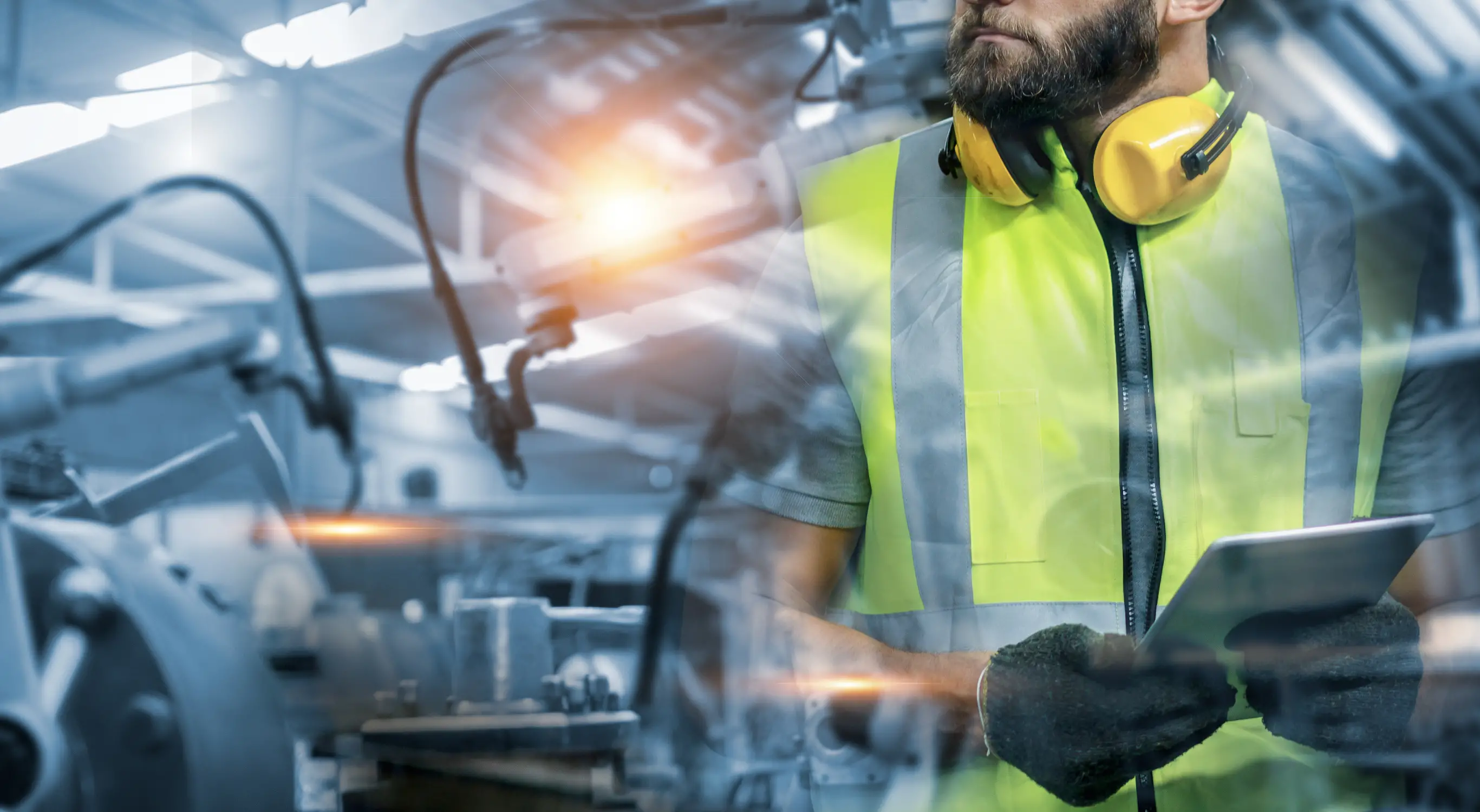
Computer-integrated manufacturing (CIM) uses computers to control the entire production process, making it more efficient and effective. CIM is used in a variety of industries, including automotive, aerospace, electronics, and food and beverage.
It is especially well-suited for industries that produce complex products or that require a high degree of precision and repeatability.
