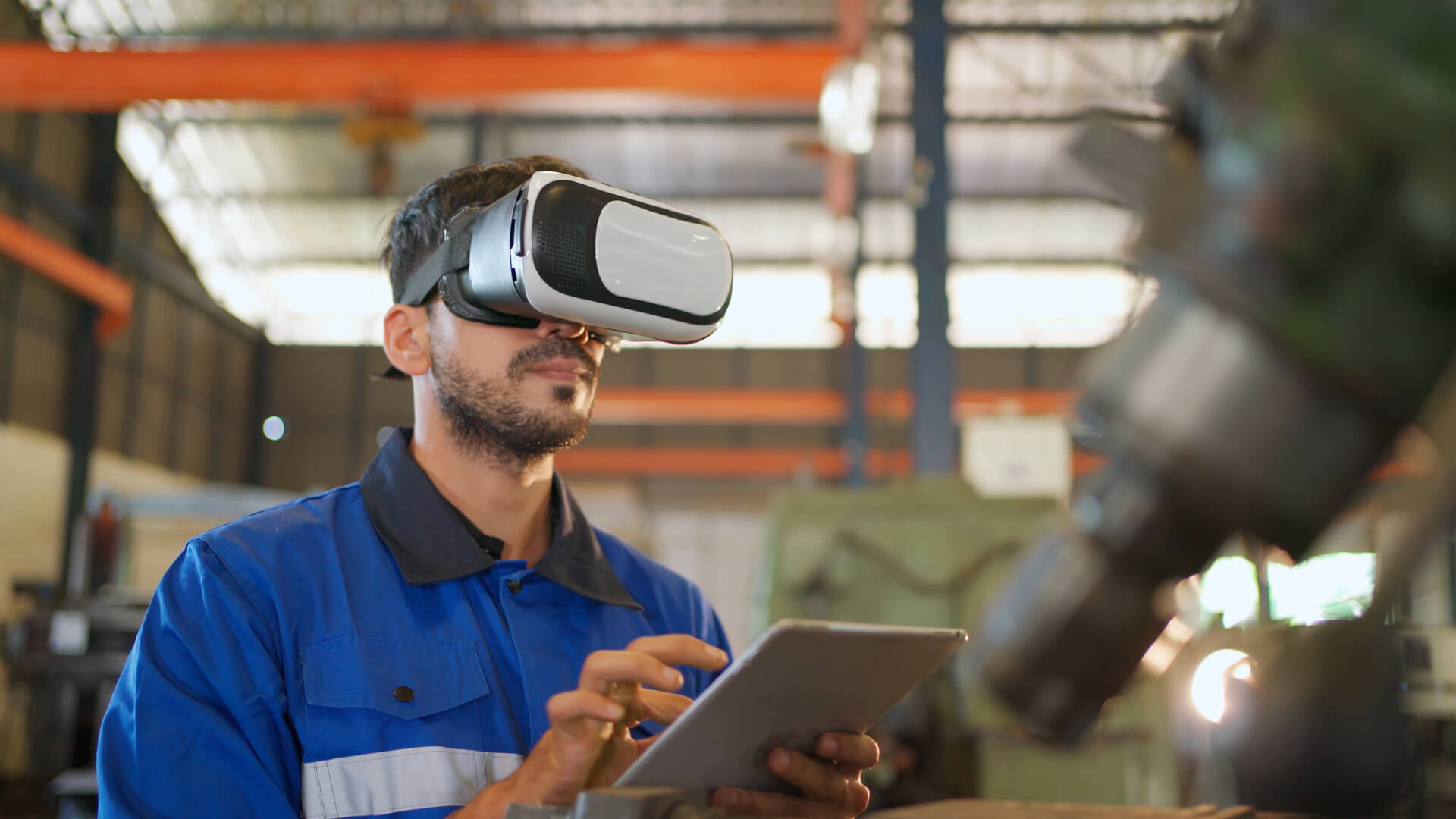
Technology has transformed manufacturing. The fourth industrial revolution is reshaping manufacturing processes with new technologies like the industrial internet of things (IIoT), artificial intelligence (AI), and machine learning (ML). Digital augmentation and automated work are part of that same revolution.
Augmentation refers to providing employees with an integrated and assistive environment that allows them to operate more efficiently. If you’re not entirely familiar with augmentation technologies but are keen on digital transformation, this post is for you. Below, we explain the meaning of digital augmentation and augmented work, the technologies they rely on, and the challenges they solve.
