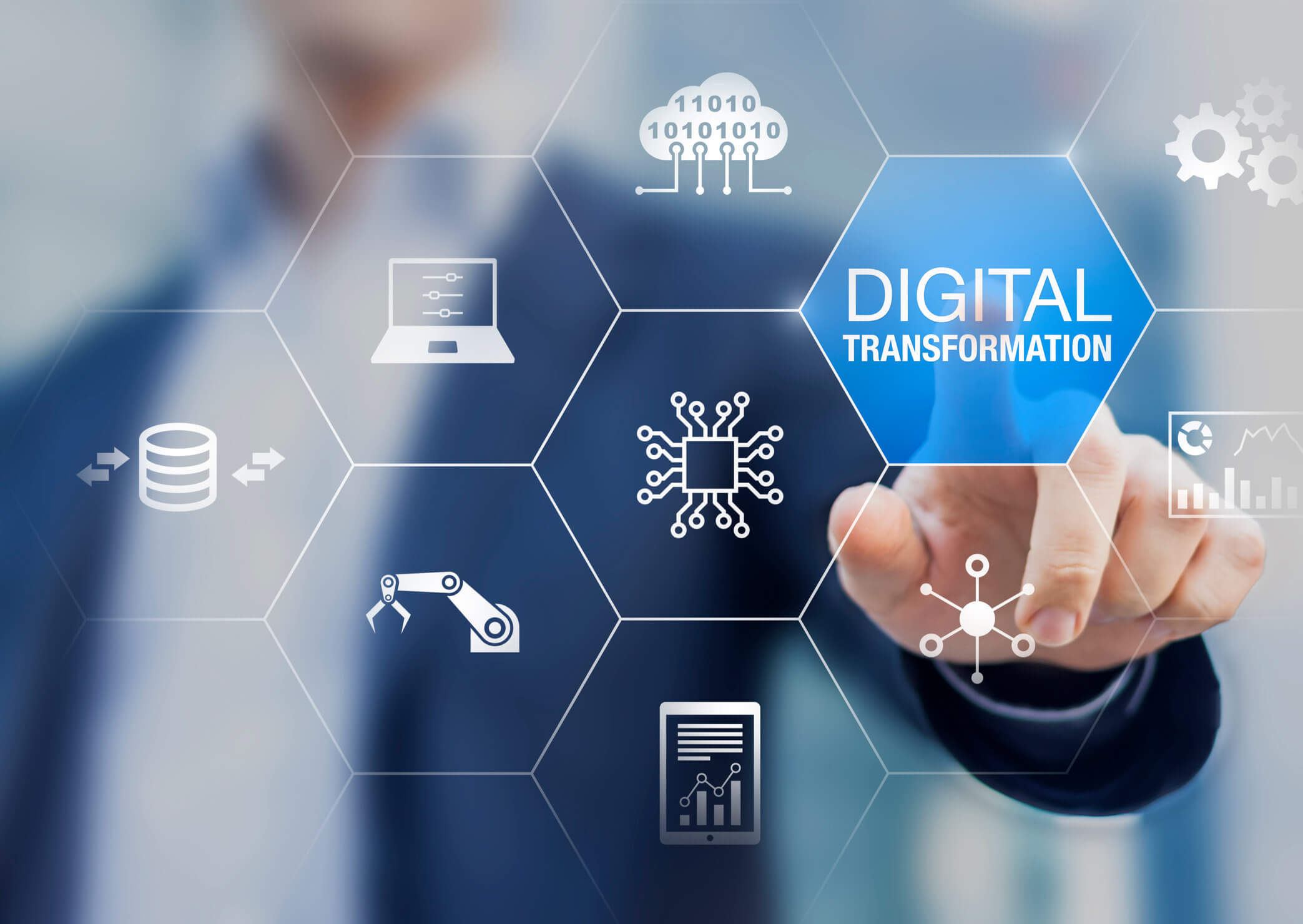
What Is Digital Transformation?
On one level, it’s just as straightforward as it sounds. Digital transformation is using digital technologies to improve business processes and outcomes. In addition, it often involves using digital technologies to digitize non-digital products.
In the digital age, many opportunities exist to upgrade status quo business processes and methods to digital business tools.
Now, while all that is true, it doesn’t tell the whole story. Digital transformation goes a couple of steps beyond that. Simply digitizing prints of old photos, for example, is one thing.
But digitizing in a way that improves business efficiency and customer experience is another. Plus, it can be tempting to focus on the digital technologies part and assume this is the whole point of digital transformation. After all, new cloud computing apps, intra-office connectivity software on mobile devices, and recordkeeping platform are always exciting.
