Operations managers have long focused on physical asset maintenance, keeping equipment running day-to-day. Now, leading companies are expanding that view to physical asset management, a broader strategic discipline that maximizes the value, performance, and lifespan of physical assets.
This shift transforms a narrow maintenance-centric mindset into a comprehensive strategy that manages an asset's entire lifecycle in alignment with business goals to ensure long-term operational success.
In this guide, we'll explore the evolution from simply maintaining assets to managing them as strategic resources. You’ll also learn updated definitions, real-world benefits, actionable best practices, and guidance on implementing the right technology solutions.
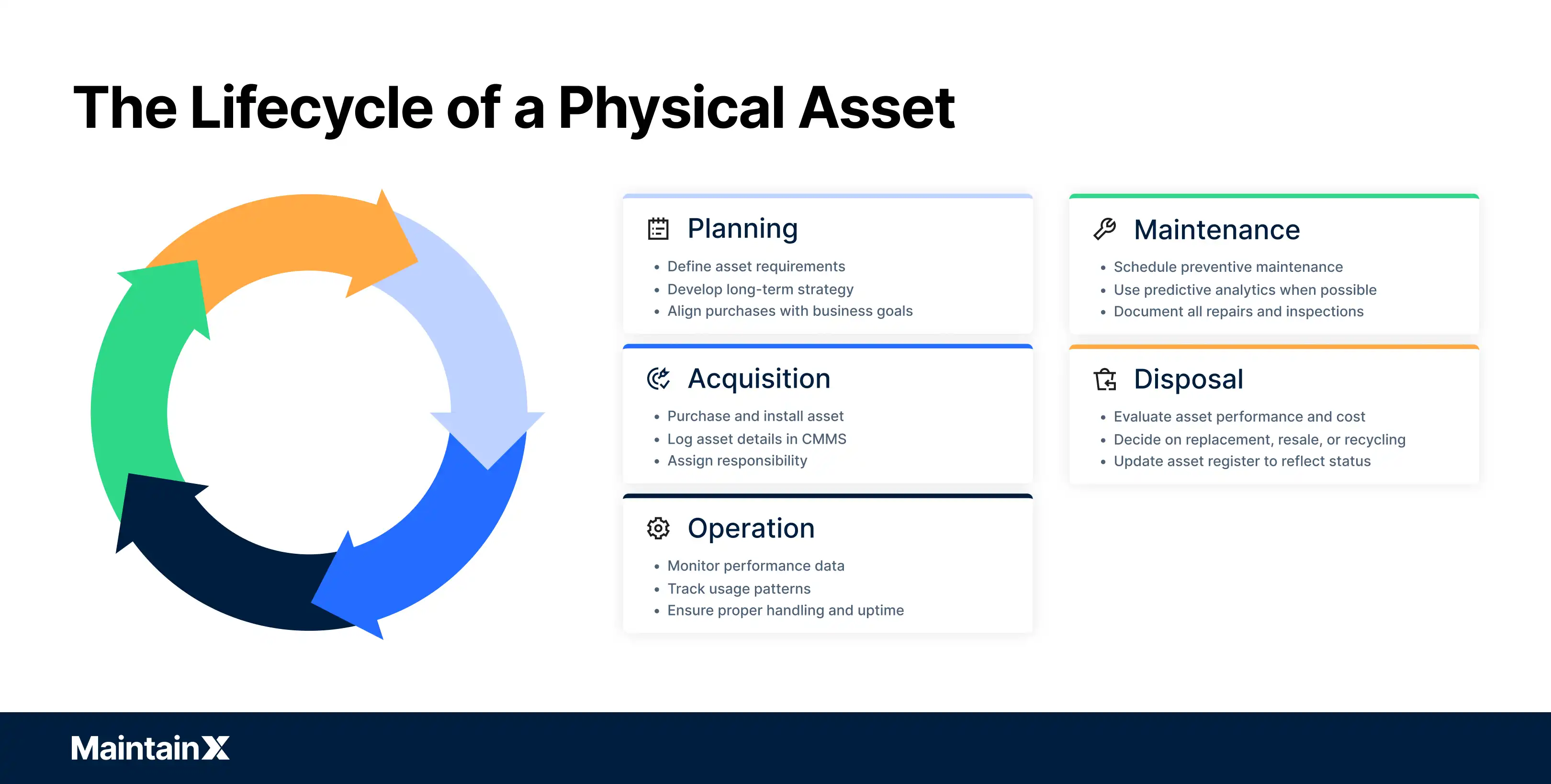
Key takeaways
- Physical asset management encompasses the entire asset lifecycle, while maintenance is just one component of this broader strategy.
- Strategic asset management extends asset life, improves reliability, reduces costs, and enhances operational performance.
- Data-driven decision-making enables continuous optimization of asset performance and maintenance schedules.
