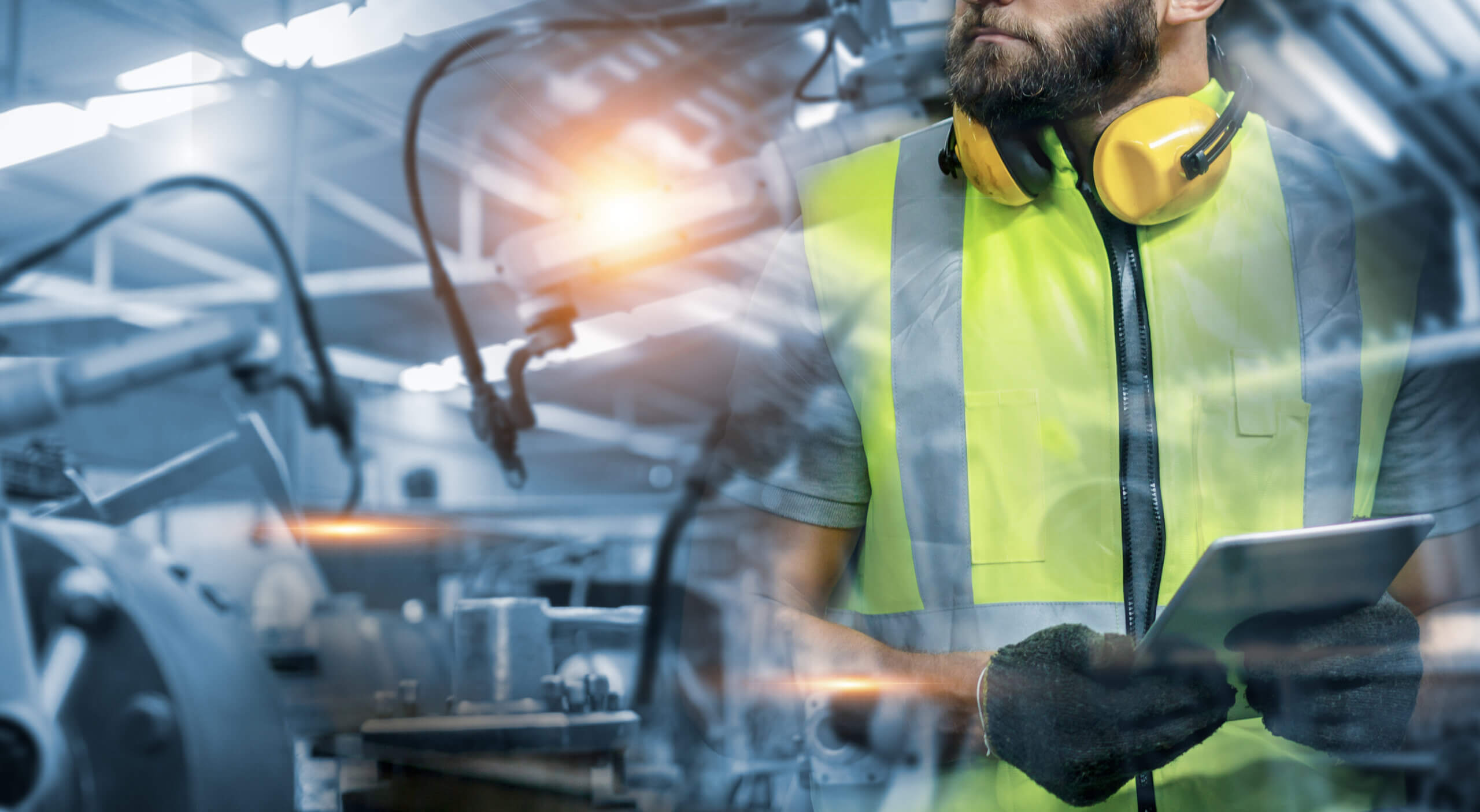
In the modern industrial landscape, the intersection of Information Technology (IT) and Operational Technology (OT) is revolutionizing manufacturing and maintenance processes. This convergence of IT and OT bridges the digital and physical worlds, enabling real-time data collection, analysis, and implementation for improved operational efficiency. Combining this with a robust CMMS will make all the difference.
From predictive maintenance to enhanced production control, the unification of these technologies offers unprecedented levels of transparency, productivity, and sustainability in manufacturing. By harnessing this synergy, businesses can drive innovation, accelerate growth, and stay competitive in the rapidly evolving Industry 4.0 landscape.
Information Technology
Information technology (IT) in manufacturing focuses on using computer systems to access and manage information. It uses hardware, software, support services, and infrastructure to create, process, store, and exchange data and information.
IT-driven tools, such as AI-powered predictive analytics, provide real-time visibility into supply chain processes, allowing manufacturers to quickly adjust to changes in demand and market conditions, thereby boosting efficiency and reducing costs. Similarly, IT promotes production accuracy by integrating advanced automation and machine learning technologies, which reduces human error and enhances product quality.
IT’s role in manufacturing also extends to predictive maintenance, using IoT sensors to monitor equipment health.
