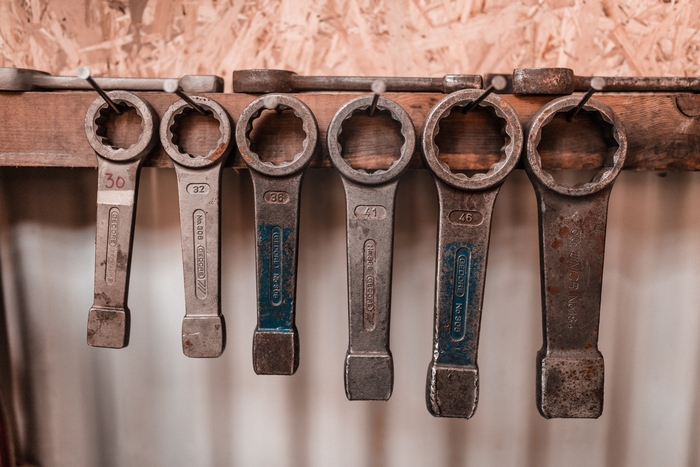
Browse any CMMS provider’s Website long enough, and you might walk away believing something that isn’t true: The positioning of positioning preventive maintenance (PM) as good and reactive maintenance (RM) as bad.
Though unintentional, the large volume of articles devoted to PM makes it seem like we’d rather be caught watching reality TV than reacting to equipment failure. However, like many complex subjects, maintenance is nuanced. Take nutrition, for example.
Many people believe certain foods are always good, while others are always bad. However, anyone who majored in nutrition will say there are, virtually, no good and bad foods. Instead, there are different foods for different circumstances.
Similarly, companies must exercise various types of maintenance in unique situations. Machines aren’t built to last forever, thus it’s impossible to practice preventive maintenance with 100 percent accuracy. Sometimes, it even costs more money to prevent their breakdowns than to fix them.
However, modern technology has made PM more cost-effective than ever before. The key to operational success is achieving the right balance of RM to PM. While it varies by industry, the average “magic formula” is one-fourth reactive maintenance to three-fourths proactive maintenance. Studies show that PM-heavy companies save an average of 12 to 18 percent on costs.
In this article, we will discuss the pros and cons of preventive maintenance vs. reactive maintenance. After reading, you will better understand how the two strategies work together, and why PM is more advantageous to success.
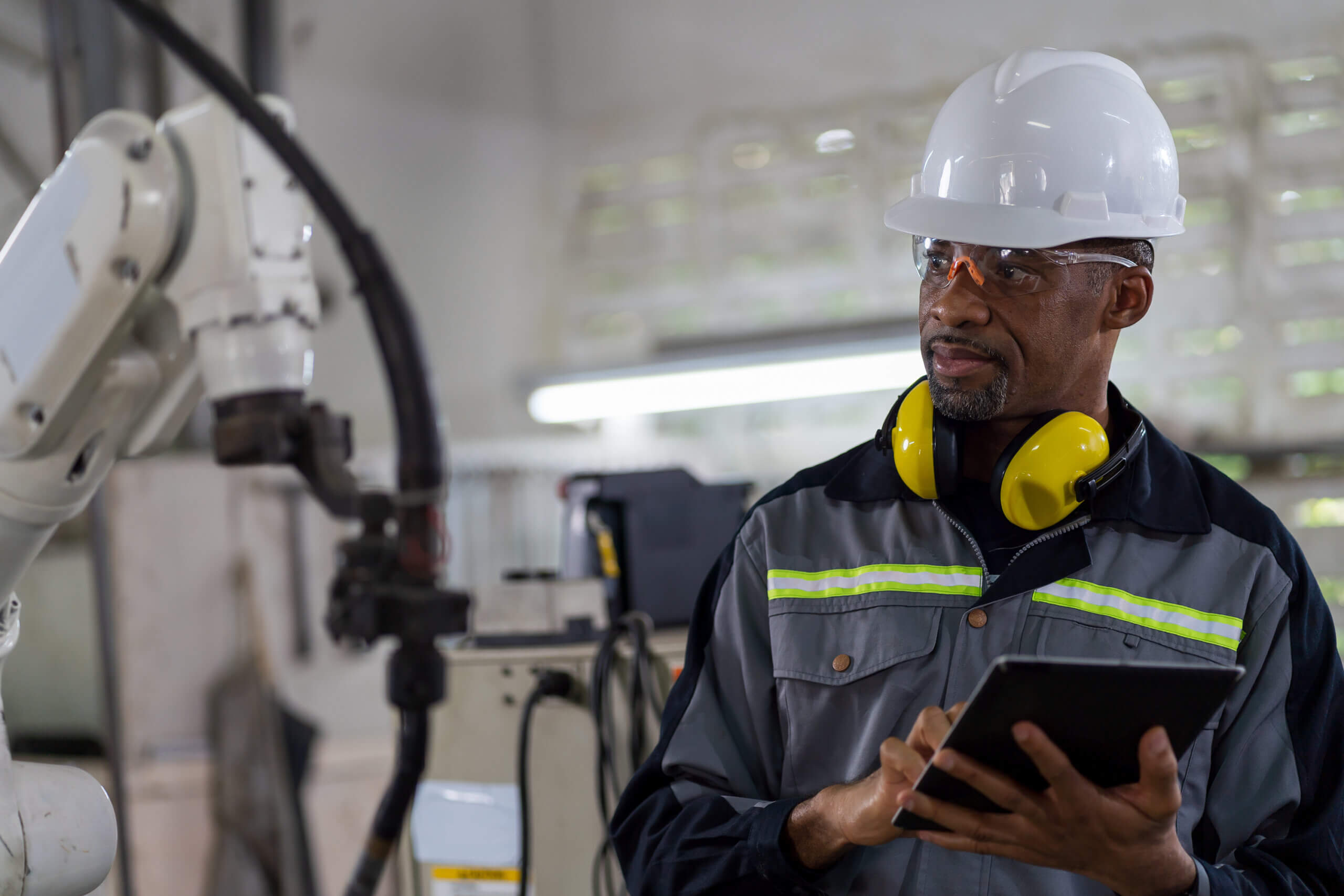
Preventive Maintenance vs. Reactive Maintenance: Which Is the Best Maintenance Strategy?
Preventive Maintenance Definition
Many important objects in our daily lives require routine care. Whether that means changing the oil in our truck every 5,000 miles or approving a Windows update on our computer, we all take recommended actions. Why?
We invested our hard-earned dollars into equipment we rely on, and we want them to work as long as possible! Similarly, companies also want their investments to live long, healthy lives. In the maintenance industry, this is called preventive maintenance.
