This guide explains what visual inspection is, the various techniques used, its applications across industries, the benefits it offers maintenance professionals, and potential challenges to be mindful of when using visual inspection as an asset-management or quality control method.
Visual inspection techniques include traditional methods using the human eye, remote visual inspection with tools like drones and cameras, and automated visual inspection powered by AI. These techniques are widely applied across industries such as manufacturing, plant maintenance, and energy and utilities, where they play a critical role in ensuring safety, preventing downtime, and maintaining quality standards. Maintenance professionals benefit from early detection of issues, improved efficiency, and cost savings, though challenges such as reduced uptime and reliance on human expertise remain important considerations.
What Is a Visual Inspection?
Visual inspection is the process of examining objects or systems using the human eye to detect surface-level defects, damage, or irregularities. It is often the first step in quality control, safety checks, or maintenance and does not require specialized tools unless enhanced with aids like magnifiers or cameras.
However, this type of inspection doesn’t necessarily only involve the inspector’s vision. Experienced professionals also can determine the presence of issues based on specific sounds that machines make or fumes from machines (such as gas in the case of a leak). Because there is no specific VI procedure to determine an issue, the effectiveness of visual inspection depends largely on an inspector’s experience.
While traditional visual inspection is still in everyday use, modern visual inspection techniques now include remote cameras, drones, condition monitoring sensors, and automated systems powered by artificial intelligence and machine learning.
“New digital and analytics technologies make it easier for quality teams to access data from different sources and in various formats, without replacing existing systems.” McKinsey
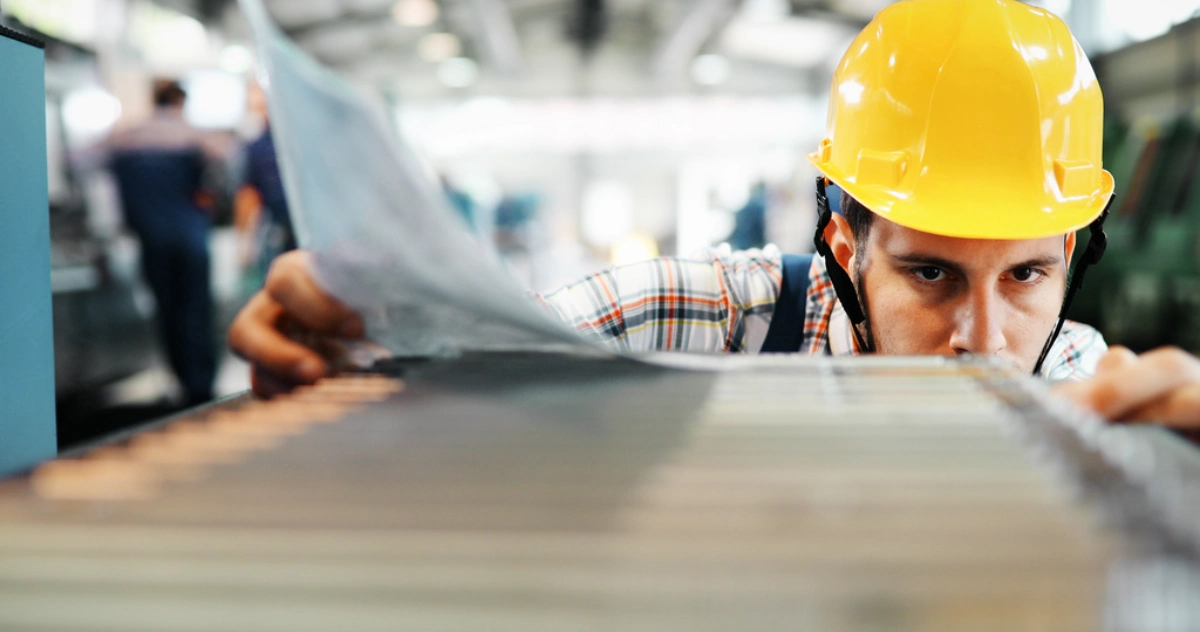
Visual Inspection (VI) Techniques
Visual inspection can cause reduced uptime. The traditional way of inspecting machines requires turning them off, which can impact production efficiency. It’s a reactive maintenance technique. These days, maintenance professionals rely on preventive maintenance techniques.
