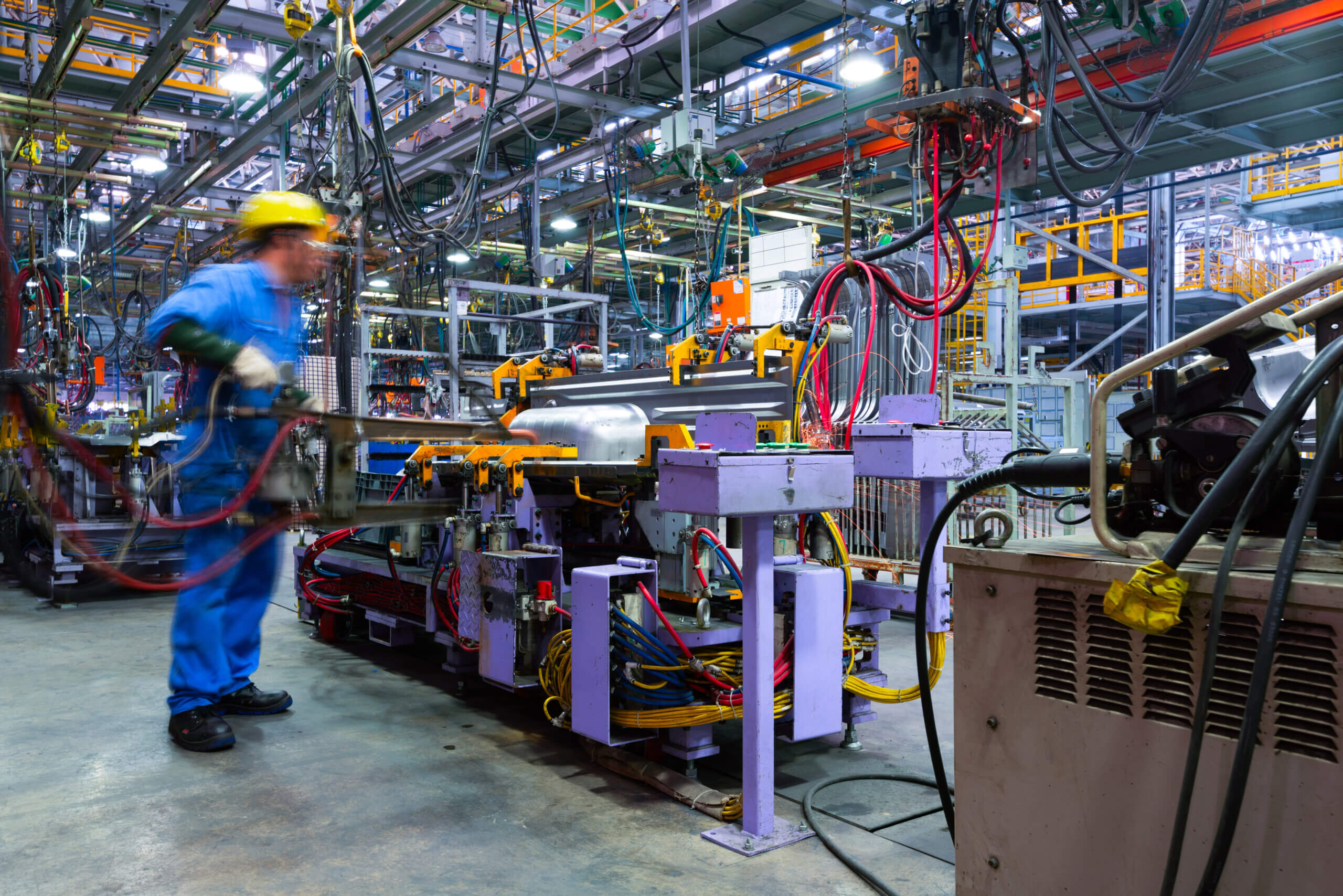
How to Improve Your Assembly Line Management
An assembly line is a manufacturing system that involves moving a product from one stage to another, where parts are added in sequence until the final product is completed.
We can trace the history of the assembly line back to the Industrial Revolution when the production of goods in motorized or automated lines first became popular.