Typically, CIM relies on closed-loop control processes based on real-time input from sensors. This allows the system to continuously monitor and adjust the production process to ensure that it is operating as efficiently as possible.
How Does CIM Work?
CIM combines technologies like Computer-Aided Design (CAD), Computer-Aided Manufacturing (CAM), and Computer-Aided Engineering (CAE). CIM also uses systems and technologies like robotics and Manufacturing Resource Planning (MRP). Others include:
- Computer-Aided Process Planning (CAPP)
- Computer-Aided Quality Assurance (CAQ)
- Production Planning and Control (PPC)
- Enterprise Resource Planning (ERP)
- Direct Numerical Control machine tools (DNC)
- Computer Numerical Control machine tools (CNC)
- Programmable Logic Controllers (PLC)
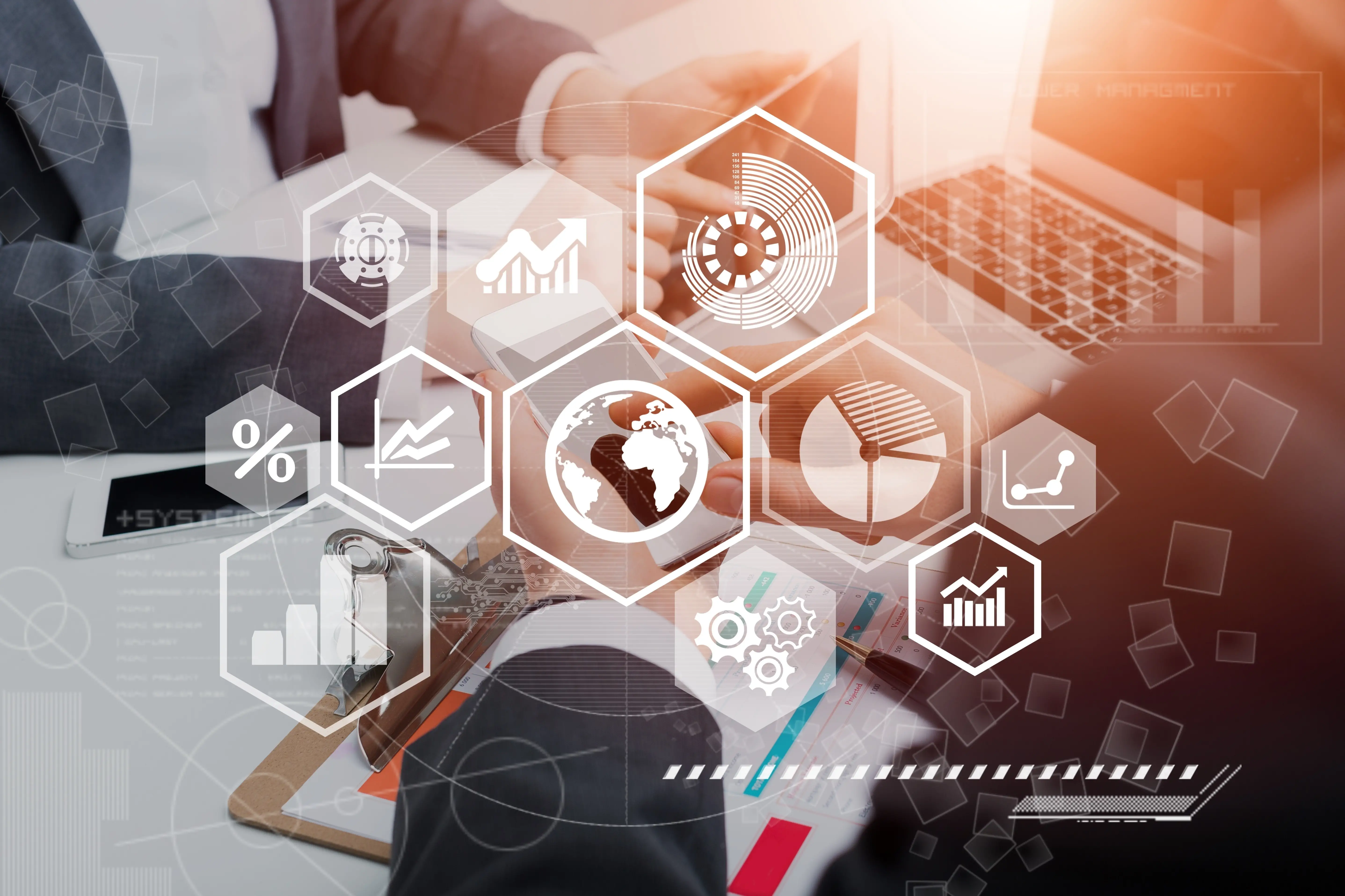
What Is the Goal of CIM?