That said, VI is far from obsolete. Plus, technological improvements make visual inspections easier. For example, maintenance professionals can now use remote cameras, drones, and AI systems to inspect areas of equipment that are hard to reach or housed in locations with hazardous materials.
Modern visual inspection techniques can be broadly classified as:
- Remote visual inspection
- Automated visual inspection
Remote Visual Inspection (RVI)
Nowadays, VIs don’t need to be conducted at the asset’s location. Instead, inspectors can use high-quality cameras and other RVI tools to collect visual data remotely.
Generally, inspectors use RVI tools when the inspection area is either dangerous or difficult to reach, or both. For example, if the site you want to inspect is miles away from your current location, you can use remote cameras, a robot, or drones to inspect the site visually.
You can inspect the asset live as the camera streams directly to your current location, ensuring your safety even when inspecting a dangerous location like a mine shortly after blasting. It’s also possible to record footage on a camera if the location lacks network capabilities. Once you access the camera, you can review the recorded footage for potential issues.
Even if you live-stream the footage, be sure to record it. This allows other members, such as engineers and technicians, to view the footage later in case you need their opinion.
Automated Visual Inspection (AVI)
As with most industries, automation is useful for visual inspection. Automated visual inspection (AVI) relies on artificial intelligence (AI) to capture visual information through cameras.
AI works the same way with visual inspection systems as with anything. First, provide the algorithm with a sample of a well-manufactured product. You can also add a few defective product samples, so the algorithm learns what it needs to look for in a defective product.
Once implemented, the AVI system will inspect every product you manufacture. The system detects defects by capturing the product’s image from multiple angles and comparing it with the pictures of the well-manufactured sample you fed into the algorithm during setup.
Similar to how it works for quality control, you can use AVI to inspect equipment visually. AVI frees up time spent on repetitive tasks to let you focus on what’s essential: timely maintenance and repairs.
Applications of Visual Inspection Across Industries
Visual inspection (VI) is a critical quality control and safety assurance method employed widely across diverse industries. It involves systematically examining products, components, or infrastructure to identify defects, ensure compliance with standards, and maintain operational integrity.
Manufacturing
Visual inspection is essential for detecting surface defects, assembly errors, and component misalignments to maintain product quality and safety. Automated Visual Inspection (AVI) systems are widely used to improve defect detection efficiency and process optimization. For example, automotive manufacturers use AVI to detect paint defects and alignment issues, while electronics industries inspect circuit boards for solder joint defects.
Oil & Gas
The oil and gas sector relies heavily on visual inspection to maintain infrastructure integrity and prevent environmental hazards. Key applications include inspecting pipelines for corrosion and leaks, monitoring storage tanks and pressure vessels for wear, and using drones or robotic crawlers for inspecting offshore platforms and subsea structures. This helps detect early signs of damage, fatigue, or corrosion, ensuring safe operations and regulatory compliance.
Automotive
Visual inspection is crucial for examining vehicle components such as car bodies, engines, and brakes to identify wear and tear, cracks, or alignment issues. This ensures vehicle safety and performance, with automated systems increasingly used to enhance accuracy and throughput in production lines.
Aerospace
Due to stringent safety regulations, aerospace visual inspection focuses on detecting cracks, stress fractures, and dimensional deviations in aircraft parts. 3D cameras and depth sensors provide precise dimensional analysis of complex components, verifying compliance with tight tolerances critical for flight safety.
Pharmaceuticals and Medical Devices
Visual inspection ensures that products are free from contamination, packaging is intact, and labels are accurate. This is vital to meet strict regulatory standards and maintain product safety. Automated inspection also verifies the proper assembly of medical devices and the presence of all required components.
Construction
In construction, visual inspection is used to assess the structural integrity of buildings, bridges, and other infrastructure. Inspectors look for cracks, material degradation, and compliance with building codes. Remote visual inspection technologies, including drones, are increasingly used to access hard-to-reach areas and provide detailed condition assessments.