However, perhaps the most famous use of the method is the Ford Motor Company in the 1910s. At the time, Henry Ford was looking to optimize the assembly process of his cars. He noticed the use of conveyor belts in meatpacking plants and slaughterhouses. As a result, he applied similar production methods to automobile manufacturing.
Instead of workers moving from station to station to assemble cars, this approach meant the product would move down the line to the workers who remained at their own stations. Ford’s assembly line launched in 1913 in his Highland Park, Illinois, automobile assembly plant. This automation sped up the mass production of cars such that the Model T was now built in only 90 minutes.
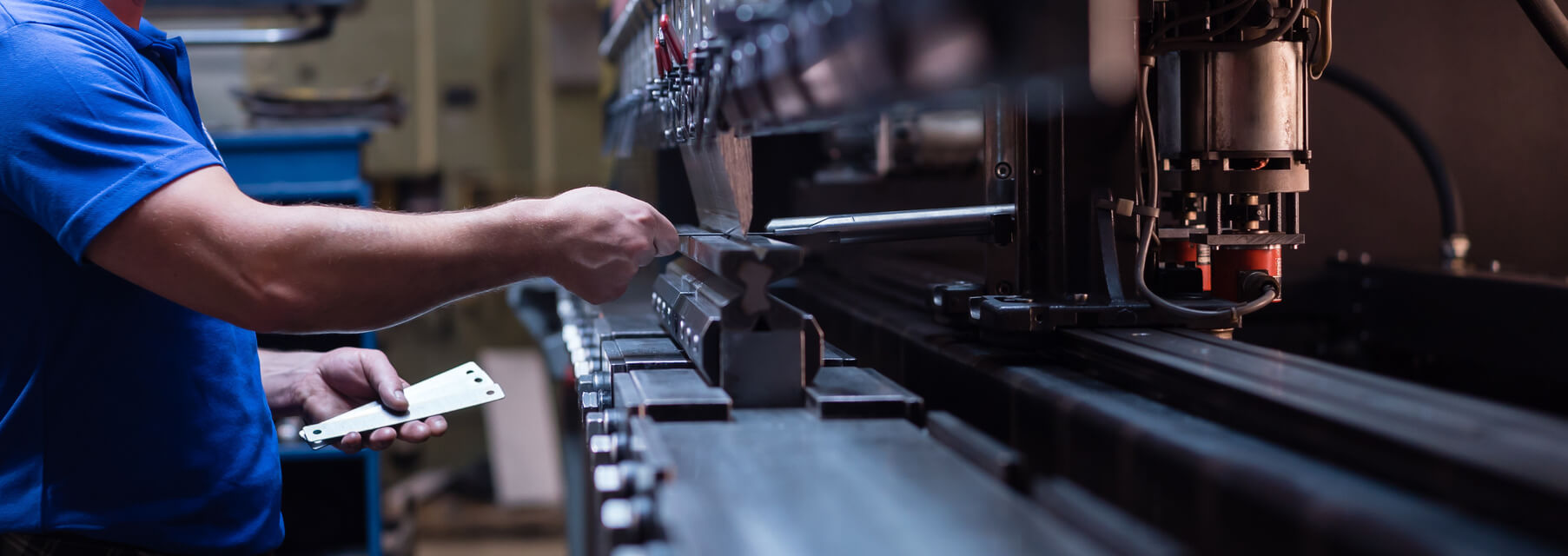
Benefits of the Assembly Line Approach
The assembly line manufacturing process has challenges. Standing in one position can become monotonous and stressful to workers. Also, workers must adhere to strict timelines for an assembly line to work properly. However, there are significant benefits to this approach.
Increasing Income
This is always a good one. Whatever your industry, you’ve likely got one eye on the bottom line at all times. An automated assembly line can boost this in multiple ways.
First, an assembly line speeds up production times, leading to increases in output and, eventually, revenues. Add this to the fact that costs tend to be reduced with this approach. You’re looking at good progress on the financial side.
Improving Staff Specialization
The assembly line method encourages staff to focus on one product or one part of a product. This allows staff to become proficient in specific tasks on the production line. By extension, specialization reduces the number of parts each assembly line worker needs to learn about. Thus, improving the quality of staff output in their focus area.
Increasing Product Complexity
If product assembly requires staff to learn various complicated parts and processes, there is a limit to how complex the overall assembly line can be. At the end of the day, people can only learn so much.