As the name implies, CIM seeks to integrate manufacturing activities. This means eliminating all barriers to making a product and getting it to the customer. In short, everything in the supply chain should work in tandem. This includes everything from product development to inventory control, manufacturing, storage, quality control, shipping, and delivery.
Stages of CIM
Successfully running a computer-integrated manufacturing system means integrating business processes across several functional areas. These are:
- Design: This includes part and product design and tool and fixture design. Part and product design comprises four phases, which are preliminary design, refinement, analysis, and implementation. Tool and fixture design involves engineers using CAD to develop the systems that produce the parts.
- Prototype Manufacture: This involves making a prototype of the intended product to test and confirm that the manufacturing process works.
- Production Planning: Teams will calculate their costs and plan their production here. The team should end this stage with a process plan outlining all the necessary equipment and materials.
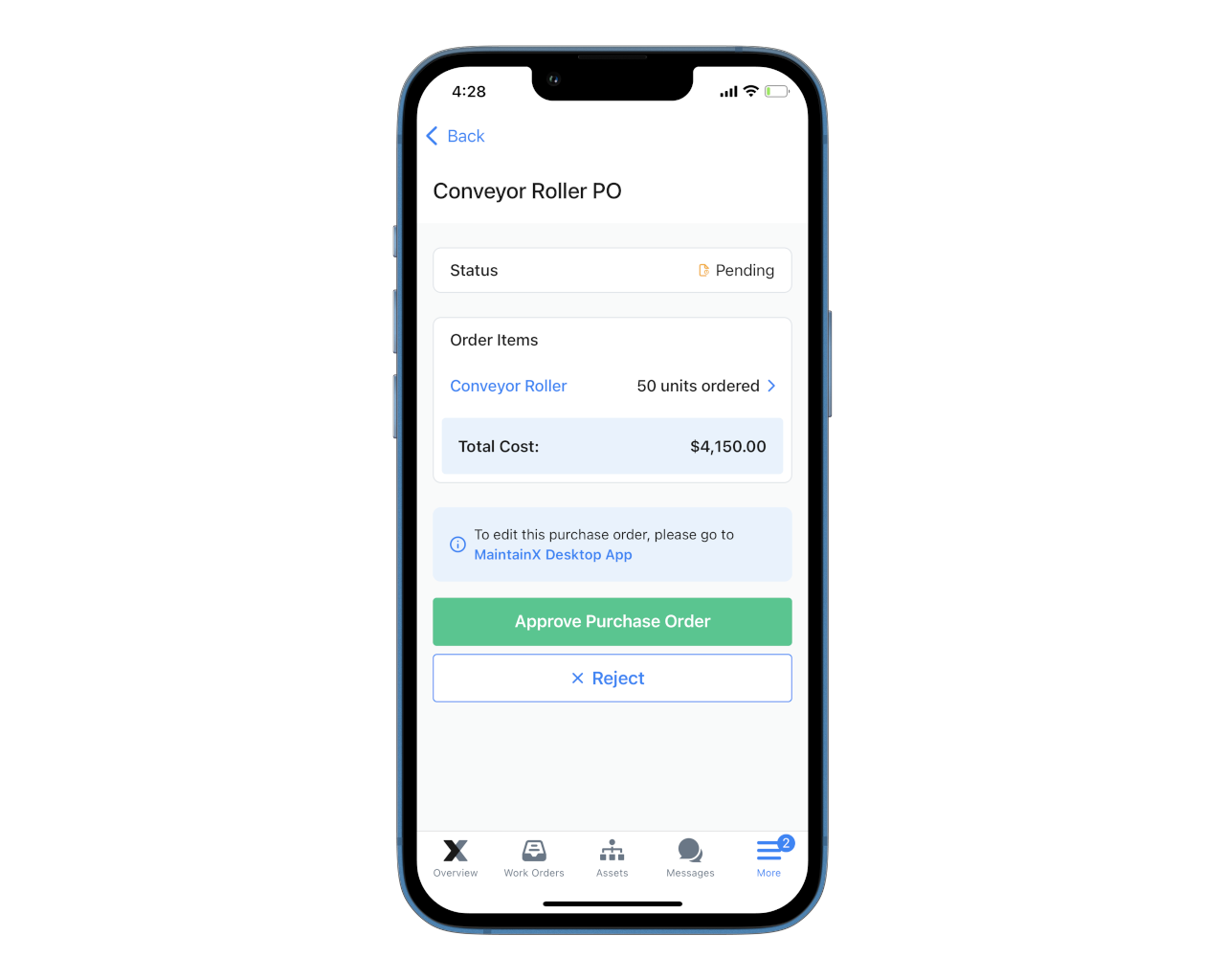
- Materials Ordering: Following the production planning stage, start on material requirements planning. Use the automated systems to create a Bill of Materials and order the necessary raw materials.
