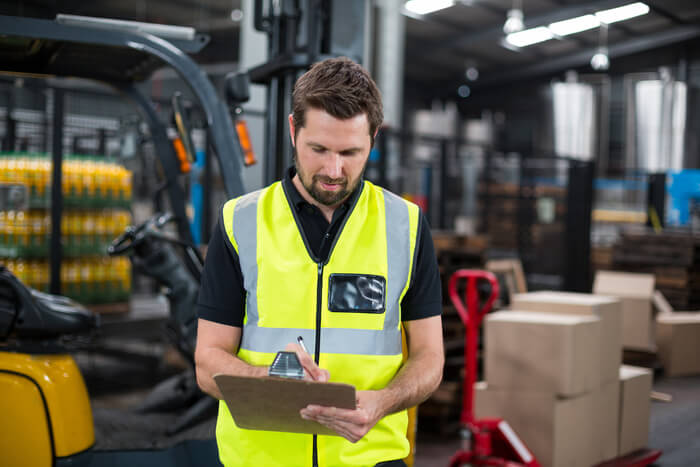
The best way to foster employee autonomy, and ensure consistent results, is to develop standard operating procedures (SOPs). These documented, step-by-step instructions for performing given tasks provide employees with everything they need to efficiently perform assignments without confusion, misinterpretation, or reinventing the proverbial wheel.
Being a manager isn’t easy. You must train new hires, create work schedules, and oversee competing priorities—all while routinely being interrupted with unexpected problems to solve. This is why smart managers train employees to execute essential tasks as well as they could themselves! It’s not enough to simply give orders and walk away. Managers must think through how to explain routine tasks that may or may not seem obvious to them. Furthermore, they must equip workers with the tools needed to get the job done.
As a result, this article will answer the question: what are the advantages of using standard operating procedures? We’ll summarize the biggest benefits of implementing SOPs and how to begin.
What Are the Advantages of Using Standard Operating Procedures?
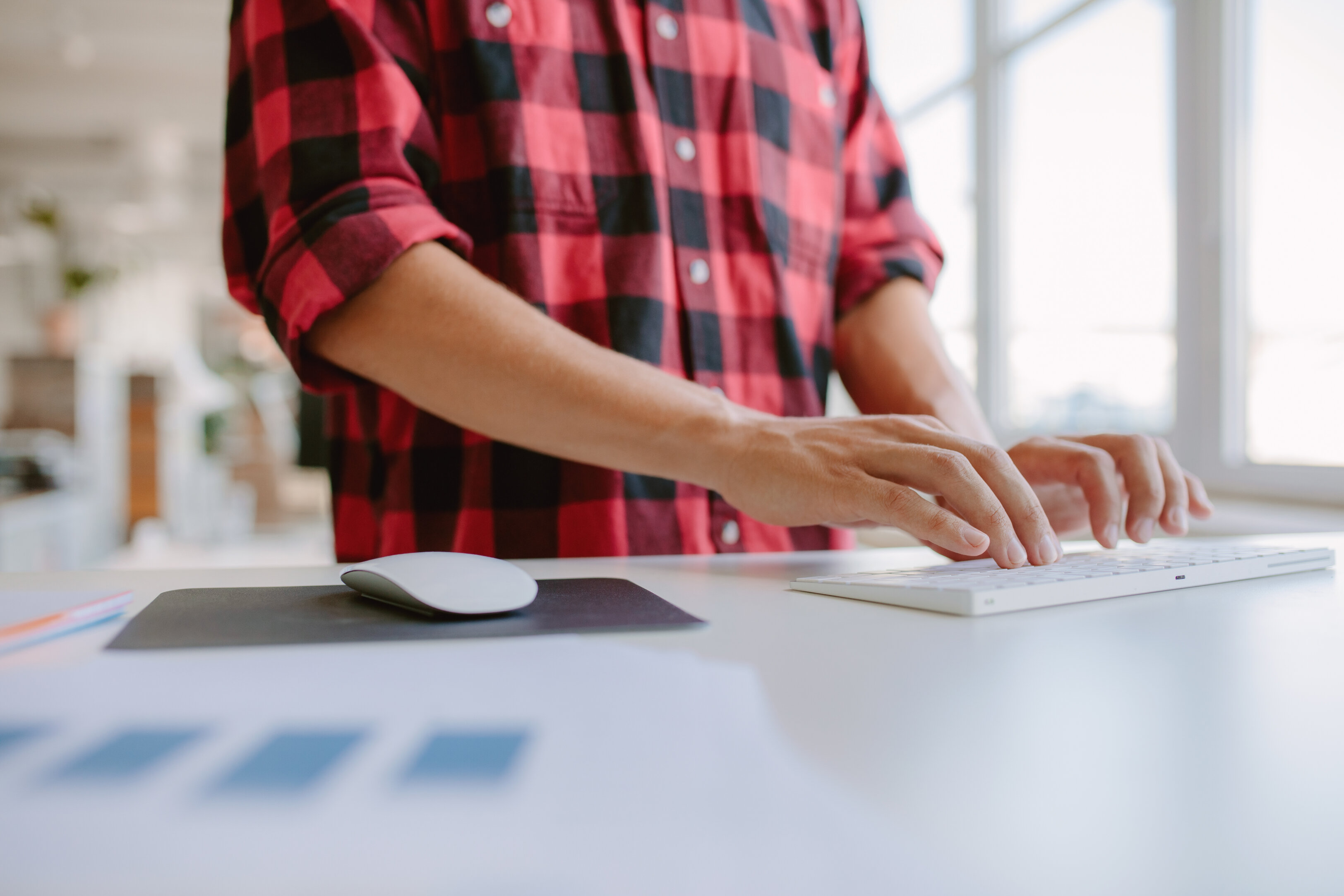
Standard operating procedures (SOPs) establish a consistent way to perform given processes to achieve the desired output. While providing employees with documented procedures won’t guarantee positive employee performance, it will go a long way to creating a culture of routine reliability, quality control, and stakeholder safety.