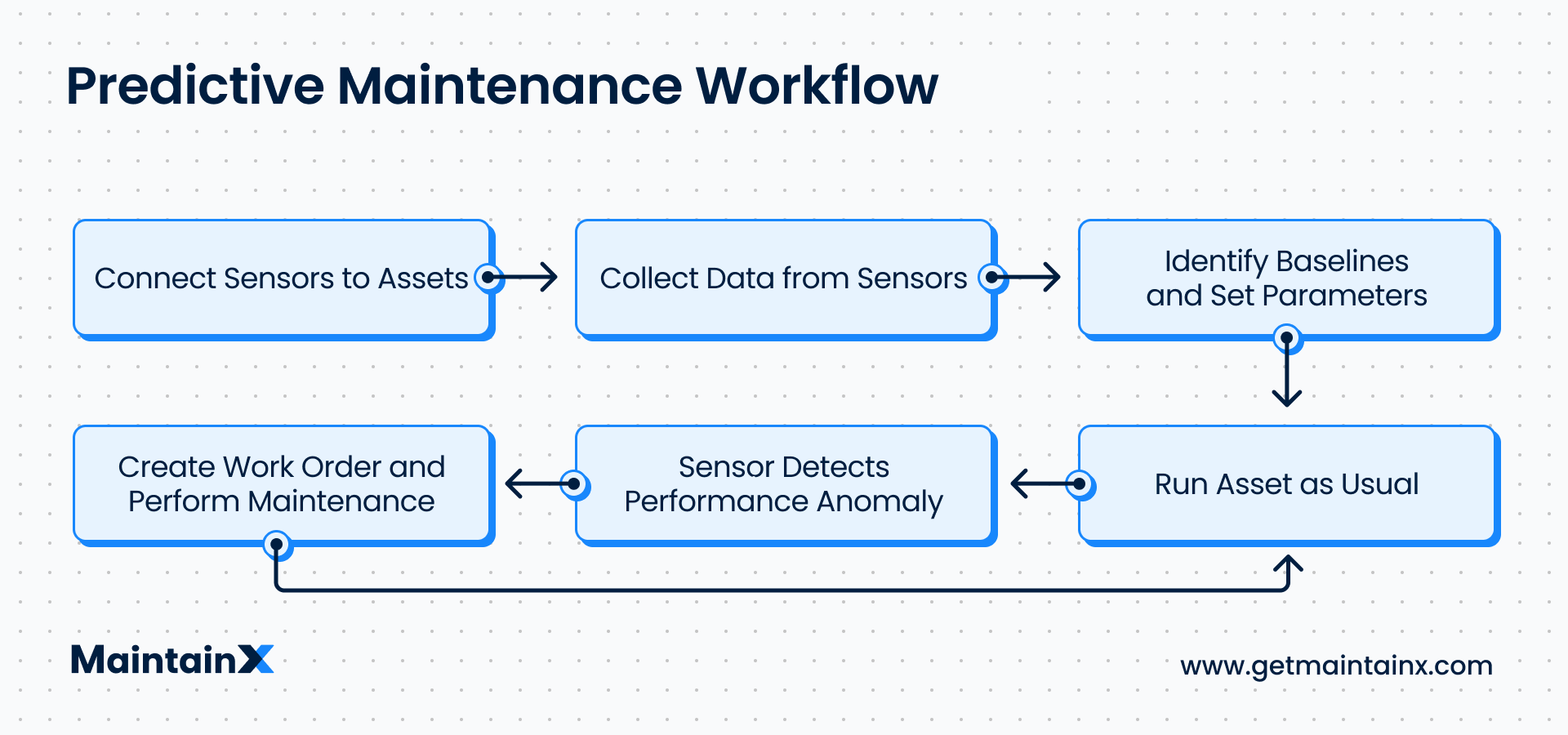
This proactive approach not only minimizes equipment downtime by alerting teams to potential issues before they escalate but also enhances the overall operational flow, ensuring a seamless manufacturing process.
Operational Technology
Meanwhile, operational technology (OT) refers to automation systems that monitor and manage events and processes. It includes programmable devices that interact with the physical world and make changes or adjustments in industrial operations. This hardware and software observes, monitors, and causes equipment, assets, and processes changes. OT systems are deployed in many industries, from manufacturing to robotics.
For example, Industrial Control Systems (ICS), a primary form of Operational Technology (OT), manage and regulate industrial processes using solutions like SCADA (Supervisory Control and Data Acquisition) for real-time data handling and Programmable Logic Controllers (PLCs) for tasks like monitoring machine efficiency and automating operations.
Manufacturing companies will generally have to deal with information and operational technology onsite. First is the physical aspect of manufacturing, where operational technology systems (OT systems) come in: managing your manufacturing processes and carrying out maintenance activities, among others. For example, predictive maintenance and sensors can increase equipment lifecycle and help prevent equipment failure and costly shutdowns.
“Digital transformation is the essential bridge between the business of today and the business of tomorrow. . . . For every organization, a strategic approach to digital transformation is crucial. Digital possibilities must shape strategy. And technology and operational decisions need to be adaptive and aligned.”
Deloitte
IT/OT Convergence
Overall, IT/OT convergence is a powerful tool that can help businesses improve their manufacturing operations. By harnessing the synergy between IT and OT, businesses can drive innovation, accelerate growth, and stay competitive in the rapidly evolving Industry 4.0 landscape.
Additional benefits of IT/OT convergence include the following:
- Increased agility: IT/OT convergence can help businesses respond more quickly to changes in demand or market conditions.
- Improved safety: By providing real-time data visibility, IT/OT convergence can help businesses identify and address safety hazards more quickly.
- Enhanced compliance: By using data to track and manage compliance, businesses can reduce the risk of fines and penalties.