What are Digital Augmentation and Augmented Work?
Digital augmentation and augmented work involve providing workers with digital technologies like IoT, AI, and ML to operate more efficiently. The simplest example of augmentation is automated decision-making, where the system automatically screens defective parts.
Augmentation technologies integrate seamlessly into a modern manufacturer’s larger production ecosystem. As a result, they assist workers in performing tasks that would otherwise be harder to accomplish. The most popular form of augmentative technology is augmented reality headsets—a device that adds 3D visual renderings to a person’s field of vision.
However, augmentative technologies can have plenty of other use cases on your shop floor. For example, you can use sensors to monitor equipment or employee health. You can attach the sensor to the equipment’s surface or add it to the employee’s protective gear checklist.
“People who are skeptical of artificial intelligence (AI) and machine learning (ML) often harbor fears of robots stealing jobs and human workers being replaced by automatons. But the reality is that AI is increasingly being applied across sectors not to replace our jobs but to enhance them.”
Forbes
Why Should You Invest in Digital Augmentation?
As you can imagine, digital augmentation and augmented work are the future of work for manufacturers. In fact, the World Economic Forum reveals:
“87% of manufacturing companies have accelerated their digitization over the past year.”
Collectively, augmentative technologies provide an integrated, assistive environment where manufacturers can perform their tasks more efficiently, safely, and with minimum errors. Thanks to its efficiency and cost benefits, augmented technologies are making their way into increasing numbers of manufacturing facilities and processes.
According to the International Data Corporation, Europe’s human augmentation market—which includes technologies like exoskeletons, augmented reality (AR), virtual reality (VR), biometrics, brain-computer interfaces, and more—will reach $100 billion by 2026.
“We’re still at the beginning stages of this new era for large investors. Those who embrace digital and analytics as necessary instruments to augment decision making will have an enormous advantage over those who rely on personal judgment and incomplete data.”