However, the assembly line process means each stage is reduced to simple processes that individual staff can handle with fewer challenges. This means that more detailed assembly can be embarked on, as one person isn’t tasked with handling all the complex parts.
Improving Working Conditions
Because the moving assembly line transports products and parts to workers instead of the other way around, there is a reduced need for workers to move around. Workers also have to do significantly less lifting of heavy parts and machinery. This can translate to a reduced risk of injury.
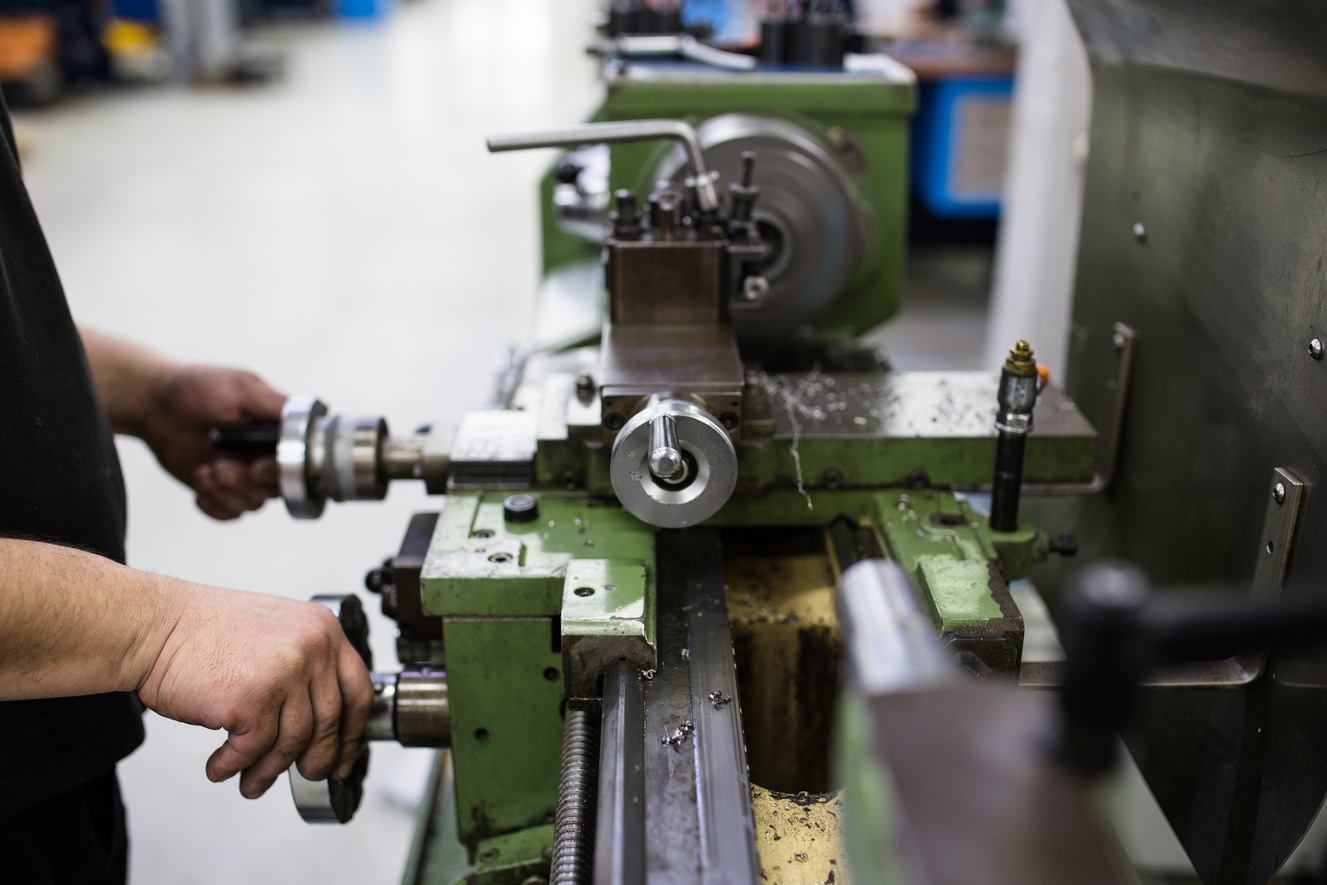
How to Optimize Your Assembly Lines
Designing a functional assembly line involves a mathematical challenge known as an assembly line balancing problem. The approach involves figuring out what tasks to assign to what stations and what amount of time to allocate for each task. It also involves taking into account production schedules, inventory levels, and the state of the supply chain.