But manufacturing companies also have to manage the digital realm of business operations: handling data and using insights to organize their operations. This is even more pertinent in Industry 4.0, as the Industrial Internet of Things (IIoT) gains more and more ground. As digital transformation becomes more popular, figuring out how to balance IT and OT will become more critical for companies.
For example, traditional preventive maintenance might work on a time-based schedule.
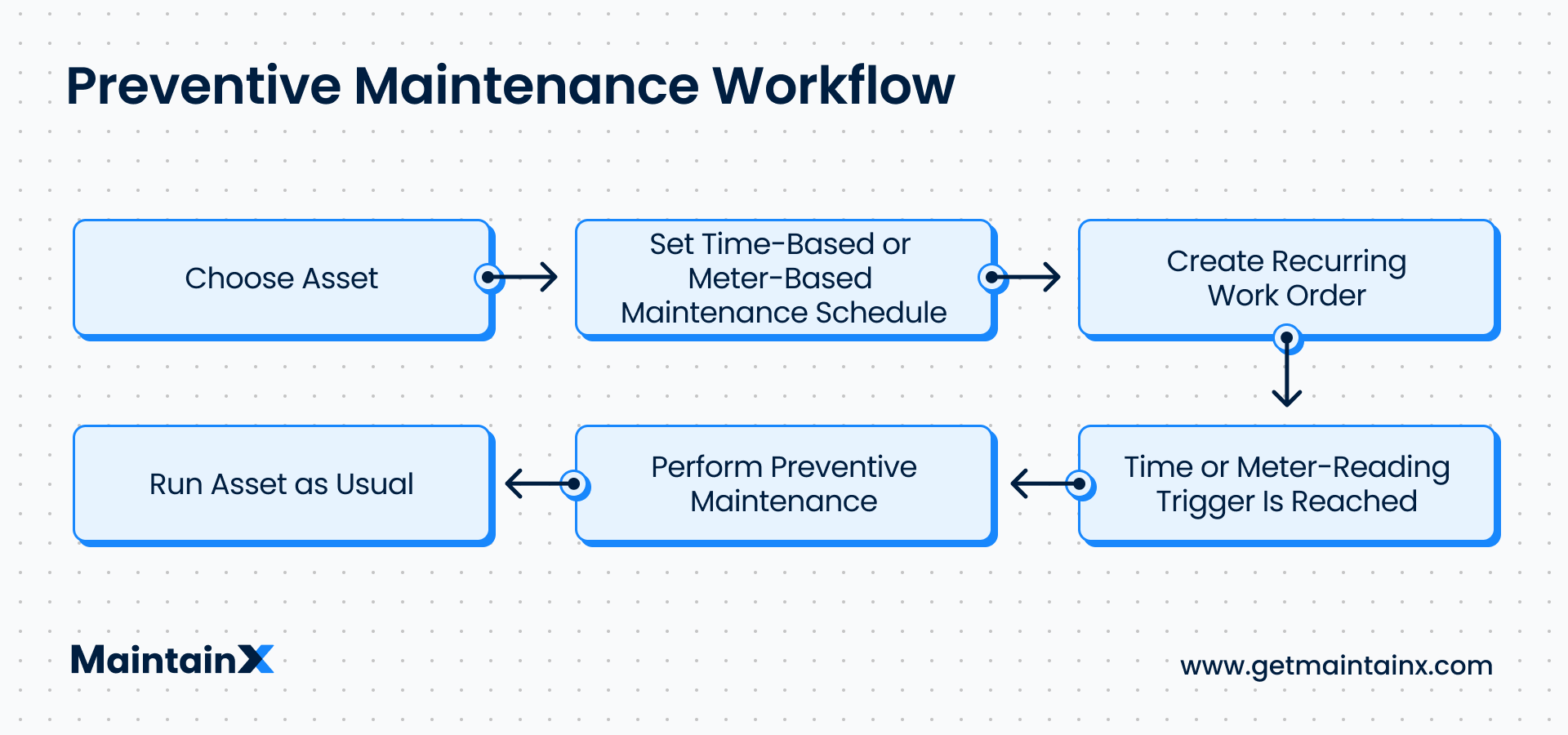
For instance, you might carry out weekly lubrication, monthly filter changes, etc. However, you can incorporate predictive maintenance into your activities with IoT sensors. Advances in machine-to-machine communication and machine learning have created a sea change, enabling the data to be captured and analyzed in real time. MaintainX’s robust Reporting provides decision-makers with actionable data.
