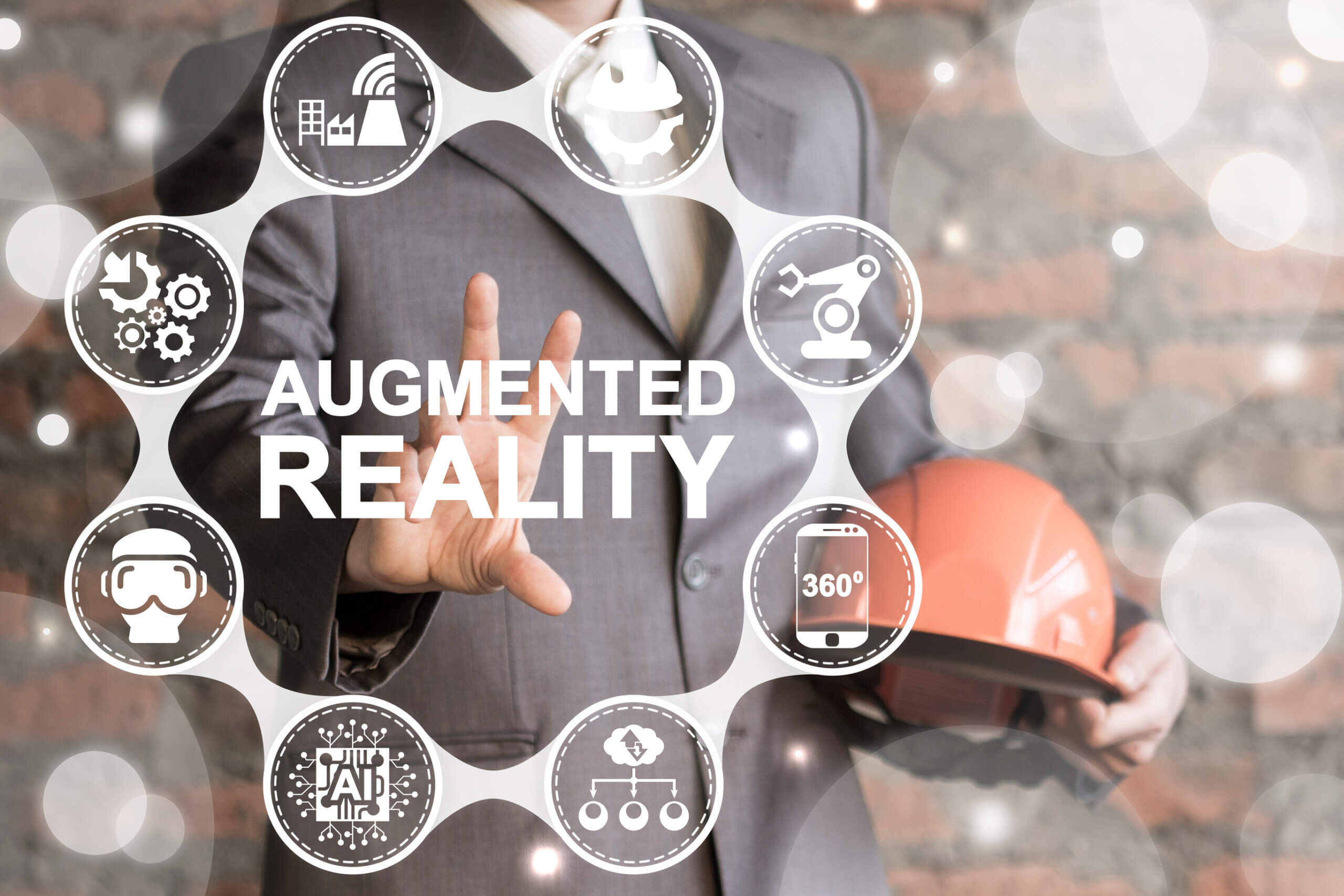
You’ve probably heard about augmented reality in terms of video games and trends. And if you have, no one would blame you for wondering what any of that has to do with maintenance or the manufacturing industry.
Well, we’ll get to that in a second. First, though, let’s be clear on what exactly augmented reality is.
What Is Augmented Reality?
As the name suggests, it refers to an augmented or enhanced experience of reality. In practice, this means superimposing content over what you see in the real world.
If you think that sounds like headphones for eyes, you’re not too far from the truth. It’s similar to virtual reality. Except where virtual reality is about engaging with things that aren’t there, augmented reality combines things that exist with things that don’t.
With an augmented reality (AR) device (which could be anything from a mobile phone to a headset), you can see, for example, computer-generated animals (or Pokemon) in your living room. The content can also span multiple senses, which means not just seeing but, in some cases, hearing and feeling things that aren’t there. AR combines three essential features:
- A combination of real and virtual worlds
- Real-time interaction
- Accurate 3D registration of virtual and real objects
“Immersive technologies, namely virtual and augmented reality, will fundamentally alter how we interact with content.”
