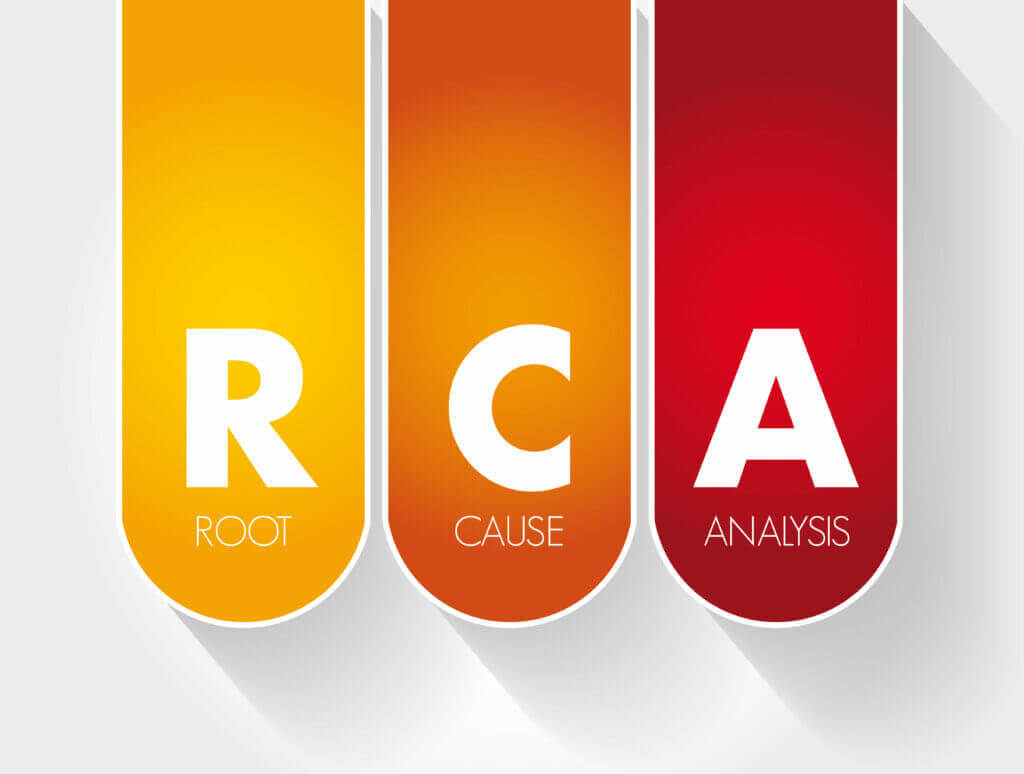
Root Cause Analysis (RCA) is your secret weapon for taking care of mysterious equipment malfunctions once and for all. If you want to treat the illness and not the symptoms, RCA is precisely what you need. It’s a structured problem-solving method to help you identify, understand, and solve the deeper causes of frequent unplanned downtimes for your most critical assets.
Root Cause Analysis Tools in Maintenance
Picture this: you’re running a routine inspection when you notice a malfunctioning centrifugal pump. You quickly assign a work request to one of your maintenance guys to fix it. Fast forward several weeks and the same pump is acting up again! So, you issue yet another emergency maintenance request. At this point, you’re getting worried. We’ve all been there: working in firefighting mode stinks! In the maintenance world, this is where root cause analysis (RCA) tools come into play.
You don’t want to spend the rest of your life reacting to a machine that should be working perfectly fine. In addition, you don’t want to blow your department’s budget prematurely.
This article explores root cause analysis, its benefits, and the most popular RCA tools used by industrial maintenance managers today.
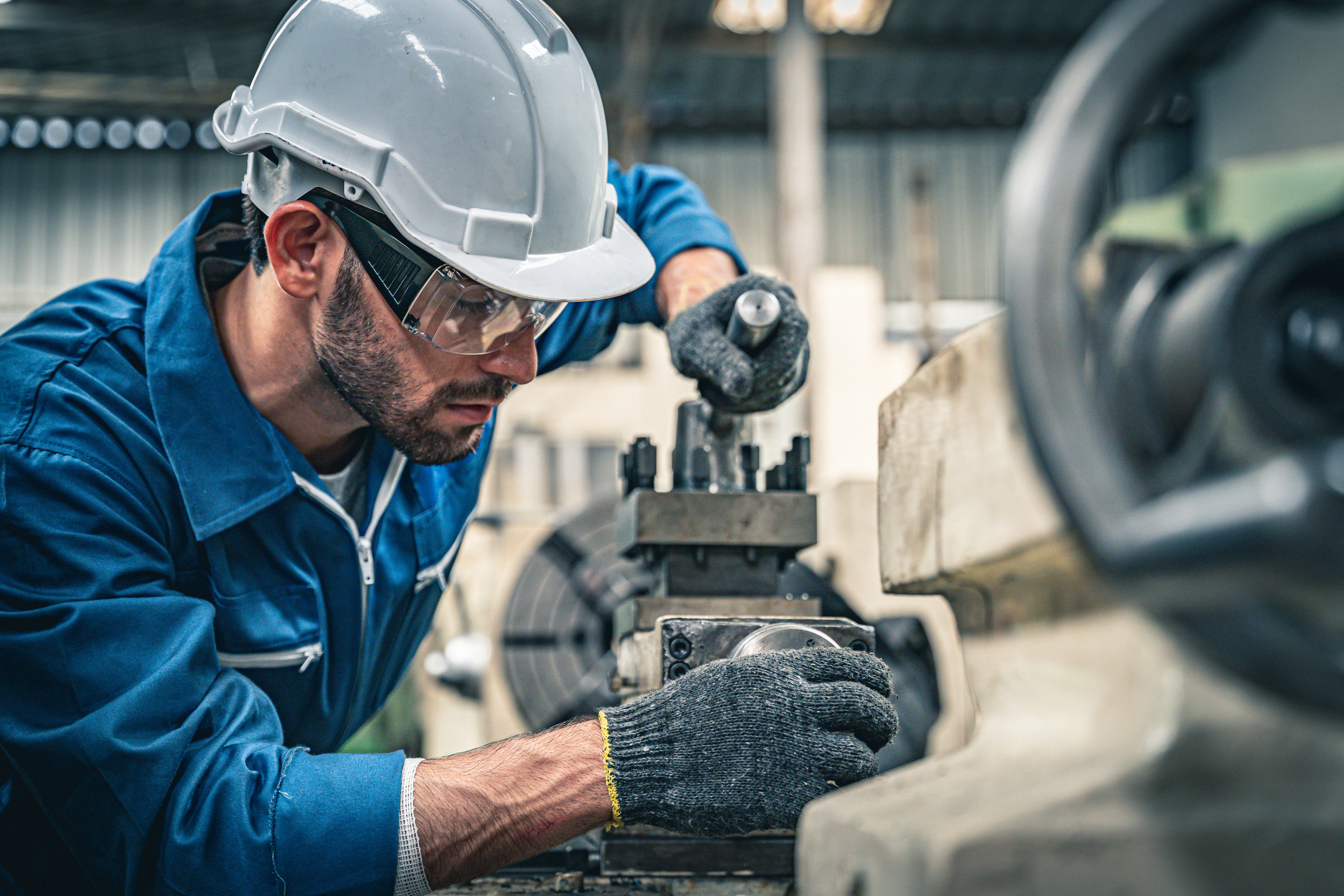
What Is Root Cause Analysis (RCA)?