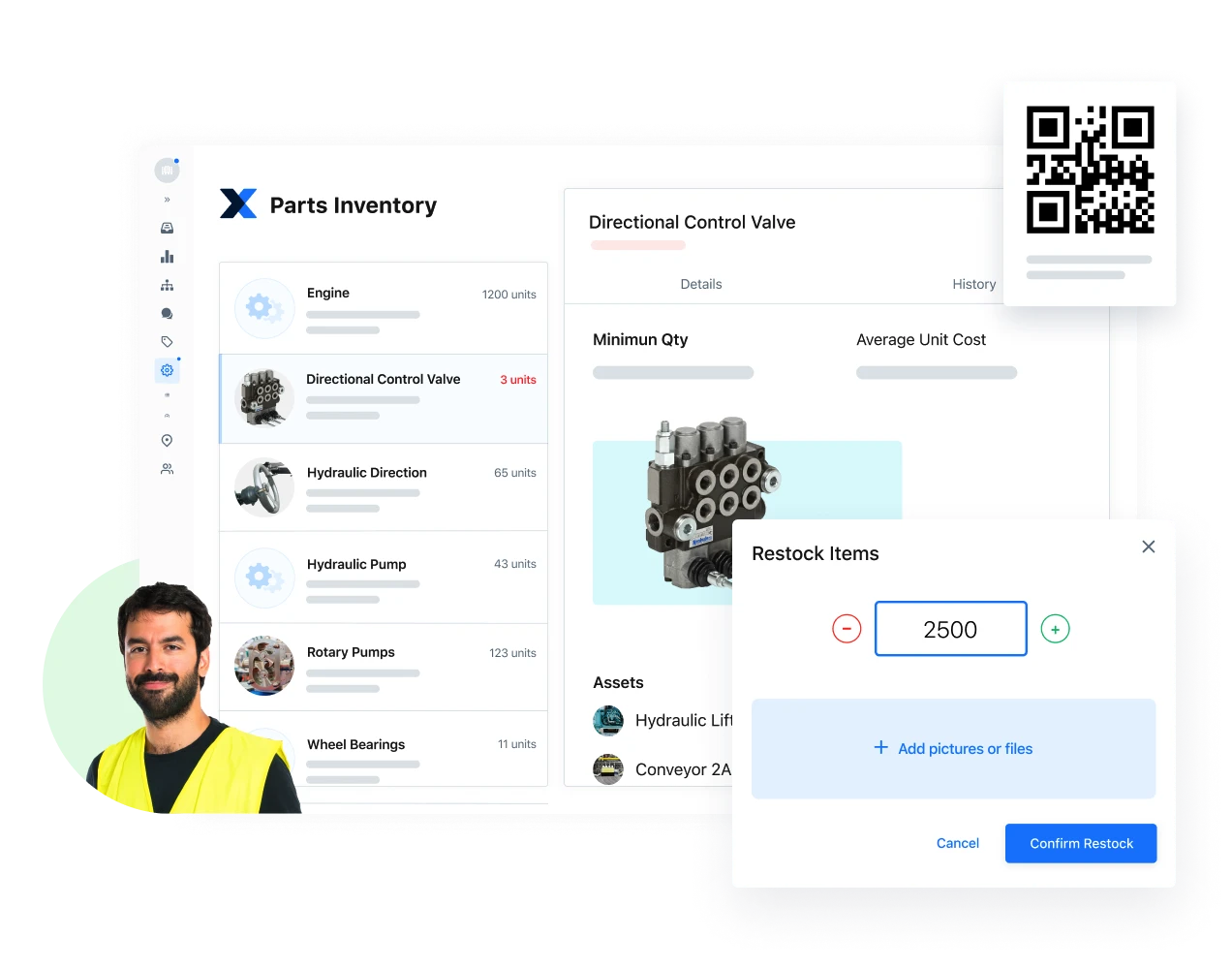
You could optimize your maintenance management process using real-time data. This could prevent breakdowns, reduce downtime, and improve corrective actions. For example, sensors can trigger notifications at certain thresholds based on their monitoring properties.
“As digital capabilities become more strategic, and complex work-arounds become less and less feasible, more companies are getting serious about breaking down these silos and converging the IT/OT operating model.”
McKinsey
IT/OT Convergence Use Cases
How can IT systems and connectivity improve your OT activities? First, consider how IT and OT convergence can optimize your business processes.IT/OT convergence initiatives are applied in various industries. Some of these are:
Manufacturing
Combining the best of IT and OT enables organizations to manage and direct their resources toward the best outcomes. IT/OT convergence gives manufacturers a holistic view of their supply chain: manufacturers know where to save costs and how much demand exists for their product, which can drive manufacturing operations.
Medical and Pharmaceutical Technology
The medical field uses operational technology as well. Medical monitoring devices can collect data about patient health and share it with necessary medical professionals, enabling better patient analysis and outcomes.
Maintenance
Combining information systems and operational systems allows organizations deeper insight into the functionality of their maintenance processes. By monitoring equipment performance data, maintenance teams can get a clearer picture of the effectiveness of their maintenance efforts and head off equipment disruptions.