McKinsey
What Does AR Have to Do with Maintenance?
As stated already, AR provides an enriched and immersive experience of perceptions. This means, for example, whether in manufacturing or maintenance, workers can have greater engagement with resources. For example: imagine you need to fix a part. Ordinarily, you would need to look through a manual or rely on someone to give you directions.
However, what if you put on a headset that provides detailed and automated work instructions to guide your activities? Let’s look a little more at the potential use cases of AR technology in maintenance and manufacturing processes.
AR Guiding Maintenance Activities
A fundamental benefit of augmented reality is that it enables people to engage with data. Instead of displaying simple data or information about certain things, you can engage with the data as immersive sensations. AR allows for data engagement in manufacturing by superimposing digital information onto physical objects and environments in real time. For example, AR can display contextual real-time data and information on production processes, machinery performance, and inventory levels. This, in turn, enables workers to make informed decisions about performing maintenance and troubleshooting tasks.
When it comes to maintenance, every company or team will have its own SOPs and procedures for specific assets. In addition, you’ll need manuals, instructions, and institutional knowledge of your team’s specific modes of operation. You might already have transitioned from paper to digital using a CMMS, but AR can take things a step further.
Consider a technician wearing the Microsoft HoloLens, or any other set of smart glasses that can overlay his real vision with preset imagery. He points the camera at a device, and instructions appear on the screen, providing step-by-step guidance.
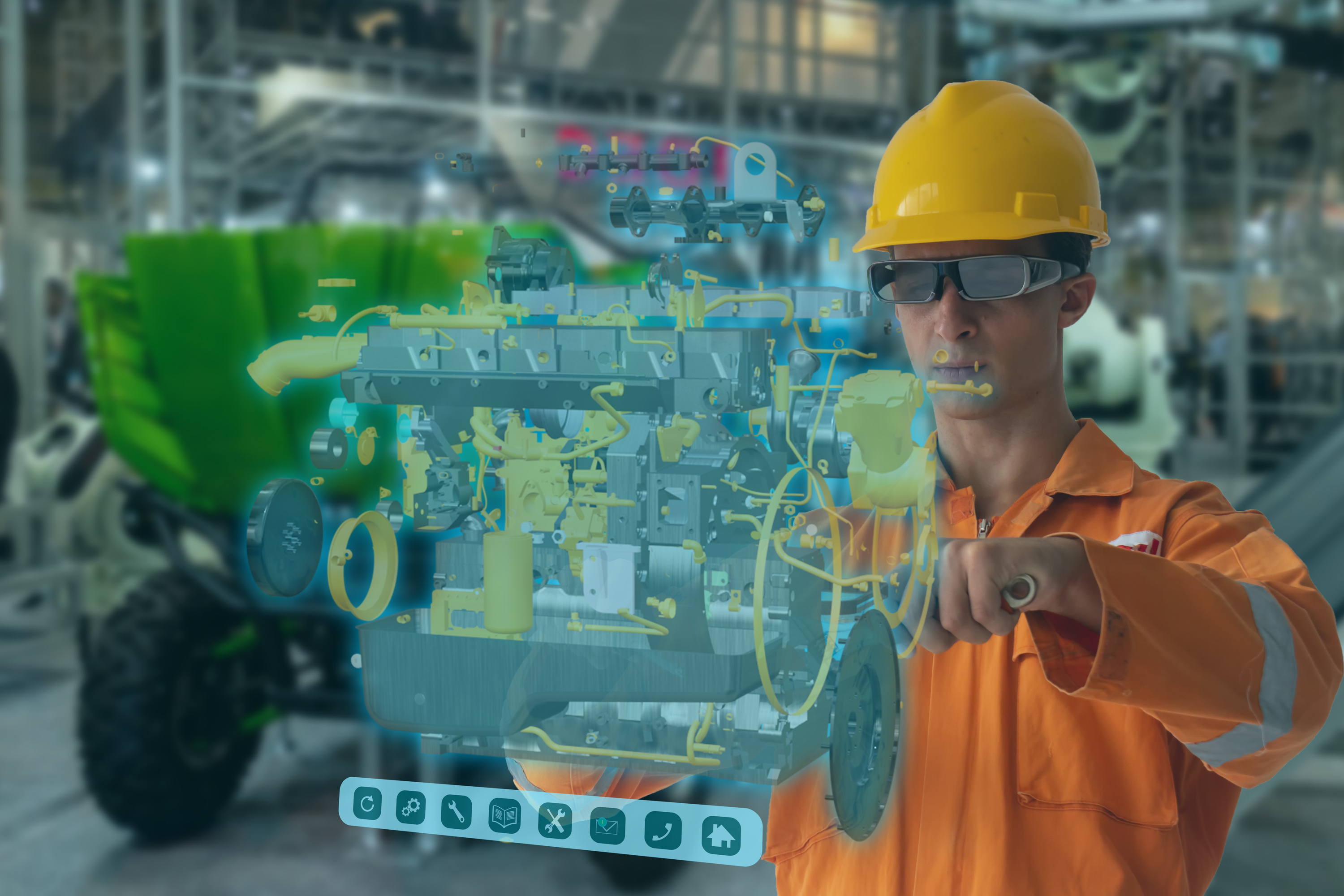
AR Facilitating Remote Collaboration
Similar to the first point, AR can facilitate remote collaboration between technicians in different places. This can be in synchronous (working simultaneously) and asynchronous (working at different times) ways.