“Leading players in a variety of heavy industries have used digital tools in dramatically reducing unplanned outages while boosting maintenance-labor productivity. Higher availability and a more-efficient workforce have increased profitability by 4 to 10 percent in some organizations.”
McKinsey
Starting Your Digital Transformation
In truth, however, digital transformation isn’t about technology. Or rather, it isn’t only about technology. The main things to think about here are culture and business strategy. And, of course, making sure that any competitive advantage you gain also keeps your workers safe and product quality high.
If you were using your computer’s calculator instead of doing sums on pen and paper, it would be a bit of a stretch to count that as an example of digital transformation. And typing in and printing out maintenance schedules instead of writing them down on a notepad isn’t really digitally transformative either.
In fact, a digital transformation journey involves genuinely integrating technology into the processes and workflows of your maintenance teams. In addition, it involves rethinking and reimagining how moving your maintenance planning to the cloud will help you achieve your business goals. Think about these questions:
- How can you optimize business operations using new technologies?
- How can employees become better at their work with the help of digital tools?
- How can you improve asset management and operational efficiency by integrating digital tools?
- What digital transformation initiatives can you implement to create a connected ecosystem for workers?
- What digitized preventive, condition-based, and/or predictive maintenance plans can help you meet your key performance indicators?
Modernization and the novelty of technology are one thing, but you can find the true goal of successful digital transformation in the answers to these questions.
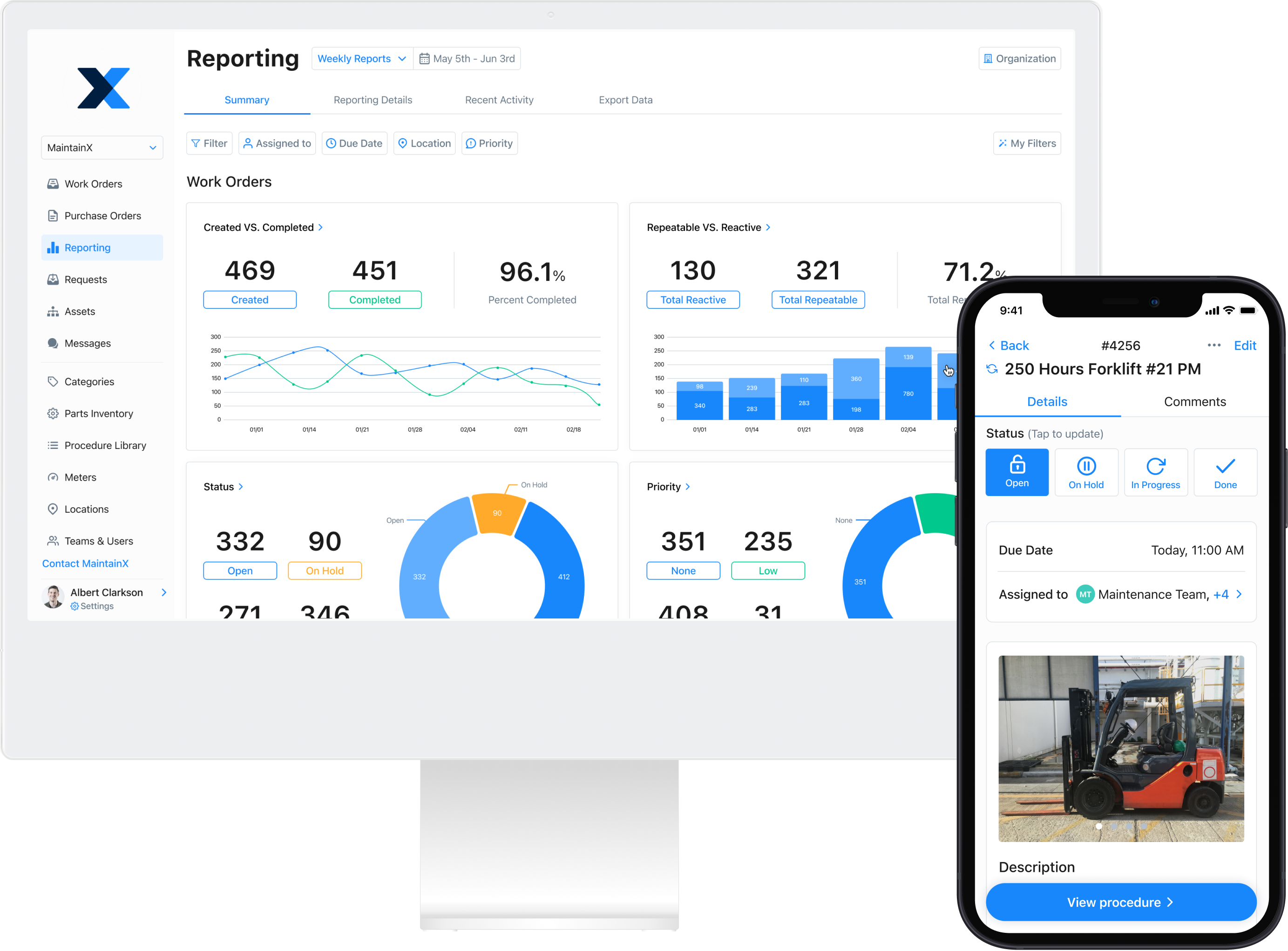
Examples of Digital Transformation of Maintenance
Examples of digital transformation in various industries including:
- Creating digitized standard operating procedures
- Implementing monthly preventive maintenance on a conveyor belt
- Using AI-based temperature diagnostic sensors for predictive maintenance
- Integrating mobile CMMS for remote workers