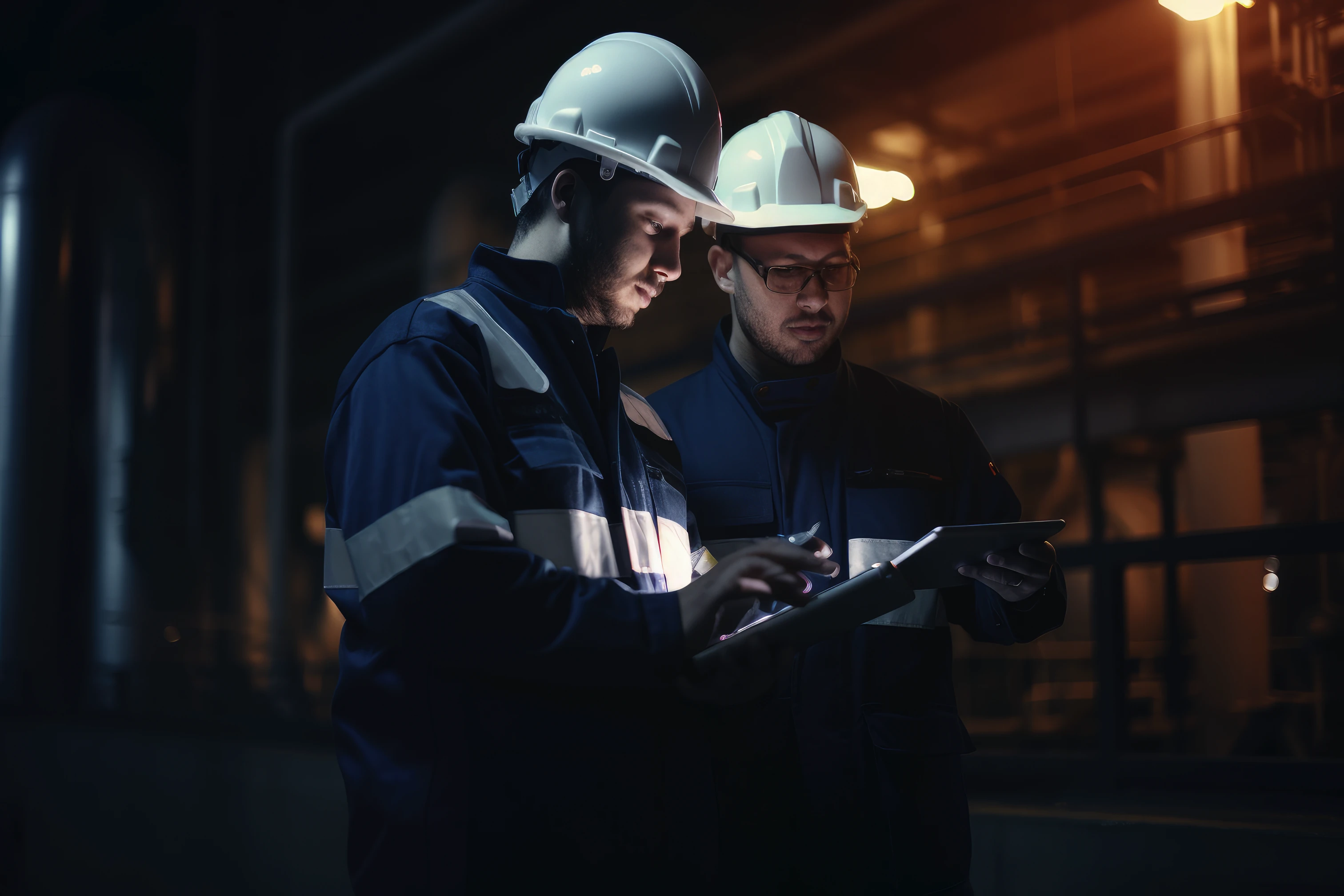
Challenges of IT/OT Convergence
Synchronizing Systems
Because IT and OT networks are often under different purviews, it can be challenging to combine their processes. For example, in practice, enterprise IT is headed by a Chief Information Officer overseeing the actions of software engineers and others. On the other hand, operational tech tends to be managed by shop floor managers, who a Chief Operating Officer oversees. Both departments have different organizational and operating systems and protocols. Reorganizing both teams to be more compatible is often easier than it sounds and requires careful consideration and planning.
Overlooking System Security
Connected to the first point, converging teams and efforts can lead to oversights regarding system security. Operational workers, who work less with cloud computing, might be less aware of cybersecurity protocols, firewalls, and malware risks. Consequences might be significant if IT teams don’t communicate the cybersecurity risks of specific protocols. All it takes is a simple oversight to allow a hacker to exploit your vulnerabilities. Keeping your businesses protected from cyberattacks is crucial to data security.
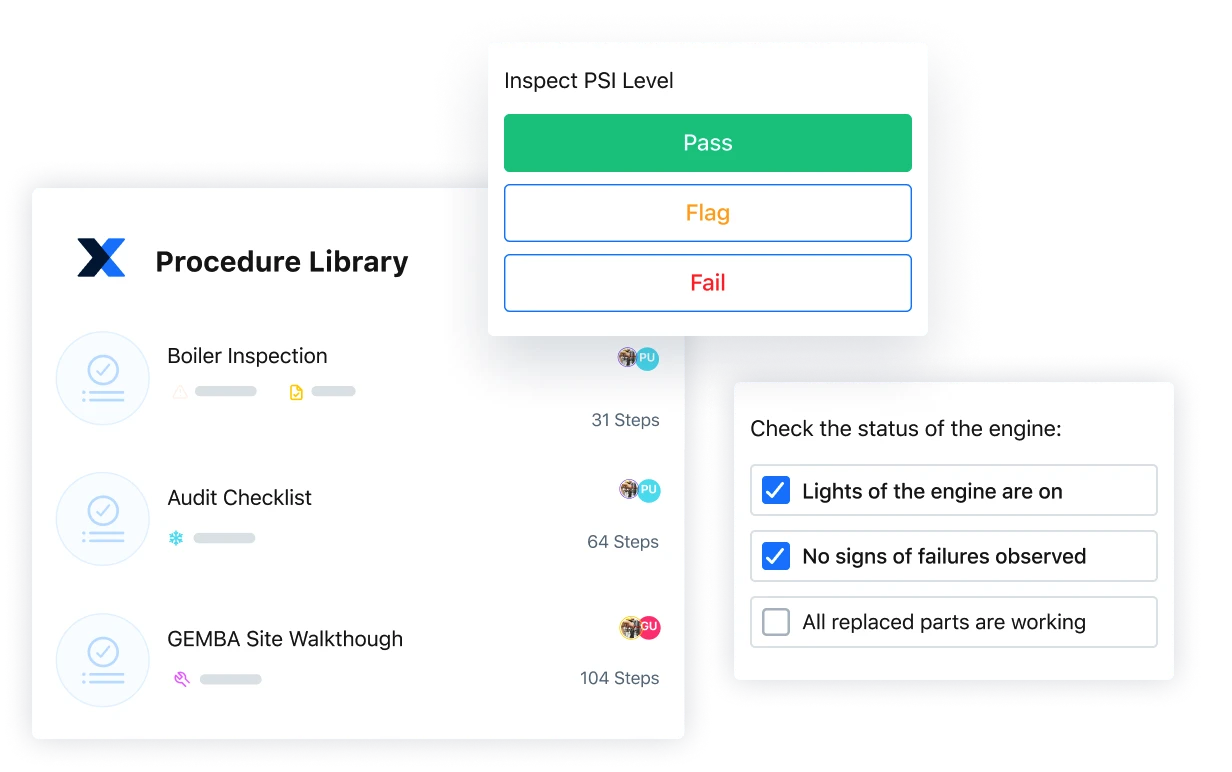
Fundamentals of IT and OT Convergence
What it means to converge information technology and OT environment will look different for every organization. Your business goals, company size, data center, and vision will guide the specifics of your approach. However, here are some points to consider in all cases.
