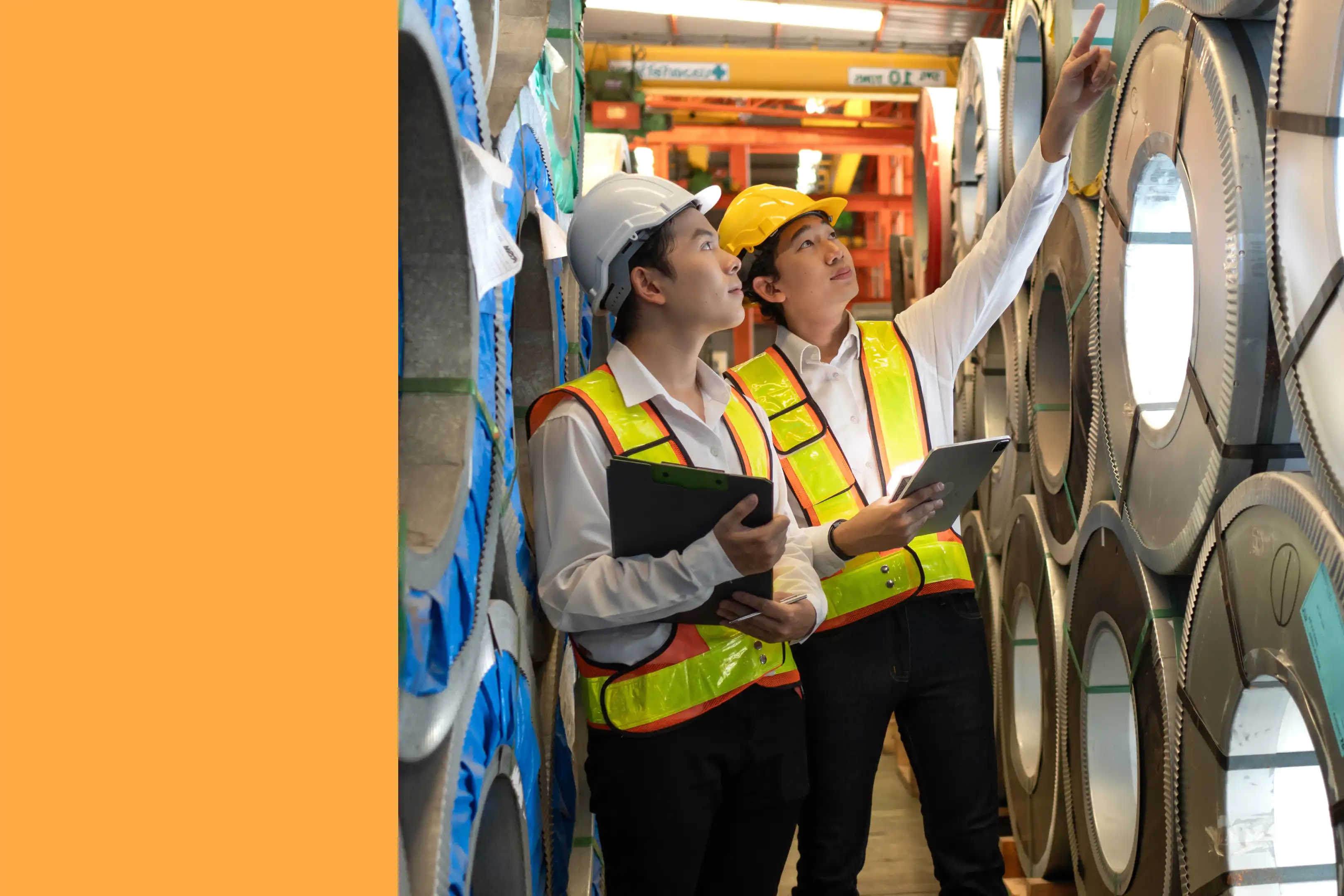
Standard operating procedures form the backbone of successful business operations across every industry. Whether you're managing a manufacturing facility, running a retail chain, or overseeing agricultural operations, SOPs create the consistency and efficiency that separate thriving organizations from those that struggle with quality control and regulatory compliance.