“In terms of maintenance demands, advanced analytics enables an optimized approach for identifying maintenance requirements….[P]redictive maintenance strategies provide more deliberate criteria for determining the need for servicing. Resources that go into the upkeep of assets can focus on value-adding work to ensure reliability while minimizing waste.”
The Enterprisers Project
Digital Transformation Strategies
As great as a digital business transformation sounds, making changes to existing systems is challenging. The last thing you want is to break a working system while attempting to improve it. So when transitioning legacy systems to new digital systems, here are a few things to keep in mind.
Use Business Goals to Define Objectives
The first step in your business transformation strategy is to create a roadmap for where you want to be. This begins by going back to your decision-making regarding your organization’s goals. For example, have you reduced equipment failure and downtime? Maintenance cost savings?
Are there any particular metrics and KPIs you want to hit? Your maintenance goals will drive your digital transformation goals and how you proceed. Try not to get swept away by all the digital transformation trends out there. The most successful digital transformation projects will have well-defined business goals and objectives to guide you along the way.
Bring Employees and Stakeholders Along
Setting yourself up for digital transformation success also involves getting buy-in from stakeholders. Whether making new products or switching to new business models, team members may face challenges adapting to new models.
Keeping your maintenance teams in the dark about your maintenance management decisions can lead to a sense of insecurity among employees. For example, are their jobs safe or are they going to be made redundant by technology?
In addition to ensuring employees feel secure enough to do their best work, proper change management techniques will help in a successful transformation journey. Employees in the system can tell you what is working and what is wrong with your current operating model. This will ensure you make changes that aren’t just for show and get you close to your actual goals.
Focus on the Customer Journey
Another crucial element in ensuring the sustainability of your transformation efforts is focused on the customer experience. Are you meeting your current customer expectations? What is the ideal user experience for your product or service? What are your own goals for your customer? If you’re running a maintenance team, you’ll likely be focused on internal clients or customers.
