Industrial organizations rely on SCADA systems to oversee assets used in production, manufacturing, fabrication, and development. These technology systems ensure production efficiency, improve decision-making processes, and communicate real-time problems to avoid unnecessary downtimes and safety hazards.
What Is SCADA?
SCADA is an acronym that stands for Supervisory Control and Data Acquisition. It’s a computer system used by organizations to gather and analyze equipment data in real time. Industries such as transportation, oil and gas, energy, waste control, water, and telecommunications use SCADA systems to monitor and control complex machinery.
SCADA is particularly integral to electrical power, gas, oil, and water distribution. These industries typically run centralized systems that monitor production sites, including remote locations. SCADA allows organizations to:
- Control processes at remote locations from a central location
- Collect data from sensors, motors, pumps, and valves
- Monitor, gather, and process data in real-time
- Record and log equipment process events automatically
According to Allied Market Research, the global SCADA market is expected to grow 6 percent. Translation: SCADA has become a crucial component of managing complex industrial processes.
How SCADA Technology Works
SCADA systems enable users to control pieces of equipment in remote locations through signal communication using data communication channels. The computer system transmits information to a central database where data is analyzed to inform reliable decision-making.
The systems include five components:
- Supervisory Computers: They are the core component of a SCADA system. Supervisory computers refer to the computer and software used to communicate with the other members. They gather data and send control commands to remote devices. Smaller organizations can use a single supervisory computer, while larger SCADA systems can use multiple workstations.
- Remote Terminal Units (RTUs): RTUs connect device sensors to the supervisory computer. They convert signals from the sensors to digital data before sending them to the supervisory system, storing the data in a distributed database. RTUs usually are deployed to remote sites and locations.
- Programmable Logic Controllers (PLCs): While RTUs are process-specific, PLCs offer more versatility at a lower price. For this reason, they’re often used as field devices. PLCs communicate with sensors, factory machines, and other end devices and then send the information to the supervisory computer.
- Communication Infrastructure: For SCADA systems to operate efficiently, they need communication infrastructure that relays the data from remote RTUs and PLCs to the centralized system. It connects the field devices to the supervisory computer.
- Human-Machine Interface (HMI): The HMI processes data. It provides a human operator, who manages and controls the system, with data from RTUs for decision-making. This technology enables operators to initiate quick responses whenever alarms go off.
Organizations can customize SCADA systems to their specific requirements. But they still need to rely on the five essential components mentioned above.
Which Industries Use SCADA Systems?
The most common industries that rely on SCADA to improve efficiency, prevent unplanned downtimes, and make data-driven decisions are:
- Transportation
- Telecommunications
- Pharmaceutical
- Food and beverages
- Manufacturing
- Agriculture
- Water and waste management
- Oil and gas
- Electrical power distribution
Depending on the type of industry and its business needs, SCADA systems can vary from simple configurations to complex installations.
History of SCADA
The 1950s
Before the 1960s, most organizations relied on manual techniques to control and monitor remote facilities. This meant that employed personnel used analog dials and push buttons to manage complex machinery. While some oil and utility companies had already begun using computers for industrial control purposes, the technology wasn’t yet an industry standard.
The 1960s
After the initial introduction of SCADA technology, equipment operators began using relays and timers that eliminated the need for technicians to visit remote areas. The downside was that the early technology was challenging to reconfigure after each use, had limited capabilities, and involved huge panels that took up precious space.
The 1970s
The term, SCADA (Supervisory Control and Data Acquisition), was introduced in the 1970s after the development of microprocessors and PLC concepts. Industrial teams could now build fully automated systems for remote deployment with no need for system reconfiguration or field workers.
The 1980s-2000s
Over the next three decades, PC-based human machine-interface (HMI) software, small computer systems, and local area networking (LAN) technology developments further revolutionized SCADA operations. By the 2000s, industrial organizations were deploying complex, distributed SCADA systems.
Today
The efficiency, productivity, reliability, and security of SCADA systems have been enhanced by introducing modern IT standards such as Structured Query Language (SQL) and the integration of web-based applications. With SQL databases, organizations can now integrate into their SCADA systems other maintenance and operational tools, such as Enterprise Resource Planning (ERP) systems. New technologies also allow for seamless data flow through the entire organization besides easy access to historical data for analysis.
Additionally, companies are now replacing hardwired SCADA system infrastructures with wireless communication technologies. Wireless infrastructure minimizes installation time, fees, and licensing requirements. Furthermore, wireless systems are not at risk of wire failure due to environmental factors and degradation.
Understanding SCADA
SCADA system objectives include monitoring, measuring, and acquiring data; communicating data control processes; and automating functionalities. These modern computer systems help organizations reduce production waste, improve efficiency, and make data-driven business decisions that allow for greater control over everyday maintenance and production processes.
Additionally, SCADA systems allow organizations to monitor and control remote locations without incurring extra costs for deploying staff to those locations.
MaitnainX and SCADA
Using a digital CMMS tool like MaintainX will make it easy to share your SCADA processes with your team. With your work in the cloud, you can improve and refine workflows for even greater efficiency.
Ready to get into the clouds? Try MaintainX for free.
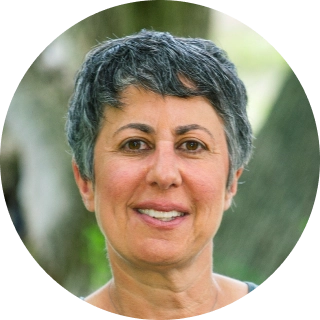
Caroline Eisner
Caroline Eisner is a writer and editor with experience across the profit and nonprofit sectors, government, education, and financial organizations. She has held leadership positions in K16 institutions and has led large-scale digital projects, interactive websites, and a business writing consultancy.
See MaintainX in action