Preventive Maintenance (PM) is planned maintenance that prolongs the lifespan of company assets, equipment, and infrastructure. Also known as preventative maintenance, PM includes adjustments, cleaning, lubrication, repairs, and replacements.
Essentially, preventive maintenance is the process of fixing small problems before they become big ones. Just like vehicle owners, company owners often get “more bang for their buck” by scheduling and assigning proactive maintenance procedures. However, there is one huge difference between the two scenarios.
Business owners often maintain hundreds, if not thousands, of valuable assets. Translation: Following a preventive maintenance schedule for every piece of equipment in a warehouse or facility can become a nightmare without proper organizational systems in place. Consequently, some companies practice what is called reactive maintenance:
Reactive Maintenance Definition
Reactive maintenance is exactly what it sounds like. Something unexpected happens with a machine, and you react. Here’s the technical definition:
Reactive Maintenance (RM) is a maintenance procedure that addresses problems as they arise. RM activities are precipitated by chance observations, equipment malfunctions and equipment failures.
Also called “run to failure,” this maintenance system does not schedule routine inspections, changing of parts, and other proactive tasks. Have you ever changed a light bulb that went out in your home? If so, you have practiced a form of reactive maintenance. You didn’t set a reminder to change the bulb every 6 months—you responded to the situation on the fly. Reactive maintenance falls into two general categories: Emergency maintenance and corrective maintenance:
Emergency maintenance often involves responding to an urgent safety requirement that must be met. In such instances, emergency maintenance must be prioritized over usual activities until the equipment is fixed. Unfortunately, this results in inconvenient downtime, reduced productivity, and sudden expenses. Emergency maintenance can be a minor inconvenience or a huge problem, depending on how valuable the faulty equipment is to production.
Corrective maintenance occurs when a worker happens to notice faulty parts during a non-related maintenance procedure, like an inspection or walkthrough. The parts are then either replaced or worked on so the machine can resume optimal performance.
