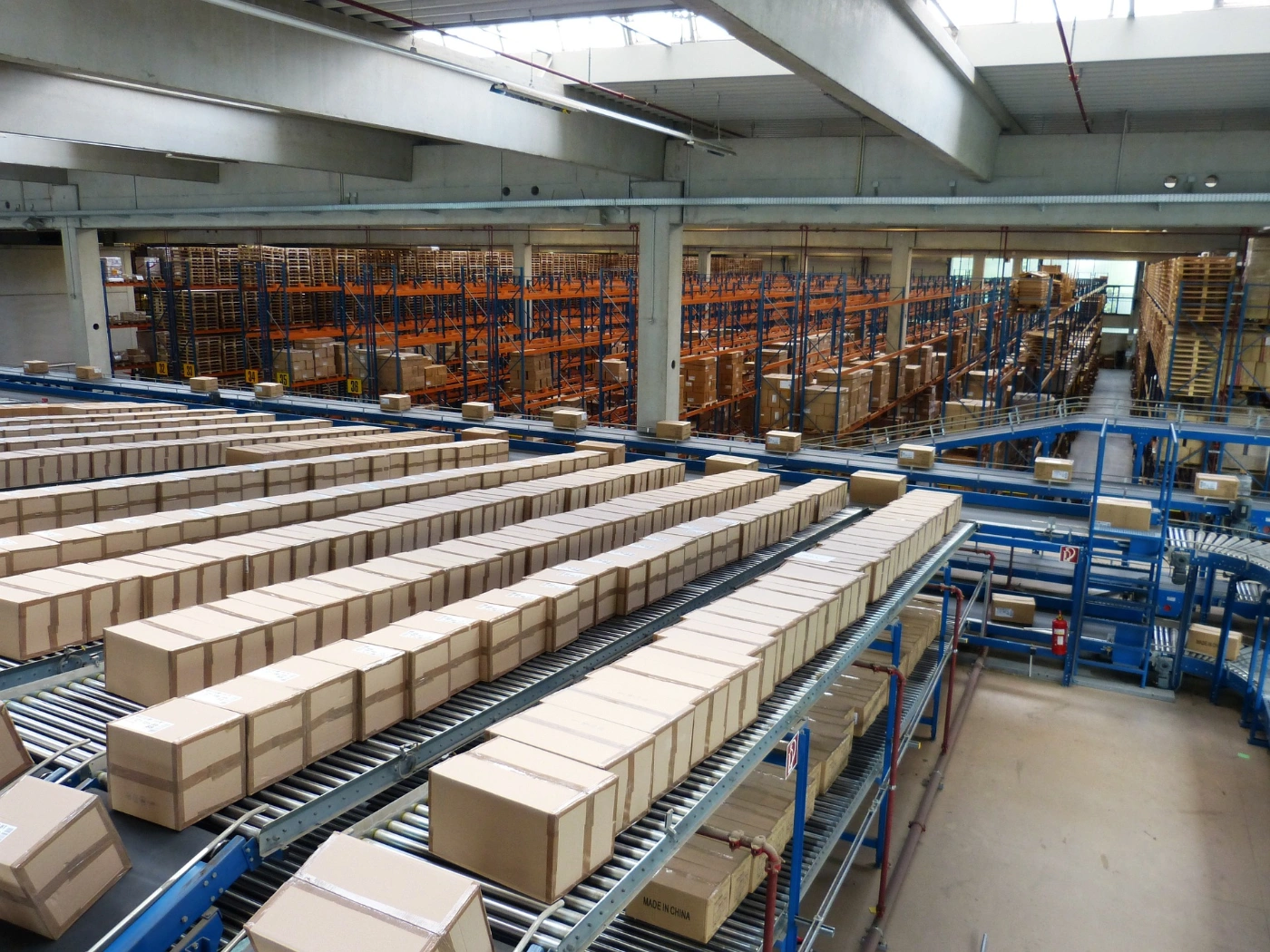
Many people don’t like the idea of being inspected. Perhaps that’s because we look at inspections from a negative standpoint. We think of an inspector as someone who is looking for something wrong instead of someone who is confirming that all is well.