Given how much of a balancing act this can be, the last thing you want is for your systems not to run smoothly.
To keep your assembly lines running at optimum efficiency, effectiveness, and productivity, you’ll need to put in place a robust assembly line management program. The particular approach you take will, of course, depend on the specifics of your business. That said, here are a few steps that can help any business:
Develop a Preventive Maintenance Strategy
The thing about assembly lines is, while they eliminate a lot of the extra work that staff might be doing, they do so by transferring that work to automated systems. As a result, wear and tear on equipment is inevitable. This means, no matter what, you will be doing some amount of reactive maintenance.
However, you can keep this to a minimum by embracing preventive maintenance.
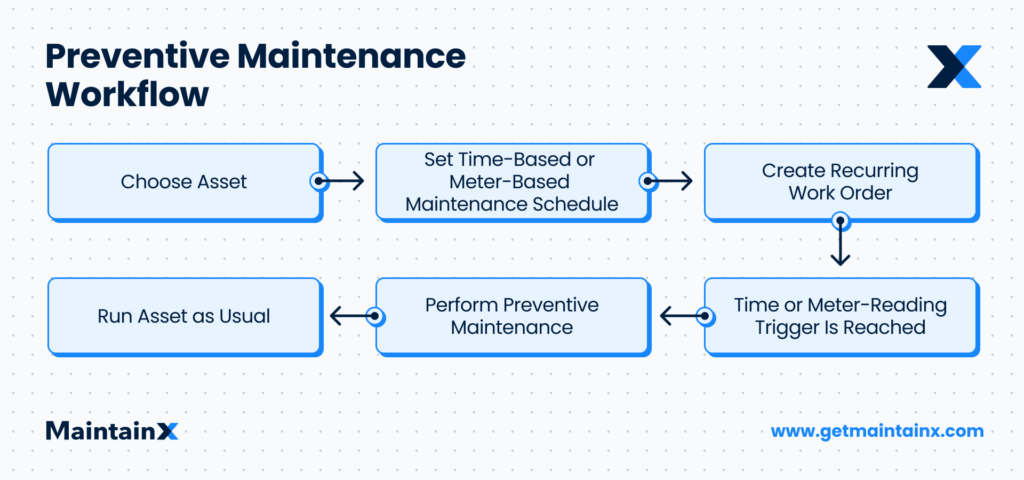
Adopting a proactive strategy allows you to handle equipment problems before they happen. In addition, you can adopt a strategy that allows you to predict when issues may arise and prepare for them accordingly.
Track Your Maintenance KPIs
Following a more proactive maintenance approach, you will likely want to keep a good eye on specific metrics and KPIs. These metrics will likely be unique to your own business but may include Mean Time to Repair (MTTR), Mean Time Between Failure (MTBF), and Overall Equipment Effectiveness (OEE).
Technological solutions and apps can offer crucial help here. For example, a good CMMS work order system helps your team record data and stay informed with real-time statistics about what KPIs to track, when, and how.
Develop Standard Operating Procedures
Standard operating procedures (SOPs) and digital work orders help ensure workers know exactly how to proceed when the time comes for preventive maintenance. In addition, a robust CMMS helps keep employees updated on company standards regarding asset maintenance and when pieces of equipment fall short.
Even in the event of a breakdown, reactive maintenance is more efficient with set steps and processes in place regarding how to proceed, saving time that might’ve been spent figuring out what to do from scratch.