By applying visual inspection across these industries, organizations can enhance safety, ensure compliance, and maintain operational efficiency.
Benefits of Visual Inspection
Implementing visual inspection in your quality control processes offers several key benefits that make it a valuable tool across industries:
Cost-Effective
Visual inspection is one of the most economical methods for detecting defects early in the production or maintenance process. By identifying issues before they escalate, it helps reduce the need for expensive repairs and replacements, leading to significant cost savings.
Efficiency
This method allows for the quick identification of obvious defects, minimizing downtime and ensuring equipment uptime. In industries where continuous operation is critical, such as manufacturing and logistics, visual inspection helps maintain productivity and meet tight production deadlines.
Safety Enhancement
Early detection of potential issues through visual inspection contributes to a safer working environment. By identifying equipment failures or hazards before they occur, visual inspection helps prevent accidents and injuries, enhancing workplace safety standards.
Versatility
Visual inspection is highly versatile and can be applied to a wide range of assets and industries. From inspecting confined spaces to large industrial equipment, it adapts to various needs, making it a valuable tool in sectors like manufacturing, construction, and asset management.
Non-Destructive Testing
One of the significant advantages of visual inspection is that it is a non-destructive testing method. This means it does not harm the equipment or products being inspected, preserving their integrity and usability. Unlike other testing methods, visual inspection allows for repeated inspections without compromising the asset's condition.
By leveraging these benefits, visual inspection remains a cornerstone of effective quality control and maintenance processes.
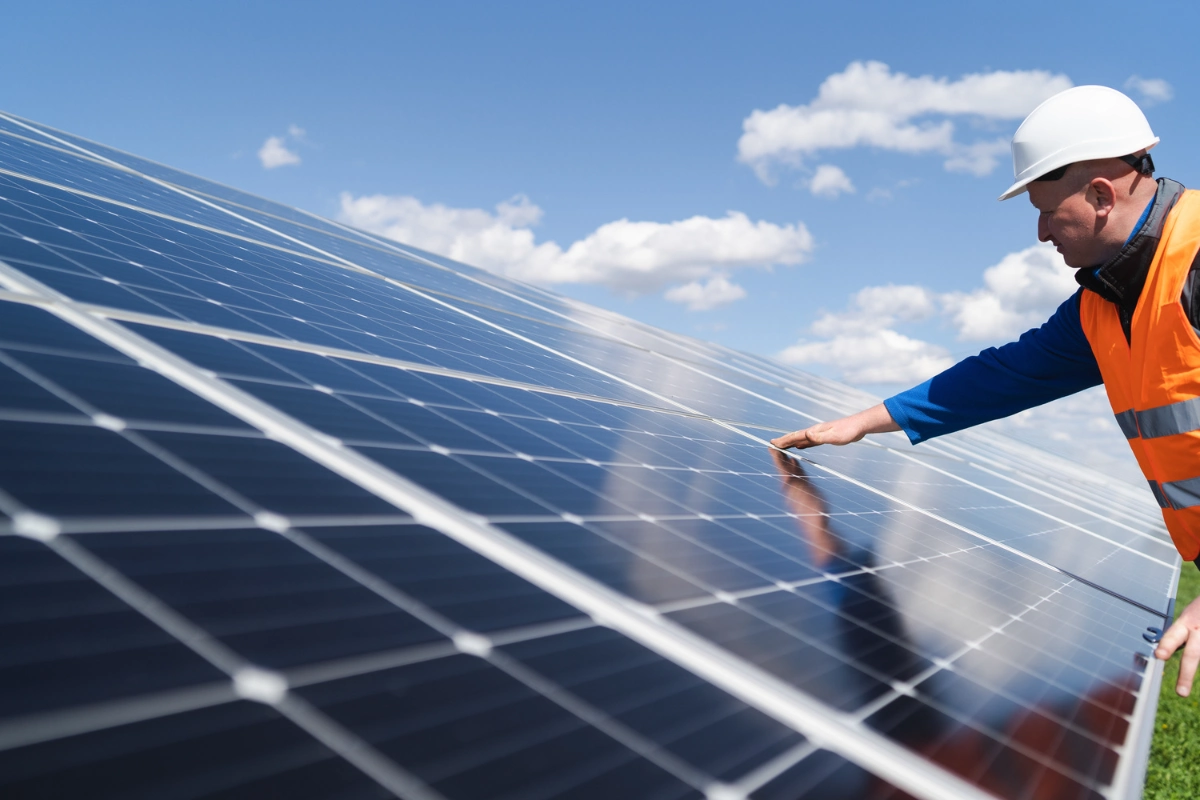
How to Standardize Visual Quality Control
You can standardize visual inspections by implementing clear procedures and checklists, similar to standard operating procedures (SOPs) used in preventive maintenance. Standardization ensures that trained personnel perform inspections in the same way every time, reducing errors and improving efficiency.