Let’s look closer at some advantages and disadvantages of preventive maintenance vs. reactive maintenance.
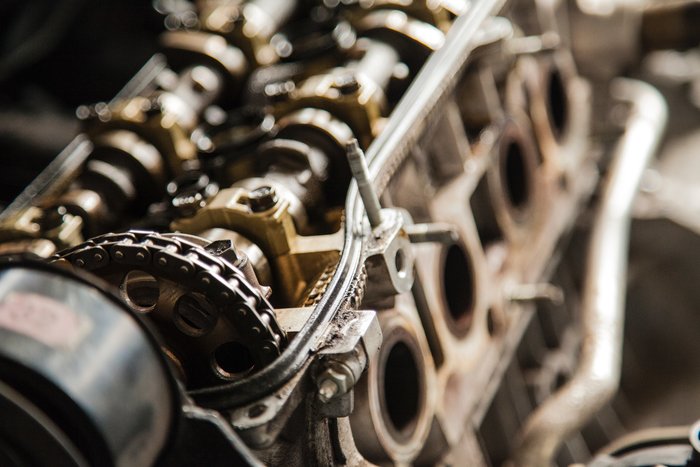
At a Glance: Running a Reactive Maintenance Program
Machines aren’t built to last forever, and with ownership comes the inevitable need for replacement. Industry experts suggest teams devote 20 percent of their time to reactive maintenance and spend the remaining 80 percent on preventive maintenance.
A good rule of thumb is to reserve RM for components that are inexpensive, easily replaceable, and unlikely to result in expensive downtime.
For example, say the cost of downtime for a particular asset is $500, and its monthly PM cost is $800.
In this instance, the company would actually waste resources by assigning PM work orders. It’s important to keep in mind that your employee’s time counts towards the cost of running PMs. Identifying RM savings opportunities requires meticulous asset analysis and cost tracking over time.
Obviously, certain situations benefit from a reactive approach. It really isn’t a question of, “Which is better: preventive maintenance vs. reactive maintenance?” With that said, running maintenance programs from a purely reactive standpoint presents more disadvantages than advantages:
Cons:
1. More Expensive Over Time
Unexpected delays during manufacturing runs often result in late orders, tarnished reputations, and decreased sales. Additionally, equipment may break down at inopportune times when workers and parts are unavailable. In such cases, companies may pay a premium for after-hour assistance, time travel, and emergency parts.
2. Shorter Asset Life Expectancy
Equipment systems that are “patched up” deteriorate faster than those optimized for efficiency. Not only is replacing complex equipment expensive, but it is also time-consuming.
3. Safety Issues
Reactive maintenance technicians often take more risks because they are under pressure to fix things ASAP. Alternatively, scheduled work orders afford the time to review standard procedures and safety requirements.
4. Higher Energy Costs
Simple PM tasks like greasing moving components or adjusting filters can reduce energy consumption by 15 percent. Ignoring these tasks will run up your energy bills.
5. Maintenance Backlogs
Unfortunately, emergency repairs happen at the expense of planned work. Backlogging tasks once in a while isn’t a big deal. However, once it becomes a habit, work orders begin to fall through the cracks. This translates to stressed-out team members who are always struggling to catch up.