McKinsey
Technologies That Enable Digital Augmentation
We talked about a few technologies—IoT, AI, ML—that enable digital augmentation. Let’s dive deeper into the role they play. Here’s how augmentative technologies collectively facilitate augmented work:
Step 1: Sensors Collect Data
Compact sensors help integrate digital systems with your manufacturing environment. For example, you can place sensors on an employee’s wearables or your equipment. The sensor will collect relevant data, such as vibrations or temperature, and transmit it over IoT, allowing your staff to monitor equipment in real time.
Regarding equipment, predictive maintenance uses sensors to alert maintenance teams to equipment before failure. In addition, predictive maintenance uses data and analytics to proactively identify and address potential equipment failures rather than reacting to them after they occur.
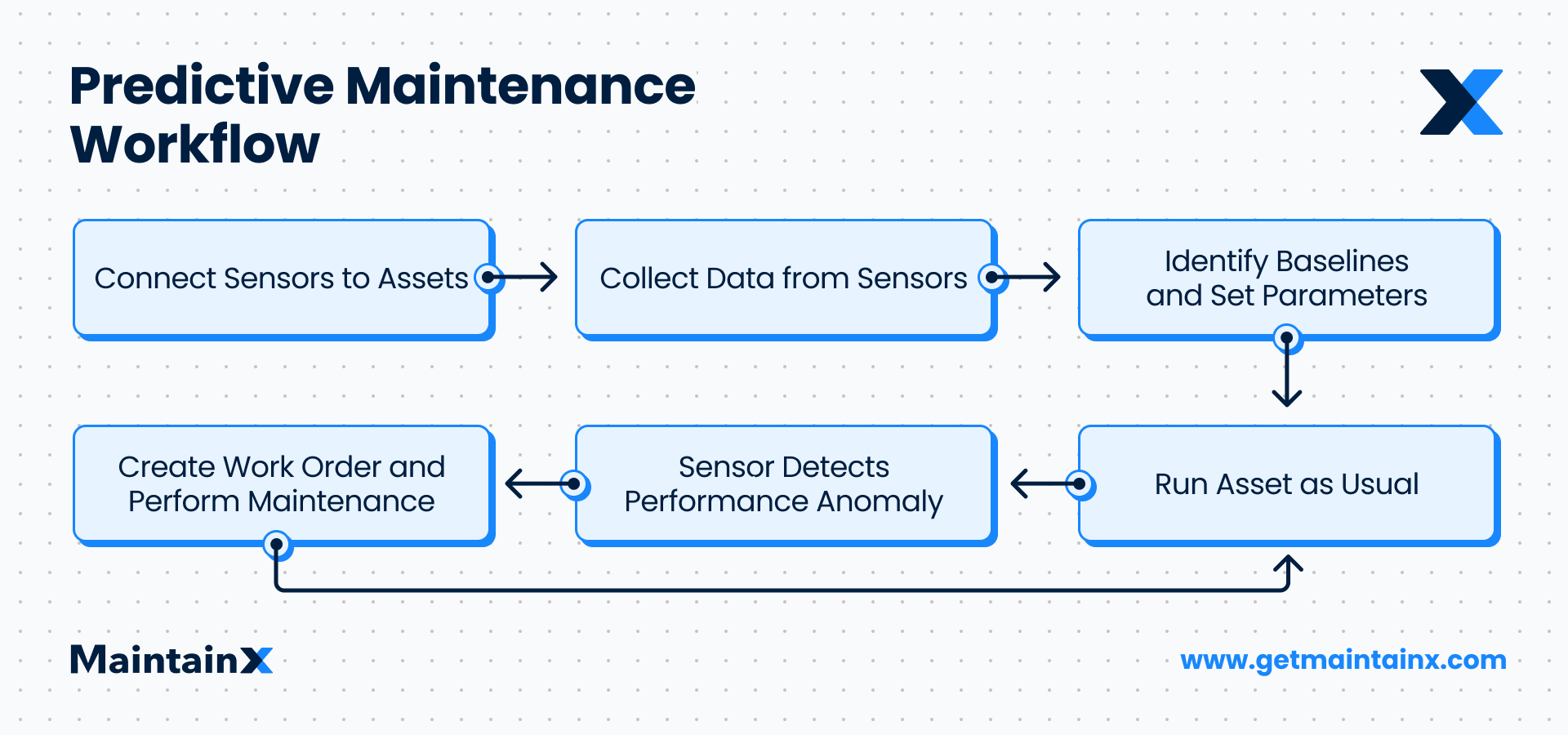
Step 2: IoT Connects Sensors With Systems
The IoT infrastructure includes WiFi, cloud storage, and security. This infrastructure connects your sensors with systems. Thanks to IoT, you can share real-time data with operators and IIoT devices for automated decision-making.
For example, if the thermometer detects temperature crossing the acceptable level, the IIoT device can automatically turn off equipment once it receives this information over the IoT.
Step 3: Big Data Empowers Augmentative Technologies
You can collect data from the sensors in a secure location, preferably on a cloud-based platform. For example, storing data in a cloud-based computerized maintenance management system (CMMS) can make data accessible remotely and ensure its security.
As you feed data into your AI and ML algorithms, they’ll become more efficient and allow you to make more insightful decisions. The algorithm can alert you regarding potential issues in equipment, enable you to identify opportunities to improve efficiency, and even fill a skills gap by automatically providing instructions to workers.
For example, suppose you’re collecting vibration data from across the shop floor from different machines that are the same model. Over time, the algorithm can predict a brewing issue more effectively. Identifying this issue before it becomes a problem allows you to avert failure and minimize downtime.