- Manufacturing (or Machining): This is the actual manufacturing process with Computer-Aided Manufacturing systems.
- Quality Control: At every stage of the manufacturing process, teams should ensure they carry out quality control procedures. If there are any errors or quality issues, workers should address them immediately. Errors might point to mistakes within the CAD stage. If so, the manufacturers should recalibrate their work instructions.
- Assembly: Here, robotics comes in. Pre-programmed robots put together the various fabricated parts into a final product.
- Storage: After another quality check and inspection, the products should proceed to storage.
- Distribution: This is the final lap, involving manufacturers getting their products into customers’ hands.
- Documentation: This involves consolidating data. At this stage, teams will use automated systems to update inventory logs, accounts, and other relevant information.
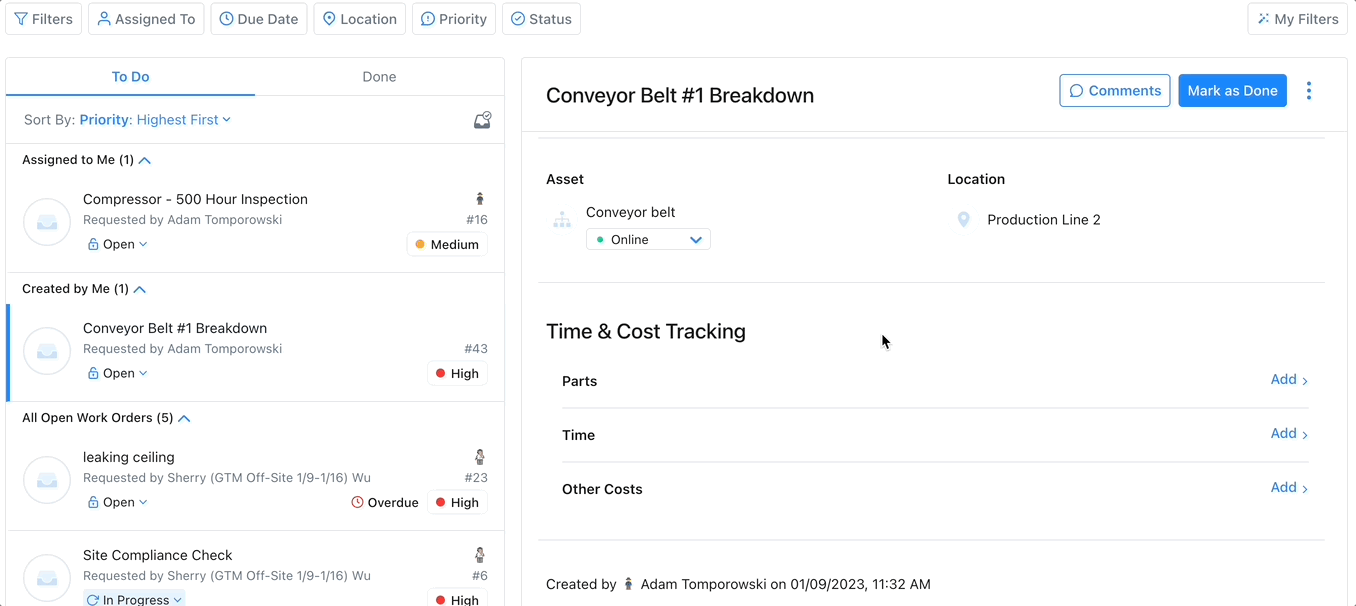
Benefits of CIM
CIM systems seek to streamline processes and improve efficiency. The benefits of CIM in practice can include the following:
- Increases Capacity: Automating your production processes means rapidly progressing from iteration to completion. As a result, you can drastically increase the number of products you create in shorter timeframes.