If you are a manufacturer who has one or any number of production lines, you should be used to inspections. These might be internal inspections performed by:
- management
- third-party inspections
- state or federal inspections
- customer inspections
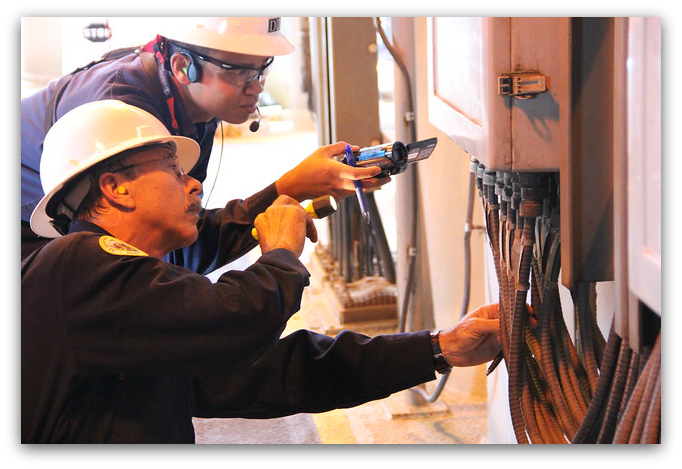
Frankly, inspections can and should happen often throughout the supply chain, and some of them may happen on your shop floor. The trick to not being bothered by whatever type of inspection you might be facing is to all always be prepared for them. How can you do that?
Well, let’s broaden our viewpoint a bit. Instead of just focusing on a customer inspection—or any other type for that matter—think in terms of your total quality control. If your processes are running smoothly and you’re always on top of all aspects of quality control, the customer inspection is simply an opportunity to show off all the things you’re doing right. A chance for prospective customers to see they can and should have faith in your company and your product. Of course, that’s all easier said than done, isn’t it?
First, let’s briefly talk about when and where the customer inspection may take place. Then we’ll discuss what steps you can take to always be prepared.
Key takeaways:
- Inspections can be done by a variety of outside parties.
- Think of your customer inspections as another facet of your quality control.
- Customer and quality inspections can be interchangeable.
Customer Inspections in the Supply Chain: When and Where
Note that your customers can be anyone in the supply chain, not just the consumer or company who purchases the final product.
Customer inspections—which we can also refer to as quality inspections—can and should happen at various points in the production process. This could be at the beginning and during the process, once the product is finished, and may even happen while in storage.
Customer Inspections of Purchased Items
This is when your customer inspects to confirm that their purchases meet their criteria. Again, this could be a finished product or a component they need to use in there own manufacturing process.
When an initial purchasing agreement is made—and depending on what the product is—the agreement could define allowances and tolerances. The customer has the ability to return their purchases should the initial agreement and expectations not be met.
On-Site Customer Inspections
Depending on the product, some companies may prefer to come to you and do an inspection before transport to their own facilities takes place. Often times, these inspections will cover more than just the product. They can turn into an opportunity for the customer to inspect your facility and equipment. Not to mention all your documentation, plus your manufacturing processes.
You can see the importance of these types of inspections when negotiating a purchasing agreement. If you already have an ISO 9001:2000 Quality Management Standards (QMS) certification in place, that can go a long way providing your customers with a greater sense of confidence in you and your product. Businesses of all sizes and industries face challenges when attempting to eliminate productivity bottlenecks, control spending, and exceed customer expectations.
Before implementing quality improvements, it’s essential to recognize one fact: your team members will determine whether initiatives become wildly successful or stall out. Fostering a company culture committed to operational excellence is a prerequisite to quality improvement. If you don’t have certification, expect that your customers will want to make regular inspections part of the negotiation process.
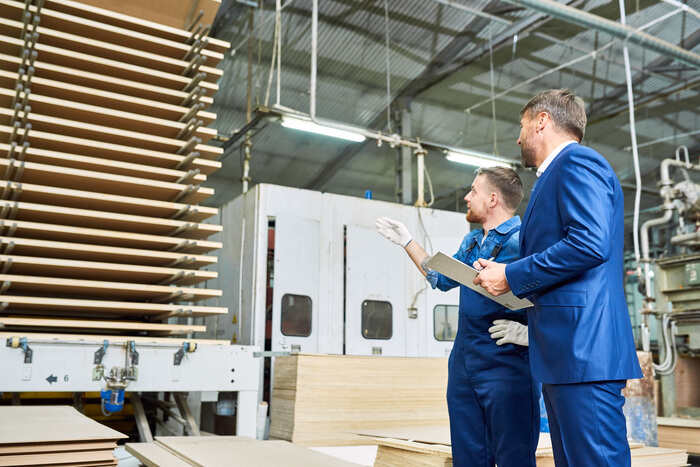
Production Line Inspections
This and the following inspection wouldn’t be classified as customer inspections. They are in the quality inspection category but are worth adding. Remember, if you are on top of all of your quality inspections, you have nothing—or at least very little—to worry about when it comes to a customer inspection.