Establish Guiding Principles and Goals
Before proceeding with any changes, establish where you want to go. What are you trying to achieve by using IT and OT together? Look at your business and your operations. Define the KPIs for the business as a whole and the IT and OT processes individually.
“…[W]e can collect information about the state of our business in real-time, put it in one location, plug it into the cloud… our machine-learning algorithms are going to learn about our business in real-time, make predictions or recommendations on how to improve the process in real-time and push back those recommendations.”
Walker Reynolds
Establish Leadership
Once you know the goals, define individual responsibilities. Integrating IT and OT processes requires a high degree of collaboration. If the concerned teams have been working in silos until now, you must examine their internal architectures closely.
The teams might require new systems of communication or new chains of command. Focus on creating leadership that applies consistent standards across teams.
Collaborating remotely is particularly useful in the manufacturing industry, where equipment is often located in different parts of a factory or even in different parts of the world. In these situations, it may not always be possible or practical for maintenance professionals to travel to the equipment site to perform maintenance tasks.
Managers can use a CMMS to assign tasks and track progress remotely. Teams can use the system to view and complete work orders, as well as update their status and progress as they work on them. For example, a manager can send notifications and alerts after assigning work orders or updating the maintenance schedule. A robust CMMS, like MaintainX, can store and share documents, images, and other resources relevant to the maintenance process.
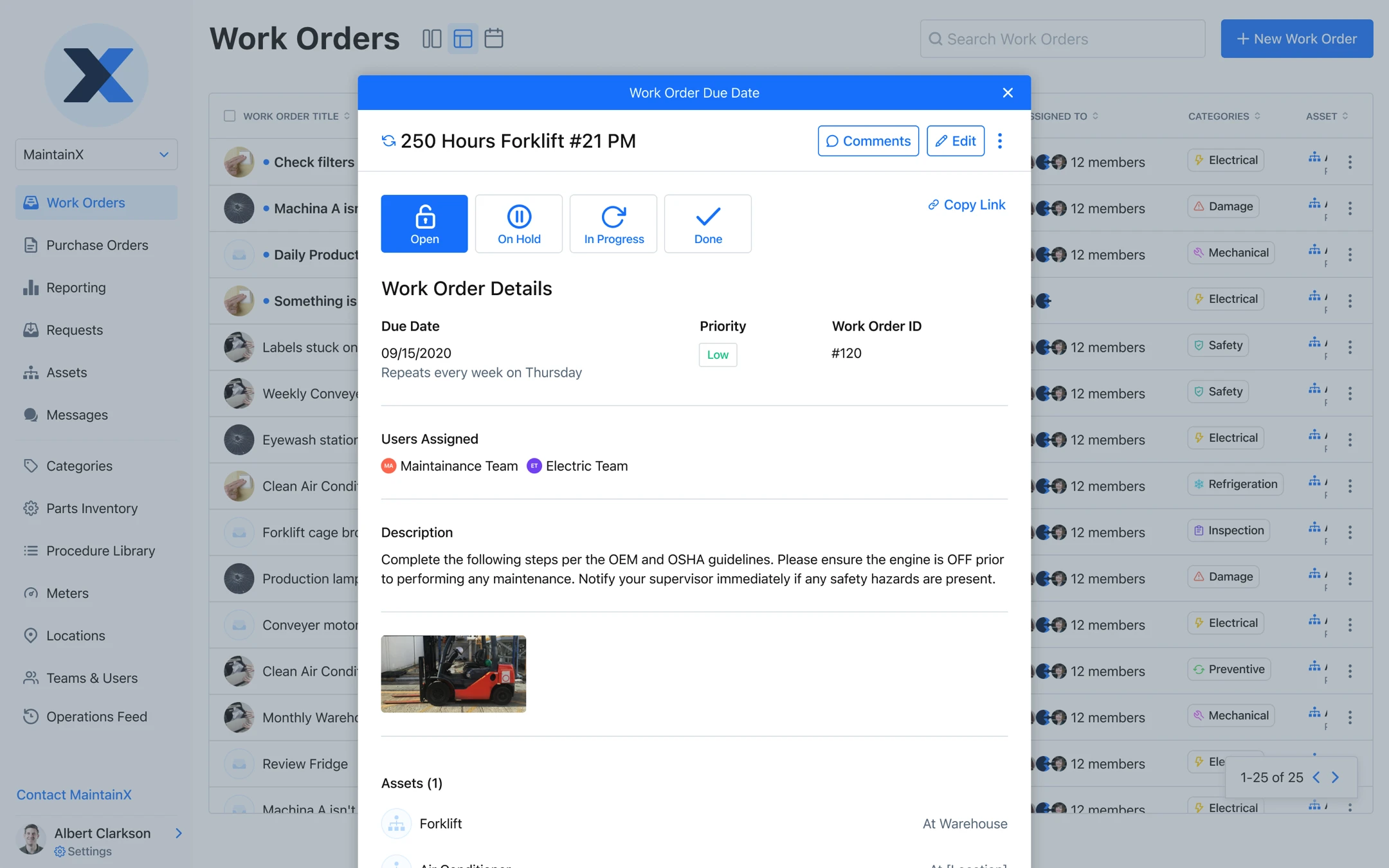
Centralize Data and Security Management
As we stated earlier, security is a significant challenge with this kind of convergence. Both departments may have different security standards and protocols, but a single guiding model is necessary. Create standard operating procedures for protecting data and the security of the company as a whole.