Key takeaways
- SOPs reduce errors by providing step-by-step instructions for routine tasks, ensuring consistent quality across all business operations.
- Effective SOPs save money by improving efficiency, reducing training time, and minimizing costly mistakes.
- Written standard operating procedures protect against knowledge loss when experienced employees leave.
- SOP documentation ensures regulatory compliance and helps meet industry standards.
- Digital SOP software streamlines the process of creating, distributing, and monitoring procedures.
What are standard operating procedures?
Standard operating procedures (SOPs) provide detailed instructions that explain how to complete routine tasks and business processes. These documented procedures transform complex processes into clear, actionable steps that any employee can follow to achieve the desired outcome.
Key components of effective SOPs include:
- Clear instructions written in active voice
- Step-by-step breakdowns of each task
- Visual aids like flowcharts or checklists
- Safety standards and regulatory requirements
- Expected outcomes and quality standards
SOPs act as a single source of truth for how work gets done in your organization. They eliminate guesswork and ensure that whether it's a new hire's first day or a veteran employee's thousandth time completing a task, the results remain consistent.
Why are SOPs important?
Clearly written standard operating procedures are essential because they eliminate uncertainty about how to best complete assignments. Put simply, anyone within your organization should be able to produce a standardized outcome for any routine task by simply following the set of instructions.
Without SOPs, businesses face increased errors, compliance failures, and inefficient use of resources. The importance of SOPs becomes even clearer when organizations with well-documented procedures experience significant improvements in operational efficiency, reduced downtime, and better resource utilization.
What types of businesses use SOPs?
Industries that commonly use SOPs include:
Manufacturing
SOPs help manufacturers comply with local, state, and federal regulations while meeting rigorous quality control, production, and safety standards. Following prescribed procedures reduces costly downtime and keeps production lines running efficiently.
Warehousing
Warehouse managers need fast and accurate shipment lines for proper inventory control and supply chain management. Every team member must follow best practices through SOPs to achieve reliable outcomes. Consistent procedures during routine activities drive speedy delivery times, customer satisfaction, and strong brand reputations.
Restaurants
When you watch someone prepare your food at a restaurant, you're witnessing food safety SOPs in action. Front- and back-of-house employees follow strict safety procedures when handling food to prevent foodborne illnesses. Restaurant SOPs also guide menu production, food preparation flow, team communication, and equipment sanitization.
Hotels
Hotels use written procedures to deliver dependable, comfortable, and high-quality guest experiences. Maintenance technicians follow SOPs for preventive maintenance on HVAC systems, plumbing, lighting, lawns, and shared facilities. Guest services teams use standardized processes for bookings, check-ins, and check-outs.
Educational institutions
Educational institutions coordinate dozens of departments and facilities. Facility managers use SOPs to maintain buildings and student accommodations. From athletic facilities to parking garages, every building requires routine upkeep. School SOPs typically cover fleet management, sanitation, fire safety, and water systems.
Other industries using documented procedures include property management, utility companies, oil and gas, healthcare, municipalities, and fleet management. OSHA's General Duty Clause requires all industries to implement SOPs for worker safety.
While SOP content varies by industry, the development process remains similar. Today's organizations increasingly adopt digital SOP platforms like MaintainX CMMS to streamline their procedures.
What are the benefits of having detailed procedures for teams?