If you produce finished goods, it’s not feasible for you or your customer to wait until production is complete before performing an inspection. You want to find any possible issues early in the process and curtail them. Correcting issues early will save you in production costs.
Finished Goods Inspection
Once production is complete, your finished items need to be inspected to make sure quality standards have been met. The inspection shouldn’t be limited to the item itself but should include all packaging materials.
Okay, we’ve talked about the what and the when of inspections, but how you can stay prepared?
Tighten Your Inspection and Quality Control Processes with 3 Easy Steps
According to the 2020-2025 Quality Control Forecast, the global quality control market is now generating nearly $37 billion in profits. As global competition continues to increase, so does the pressure to maintain uniform commodity and service standards, earn consumer trust, and implement foolproof systems that keep teams organized.
No matter the size of your operation, you should try to implement the three steps listed below. They will aid in general quality control and make sure you’re always ready for customer inspections. And remember, I said above these are easy steps—and they are, especially with the aid of software like MaintainX.
1. Standardize Workflows
Having a standardized workflow means everyone is on the same page. Workers know what they need to do and in what order. Operations are streamlined, downtime is minimized, and the chances of miscommunication almost completely disappear. Results from creating stronger standard operating procedures and inspection reports can absolutely make a difference to your organizational productivity, efficiency, brand reputation, and capital management.
How complex or basic your workflows are is going to depend on your business and processes. With a workflow, everything is clear-cut. Where things start and stop, the direction they should take, and the expected end results. You can even factor in alternate steps to take should it be necessary. Assign someone responsibility for each of these steps.
With your standardized workflow in place, it’s simple to optimize results. A workflow can provide the following benefits:
- A reduction of project risk
- Limits the need for management intervention
- It will define duties and responsibilities
- Improve timelines
- Provide audit trails
Having a standardized workflow in place is the first step toward being ready for a customer inspection.
2. Digitize for Efficiency
If you’re looking to be efficient, think about mobile applications for your workflows and forms. Digitizing doesn’t automatically mean you need to create entirely new workflows, but you’ll likely need to rethink some of your existing standards. Ultimately, this will make your processes that much more effective.
When switching to digital, you’ll need to define the elements of the workflow, typically by means of the feedback and interviews of a team of end-users (e.g. shop floor maintenance workers). When the workflow is complete, everyone on the team can use the single application.
- Ultimately more cost-effective
- Helps to identify quality issues faster
- Faster access to analytics
- Faster audit and customer inspections
3. Optimize Workflow Based on Feedback and Only Measure What Matters
Your workflow shouldn’t be static, but also don’t change it on a whim. So when should you make adjustments? Listen to the feedback of both junior and senior operators. Their insights into carrying out tasks and processes in real-time are crucial. What metrics are you using? What metrics matter the most? Do you need to measure everything?