According to the American Society for Quality (ASQ), root cause analysis involves a range of tools, approaches, and techniques used to uncover the primary causes of problems.
The goal of RCA is to prevent recurring issues from happening by eliminating their root causes. The process follows a chain of causes and effects to pinpoint the origin.
Toyota founder Sakichi Toyoda originally developed root cause analysis to improve the efficiency of the automaking manufacturing process. Today, RCA is a critical component of the international Total Quality Management (TQM) movement, the corporate process improvement movement, and the drive for quality control.
How Does RCA Work?
RCA works on the principle that all events have causal relationships.
Addressing the effect of an undesirable event isn’t always enough. Tracing the sequence of events back to the original “falling domino” is necessary to complete problem resolution.
In a nutshell, root cause analysis can help you understand what happened, how it occurred, and the reason why. The process is based on “the three Rs”:
- Recognize: When an asset breaks down, you may not be able to find the true cause of the event from a simple observation. What you observe is only a symptom. Pinpoint the true cause of the problem to prevent future occurrences.
- Remedy: Once you’ve recognized the actual cause of the problem, take corrective action. Afterward, monitor the asset to see if the issue reoccurs. Should the issue reoccur, your team likely mistook a partial cause for the root cause. In such instances, go back to the drawing board and perform a more thorough RCA.
- Repeat: Finally, replicate working solutions with similar assets in other locations. This will help prevent the same errors from showing up in other facility areas.
It’s worth mentioning that you also can perform RCA when confronted with surprisingly positive outcomes. In this instance, RCA can help the organization replicate the results to improve productivity in other areas.
“Companies that can quickly identify the root cause of change have a strong competitive advantage due to their ability to react more quickly and make better decisions.”
Forbes
Benefits of Root Cause Analysis Tools
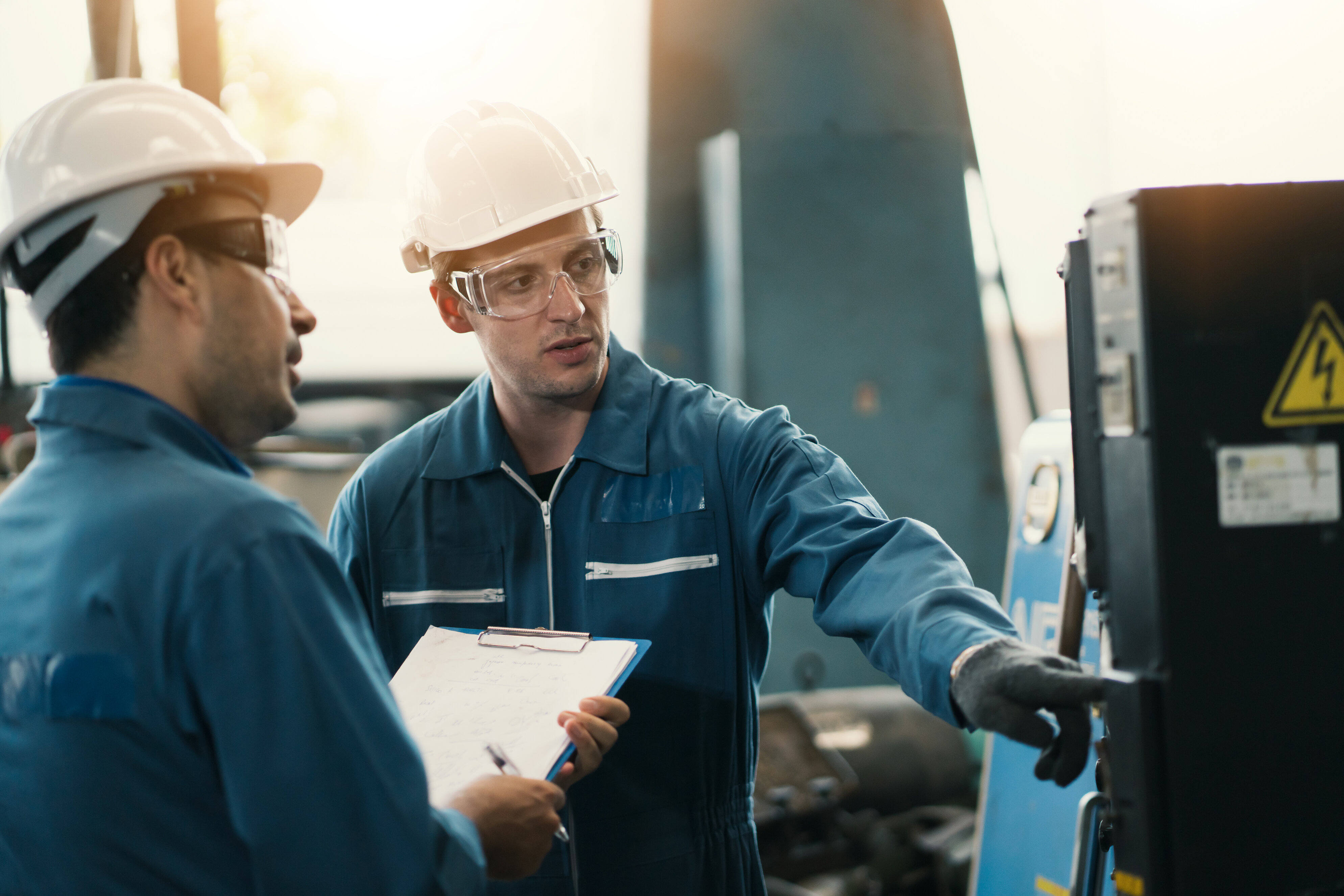
The primary benefit of conducting root cause analyses is clear: the end to recurrent problems! Who doesn’t like the sound of that?