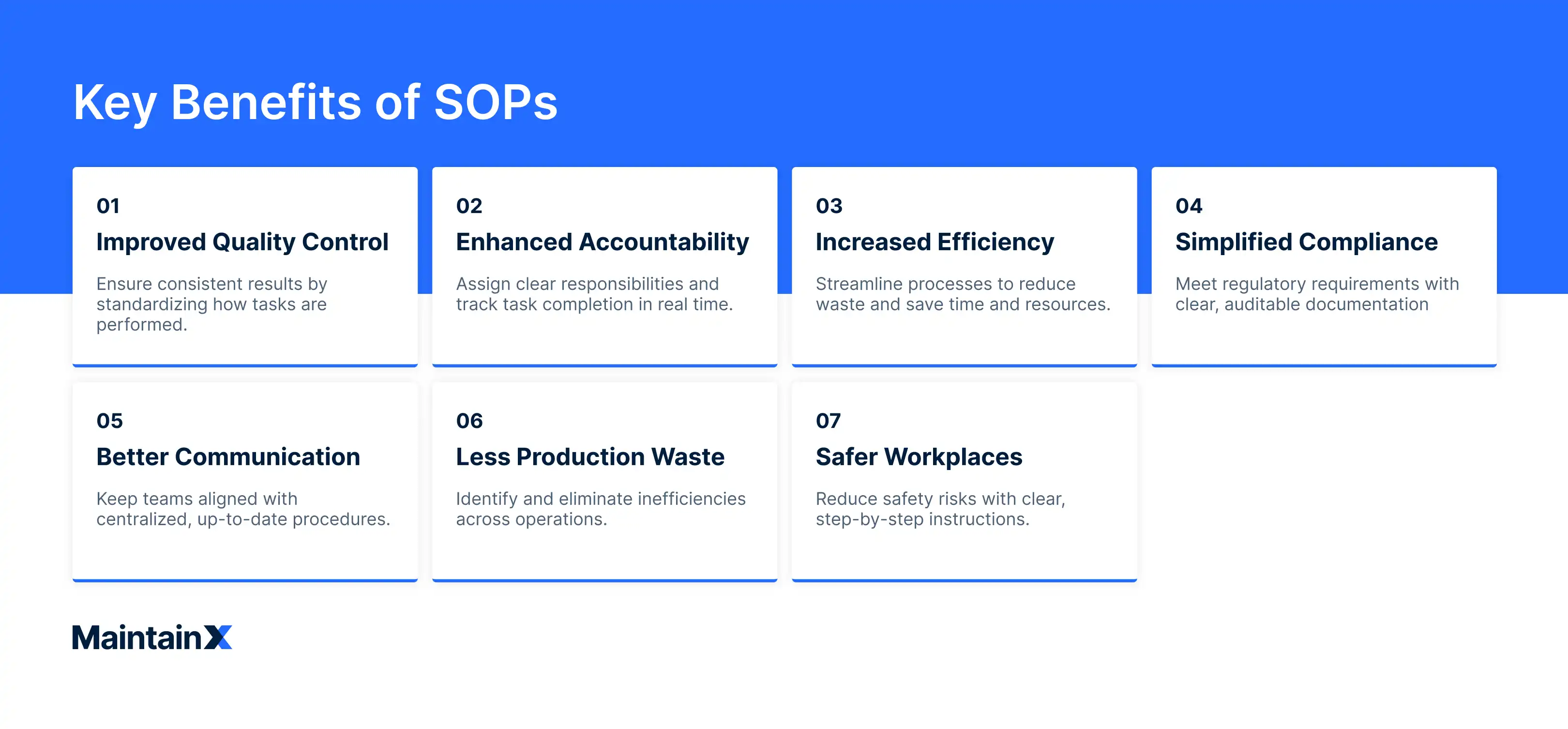
As previously mentioned, taking the time to write, assign, and manage standard operating procedures provides many benefits. Some of the most noteworthy benefits of standard operating procedures include:
1. Improved quality control
Wouldn’t it be amazing for every employee to “get it right the first time?” As the name suggests, SOPs establish standard methods for completing tasks as part of a unified quality management system. Standardization ensures that neither production nor performance is compromised when new hires come on board. Established protocols provide a baseline that ensures quality will never be compromised in the event of unforeseen circumstances, competing priorities, or employee shift changes.
