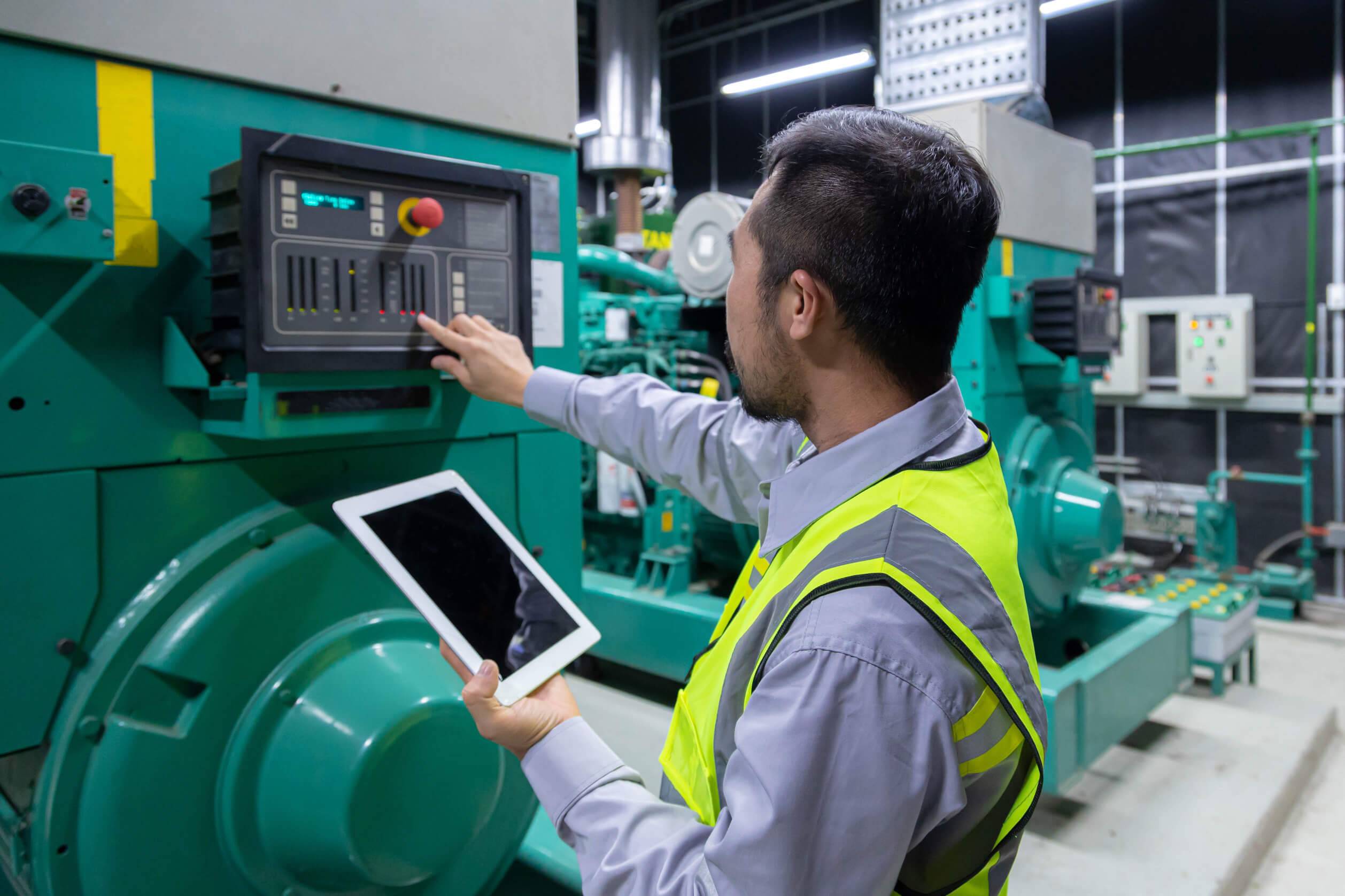
While preventive maintenance is one of your best bets for reducing unplanned downtime, unlocking greater efficiency, and optimizing your spending, it’s possible to take your maintenance program even further. Despite its benefits, preventive maintenance on a schedule can lead to unwanted downsides such as overmaintenance and wasted resources.