RCA enables organizations to move from short-term to long-term solutions for inconvenient asset breakdowns. You’ll be able to deal with the source of an equipment breakdown. With that said, there are less obvious benefits to RCA, including:
- Reduced Maintenance Costs: Constantly fixing the same equipment problem is expensive. Finding longstanding solutions reduces emergency repair costs over time.
- Maintenance Task Prioritization: RCA helps prioritize maintenance activities for a facility’s most crucial assets. Management can better determine which maintenance tasks have a lasting impact on uptime. This allows more time for high-value tasks.
- Improved Safety and Reliability: RCA enables organizations to provide safe working environments by eliminating issues that hamper employee safety. Employers are obligated under OSHA regulations to handle risk management. In addition, RCA helps ensure consumer products are safe, high-quality, and non-defective.
- Enhanced Product Availability: Constant equipment breakdowns affect production timelines. Delayed timelines negatively impact product releases, which harms market share. Root cause analysis tools make it easier to deal effectively with equipment breakdowns and improve product availability.
- Improved Team Communication: Teams that use root cause analysis tools can better articulate exactly how and why common problems happen when writing standard operating procedures.
When effectively executed, RCA improves both maintenance operations and a company’s bottom line. Now, let’s look at ideal situations for using root cause analysis techniques.
When to Use Root Cause Analysis Tools
Root Cause Analysis tools include Failure Mode and Effect Analysis (FMEA), Fishbone Diagrams, What-If, HAZOP, and Fault Tree Analysis, to name just a few RCAs used in maintenance across industries.
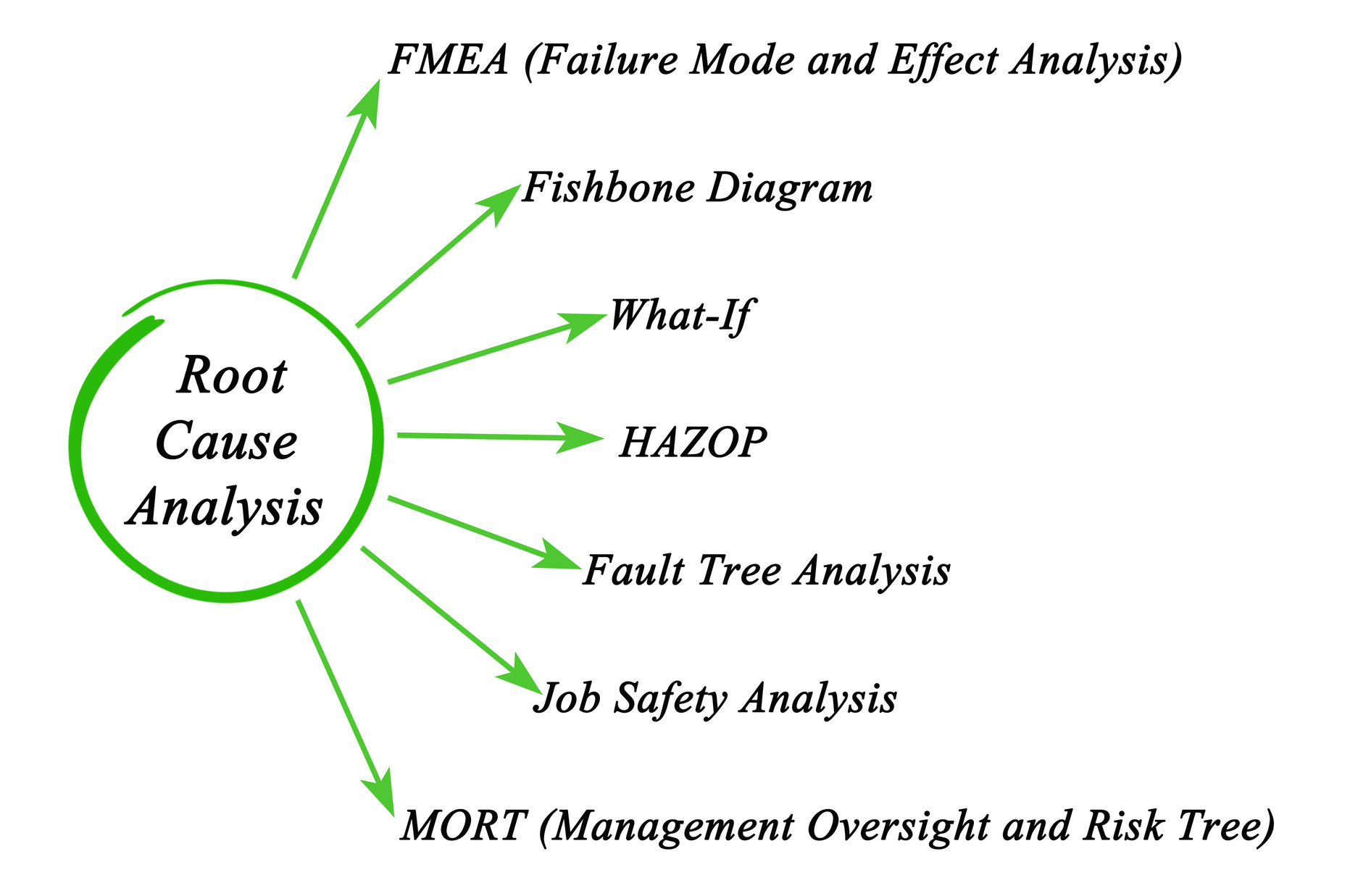
Despite the undeniable benefits, there are situations when using root cause analysis techniques isn’t cost-effective. RCA requires significant money, time, and workforce to execute successfully.