- Investing in integrated asset management software provides centralized visibility, automation, and analytics for improved ROI.
- Developing a formal asset management strategy helps identify and mitigate risks related to asset failure and ensures regulatory compliance.
What is physical asset management?
Physical asset management is a comprehensive approach to managing tangible assets throughout their entire lifecycle: planning, acquisition, operation, maintenance, and eventual disposal. Physical assets include equipment, machinery, vehicles, facilities, infrastructure, and other tangible items that support an organization's operations.
Unlike financial asset management (which focuses on investments like stocks and bonds) or intangible asset management (which handles intellectual property), physical asset management specifically addresses the fixed, tangible assets critical to operations. These assets typically represent significant capital investments and directly impact an organization's ability to operate efficiently, safely, and profitably.
The benefits of physical asset management
Adopting a strategic physical asset management program yields significant benefits for business operations.
Extended asset life and reliability
Proactive management leads to better care of equipment, directly improving asset longevity and reliability. Assets that are well-managed typically have longer lives, delivering higher returns on investment and deferring replacement costs. Strategic management ensures assets run safely and efficiently, far beyond their expected lifespan.
Cost efficiency and operational performance
A comprehensive asset management approach optimizes the entire asset lifecycle. By analyzing performance data and making strategic decisions about deployment, organizations reduce costs while improving operational performance. Leading companies using technology-enabled asset management have significantly improved bottom-line results through enhanced asset utilization.
Risk reduction and compliance
A formal asset management strategy helps identify and mitigate risks related to asset failure, safety concerns, and regulatory compliance. This strategic approach serves as effective risk management, protecting companies from downtime, accidents, legal issues, and reputational damage.
Asset maintenance vs. asset management
It's important to clarify the difference between asset maintenance and asset management, as they represent two distinct but related concepts.
Asset maintenance refers to the routine tasks and processes required to keep assets in good working order, including repairs, lubrication, inspections, and part replacements to prevent equipment failure. Maintenance is primarily focused on preserving the operational condition of existing assets.
The world is moving away from this constrained approach. As McKinsey found in a 2023 survey, “Asset productivity is a universal priority: 99 percent of respondents told us their organizations had undertaken a maintenance transformation in the past five years. Most respondents are also seeking to take advantage of new technologies and methodologies.”
Meanwhile, physical asset management covers the entire lifecycle and productivity of assets. It includes strategic activities like:
- Asset planning and acquisition
- Asset performance tracking and analysis
- Risk assessment and mitigation
- Resource allocation and optimization
- Replacement and disposal decisions
Asset maintenance is, therefore, a critical component of asset management. However, physical asset management goes much further to include strategic decisions about which assets to acquire, how to deploy them, when to replace them, and how to maximize their value throughout their lifecycle.
To illustrate, consider a fleet of vehicles:
- Maintenance involves keeping each vehicle running through oil changes, brake repairs, and other routine maintenance services.
- Management consists of deciding when to acquire or retire vehicles, tracking utilization patterns, analyzing performance data, and strategically allocating resources based on business priorities.
By shifting from a narrow maintenance outlook to a strategic management approach, operations leaders can make sure assets are not only maintained but also optimized for reliability, performance, and value throughout their lifecycle.
Organizations that successfully implement comprehensive asset management programs often leverage specialized asset management software to coordinate these activities. Enterprise asset management (EAM) solutions represent a more advanced evolution of basic maintenance systems, offering extensive functionality for tracking assets throughout their complete lifecycle.
As businesses mature in their asset management practices, they typically progress from simple maintenance tracking to sophisticated asset management software platforms. These systems integrate with other enterprise systems and support data-driven decision-making across the organization.
Best practices for proactive asset maintenance
A cornerstone of effective physical asset management is proactive maintenance, anticipating and preventing problems before they occur, rather than simply reacting after failures. Here are actionable best practices:
Use standardized checklists and inventory tracking
Implementing standardized checklists and inventory management is one of the simplest yet most effective practices. Checklists ensure technicians perform all necessary steps during inspections, servicing, and safety checks, helping to catch potential issues early.
Maintaining an accurate asset inventory, including an equipment registry with details like model, location, and maintenance history, and a spare parts inventory, means you have the right information and components available to perform preventive repairs in a timely and organized way.
While paper checklists can work, digitizing and automating them through a modern asset management system improves efficiency and consistency. Digital systems can alert teams when checklist items are missed or when parts inventory runs low, reducing delays and keeping critical maintenance tasks from slipping through the cracks.
Implement preventive maintenance schedules
Preventive maintenance involves servicing equipment at planned intervals based on time, usage, or condition to prevent breakdowns. This could mean routine lubrication every month, replacing filters after specific hours of runtime, or performing annual safety inspections.