This is where predictive maintenance comes in. By predicting specific failures, you can narrow down the scope of your preventive maintenance tasks and limit them to when they are most necessary. This can be a challenging approach, but when done right, it can help you better manage your resources, address issues with more specificity, and improve asset lifespans. Plus, you can reduce overmaintenance and increase asset availability.
Successful predictive maintenance relies on teams using the right software, and in this article, we explore the best software options available, explore key features to look out for, and offer tips on making the right choice.
What is predictive maintenance software?
Predictive maintenance software solutions help teams plan, execute, and manage predictive maintenance tasks. They typically include preventive maintenance modules such as work order management and scheduling tools but also have asset monitoring and integration functions that facilitate predictive workflows. By analyzing data from various sources, such as sensors, historical maintenance records, and operating conditions, predictive maintenance solutions can identify patterns and potential issues before they lead to equipment failure.
Top 10 predictive maintenance software solutions
While predictive maintenance hasn’t yet fully taken over the maintenance field, the market is already filled with options to help organizations begin their journey. Here’s a list of the top 10 predictive maintenance software solutions currently available.
1. MaintainX
MaintainX is an AI-powered, mobile-first software Computerized Maintenance Management Software (CMMS) that offers simplified work order management, seamless asset tracking, and robust integrations.
Key features
- Asset management.
- Digital work orders.
- Inventory and parts management.
- Real-time reporting and analytics.
- Mobile-first approach.
- Integration with existing ERP systems.
Strengths
- Seamlessly connects sensors, PLCs, SCADA systems, MES, and Historians to the CMMS.
- Monitors parameters like temperature and liquid levels to trigger maintenance when needed.
- Offers a user-friendly interface with strong mobile capabilities.
- Proven return on investment (ROI) through numerous case studies.
2. IBM Maximo
IBM Maximo is an enterprise asset management platform leveraging AI and IoT for advanced predictive maintenance and lifecycle management.
Key features
- Asset lifecycle management.
- Predictive maintenance analytics.
- Integration with IoT and AI.
- Work order management.
- Extensive reporting capabilities.
Strengths
- Comprehensive functionality powered by IBM’s AI technologies.
- Robust analytics, which are ideal for large enterprises with complex asset management needs.
- High scalability to accommodate growing asset bases and evolving requirements.
3. SAP Predictive Maintenance and Service
SAP Predictive Maintenance and Service is a solution integrating machine learning with SAP ERP to deliver real-time monitoring and predictive analytics.
Key features
- Integration with SAP ERP.
- Machine learning for predictive analytics.
- Real-time monitoring of asset health.
- Automated service processes.
Strengths
- Strong integration with SAP systems for seamless workflow.
- Advanced analytics and machine learning capabilities for accurate predictions.
- Comprehensive support for various industries, enhancing its versatility.
4. UpKeep
UpKeep is a mobile-focused CMMS designed for easy work order management, maintenance scheduling, and inventory tracking.
Key features
- Mobile-first CMMS.
- Work order management.
- Preventive and predictive maintenance scheduling.
- Inventory management.
- Real-time reporting.
Strengths
- Highly user-friendly with a focus on ease of use in the field.
- Mobile-centric design allows for effective maintenance management on the go.
- Quick implementation and a short learning curve, making it accessible to teams of all sizes.
5. Fiix by Rockwell Automation
Fiix is a CMMS offering IoT integration, predictive analytics, and scalable asset management for organizations.
Key features
- AI-driven predictive maintenance.
- Asset management.
- Work order management.
- Integration with IoT sensors and business systems.
Strengths
- Advanced predictive maintenance capabilities through AI and IoT integration.