Put simply, it isn’t feasible to rely on root cause analysis tools for every problem you encounter. While there are no rules for when to perform RCA, the following two instances provide a good rule of thumb for assessing RCA candidates:
1. Persistent Faults
This criterion is the most obvious: when an asset breaks down repeatedly, fixing the visible problem probably won’t help in the long term. Dig deeper to uncover the hidden contributing factors.
2. Impact of Failures
In instances where equipment failures could be extremely harmful, such as an airplane crash or an oil rig explosion, managers should perform RCA. Beyond safety hazards, incidents in which the cost of downtime significantly outweighs the cost of repair are strong candidates for RCA.
Proactively investigate failures that impact production, plant safety, or other critical systems.
Industries Using Root Cause Analysis Tools
While RCA can benefit almost any business and industry, specific sectors use it more. Industries that practice RCA include:
Manufacturing
The manufacturing industry performs RCA for industrial process controls. It helps manufacturers ensure that products meet required quality-control requirements, safety standards, and OSHA guidelines. In addition, manufacturers use RCA in asset reliability engineering and maintenance.
IT and Telecommunications
This industry uses root cause analysis tools to detect the primary causes of severe IT issues, like security breaches. It helps organizations ensure their systems, networks, and databases are secure from cyber-attacks.
Healthcare
Healthcare practitioners routinely practice RCA to prevent medical errors. The National Center for Biotechnology Information (NCBI) suggests that better RCA would enable healthcare professionals and patients to minimize such mistakes.
Food & Beverage Production
According to the Food Safety and Inspection Service (FSIS), 31 products (amounting to 1,462,019 pounds of food) were recalled in 2020. In fact, RCA tools help food and beverage producers avoid recalls due to safety concerns, thus preventing lost revenue and lawsuits.
Environmental Science
Finally, environmental engineers rely on RCA to prevent unnecessary pollutants from being released into the environment. The problem-solving process plays a crucial role in reducing equipment-caused environmental releases, industrial waste, and human errors that harm air and water quality.
Other industries that benefit from root cause analysis include medical devices, transportation, pharmaceuticals and dietary supplements, oil and gas, nuclear power, shipping, aviation, and space exploration.
How to Conduct a Basic Root Cause Analysis
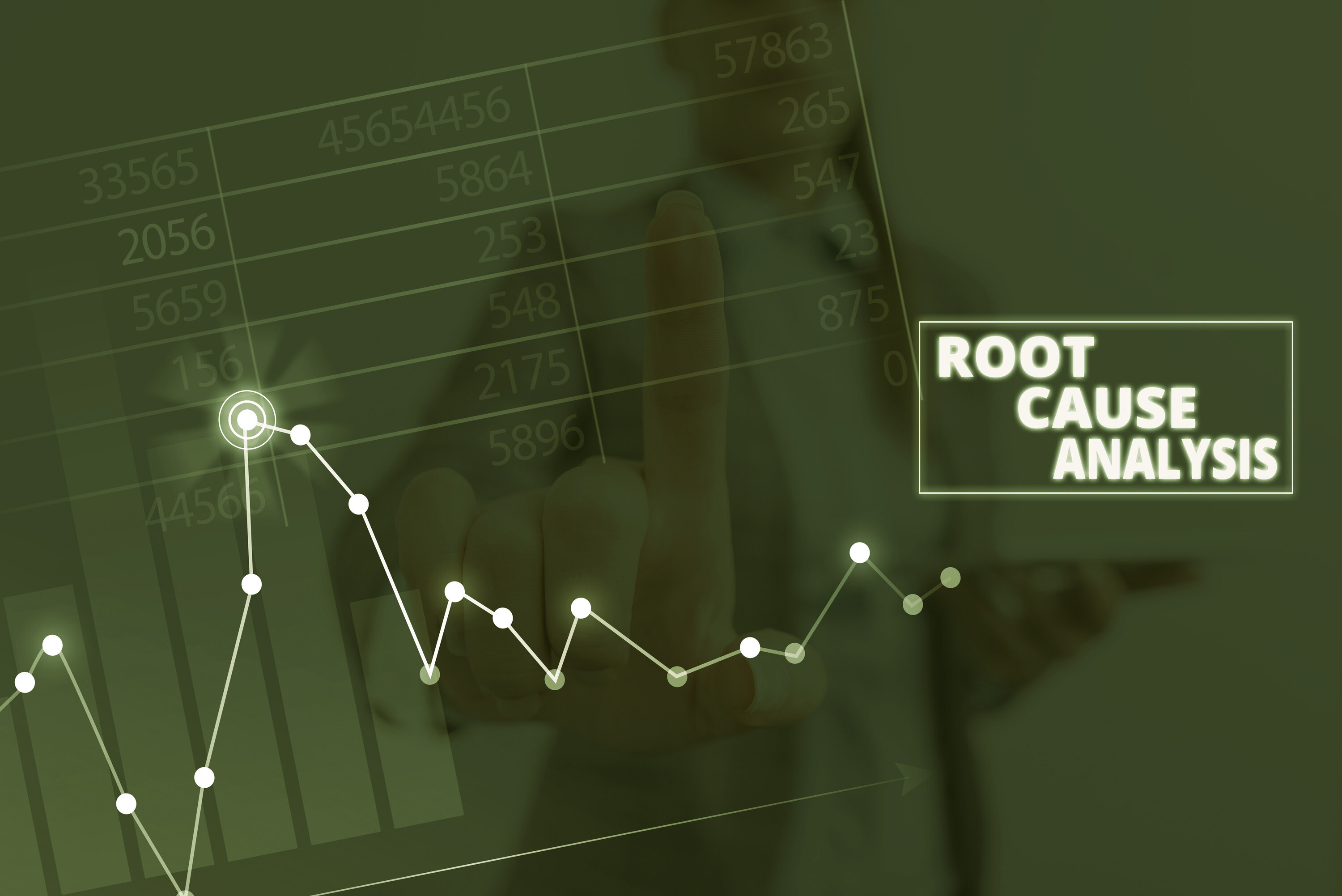
Step 1: Define the Problem
Identify the problem you must solve. What’s happening and what are the symptoms of the occurrence?