Once you have foundational SOPs in place, you can begin to identify opportunities for greater efficiency. Every world-class operation begins with consistent quality control.
2. Enhanced accountability
Have you ever discovered an important task uncompleted upon arriving at work? Maybe your facility’s bathroom counters weren’t wiped down properly the night before. Sadly, when you ask who was responsible for the task, you see nothing but pointing fingers.
Digital SOP assignments provide an extra measure of accountability for business activities. SOP software facilitates employee training by allowing you to see when employees open and close assigned work orders in real time. SOP software automatically applies a digital time-stamp to task activity. Managers can even require uploaded photograph documentation and signatures for additional peace of mind.
3. Improved efficiency
What organization doesn’t want to improve efficiency? The more work you can accomplish with minimal effort, the more capital you have to spend in other areas. Additionally, inefficient workplace processes sometimes yield frustrated, unproductive employees.
Take the time to distill complex processes into streamlined steps, and you will likely eliminate several forms of waste. It’s not uncommon for even the tightest ships to uncover unnecessary steps that waste precious energy, time, and resources.
4. Simplified regulatory requirements
SOP software provides organizations with digital audit trails that they can use to improve quality assurance and regulatory compliance. Besides reinforcing critical safety and compliance standards among employees, cloud-based records can serve as a crucial defense in the event of an OSHA audit.
Essentially, would you rather spend hours digging through hefty filing cabinets for paper records or spend seconds generating an automated compliance report? Even the most minor OSHA violations start at $1,221 for each incurred penalty.
5. Streamlined communication
Another benefit particular to digital SOPs is streamlined team communication. MaintainX serves as a centralized communication platform with both individual and team messaging.
You can share important informational updates with your team in real time via desktop, smartphone, or tablet. The app’s work order commenting feature allows users to virtually eliminate the types of miscommunications that lead to incomplete work assignments. Our customers say it’s the software’s most surprisingly useful feature—hands down.
6. Reduced production waste
As briefly mentioned before, most organizations waste significantly more resources on poorly mapped procedures than they realize. Lean Six Sigma is an operational methodology that identifies eight primary types of waste you can eliminate for maximum efficiency, including:
- Transportation waste
- Inventory waste
- Excess motion
- Overproduction
- Manufacturing defects
- Wait time
- Underutilized skills
- Over-processing
SOPs can help identify types of waste so you can begin to eliminate or minimize them. Consistently monitor the implementation of your SOPs to get a handle on areas of improvement. Again, a CMMS like MaintainX makes monitoring O&M KPIs significantly easier.
With MaintainX, operational managers can instantly generate personalized reports on metrics such as mean time to repair (MTTR), planned maintenance percentage (PMP), and more.
7. Improved workplace safety
Finally, why are standard operating procedures important? They help keep team members safe! Workplace safety is paramount. Regardless of the industry, you are responsible as an employer to always provide a safe work environment for team members.
Hazardous electrical, chemical, or fall protection oversights can lead to accidents. Not only do such incidents unjustly harm workers, but they cost big bucks when OSHA gets involved.
Written SOPs that distill work processes into clear step-by-step instructions can streamline new employee onboarding, reduce errors, and support safe working conditions. Use SOPs to ensure all employees complete tasks without compromising their own safety or that of their staff members.
What do you risk with bad SOPs?
Poorly written or outdated SOPs can be worse than having no procedures at all. Bad SOPs create confusion, increase errors, and lead to non-compliance with industry regulations.
Common risks of ineffective SOPs include:
- Increased error rates: Vague or complex instructions leave too much room for interpretation, leading to mistakes.
- Employee frustration: Unclear procedures waste time and create stress for team members trying to complete tasks correctly.
- Compliance violations: Outdated SOPs may not reflect current regulatory requirements, exposing the organization to fines.
- Inconsistent results: When procedures lack detail, different employees produce different outcomes.
- Safety hazards: Incomplete safety procedures put workers at risk.