- Strong reporting and analytics for data-driven decision-making.
- Scalable solution suitable for organizations with growing and diverse asset bases.
6. Dude Solutions (Asset Essentials)
Dude Solutions is an asset management solution with predictive and preventive maintenance tools for multiple industries.
Key features
- Work order management.
- Asset tracking.
- Preventive and predictive maintenance.
- Comprehensive reporting.
Strengths
- Tailored to various industries, including manufacturing, healthcare, and education.
- Strong community support and extensive resources for users.
- Flexible and adaptable to different organizational needs and structures.
7. eMaint by Fluke
eMaint is a CMMS platform offering seamless integration with Fluke measurement tools for preventive and condition-based maintenance.
Key features
- Asset management.
- Work order management.
- Preventive and predictive maintenance.
- Mobile access.
Strengths
- Seamless integration with Fluke’s measurement tools and devices for condition-based monitoring.
- Bridges the gap between hardware and software.
- Robust support for various maintenance strategies and approaches.
8. Hippo CMMS
Hippo CMMS is a maintenance management system that streamlines preventive maintenance, asset tracking, and more.
Key features
- User-friendly interface.
- Work order management.
- Preventive maintenance scheduling.
- Asset tracking.
- Mobile access.
Strengths
- Intuitive design makes it easy to implement and use, even for smaller organizations.
- Strong customer support and extensive training resources.
- Cost-effective solution that scales with business growth.
9. Infor EAM
Infor EAM is an enterprise-grade asset management solution with predictive analytics and IoT integration, designed for large-scale operations.
Key features
- Asset management.
- Work order management.
- Predictive maintenance analytics.
- Mobile access.
- Integration with IoT and ERP systems.
Strengths
- Robust functionality and scalability, ideal for large enterprises.
- Advanced analytics and IoT integration for comprehensive asset management.
- Extensive customization options to fit specific business processes.
10. Augury
Augury is an AI-driven machine health platform offering real-time condition monitoring and predictive maintenance insights to reduce downtime.
Key features
- AI-based machine health solutions.
- Real-time condition monitoring.
- Predictive analytics.
- Maintenance insights.
Strengths
- Cutting-edge AI and machine learning capabilities focused on machine health.
- Provides precise predictive maintenance insights to prevent production downtime.
- Strong focus on reducing maintenance costs and extending asset life.
How to choose the best predictive maintenance software
Choosing the right predictive maintenance software can be overwhelming, given the variety of options available. To make the best decision, it's important to focus on key factors that align with your organization’s needs. Here’s a quick guide to help you navigate the selection process.
Identify your requirements & essentials
Step one in this process should be clearly defining your organization’s specific maintenance needs. What are the goals of your maintenance program? Also, consider the type of assets you manage, the size of your operation, and the critical maintenance challenges you face. Knowing these essentials will help you narrow down your options and avoid getting lost in the sea of software solutions.
Prioritize ease-of-use
No matter how powerful a software solution is, it won't be effective if your team can't use it. This is especially important with predictive software that relies on accurate and robust data entry by users. Look for software with an intuitive user interface that requires minimal training. Ease-of-use ensures faster adoption, less resistance from users, and more consistent data entry and monitoring.
Ensure integration with existing systems
To get the best out of your predictive maintenance software, it should integrate seamlessly with your existing systems, such as Enterprise Resource Planning (ERP) systems, Computerized Maintenance Management Systems (CMMS), or Internet of Things (IoT) devices. This integration enables smooth data flow and prevents silos, making it easier to gain comprehensive insights into your operations.
Look for robust predictive analytics capabilities
The core of predictive maintenance is condition monitoring and data analytics. Make sure the software you choose has advanced predictive analytics capabilities, including machine learning and real-time data analysis. These features will allow you to accurately forecast maintenance needs, optimize scheduling, and reduce downtime.
