Industry 4.0 has introduced manufacturers to a range of new technologies. While these technologies make factory floors more efficient, they require a framework that enables systems to communicate accurately and efficiently. That’s where the ISA-95 standard helps.
ISA-95 (Enterprise-Control System Integration) is an international standard for integrating enterprise and control systems. The standard enables the development of an interface for communication between various levels of a manufacturing enterprise. It is based on the Purdue Reference Model for computer-integrated manufacturing (CIM).
Imagine a busy car manufacturing plant. On the factory floor, robots assemble chassis and workers install engines. In corporate offices, executives set production targets and manage supply chains. Between these two levels, other managers track production and schedule maintenance. ISA-95 provides a common language and framework to ensure stakeholders across all these levels can communicate easily.
This article explains what ISA-95 is (also known as ANSI/ISA-95, IEC 62264, and the Purdue model for industrial control systems), the different levels of the ISA framework, and why this standard is critical to ensuring clear and consistent communication protocols between automated equipment, controls, and software.
Why is ISA-95 important?
ISA-95 specifications create common information models and terminology, making the exchange of data between enterprise systems, control functions, and manufacturing operations systems frictionless. It is applicable to all industries and is designed to facilitate clear communication between your organization, your hardware/software suppliers, and your supply chain. It’s also immune to most technological upgrades.
In 1995, the International Society of Automation (formerly the Instrumentation, Systems, and Automation Society) and the American National Standards Institute developed ISA-95 as a successor to the ISA-88. The new framework includes guidelines for incorporating modern technologies like IoT, digital sensors, and smart machinery into a standardized format.
Without this universally accepted data exchange framework, it would be nearly impossible to connect sensors, actuators, controllers, and manufacturing processes across thousands of different pieces of equipment and types of software.
Systems wouldn’t ‘talk’ to each other in a universal language, which would make it incredibly difficult for businesses to integrate different parts of their production process successfully.
5 Levels of the ISA framework
The ISA framework includes a structured hierarchy of five levels that describe the flow of information and activities within an organization, from the plant floor up to the enterprise level. Here are the levels of the ISA-95 framework:
- Level 0: Production process
- Level 1: Sensing and manipulation
- Level 2: Monitoring and supervision
- Level 3: Manufacturing operations management
- Level 4: Business planning and logistics
Levels 0-2 include activities directly involved in manufacturing and information about materials, personnel, and equipment. This includes elements such as plant safety, reliability, efficiency, product quality, and regulatory compliance.
Level 3 includes activities related to manufacturing operations, such as optimizing the production process.
Level 4 includes business planning and logistics decisions, such as production levels and material type.
With that in mind, here’s a more detailed look at each level.
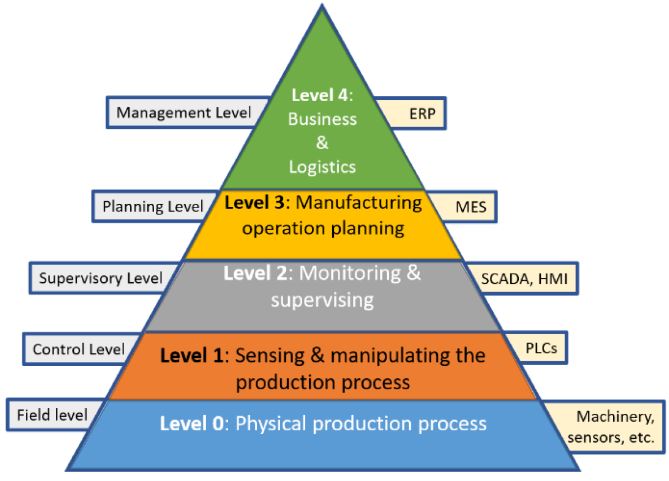
Level 0: Production Process
This level defines the actual physical production processes that generate the data you need to collect for your automation system.
Level 1: Sensing and Manipulation
Level 1 is closest to your factory floor and assets and includes sensors and valves. The sensors and other IoT devices you use on the factory floor collect data from manufacturing processes and transmit the data to a controller or subsystem.
Level 2: Monitoring and Supervision
This level includes the I/O subsystems, logic solvers, and DCS controllers. The systems and controllers at this level supervise and regulate the manufacturing environment.
For example, an accelerometer might transmit vibration data to a programmable logic controller (PLC), which may turn off the machine when the vibrations go above or under an acceptable level.
You can apply this process to any sensor-control system combination if you connect the sensors with the subsystems, logic solvers, or controllers using IIoT (Industrial Internet of Things).
Level 3: Manufacturing Operations Management
Level 3 involves workflows that help achieve goals such as production scheduling, workload balancing, and optimizing production using a manufacturing execution system (MES).
This level involves using software solutions such as computerized maintenance management systems (CMMS), supervisory control and data acquisition (SCADA), and advanced process control (APC) to manage various functions at your plant. These functions include quality, production, information integrity, and maintenance.
The workflows in level 3 aren’t limited to controlling equipment – they also direct people to take action to integrate the plant’s automatic and manual activities.
Level 4: Business Planning and Logistics
Level 4 defines administering business-related activities and plans through enterprise systems, such as an ERP system, CMMS, and CRM. These systems use data from level 3 as input to make smarter decisions. This level is where production teams decide how much to produce and what type of raw materials to use.