- Customer dissatisfaction: Inconsistent quality affects customer service and brand reputation.
- Higher costs: Errors, rework, and compliance issues all impact the bottom line.
How to write useful SOPs
Creating standard operating procedures requires careful planning and execution. Follow these key steps to develop SOPs that actually improve your business operations:
1: Identify key processes that need SOPs
Start by identifying areas where standardized procedures will have the most impact. Focus on:
- High-frequency routine operations
- Tasks with regulatory requirements
- Processes where errors have significant consequences
- Activities performed by multiple team members
- Complex processes requiring consistent execution
2: Gather input from the right team members
The best SOPs come from collaboration with the employees who actually perform the tasks. Their insights ensure that procedures reflect real-world conditions and identify areas for improvement.
3: Write clear, actionable procedures
Use simple language and active voice (write "inspect the equipment" instead of "the equipment should be inspected"). Break down each process into detailed steps that leave little room for misinterpretation. Include:
- Specific actions required
- Tools and materials needed
- Safety precautions
- Expected timeframes
- Quality checkpoints
4: Standardize the format and review process
Maintain a consistent SOP format across your organization. This makes it easier for employees to follow any procedure, regardless of department. Establish a review process to ensure accuracy before implementation—for example, have the procedure tested by someone unfamiliar with the task, reviewed by a subject matter expert for technical accuracy, and approved by a manager who can verify that it meets safety and compliance requirements.
5: Distribute, train, and monitor usage
Implementing standard operating procedures requires more than just writing them. Ensure easy access through digital SOP software, provide consistent training for all team members, and monitor compliance through regular audits.
6: Review and update SOPs regularly
Business processes evolve, and your SOPs must keep pace. Schedule regular reviews to ensure procedures remain current with industry standards and regulatory requirements.
SOPs are a pillar of operational excellence
Standard operating procedures represent more than just written instructions—they embody an organization's commitment to quality, safety, and continuous improvement. By investing in comprehensive SOP documentation and using modern SOP software for distribution and monitoring, businesses create a culture of consistency that drives operational excellence.
The right tools make all the difference in managing SOPs effectively. Digital platforms like MaintainX transform static documents into dynamic, accessible procedures that teams actually use. With features for real-time updates, mobile access, and compliance tracking, modern CMMS software ensures your SOPs work as hard as your team does.
FAQs
What are the 5 main benefits of an SOP manual?
The five main benefits of a comprehensive SOP manual are:
- Consistent quality control across all operations and locations
- Reduced training time for new employees through clear, documented procedures
- Regulatory compliance with industry and safety standards
- Knowledge preservation that protects against employee turnover
- Cost savings through improved efficiency and fewer errors
How often should SOPs be reviewed?
SOPs should be reviewed at least annually, but certain factors may require more frequent updates:
- After any regulatory changes in your industry
- When new equipment or technology is introduced
- Following any safety incident or near-miss
- When employee feedback indicates confusion or inefficiency
- During major organizational changes or expansions
What is the most important reason for following an SOP?
While all benefits matter, ensuring consistent quality and safety stands as the most critical reason for following SOPs. Standardized procedures protect both employees and customers by establishing clear expectations and reducing the risk of errors that could lead to injuries, product defects, or service failures. This consistency builds trust with customers and creates a safer, more predictable work environment for all team members.
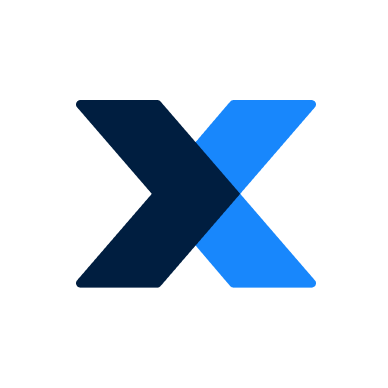
The MaintainX team is made up of maintenance and manufacturing experts. They’re here to share industry knowledge, explain product features, and help workers get more done with MaintainX!