Here’s how to standardize visual inspections effectively:
- Create Clear Procedures and Checklists: Develop a detailed list of assets to inspect, determine the frequency of inspections, and identify specific parts of the equipment to examine. This ensures consistency across all inspections.
- Involve Trained Personnel: Ensure that trained personnel conduct inspections. Their expertise helps identify potential issues accurately and ensures inspections are performed to a high standard.
- Leverage Technology: Where applicable, use tools like automated visual inspection systems to enhance accuracy and speed. These systems can detect defects more efficiently and reduce human error.
- Minimize Errors: Standardized processes reduce the likelihood of errors by ensuring that all steps are systematically followed.
- Improve Efficiency: Following standardized procedures allows inspections to be completed more efficiently, helping to maintain production schedules and reduce downtime.
By standardizing visual inspections, you can ensure quality, consistency, and efficiency in your maintenance and quality control processes.
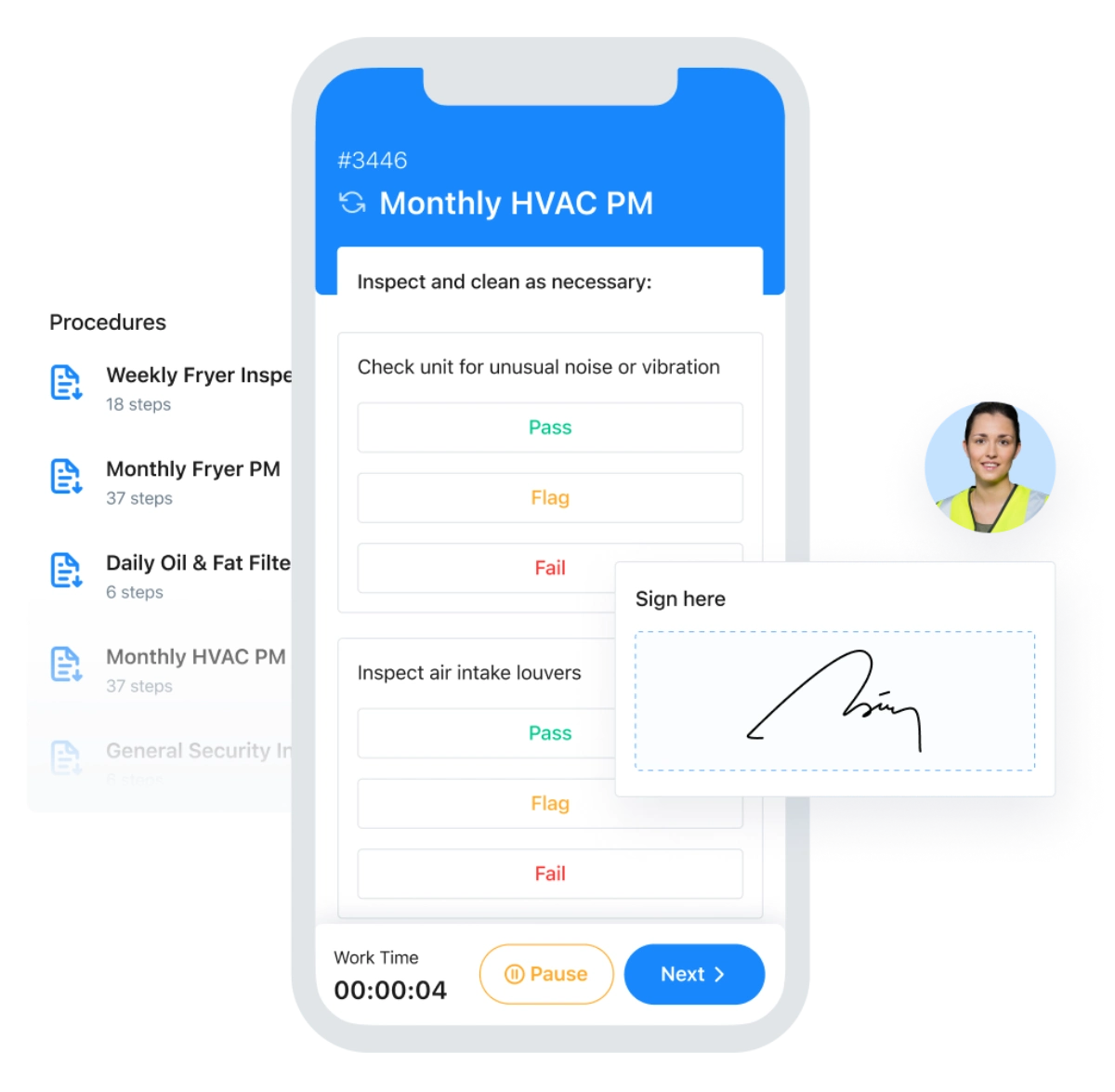
How a CMMS Helps with Visual Inspection
A CMMS can make the visual inspection workflow a lot simpler. For example, a maintenance professional may want to check asset history for recent repairs when investigating a potential issue during a VI. If you use a CMMS, the maintenance professional will have real-time access to repair history, downtime history, and specific asset work orders.
If the VI reveals an issue, the maintenance professional can create a checklist or procedure using a CMMS to provide technicians easy access, helping them complete work orders faster. As technicians complete work orders, they can upload pictures of completed work using a mobile CMMS.
Book a 1-1 tour and try MaintainX for free to see how a CMMS makes visual inspections easier.
FAQs on Visual Inspections