Consider the case of manufacturing companies that need quick assistance from far-away technicians. Technicians in one place could use AR to collaborate with technicians in different locations, allowing for a smoother and more direct flow of information. As with other examples, you can do this with hands-free, wearable AR systems like AR glasses or headsets.
AR Optimizing Product Development
Another application of AR in a manufacturing environment is product design. Once designs for a new product are created, they can be made available to workers via AR systems.
Workers at different stages of the production line thus will have easy instructions to follow, with step-by-step guidance. Again, the automotive industry offers a good example. With all the various car models, workers need to adapt quickly on the factory floor. AR instructions can help make the assembly seamless.
AR Ensuring Quality Control
Augmented reality can play a crucial role in ensuring quality control and assurance in manufacturing by providing real-time data and visual guidance to workers during the production process.
AR can display digital instructions, specifications, and guidelines for product inspection directly on the product, thereby reducing the chances of human error and ensuring consistent quality across products.
Likewise, AR can highlight and correct deviations from specified standards in real time, improving the accuracy of the production process.
In addition, AR can visualize the production process in 3D, making it easier for workers to understand the process flow, detect potential quality issues, and make necessary adjustments.
“Across domains, augmented reality … is changing how products and services are developed and delivered, which is transforming into increased productivity and operational efficiencies.”
Deloitte
Benefits of AR in Manufacturing
So now we know some of the applications of AR. But how can they transform your operations for the better? Let’s first look at some of the benefits of augmented reality.
AR Saves Time and Effort
AR solutions can help optimize your manufacturing and maintenance processes. For one, technicians will spend less time referring to manuals for information that AR can feed them in real time. This will result in faster problem diagnosis, analysis, and maintenance repairs.
AR Improves Your Bottom Line
Augmented reality technology can help reduce downtime. For example, AR tech can facilitate remote collaboration outside simulations to guide processes. As a result, workers on the shop floor can collaborate with workers in other locations for quicker repairs. This will speed up repairs onsite and allows workers to focus on production.
AR Improves Consistency
With standardized processes that everyone can follow, you’re more likely to see consistent outcomes. Augmented reality can increase consistency in manufacturing by providing real-time information and guidance to workers on the factory floor. Workers can access information such as assembly instructions, product specifications, and technical drawings directly in their field of view without leaving their workstations or referring to separate manuals. This can reduce the risk of human error and increase the consistency of the manufacturing process.
Also, AR can provide workers with real-time feedback on their performance, making it easier for them to identify and correct mistakes before they become more significant problems. This can help ensure products are manufactured to specifications, reducing the risk of quality issues.
AR Reduces Reliance on Individual Workers
Having certain workers on the factory floor with more expertise than others is expected. However, this can be problematic for teams that depend on the same workers in all cases. AR can help reduce reliance on specific workers by providing detailed and easy-to-follow guides that anybody can use. You’ll have a much stronger team when more people are empowered to take action. Furthermore, AR can help train new workers by guiding them through a manufacturing or maintenance process step-by-step to help ensure they perform their tasks correctly and consistently from the start.