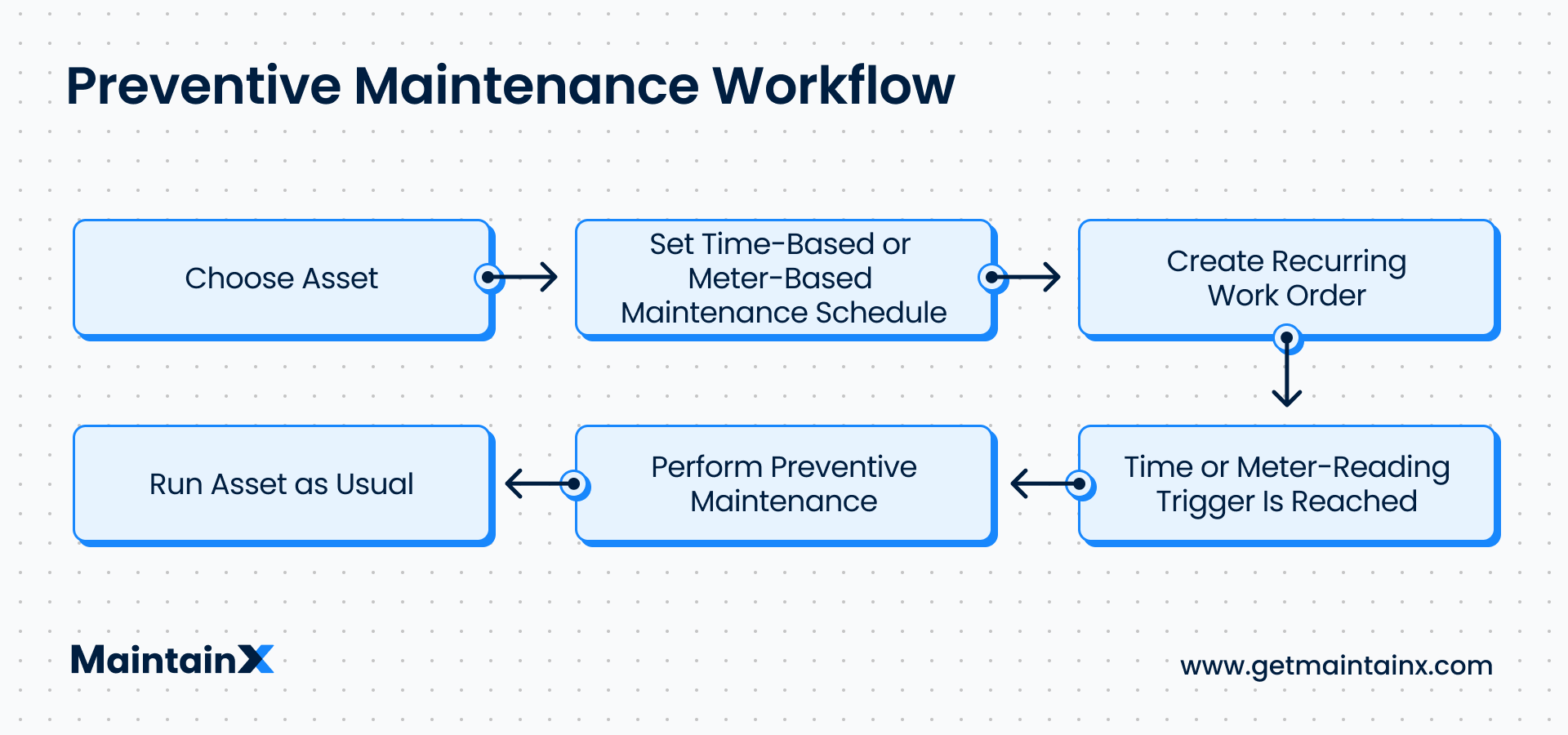
At a Glance: Running a Preventive Maintenance Program
Depending on the number of assets within an organization, and the number of workers available, regularly monitoring (and assigning) ALL recommended maintenance procedures might seem impossible.
For example, a small property management team might have 300 items requiring routine maintenance; whereas a large manufacturing facility might have 30,000 assets. Translation: Binders busting at the seams with paper checklists just won’t cut it.
Traditionally, the primary disadvantages of PM have been a) high-cost CMMS systems and b) learning curves required to benefit from using them.
However, in recent years, new digital maintenance solution providers have tackled both issues. MaintainX partnered with the world’s top engineers to design the first preventive maintenance software built for smartphones. The iOS, Android, and desktop apps are free, with premium features available for small monthly fees. With MaintainX in your PM toolbox, it’s easy to enjoy the benefits of PM, like:
Pros:
1. Greater Annual Savings
Organizations that adopt preventive maintenance philosophies often save more money than those that don’t. According to Jones Lang LaSalle’s “Determining The Value of Preventive Maintenance,” a telecommunications company experienced a 545% ROI when implementing a preventive maintenance plan.
Additionally, the unplanned downtime cost of industrial manufacturers may be more than $50 billion per year. So, what is the no. 1 cause of downtime? According to the Plant Engineering Maintenance Study, aging equipment is considered to be the most popular cause of downtime. Operator error and lack of time were other common reasons listed by maintenance personnel.
2. Enhanced Safety
The more often assets are checked, the less likely safety hazards will occur. Businesses that follow preventive maintenance schedules reduce the risk of unexpected breakdowns, health threats, and liability lawsuits.