Write a problem statement, including a detailed description of the issue at hand. Include any available data to clarify the facts. The assessment should provide your problem-solving task force with a thorough explanation of the problem.
Step 2: Collect Data
Next, seek to gain a complete understanding of the failure, its causal factors, and root causes.
Use the SMART principle to ensure that the data you’re collecting is specific, measurable, action-oriented, realistic, and time-specific.
Data collection includes information about the existence of the problem, how long it existed, and its impact on the organization. Maintenance data worth collecting includes:
- Asset age
- Manufacturer’s manuals
- Machine operating characteristics
- Operating environment characteristics
- Length of time in continuous operation
- Operating patterns and maintenance history
- Machine operators and maintenance technicians responsible
We recommend using a digital platform such as MaintainX CMMS to collect asset data.
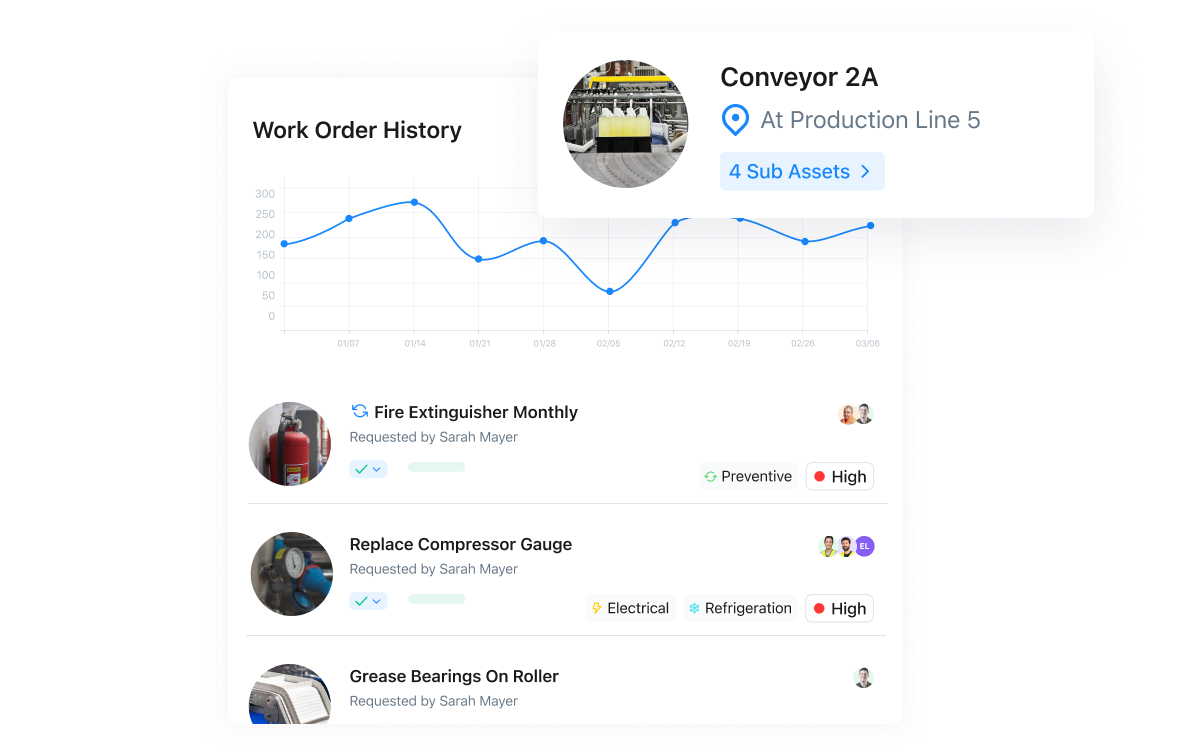
Step 3: Identify All Potential Factors
As soon as you’ve collected enough information about the problem, it’s time to get organized. Develop a structured way to analyze your data to identify any knowledge gaps. At this stage, you’re looking to determine:
- The sequence of events that preceded asset failure.
- Surrounding conditions that may have contributed to the failure.
- Any other problems that occurred as a result of the main failure.
Develop a causal factor chart to provide a sequential description of the events leading to the failure, in addition to surrounding conditions.
The more information you have, the more detailed your causal factor chart will be. Identify as many causal factors as possible instead of limiting yourself to just one or two.
Step 4: Identify Your Root Cause
Next, investigate why the causal factors exist to unearth a definitive reason for the occurrence of asset failure. For your RCA process to be effective and bear relevant results, you must dig deep enough to identify the leading cause of failure.
When investigating root causes, remember that they should be:
- Hidden: Root causes are not typically easy to find. The goal is to uncover specific underlying reasons that you would overlook at first glance. The more targeted the root cause, the easier it becomes to generate solutions.
- Cost Efficient: Ultimately, RCA should be cost-effective. Don’t dedicate resources to a process that won’t bear lasting solutions to a problem.
- Controllable: Focus on root causes on which management can realistically take action. For example, severe weather as a root cause for delayed deliveries isn’t under management’s control. The root cause you identify should enable the team to develop specific recommendations to remedy the situation.
It’s worth emphasizing that RCA assumes that all failures and systems are interrelated. Thus, a single action can trigger a chain of other events. By tracing these events, you’ll be able to discover where the problem started and how it resulted in the failure you’re dealing with.
Types of Root Causes
Did you know it’s possible to identify more than one type of reason for failure? The three types of root causes are:
1. Human Causes
Sometimes, failure comes from machine operators, maintenance technicians, and other individuals doing something wrong. Human causes often result in physical causes. For example, car brakes can fail because the mechanic forgot to refill the brake fluid.
2. Physical Causes
These are causes that result from a material item failing. For example, the windshield wipers in your vehicle lose traction over time.
3. Organizational Causes
These are business processes, systems, or policies that result in faulty decision-making. For example, the vehicle’s maintenance checklist didn’t include a brake fluid refill, so the mechanic assumed it was unnecessary.