- Reduces Downtime: Because CIM involves such detailed planning with automated processes, you eliminate the potential for error. In addition, using a predictive maintenance plan and a CIM system, you’ll have even better success managing your assets. You’ll have a better sense of when breakdowns may occur. This means you can schedule predictive (or preventive) maintenance activities without unplanned interruptions to your entire production line.
- Improves Inventory Management: CIM system efficiency means using raw materials quicker and getting products to customers on time. You’ll be dealing with reduced inventory but will better know the lead times for ordering spare parts. This is especially beneficial if you aim for a lean system.
- Reduces Costs: CIM environments help to save costs (and increase profitability) in multiple ways. For one, since you’ll have less inventory, you’ll spend less on facility storage. Because your products will have higher degrees of accuracy, you’ll lose less stock to errors.
Using a CMMS with CIM Systems
While we’ve looked at the benefits of computer-integrated manufacturing systems, using them can present some challenges. These include integrating computer systems from different suppliers, ensuring data integrity, and overseeing process control. A computerized maintenance management system (CMMS) is a valuable tool that can help mitigate these challenges. Let’s consider how.
Managing Tools from Different Suppliers
CIM systems aim to integrate many disparate parts of a manufacturing process. As a manufacturer, you’re unlikely to find one tool that does all these things simultaneously. You’re more likely to obtain CAD/CAM, ERP, or artificial intelligence robotics from different suppliers or service providers.
Managing these computer-control tools can be challenging for your team, as the various systems and machines require different things. A CMMS can make things much easier for you here.
A CMMS can improve facility management overall. MaintainX, for example, also allows you to store information and documents, such as standard operating procedures, in the cloud.
MaintainX even houses a global procedure library. This will allow your team access to any information they need about the procedures for various machines.
Ensuring Data Integrity
For CIMs to work correctly, they need highly accurate data. A CMMS can help you measure and record up-to-date data across your facility.
You can create KPIs and metrics regarding what data to record and when. MaintainX, for example, allows you to automate work orders. You can create maintenance work orders to capture and record data at set intervals.
Overseeing Process Control
While computer-integrated manufacturing management systems ensure high accuracy and speed, they are not entirely autonomous. In the event of occurrences that require human attention, you want to make sure shop floor staff are on hand.
Maintenance management software can help maintenance teams with swift, real-time communication, ensuring you reach who and when you need to. The only CMMS with in-app chat, MaintainX, is work order software that automates preventive maintenance scheduling. This makes it easy for you to communicate with your staff directly on their mobile devices. In addition, MaintainX’s robust reporting features provide real-time work order assessment for maintenance task optimization.
MaintainX and Computer-Integrated Manufacturing
If you like the sound of what CMMS systems can do for your computer-integrated manufacturing, consider using MaintainX. We designed MaintainX to help streamline your workflow, reduce breakdowns, and increase uptime. Use MaintainX’s work order management features to automate your maintenance tasks and optimize your asset management today!
FAQs
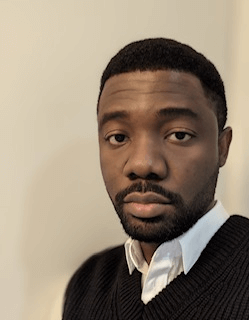
Lekan Olanrewaju is a content writer with years of experience in media and content creation. He has held positions at various media organizations, working with and leading teams at print magazines, digital publications, and television productions.