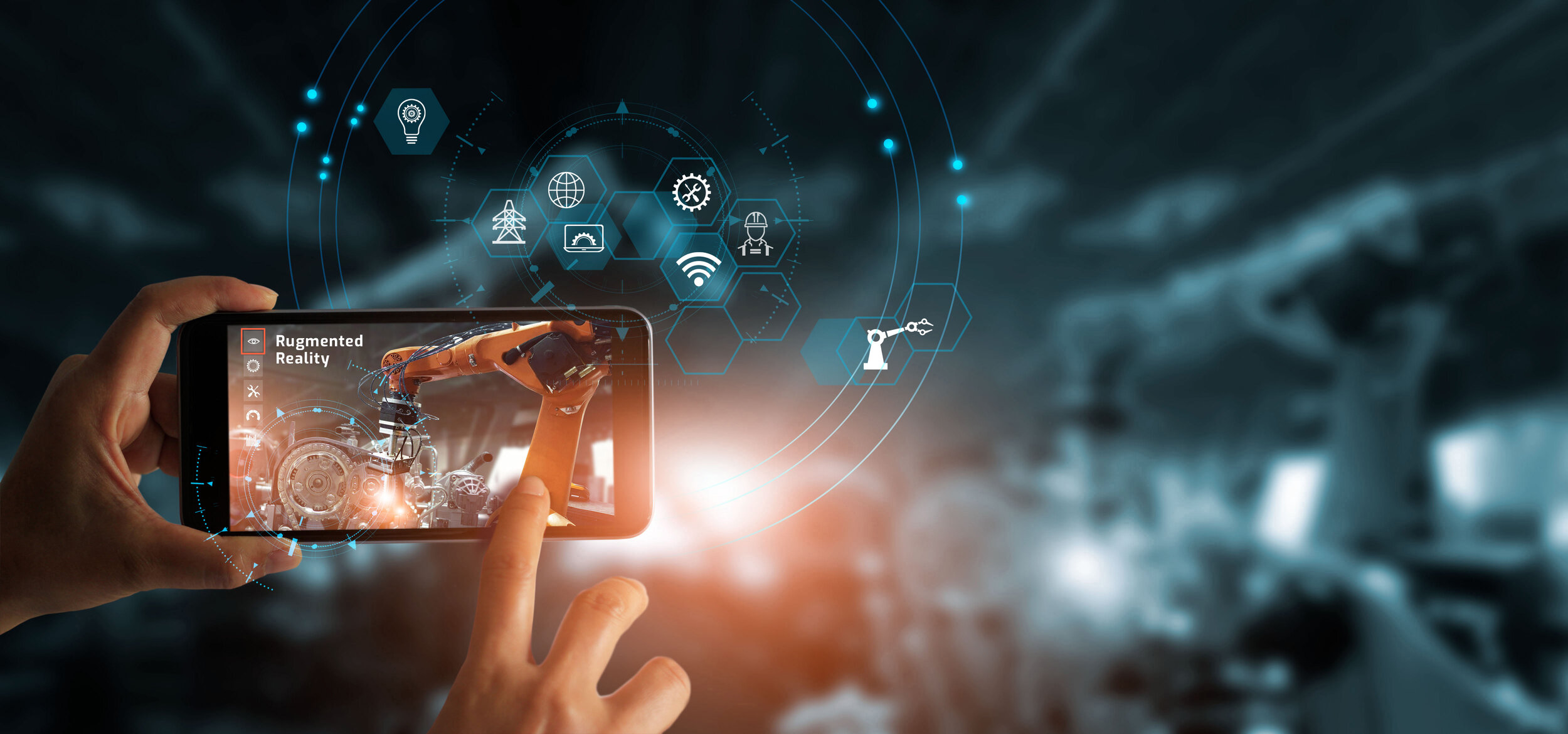
3 Challenges Augmented Work Solves for Modern Manufacturers
Implementing augmentative technologies will allow you to address some of the most pressing challenges of a modern manufacturer, such as:
Minimizing Human Error
You can place sensors on workers’ protective gear. The sensor can monitor the worker’s level of fatigue based on the worker’s bodily characteristics. Augmentative technologies can make repetitive tasks less boring using interactive work instructions, improving workers’ engagement and concentration. Ensuring workers are engaged and not fatigued can help minimize errors on the shop floor.
Streamlining Production
Monitoring all workers at all times is impractical. However, computer vision combined with AI and ML can analyze an operator’s actions as they work and guide workers to the next step. For example, computer vision might present a set of instructions to a worker after it captures a specific hand gesture, guiding the worker to the next steps while they acquire a new skill.
Improving Process Visibility and Control
Traditionally, manufacturers manually recorded and analyzed manufacturing data. However, augmentative technologies automate this process, providing greater process visibility. In addition, digital systems can auto-collect manufacturing data continuously, offering relevant parties all the information to make data-driven decisions.
How Manufacturers Can Use Digital Augmentation
One of the most valuable ways to use digital augmentation is for prescriptive maintenance—a maintenance approach that takes the use of data and ML a step further than predictive maintenance.
Prescriptive maintenance relies on algorithms to access manufacturing data and make suggestions. With this workflow, technicians will know of potential maintenance work before failure and/or scheduled preventive maintenance.