Consider scalability and flexibility
As your organization grows, your maintenance needs will evolve. Choose software that can scale with your business and adapt to changing requirements so you don’t have to seek new solutions whenever your needs change. This scalability ensures that your predictive maintenance strategy remains effective, regardless of how your asset base or operations expand.
Evaluate support and training options
Even the best software requires good support. Check if the vendor offers comprehensive support and training resources, including customer service, online tutorials, and user communities. Strong support ensures that your team can effectively use the software and troubleshoot any issues that arise.
Consider reporting features
Whatever your maintenance program, predictive or otherwise, it’s important that you keep an eye on your performance to identify areas of improvement. Getting a software solution with robust reporting features will enable you to track your most critical KPIs at a glance, measure your progress, and identify any potential mistakes you’re making. You’ll be able to eliminate errors and double down on what works.
Unlock the best predictive maintenance software with MaintainX’s CMMS
Ready to transform your maintenance operations? Unlock the power of predictive maintenance with MaintainX’s CMMS. Designed to streamline your workflow, improve asset reliability, and reduce downtime, MaintainX offers the tools you need to keep your equipment running smoothly and efficiently.
Asset & equipment management
- Centralizes the tracking and management of all assets.
- Enables predictive maintenance by monitoring asset health and performance through data collection and analysis.
Reporting & analytics
- Provides custom dashboards and reports to analyze asset performance.
- Helps identify trends and predict maintenance needs, reducing unplanned downtime.
Digital work orders
- Streamlines maintenance workflows by creating, assigning, and tracking work orders in real time, ensuring timely maintenance interventions based on predictive insights.
Inventory & parts management
- Tracks inventory levels and usage to ensure that necessary parts are always available, which is crucial for timely predictive maintenance actions.
Meters and sensor integration
- Allows real-time data collection from equipment, enabling predictive maintenance by monitoring asset conditions and triggering maintenance actions when predefined thresholds are met.
Predictive maintenance software FAQs
Are companies using AI for predictive maintenance of industrial equipment?
Many companies are increasingly leveraging Artificial Intelligence (AI) for predictive maintenance of industrial equipment. AI algorithms analyze vast amounts of sensor data to detect patterns and anomalies that may indicate potential equipment failures. This proactive approach allows businesses to predict maintenance needs before issues arise, minimizing downtime and optimizing the performance of critical assets.
What is preventive maintenance software?
Preventive maintenance software is a tool designed to schedule and manage regular maintenance activities to prevent equipment breakdowns and failures. Unlike predictive maintenance, which relies on data to predict future failures, preventive maintenance follows a set schedule based on time or usage intervals. This software helps organizations plan routine inspections, part replacements, and other tasks to maintain optimal equipment performance.
How can predictive maintenance software enhance the longevity of a truck/vehicle fleet?
Predictive maintenance software can significantly enhance the longevity of a truck or vehicle fleet by continuously monitoring the health of each vehicle through sensors and diagnostic data. By identifying early signs of wear and tear, the software can alert maintenance teams to potential issues before they become serious, allowing for timely repairs. This proactive approach reduces the risk of major breakdowns, lowers maintenance costs, and extends the overall lifespan of the fleet.
How can machine learning be applied to predictive maintenance software strategies?
Machine learning can be applied to predictive maintenance software strategies by analyzing historical and real-time data to identify patterns that predict equipment failures. These algorithms learn from the data over time, becoming more accurate in forecasting when maintenance is needed. By using machine learning, organizations can achieve more precise predictions, optimize maintenance schedules, and reduce unnecessary maintenance activities, ultimately leading to cost savings and improved operational efficiency.
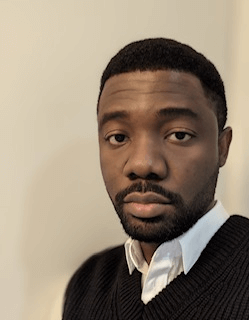
Lekan Olanrewaju is a content writer with years of experience in media and content creation. He has held positions at various media organizations, working with and leading teams at print magazines, digital publications, and television productions.