Step 5: Take Action
Finally, implement solutions to deal with the identified causes to prevent future occurrences. Your remedies should be actionable, achievable, and measurable.
Questions worth asking include:
- What immediate actions can we take to resume normal operations?
- How can we prevent the problem from happening again?
- How will we implement the solution?
- Does the solution pose costs and/or risks?
- Who will be responsible for it?
Remember: a single problem may have multiple solutions. Keep in mind that you may need to redo the root cause analysis if the problem keeps occurring. Unfortunately, it’s not uncommon to revisit early conclusions when faced with new evidence.
Popular Methods of Root Cause Analysis
Root cause analysis doesn’t take a single approach to problem-solving.
Think of it as a conceptual framework that allows you to investigate failures beyond their face value. This means there are many ways to execute RCA successfully.
In this section, we’ll look at some of the most popular methods of conducting root cause analysis. Each is beneficial to the different industries and situations investigated.
Failure Mode and Effects Analysis (FMEA)
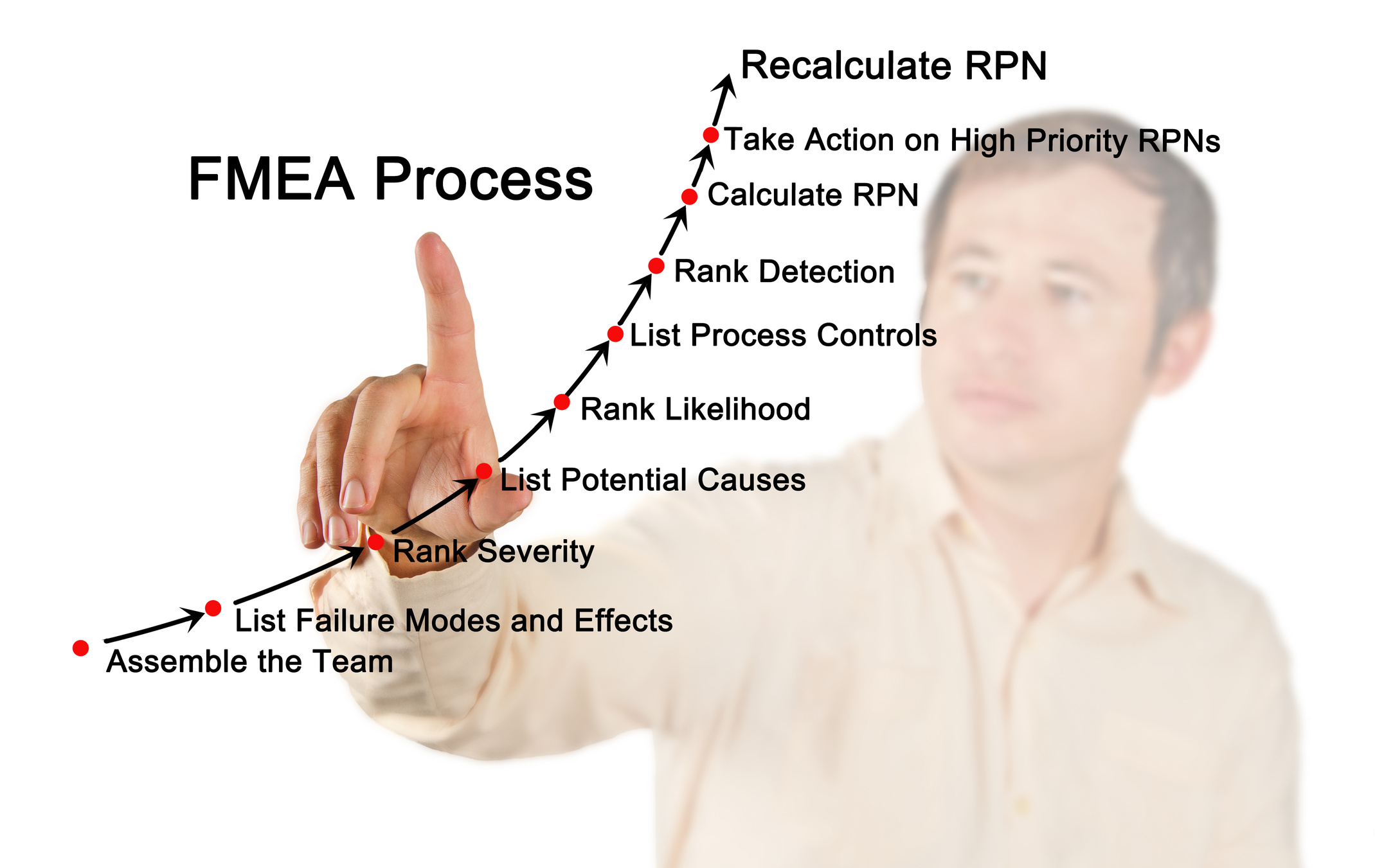
Failure Modes and Effects Analysis (FMEA) is a systematic method that identifies, analyzes, and documents potential failure modes and their impact on business processes and productivity.
This framework prioritizes maintenance actions by assigning them to risk priority numbers (RPN). It aims to anticipate and mitigate the impact of failure proactively.
The three primary types of FMEA are:
- Process FMEA: PFMEA helps to identify potential failures in business processes. The goal of PFMEA is to improve the production process to prevent problems in the end product.
- Design FMEA: Organizations deploy this type of FMEA during the product development cycle. It focuses on product design and investigates safety concerns, regulatory requirements, and potential failures. DFMEA ensures that companies deliver high-quality, safe, and reliable products to customers.
- System FMEA: System FMEA analyzes entire systems and subsystems to ensure teams remedy potential failures that could impact overall productivity. It investigates workplace and system integration, among others.
Not surprisingly, safety-oriented industries, such as manufacturing, warehousing, and aerospace industries, extensively use FMEA. Advantages of FMEA include:
- Optimized production costs
- Minimized incidences of product recall
- Structured system for prioritizing corrective maintenance
- Qualitative and quantitative controls for evaluations
Despite these benefits, FMEA does have its limitations. For example, it doesn’t describe causal relationships between failures and potential causes.
FMEA teams are also not required to provide evidence of causal relationships. With that said, FMEA remains an extremely popular root cause analysis tool within industrial maintenance settings.