Regardless of organizational size or type, every operational manager should implement SOPS to:
1. Achieve Consistency
Even simple processes are susceptible to various interpretations. One fun aspect of working with different personalities is discovering how many different ways there are to approach tasks. While innovation is essential to remain competitive in today’s workforce, standardization is crucial to maintaining consistent results.
Providing employees with detailed, standardized instructions on how to perform repeating tasks ensures predictable outcomes. Whether baking bread or manufacturing automobiles, managers must identify the best possible way to approach each routine task for consistent results.
2. Improve Quality Assurance and Safety
Of course, the result of consistent task execution is often quality assurance. Well-written SOPs enable workers to clearly understand the expected results for each stage of any given task. Paying attention to detail during the production process is crucial to making high-quality finished products.
Not only is meeting quality standards essential to maintaining customer satisfaction, but it’s also crucial for safety. According to Plant Engineering’s Facility Maintenance Report, 12 percent of unplanned downtime is the result of operator error. Step-by-step instructions reduce the likelihood of human errors that results in equipment downtime, safety hazards, and subpar results.
Since “quality” is often objective, businesses are encouraged to rely on third-party industry standards. The International Organization for Standardization publishes documented standards like ISO 9001, ISO 14001, and ISO 27001 for multiple industries.
3. Save Time and Money
Another advantage of using standard operating procedures is profitability. Trimming the fat off frequently executed tasks can drastically improve productivity and optimize costs.
In lieu of SOPs, each employee may choose to approach a task in a different manner. While most workers probably complete their duties fairly efficiently, some may waste time, effort, and resources on unnecessary steps.
The best way to begin this process is by using SOPs to remove the most costly eight types of waste—defects, overproduction, waiting, not utilizing talent, transportation, inventory excess, motion waste, and excess processing.
4. Simplify Employee Management
SOPs are important as they can serve as a framework for measuring employee performance. When employees know exactly what’s expected of them, evaluating performance and providing feedback for improvement becomes much easier.
Additionally, well-structured SOPs streamline the onboarding process for new hires. Instead of repeatedly recalling how to complete assigned tasks and what important details must be covered, managers can require new workers to study SOPs as part of their training. Again, documented processes save time all around!
5. Avoid Knowledge Loss
According to the Society for Human Resource Management, the average company experiences an annual 18 percent turnover rate. Managers risk jeopardizing crucial production processes if key employees leave without passing on their knowledge to replacement hires.
Digital SOPs, in particular, ensure organizational knowledge is documented, accessible, and secure. Storing essential work instructions on data-encrypted servers in the cloud is more efficient than saving important SOPs in binders and filing cabinets. Additionally, standard operating procedure software makes it easier for team members to edit processes as assets and processes change.
6. Simplify Audits
Lastly, SOPs provide clear mechanisms for performing internal audits on company procedures. In addition to writing technical SOPs—that cover how to perform tasks—businesses can also write management SOPs.
Among other things, the latter provides guidelines for developing, reviewing, and updating existing SOPs. Diligent review processes enable managers to consistently identify areas to improve. Additionally, digital audit trails provide peace of mind should a regulatory agency ever require proof of compliance with industry standards.
7. Enhance Autonomy
Finally, a less frequently discussed advantage of using standard operating procedures can be increased feelings of autonomy. Organizations that make SOP checklists accessible via mobile applications empower employees to make good decisions without having to ask managers for reassurance all of the time.
According to a University of Birmingham study, higher levels of autonomy translate to greater job satisfaction and well-being. The researchers analyzed 2 years’ worth of data concerning 20,000 employees to evaluate the effects of workplace autonomy.
Streamline SOPs with MaintainX
We hope you’ve enjoyed learning about the advantages of using standard operating procedures. If you want to run smooth operations, you must provide workers with clear, organized, and accessible written instructions. As discussed, the return on investment (ROI) can be massive!
With that said, the process of documenting dozens, if not hundreds, of procedures can feel overwhelming. But it doesn’t have to be tedious if you consider adapting one of the many CMMS systems. MaintainX offers:
- Free templates available for download (we’ve got hundreds)
- Cloud-based checklists for editing on the fly
- Digital dashboards with key performance indicators
- Recurring work order automation for preventive maintenance
- Team messaging that keeps everyone on the same page
Read more about the benefits of digital SOPs and how to automate your business processes here.
FAQs
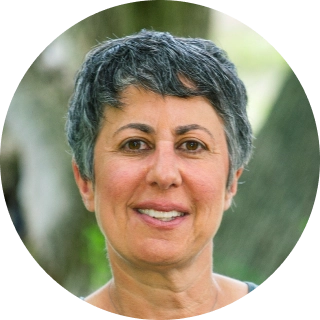
Caroline Eisner is a writer and editor with experience across the profit and nonprofit sectors, government, education, and financial organizations. She has held leadership positions in K16 institutions and has led large-scale digital projects, interactive websites, and a business writing consultancy.