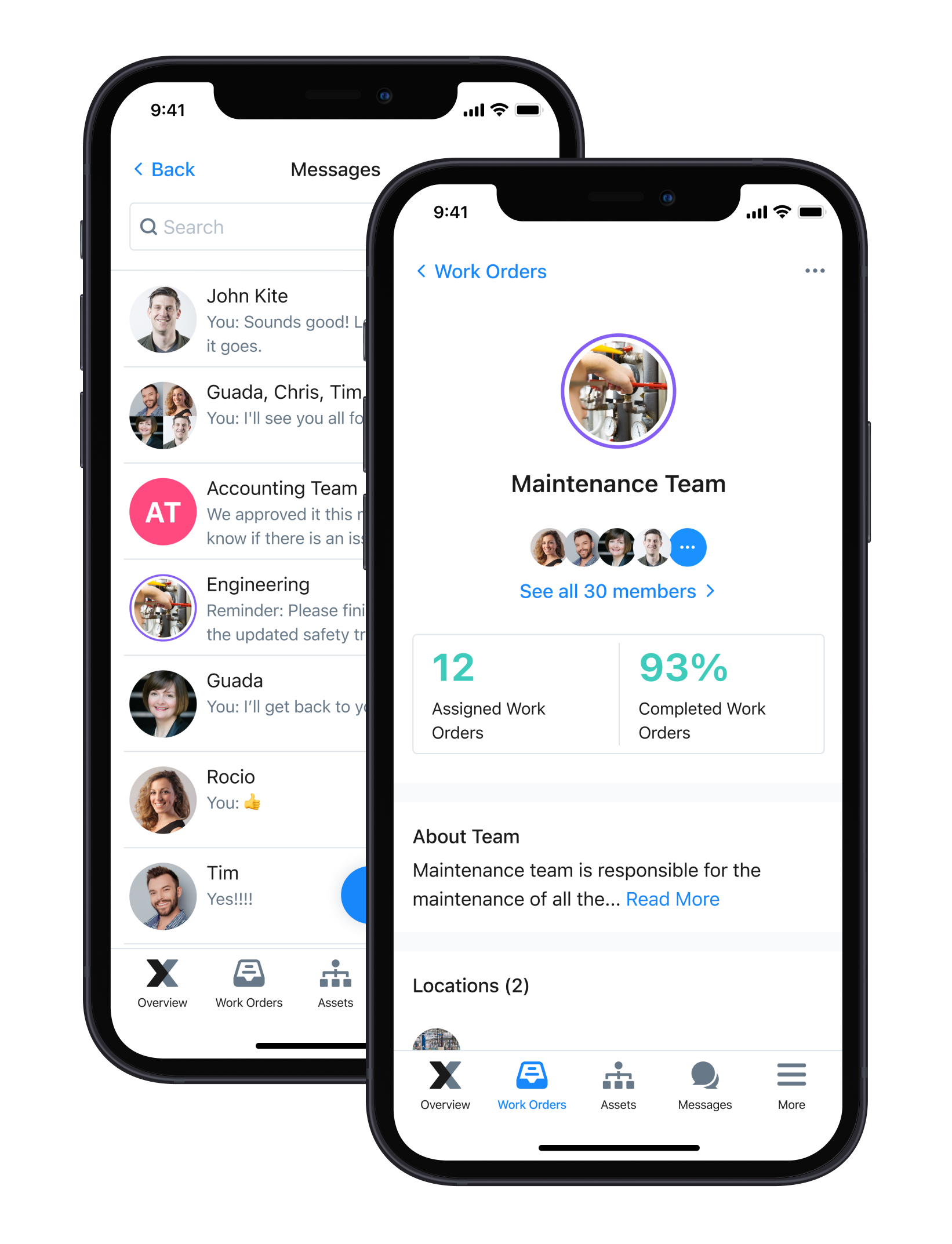
Create a Digital Transformation Plan for Your Maintenance Team
If you’re running a maintenance team and unsure if you should create a digital transformation plan for them, here are a few reasons you should consider going ahead.
You Might Be Losing Out on Business Value
The benefits of adopting technology in your maintenance strategy are numerous.
For example, a CMMS will help you reduce downtime by integrating digitized standard operating procedures (SOPs) with an effective predictive or preventive maintenance program.
Moving your maintenance team to a robust digital system will help improve effectiveness and efficiency, increase output, and save on downtime costs.
Industries Look Very Different Nowadays
If you haven’t felt the effects personally, you’ve likely seen the headlines. The supply chain challenges that resulted from the Covid-19 pandemic still reverberate. From startups to major companies like Amazon, in industries from the manufacturing industry to hospitality to healthcare, companies continue to face significant challenges in managing their workflows.
As a result, taking advantage of digital technologies to streamline operations, automation, and proactive maintenance tasks in real time is more crucial than ever.
Maintenance Is Changing Anyway
The field of maintenance is changing significantly. Today, it’s not unheard of for teams to use artificial intelligence (AI) to monitor assets via machine learning. Neither is it rare to carry out data analytics using big data for visibility into asset performance. Also, the Internet of Things (IoT) enables equipment monitoring. All around us, the future of maintenance is changing. Maintenance teams need to act in order to be left behind.
Transform Your Maintenance Operations with MaintainX
From automated work orders and maintenance processes to in-app chat functionality and increased equipment useful lifecycles, MaintainX’s CMMS platform offers the tools you need to transform your workplace. Not to mention, you’ll have access to in-depth analytics in real time, allowing you to continuously improve your processes.
FAQs
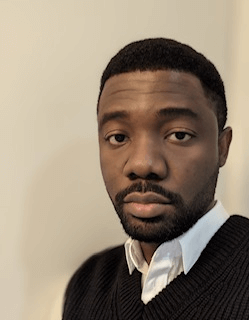
Lekan Olanrewaju is a content writer with years of experience in media and content creation. He has held positions at various media organizations, working with and leading teams at print magazines, digital publications, and television productions.