Establishing thorough preventive maintenance schedules for all company assets is essential to avoid the trap of purely reactive repairs. Just as you change the oil in your car regularly to keep the engine healthy, industrial assets require periodic care to operate cost-effectively.
A good maintenance management program treats preventive maintenance as a dynamic process, continuously refining schedules based on experience and data. Adjust service frequency if you find an asset could be maintained less often without issues, or increase frequency if data reveals emerging problems.
This optimization balances resource utilization (technician time, spare parts) and helps reduce maintenance costs by addressing issues early when they are less expensive to fix.
Leverage predictive maintenance technologies
Predictive maintenance takes prevention to the next level by using data and technology to forecast when failures might occur. Sensors, industrial IoT devices, and analytics software monitor asset conditions in real time, tracking metrics like temperature, vibration, pressure, or runtime hours.
These data feeds are analyzed for warning signs so maintenance can be performed right before a problem develops. This approach minimizes unnecessary maintenance while preventing most unexpected breakdowns.
To get started, identify critical equipment and deploy sensors or leverage existing PLC/SCADA data. Use predictive analytics tools to interpret the data and identify emerging issues. Even monitoring vibration on your most critical motors can yield quick wins by preventing major unexpected failures.
Use data for informed decision-making
Today's physical asset management strategies should be heavily data-driven. Every work order, inspection finding, and sensor reading provides valuable information that can inform better asset decisions.
Tracking failure trends might reveal that a certain machine fails every 18 months, on average, so you can proactively replace components at 17 months to prevent downtime. Monitoring maintenance costs per asset can highlight when an asset becomes too expensive to maintain and should be replaced.
Establish relevant key performance indicators (KPIs) such as mean time between failures (MTBF), mean time to repair (MTTR), overall equipment effectiveness (OEE), and maintenance cost as a percentage of asset value. Track these metrics over time and review them regularly to guide continuous improvement.
Data-driven decision-making transforms maintenance from guesswork into a science, allowing for proactive management based on evidence rather than intuition. This approach significantly improves asset performance and reduces waste over time.
Empower and train your maintenance workforce
Even with the best processes and technology, success in physical asset management ultimately depends on people. Invest in your team through training and workforce enablement to ensure maintenance staff are up-to-date on equipment knowledge, safety practices, and digital tools.
Empower technicians with mobile devices running modern computerized maintenance management software (CMMS)/EAM applications so they can access work orders, checklists, and asset history on the go.
Consider upskilling technicians in advanced diagnostics like vibration analysis, thermography, or data analysis so they can participate in predictive maintenance efforts. Foster a culture where maintenance teams are proactive problem-solvers rather than just firefighters.
A workforce armed with the right skills and tools will naturally take more ownership of asset care, leading to more consistent preventive actions, quicker issue resolution, and innovative solutions that improve reliability.
Invest in the right physical asset management software
Modern physical asset management software integrates maintenance with asset tracking, inventory, and financial analysis to provide a unified platform for comprehensive asset management. Here's why investing in a robust system yields high returns:
- Centralized asset repository: Creates a single source of truth for all asset information, from purchase details to maintenance records, to eliminate data silos.
- Process automation: Streamlines routine workflows like maintenance scheduling and inventory management with seamless integration across departments.
- Data-driven insights: Provides analytics dashboards that quantify ROI through key metrics like downtime reduction and maintenance costs, supporting better decision-making.
- Compliance management: Ensures proper documentation of all activities with audit trails, supporting regulatory requirements, and risk management.
Investing in dedicated asset management software delivers exceptional ROI throughout your organization's asset management journey. As digital transformation continues to reshape maintenance operations, these systems will increasingly incorporate AI and machine learning capabilities to deliver even greater predictive insights and automation opportunities.
FAQs on Physical Asset Management
A physical asset manager is a professional responsible for overseeing the complete lifecycle of an organization's physical assets, including planning, acquisition, maintenance, optimization, and disposal. They develop strategies to maximize asset value, reliability, and performance while minimizing costs and risks, and often use data analytics to make informed decisions about asset investments and maintenance priorities.
Physical assets include machinery and equipment (production lines, CNC machines, HVAC systems), vehicles (trucks, forklifts, company cars), facilities (buildings, warehouses, retail locations), infrastructure (pipelines, electrical systems, roads), IT hardware (servers, computers, networking equipment), and tools and instruments used in operations. These tangible assets typically represent significant capital investments that directly support an organization's ability to operate.
A physical asset management strategy is a documented plan that outlines how an organization will manage its physical assets to achieve business objectives. It typically includes approaches for asset acquisition, maintenance methodologies (preventive, predictive, condition-based), performance monitoring, risk assessment, resource allocation, technology implementation, and retirement/disposal procedures. An effective strategy aligns asset decisions with organizational goals while optimizing the balance between asset performance, cost, and risk throughout the entire asset lifecycle.
See MaintainX in action