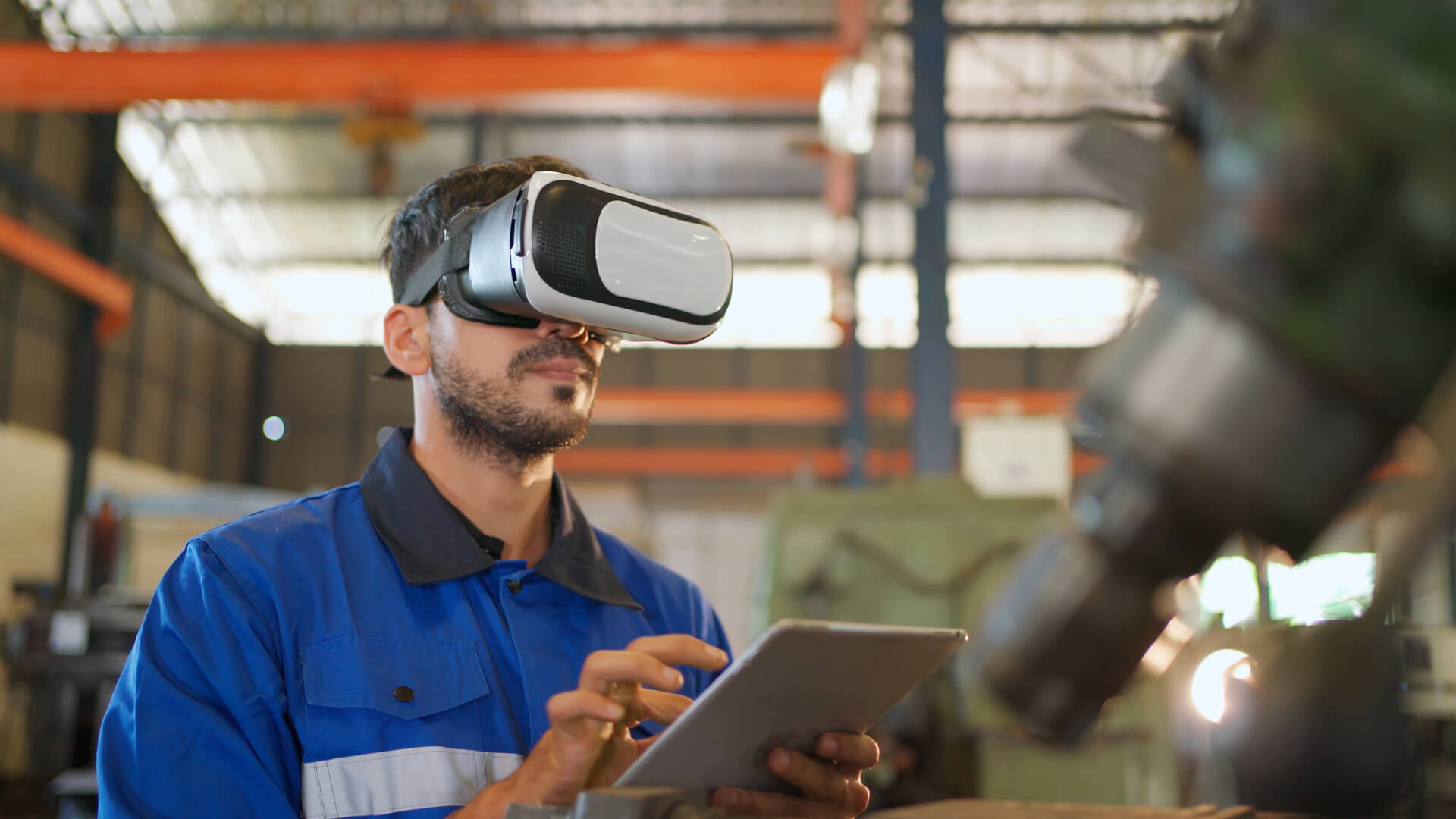
Challenges of AR in Manufacturing
- AR training is hard: Generally, new ideas can be challenging if your workers are used to one way of doing things. AR is no different. Getting workers who traditionally follow physical manuals to use AR guidance can involve steep learning curves. Given the time and costs involved, many decide the investment in upskilling isn’t worth it. However, augmented reality can be a source of just-in-time training. Workers get the skills as their work requires them.
- AR is not yet widely adopted: While the field is gaining traction daily, AR isn’t yet widely adopted in maintenance and manufacturing. The potential for product development is broad, and new products are being developed regularly.
Augmented Reality and CMMS
Speed, easy collaboration, and reduced downtime are the main benefits of augmented reality in manufacturing. Despite the existing challenges to augmented reality, you can reap many of these benefits by using a CMMS.
MaintainX is a computerized maintenance management software that can help streamline your workflow operations and facilitate team collaboration. And if you do want to enable augmented reality in your company, MaintainX has many features that will make that run smoothly, such as:
- Automated Work Orders
- In-app instant messaging
- Real-time asset and parts inventories
- Digitized SOP and Global Procedure Library
- Video and picture sharing
- Mobile app functionality, with unprecedented connectivity from your mobile device
FAQs
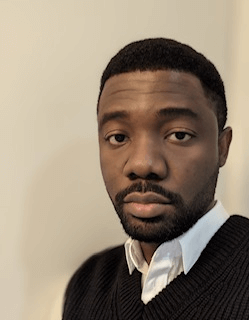
Lekan Olanrewaju is a content writer with years of experience in media and content creation. He has held positions at various media organizations, working with and leading teams at print magazines, digital publications, and television productions.