The 5 Whys
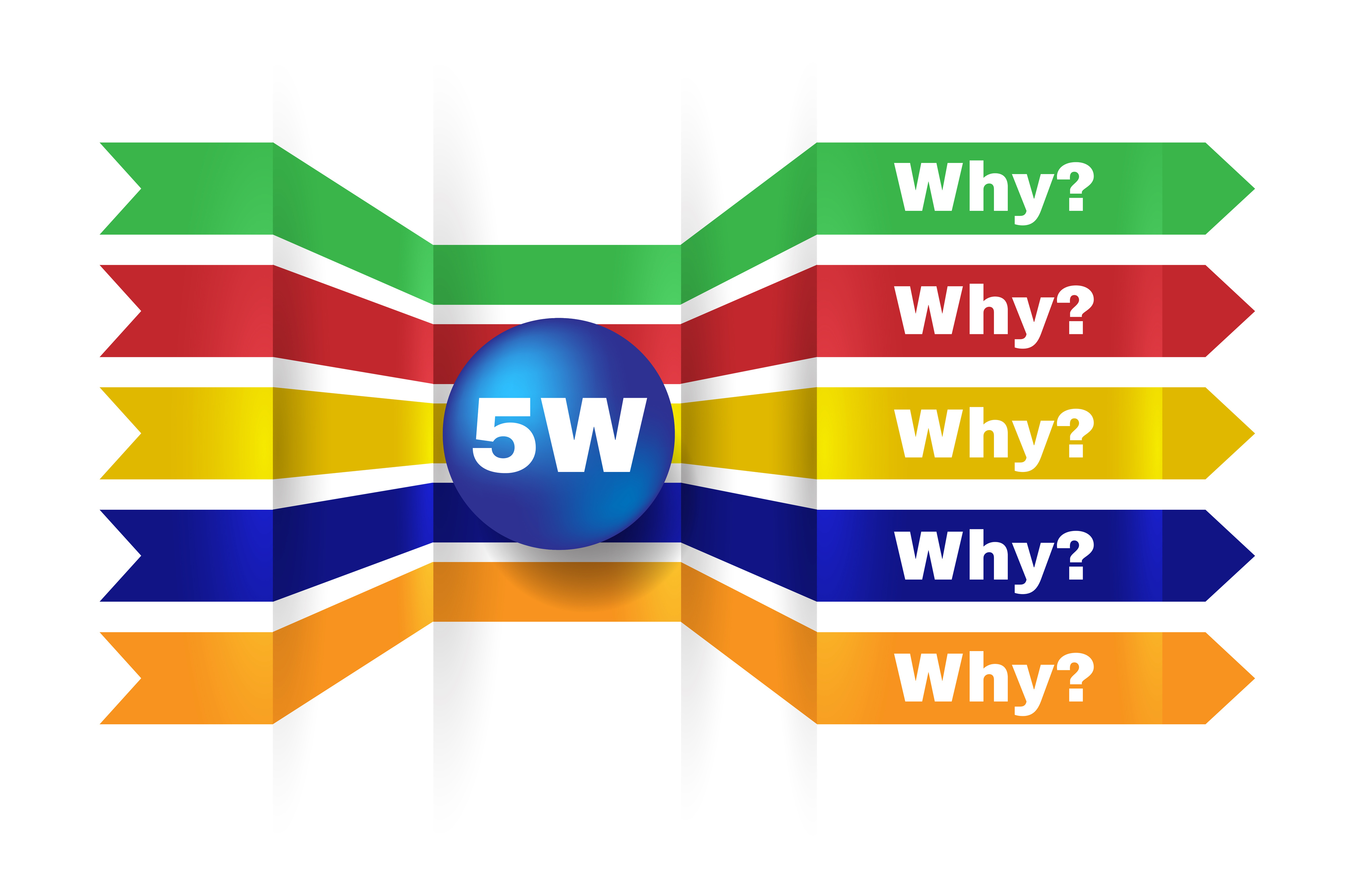
Sakichi Toyoda, the Toyota founder, developed The Five Whys process to solve complex manufacturing problems. The question-based technique establishes cause-and-effect relationships by asking the question “Why?”
Interestingly, the technique works on the principle that you can get to the root cause of the problem by asking “Why” until you reach a countermeasure. It encourages organizations to find solutions to problems from workers experienced with the processes in question.
This method is straightforward yet practical. It’s used across several industries to find practical solutions to problems. Here’s an example of the process in action:
Problem statement: A conveyor belt broke down during peak hours
#1 Why: It was overloaded, and the fuse blew.
#2 Why: Its bearings were not properly lubricated.
#3 Why: The lubrication pump wasn’t fully functional.
#4 Why: The pump’s shaft wore out.
#5 Why: There’s no way of preventing metal scraps from getting into the pump.
Despite its popularity, organizations rarely use The Five Whys technique in formal investigations. Some managers criticize the method for promoting linear thinking that ignores non-obvious causes.
In addition, they suggest the method doesn’t provide adequate guidance for implementing solutions. The Five Whys is best for resolving minor problems and generating causes with other RCA methodologies.