Take some time to decide which measures really matter. A good time to do this is when you make the change over to digital. As mentioned above, this is when you should redefine your workflow. Remember, your endgame is to be efficient. Using unnecessary metrics takes away your focus, and builds an unstable foundation for future inspections. Here are some key areas to build metrics around:
- Your customer’s experience
- Quality
- Efficiency
- Inventory
- Waste
- Maintenance
- Costs
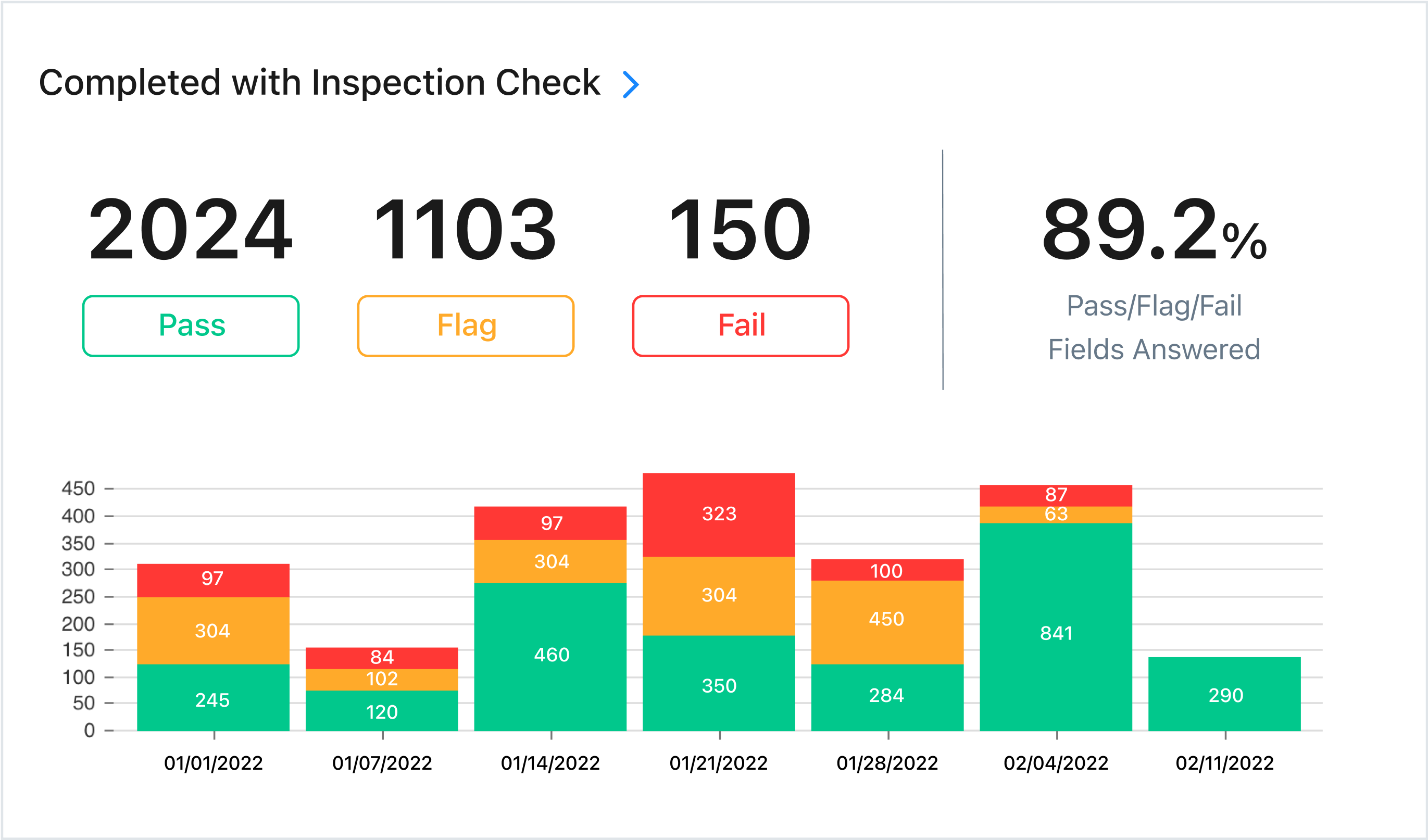
Inspections Don’t Have to be a Negative Experience
The choice is yours. You can view customer inspections—or any type of inspection—as an opportunity to confirm that all is well.
If you have all of your quality control processes in place, inspections won’t be something to fear. Instead, you’ll want to put the results right up on your office wall for everyone to see.
Enlist the support of work order software to assign digital work orders, provide employees with user-friendly checklists, and oversee quality control in real-time. MaintainX provides users with a flexible platform to better organize their quality improvement efforts, track KPIs, and glean insights that lead to measurable progress.
Businesses of all types—from restaurants to manufacturing facilities—use our mobile-friendly app to save time, money, and energy that could be better directed elsewhere!
FAQs
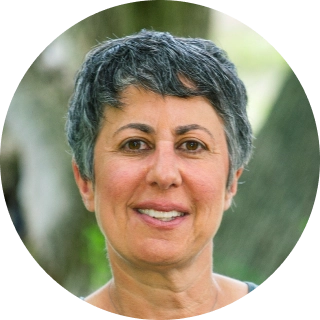
Caroline Eisner is a writer and editor with experience across the profit and nonprofit sectors, government, education, and financial organizations. She has held leadership positions in K16 institutions and has led large-scale digital projects, interactive websites, and a business writing consultancy.