Check out the National Institute of Standards and Technology (NIST) framework for more information about managing and reducing cybersecurity risk to your critical infrastructure and industrial control systems. NIST 800-171 includes standards and guidelines to protect controlled unclassified information (CUI) not regulated by the US government. This can include identification and authentication, and configure management.
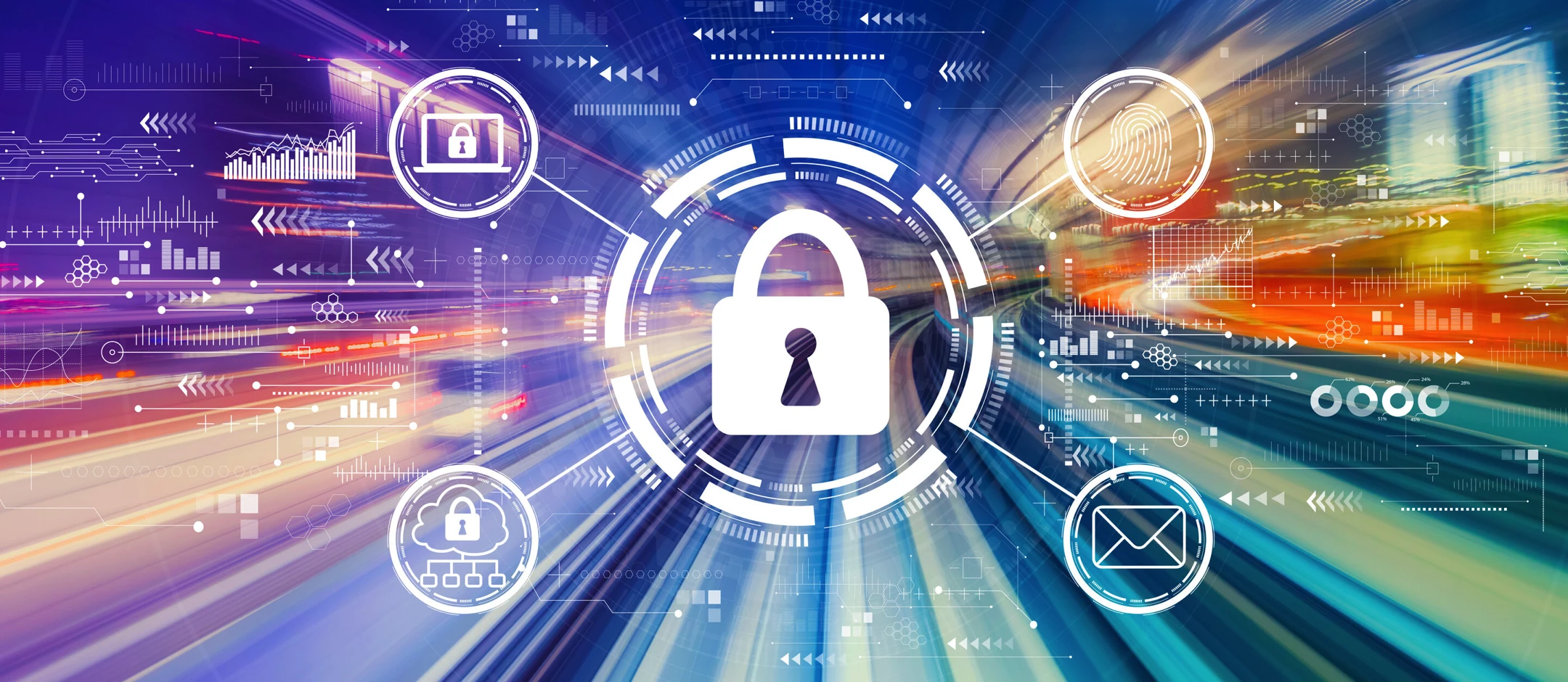
CMMS Data Privacy
MaintainX takes data privacy very seriously and has again received SOC 2 Type 2 Compliance Renewal and ISO 27001 Certification.
