant pages and prompts in the app.
- Data entry and update: Ensure your workers know how to execute real-time updating of records when they take parts out of inventory or add new parts.
- Reporting and analytics: Reporting tools can turn inventory data into actionable insights. Be sure that your team members are familiar with these features, can interpret the data, and feel empowered to take action
Other tasks to ensure your team members fully understand include handling inventory transactions, managing suppliers and purchase orders, and quality control and auditing.
Training your team in digital inventory practices can help improve the accuracy and efficiency of inventory management processes. Equipping employees with the necessary skills ensures reliable data management, streamlined workflows, and improved collaboration, leading to time and cost savings, as well as increased overall productivity.
Never stock out again: Digitize your inventory management with MaintainX
Ready to digitize your inventory? MaintainX offers features including low inventory alerts, QR and barcode scanning, full inventory reporting, and cost tracking, alongside robust work order management features like work order templates, digital audit trails, and reporting dashboards.
Book a tour of MaintainX to see how you can take your inventory and maintenance management to the next level.
FAQs
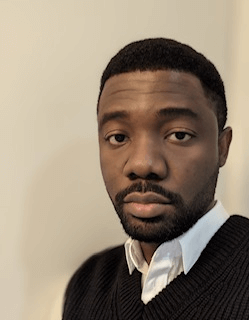
Lekan Olanrewaju is a content writer with years of experience in media and content creation. He has held positions at various media organizations, working with and leading teams at print magazines, digital publications, and television productions.