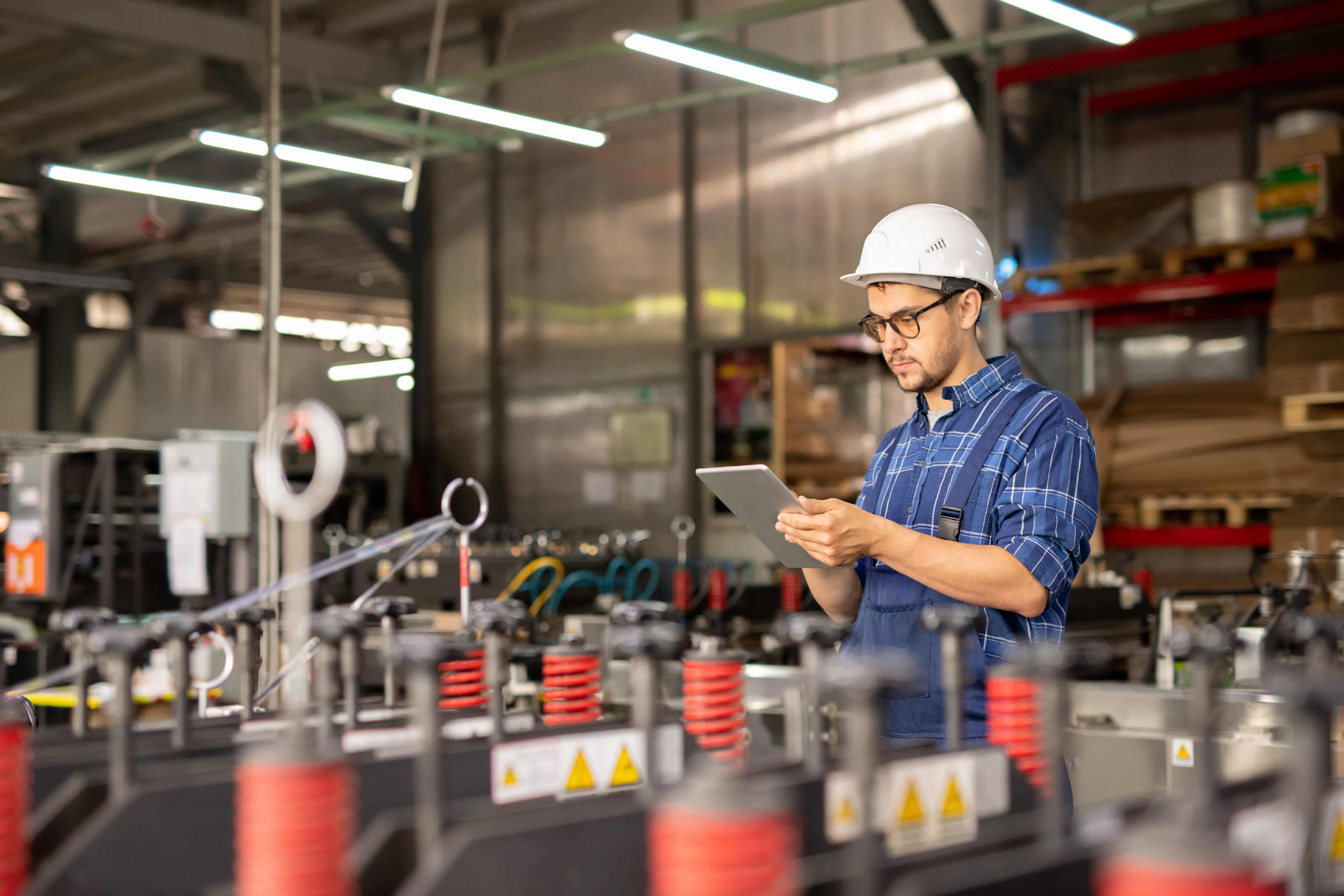
Use MaintainX to Manage Your Assembly Line Maintenance
Just imagine how already efficient Ford would've been years ago if there was a CMMS Ford could've used when it was streamlining assembly lines!
MaintainX is much more than a Computerized Maintenance Management Software s(CMMS). With functionalities including digital work orders and reporting, data management, and instant messaging, MaintainX streamlines maintenance management by helping you automate your processes and track your progress in real-time. In addition, the mobile-friendly software gives you everything you need to run effective assembly line operations.
Book a tour to learn more about how MaintainX can help.
FAQs
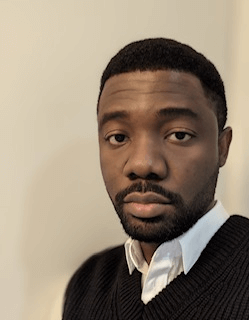
Lekan Olanrewaju is a content writer with years of experience in media and content creation. He has held positions at various media organizations, working with and leading teams at print magazines, digital publications, and television productions.