Fault Tree Analysis
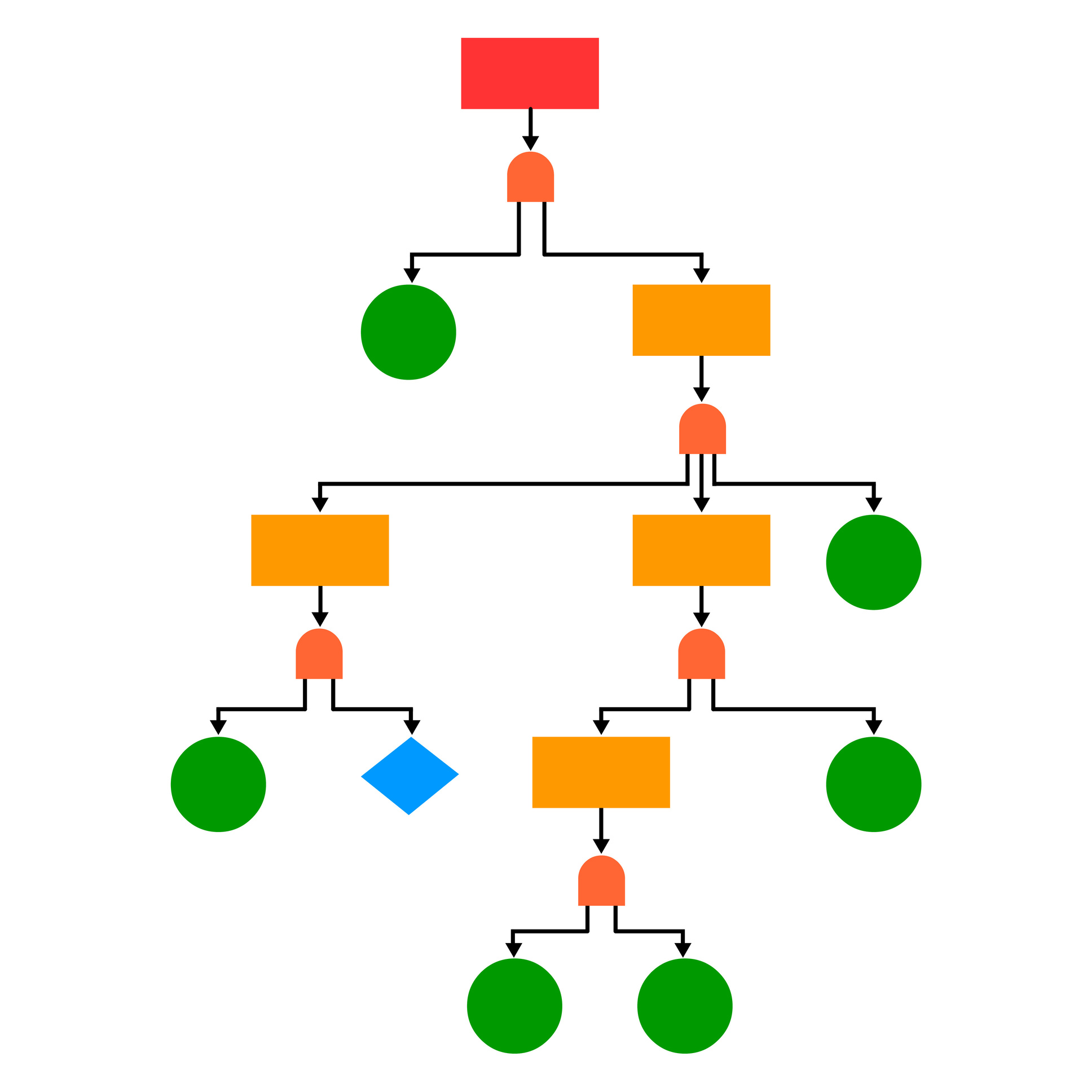
Fault Tree Analysis (FTA) is a graphic technique that describes a combination of possible occurrences within a system that can result in undesirable outcomes.
Initially developed by Bell Laboratories for the U.S. Air Force Inter Continental Ballistic Missile (ICBM) launch control system evaluation, the technique uses boolean logic. It also takes into account both human and system failures.
The process maps logical relationships between asset failures and subsystems. It places the failure being analyzed at the top of the chart and then looks at the possible causes. Causes with logical “OR” combination-causing effects are put together using a logical “OR” operator.
An “OR” points to the possibility that the cause could be one thing or another. Alternatively, an “AND” indicator suggests both factors are necessary for an issue to occur.
Additional Root Cause Analysis Methods
- 8D Problem-Solving: Developed by Ford Motors, 8D Problem-Solving aims to identify, correct, and eliminate recurring problems in products and processes. Quality engineers in many industries—automotive, retail, manufacturing, and healthcare—use the Eight Disciplines approach to deal with safety and regulatory issues.
- Six Sigma Methodology: The Six Sigma approach advocates using the DMAIC process (Define, Measure, Analyze, Improve, Control) to deal with problems. Motorola developed the process to help its managers work faster while making minimal mistakes.
- Pareto Analysis: Vilfredo Pareto, an Italian economist, says that 80 percent of consequences stem from 20 percent of causes. The 80/20 rule is known as Pareto’s Principle. Use a Pareto chart to outline how most of the failures are caused by a small number of factors. Then, prioritize the causes that result in the highest number of bad effects.
- Cause and Effect Diagram: This tool is also known as the Ishikawa or fishbone diagram. It illustrates how the impact of a failure relates to underlying causes. This particular method is effective for visual brainstorming sessions.
Do you know what’s cool? You can use any of the methods mentioned above to conduct a root cause analysis! Different managers prefer different methodologies to conduct RCA.
If one methodology doesn’t deliver the desired results, choose another for a follow-up round of RCA. In complex cases, some organizations choose to hire consultants to spearhead the process. For these reasons, it’s impossible to declare any root cause analysis tool “the best” one.
Want to continue learning more about root cause analysis tools? Check out this webcast by ASQ fellow Jim Rooney: Root Cause Analysis for Beginners, Part 1.
Decrease Downtime with MaintainX
If you’re seeking lasting resolutions to your equipment woes, root cause analysis tools may be exactly what you need. As previously mentioned, there is no “right” way to conduct RCA.
Assemble an experienced team that understands the issues at hand, choose your RCA tool of choice, gather as much data as possible, and figure out what’s really going on! And, if you haven’t already, download MaintainX CMMS to simplify your facility’s asset cataloging process.
Your team members will love the platform’s convenient messaging, inventory management, and work order prioritization features. The best part? Most users require zero training to get started! Simply download the app to your desktop or mobile device and follow the prompts.
FAQs
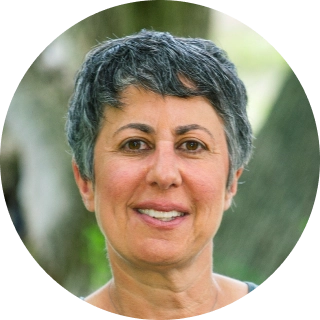
Caroline Eisner is a writer and editor with experience across the profit and nonprofit sectors, government, education, and financial organizations. She has held leadership positions in K16 institutions and has led large-scale digital projects, interactive websites, and a business writing consultancy.