Direct visual inspection involves checking equipment or assets up close, using the naked eye or basic tools like flashlights. It’s commonly used for accessible equipment and during daily or regular inspections to catch early signs of wear or failure.
A standard visual inspection process includes following a checklist, observing for signs of damage, logging results, and triggering follow-up actions if needed. Many teams use a CMMS to conduct visual inspections consistently and link findings to specific assets and work orders.
Visual testing is a formalized inspection method that follows industry standards, often requiring specific lighting, distances, or magnification tools. In contrast, general visual inspections are more flexible and used as part of day-to-day maintenance routines.
Common visual inspection methods include:
- Direct inspection (walkarounds or line-of-sight checks)
- Remote visual inspection (using drones or borescopes)
- Automated visual inspection (AI-powered cameras for repetitive tasks)
Each method supports different levels of accessibility, accuracy, and automation.
The frequency of regular inspections depends on asset type, risk level, and usage. Critical assets may need daily inspections, while others may be reviewed weekly or monthly. Use condition-based triggers in your CMMS to schedule them efficiently.
To collect data remotely, teams use cameras, drones, or robotic crawlers to stream or record footage. This data can be reviewed in real time or uploaded into a CMMS for documentation, collaboration, and compliance tracking.
When you conduct visual inspections using a consistent checklist and process, you reduce variability, improve data quality, and make it easier to identify recurring issues. Standardization also supports training, audits, and cross-site comparisons.
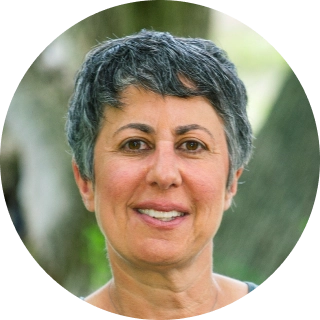
Caroline Eisner
Caroline Eisner is a writer and editor with experience across the profit and nonprofit sectors, government, education, and financial organizations. She has held leadership positions in K16 institutions and has led large-scale digital projects, interactive websites, and a business writing consultancy.
See MaintainX in action