3. Longer Equipment Lifespan
Preventive maintenance schedules ensure business assets are running according to the manufacturer and consumer guidelines. As poorly performing parts are updated, assets run in tip-top shape throughout the year.
4. Increased Productivity
Studies show poor maintenance strategies can reduce production capacity by 20 percent. Modern preventive maintenance solutions allow operational managers to digitize essential equipment details, assign recurring work orders, and review asset history from the convenience of their desktops and smartphones.
Additionally, maintenance personnel can also receive mobile task alerts, photograph equipment failures, and sign off on task completion in real time. Both streamlined PM systems and reduced downtime contribute to greater team efficiency, productivity, and focus.
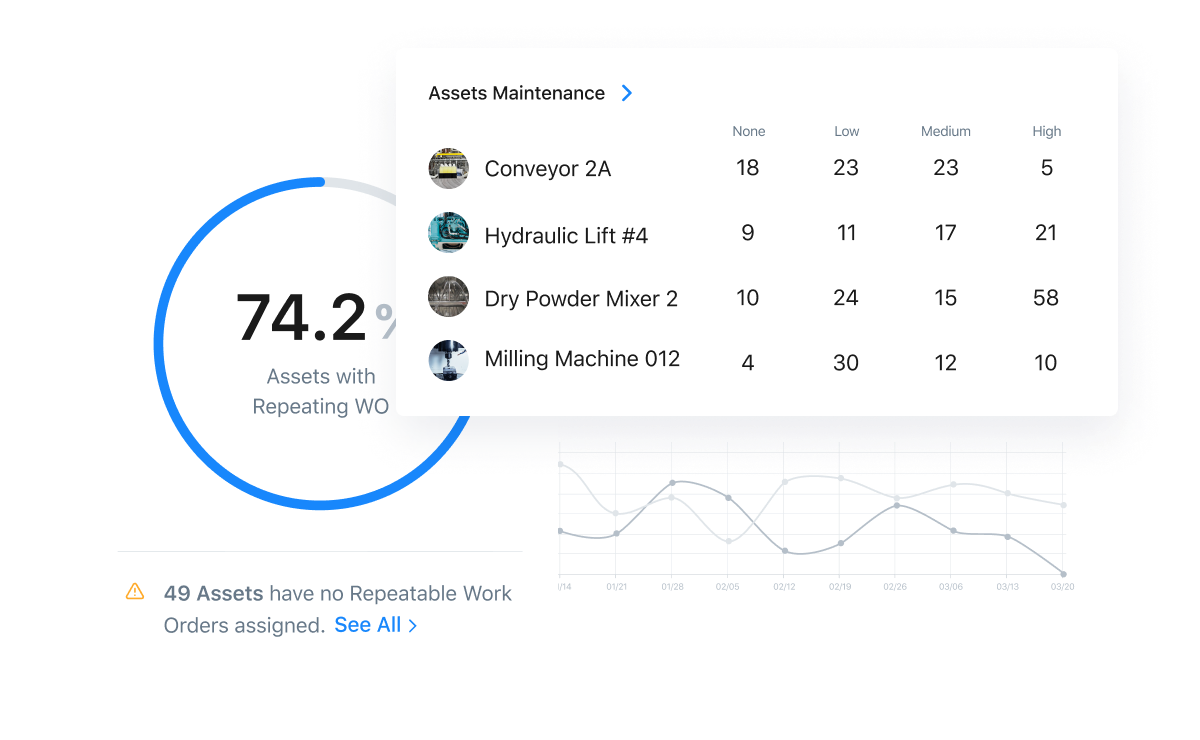
5. Less Energy Consumption
Poorly maintained electrical assets often consume more energy than those operating in normal conditions. PM allows energy-robbing issues to quickly be addressed, resulting in smaller utility bills. The more energy your business saves, the higher your profits will be. Our environment will also thank you.
6. Lower Insurance Premiums
Many business insurance providers offer lower premiums for companies that practice and document their preventive maintenance routines. If equipment is less likely to break down, there is a lower likelihood that you will need to make expensive claims.