SOC 2 Type 2 Compliance
The SOC 2 Type 2 compliance designation is an external audit of MaintainX’s internal controls that protect customer information. The audit focuses explicitly on MaintainX’s description of its organizational system and designates that our internal controls are designed and operating effectively.
As the compliance renewal reinforces, MaintainX fulfills the crucial industry standards that SOC 2 criteria require.
SO 27001 Certification
As with our 2023 SOC 2 renewal, the MaintainX platform received ISO 27001 certification. The certification confirms once again how seriously we take the protection of our customers’ information, the privacy of their data, and their supporting services.
According to the International Organization for Standardization, its internationally accepted ISO 27001:2022 (previously known as ISO/IEC 27001:2013):
“specifies the requirements for establishing, implementing, maintaining and continually improving an information security management system within the context of the organization.”
.webp)
Combine Your Information and Operational Technology with MaintainX
MaintainX is a CMMS system that helps centralize data and streamline processes. Service providers like MaintainX can help you integrate your IT and OT processes by facilitating collaboration, helping to establish and communicate your standard operating procedures, and managing your data. Enterprise asset management software, like MaintainX, simplifies your work management, asset maintenance, planning and scheduling, supply chain management, and environmental, health, and safety (EHS) initiatives.
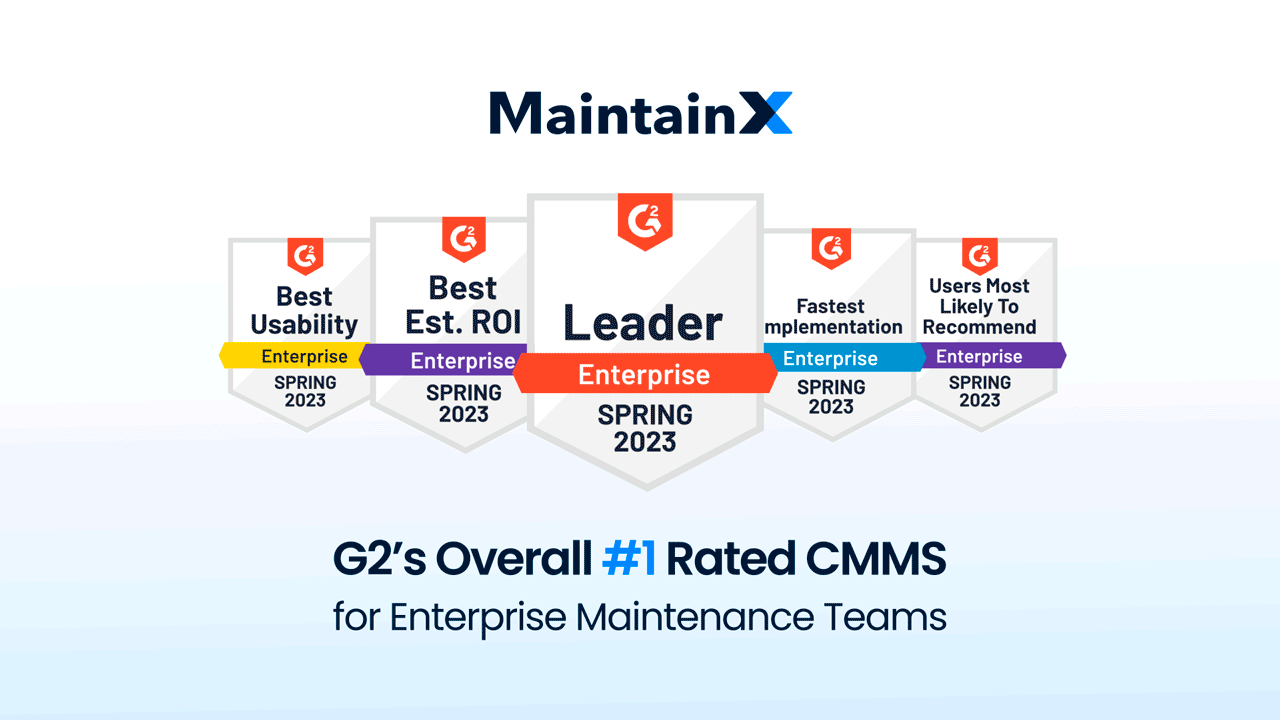
MaintainX’s powerful Reporting features provide valuable data and insights into your operations. These insights will help you to make data-driven decisions to optimize your business processes further. On the ground, real-time KPIs like MTTR and MTBF can provide the actionable data you need for decision-making, like when it’s time for equipment upgrades.
Using MaintainX to manage your work orders also ensures you are creating an audit trail as you work. This means you can evaluate the performance of your convergence as you proceed. If that sounds interesting, try MaintainX today!
FAQs
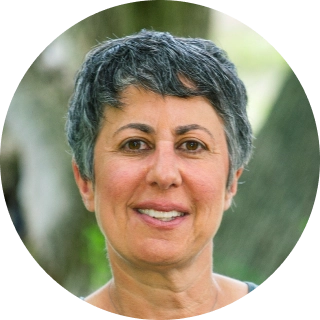
Caroline Eisner is a writer and editor with experience across the profit and nonprofit sectors, government, education, and financial organizations. She has held leadership positions in K16 institutions and has led large-scale digital projects, interactive websites, and a business writing consultancy.