AR technology-based and mixed-reality devices like Microsoft HoloLens can overlay 3D information on a worker’s physical space. As the worker performs maintenance tasks, the camera records these interactions and relays them to the software. The software processes the information and provides real-time guidance to technicians on the best way to perform the maintenance task.
While AI and ML are far from achieving human intelligence, they still have basic problem-solving skills, which can help take actions necessary to prevent failure. For example, when a machine’s temperature is rising consistently, the algorithm can instruct the machinery to operate slowly and alert a technician.
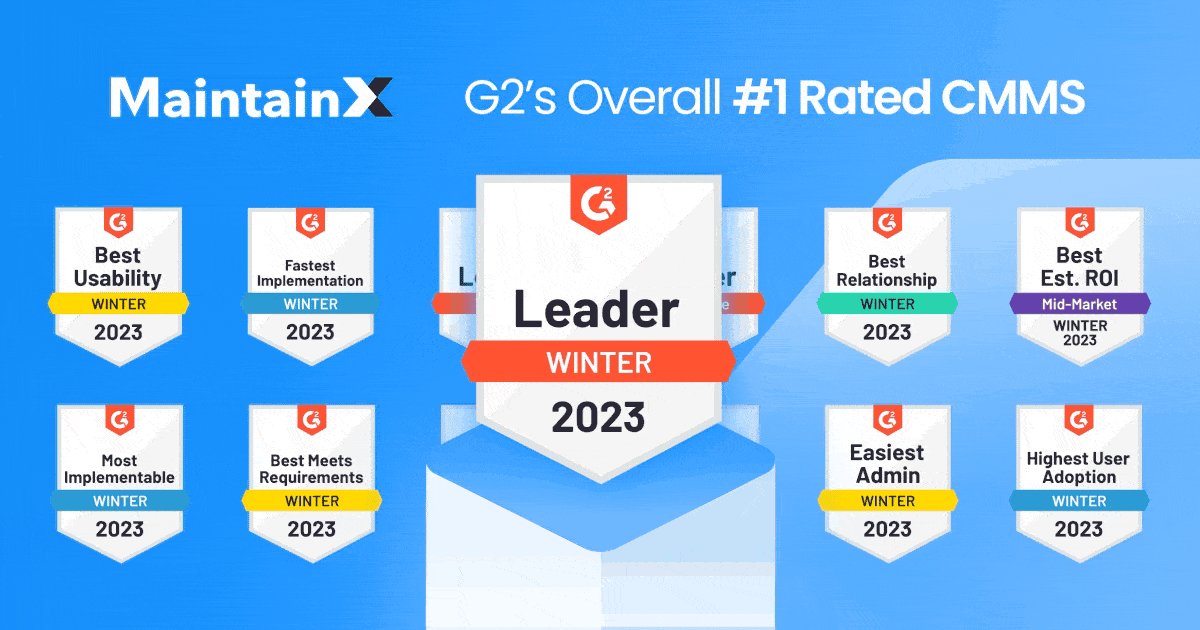
MaintainX: A Cloud-Based CMMS to Support Your Digital Augmentation Efforts
Digital augmentation can improve all aspects of a business. It facilitates real-time upskilling, improves human performance, speeds up onboarding, monitors the supply chain, and much more. However, much of digital augmentation capabilities rely on data. You need to organize and store data over a cloud-based platform, so it’s always readily available.
That’s where a CMMS like MaintainX helps. MaintainX can store essential data in a secure cloud environment. The app also has built-in automation features, which in turn, allow you to automate maintenance tasks.
For frictionless maintenance, you can create work orders, step-by-step workflows, and ready-to-use checklists on MaintainX. When technicians have questions or need additional instructions, they can request help with the built-in chat feature using their smartphone.
If that sounds interesting, add MaintainX to your digital augmentation toolkit today.
FAQs
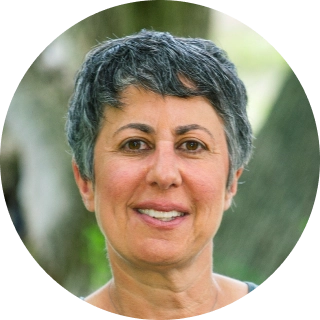
Caroline Eisner is a writer and editor with experience across the profit and nonprofit sectors, government, education, and financial organizations. She has held leadership positions in K16 institutions and has led large-scale digital projects, interactive websites, and a business writing consultancy.