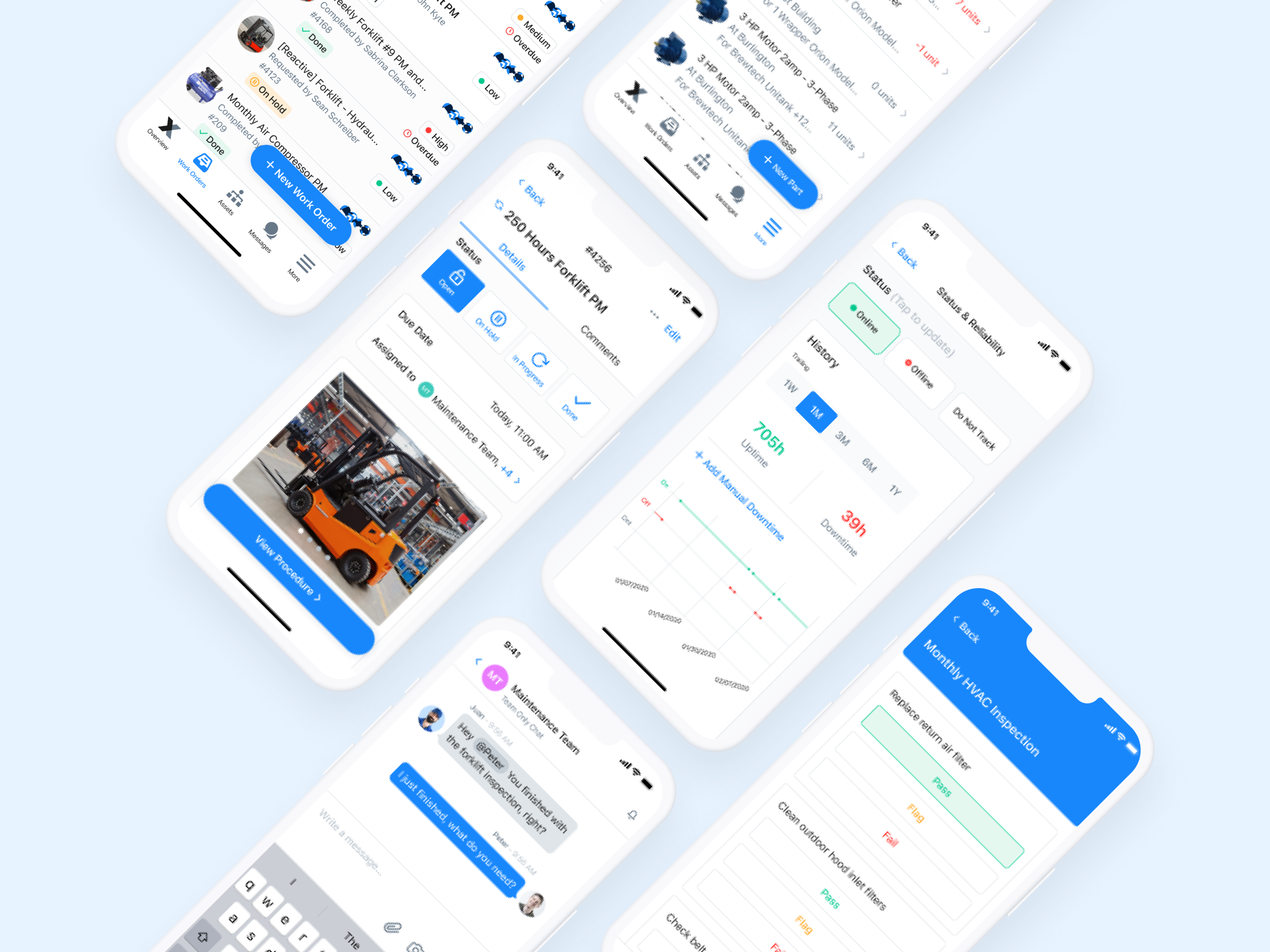
Simplify Preventive Maintenance with MaintainX
So, do you really have to choose between preventive maintenance and reactive maintenance? As we’ve shown, one method isn’t always better than the other. However, most organizations can reduce downtime, decrease annual costs, avoid backlogs, and extend asset life by pursuing preventive maintenance at least 80 percent of the time.
Are you ready to streamline your organization’s PM efforts? Our mobile-first app allows operational managers to track assets, create work orders, assign team members, and conduct cost analyses within minutes. Anyone with a smartphone can download the app and get started with zero training.
FAQs
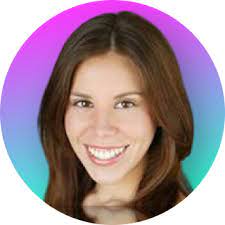