8 Parts of the ISA-95 Standard
ISA-95 standards are divided into six parts:
Part 1 – Models and terminology
Part 1 includes terminologies and object models (hierarchy models, object models, operations activity models, and functional data flow models) required to communicate between enterprise systems, manufacturing operations, and control functions.
Part 2 – Object model attributes
Part 2 defines models and tables for each object defined in Part 1, as well as the information and the structure of the information the ERP system should transmit to the MES.
Part 3 – Activity models of manufacturing operations management (MOM)
Part 3 includes MOM activity models that facilitate the integration of enterprise systems with the control system. An activity model is an activity diagram that explains the sequence of steps required to form a complex process.
Part 4 – MOM object models and attributes
Part 4 defines object models and attributes that inform the information exchange between MES activities (as defined in Part 3).
Part 5 – Business-to-manufacturing transactions
Part 5 describes how enterprise systems exchange information with manufacturing and automation systems at levels 3 and 4 of ISA-95. Part 5 relies on models defined in Parts 1 and 2 and defines transactions related to the exchange of objects that the ISA-95 defines in Parts 2, 4, and 5.
Part 6 – Messaging service model
Part 6 defines a messaging service model that enables applications performing business and manufacturing activities across levels 3 and 4 and within level 3 to exchange information.
Part 7 – Alias service model
This part defines a global namespace to enable accurate data exchange between systems. The namespace is a naming convention. It enables data conversion from local to global names across every integration within your manufacturing system.
Part 8 – Information exchange profiles
Part 8 describes the framework for connecting digital tools, such as software systems, in a standardized way. Software that is ISA-95 compliant and has messaging models that comply with Part 6 and global names described in Part 7 can generally be integrated easily with other ISA-95-friendly software.
How MaintainX supports ISA-95 compliance
Optimize your asset and equipment management
MaintainX CMMS centralizes asset tracking and management, which aligns with ISA-95’s goal of optimizing resource management. It also supports asset digitization and lifecycle tracking, a crucial aspect of maintaining operational efficiency.
Track everything with digital work orders
MaintainX’s digital work orders can help your business ensure that every maintenance task is assigned, tracked, and completed efficiently for more operational control, faster work execution, and better cost savings. For example, Duracell reduced stock variability to save an estimated $50,000 a year by synchronizing parts inventory data automatically between MaintainX and SAP.
Unlock a birds-eye view with reporting & analytics
Data-driven decision-making is a core aspect of ISA-95 – MaintainX provides the detailed insights you need into maintenance activities, asset health, and operational performance. Dashboards, reports, and historical data give you reliable information to make confident decisions.
Supervise inventory & parts management
MaintainX helps streamline inventory tracking and management, ensuring that when work orders are assigned the necessary parts are actually available. Align with the ISA-95’s requirements for resource management and inventory control, and ensure your maintenance technicians are performing repairs efficiently with the tools and parts they need.
Integration capabilities
MaintainX integrates with industry-leading ERP systems like SAP and Microsoft Dynamics, supporting seamless information exchange between enterprise management and control systems. Multiple integration options extend your system’s functionality further, connecting PLC’s, sensors, inventory systems, accounting software, and more into one efficient ecosystem.
Try MaintainX for free to streamline your manufacturing and maintenance processes and enable faster digital transformation for your organization.
ISA-95 FAQs
Yes, as manufacturing facilities and production plants become more connected and digitally driven the ISA-95 framework is still very important. The universal adoption of ISA-95 ensures the myriad pieces of digitally enhanced equipment in your plant are compatible with each other, with different software packages, and with common production processes. While not completely watertight, it sets the majority of digital integrations up for success by providing enough commonalities to connect and run disparate systems.
A Manufacturing Execution System (MES) is software that monitors, controls, and documents the production processes happening on the shop floor. The data recorded from machinery and sensors on the shop floor is available in real-time within all integrated systems, allowing production planners, inventory controllers, and maintenance managers to make more informed decisions thanks to the connectivity of many different elements.
ISA-95 does not include specific guidelines for how to implement each part of the model, and which architecture to use. Some manufacturing systems and processes sit outside the recommended framework, which can create uncertainty around how to approach different integration steps. This leads to manufacturers creating bespoke workarounds that suit their operation but may not be compatible with a different process added at a later date.
ISA-95 models provide the common language necessary for enterprise resource planning (ERP) and physical process control systems to 'talk' to each other. Connecting your ERP with ISA-95-aligned sensors and processes through an API layer allows machines and software to communicate and for people to manage production more efficiently. When properly implemented, this reduces the risks, costs, and potential errors that come with creating a holistic manufacturing execution system.
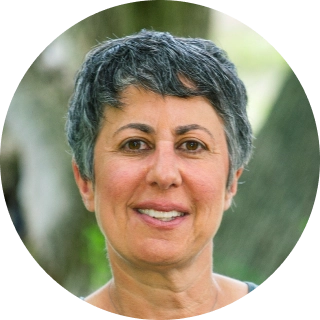
Caroline Eisner
Caroline Eisner is a writer and editor with experience across the profit and nonprofit sectors, government, education, and financial organizations. She has held leadership positions in K16 institutions and has led large-scale digital projects, interactive websites, and a business writing consultancy.
See MaintainX in action