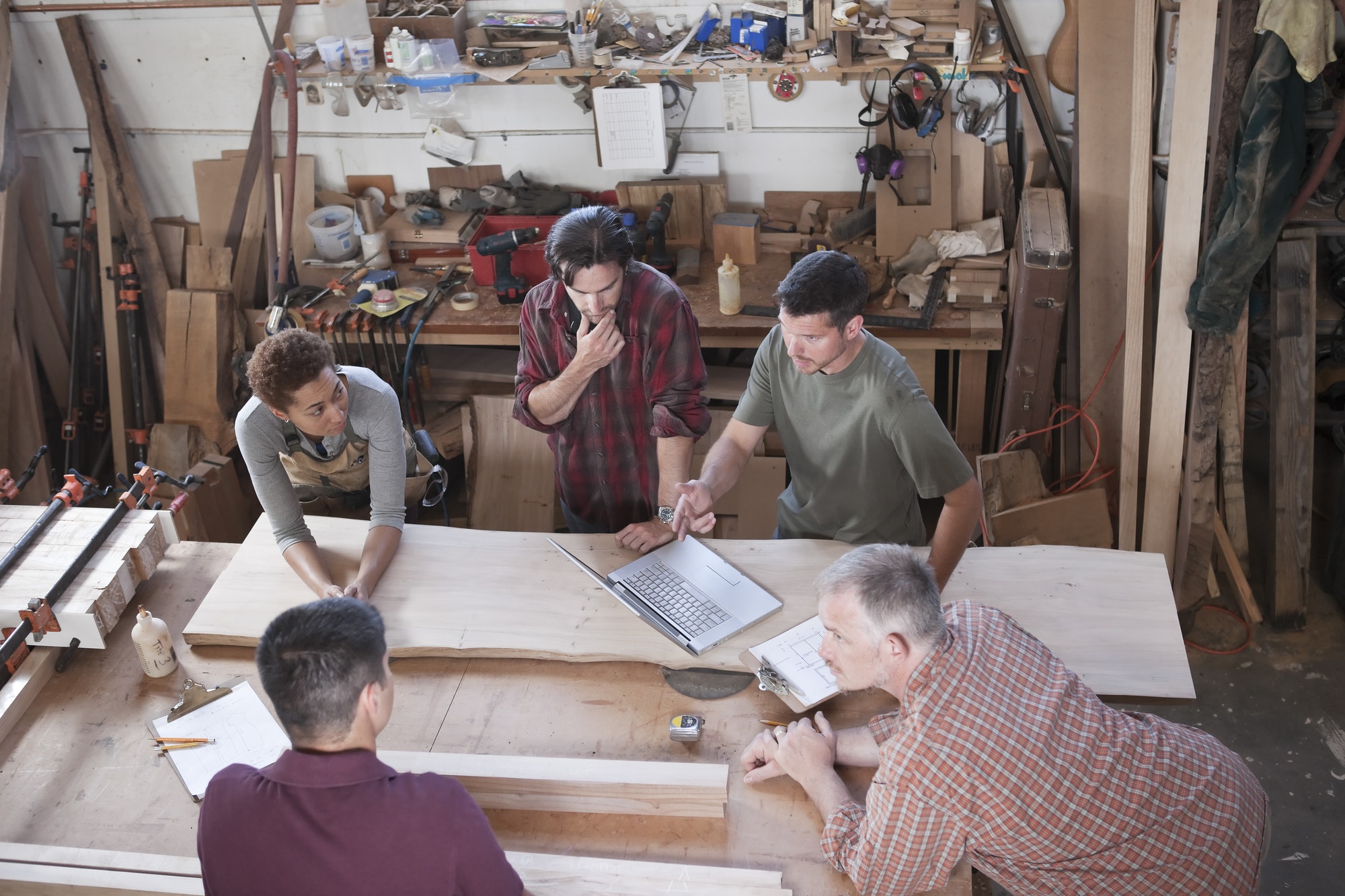
Are you new to Design Failure Mode and Effects Analysis (DFMEA)? This step-by-step guide will provide handy pointers for conducting your first DFMEA, including some common mistakes to look out for.
In recent years, this subset of FMEA has quietly gained popularity in corporate settings. Why? Because it allows engineers to identify the risk factors associated with product design before companies invest money in ineffective materials, processes, and manufacturing equipment.
What Does DFMEA Stand for?
Let’s begin by answering the most basic question: what is DFMEA?
DFMEA stands for “Design Failure Mode and Effect Analysis.” Engineers execute DFMEA to prevent unnecessary product development issues. It’s an analytical process companies use to identify, mitigate, and eliminate product design risks. In fact, Capgemini explains that “Efficiency by design can contribute to productivity gains by helping in areas such as asset utilization and cost for defects. It will also make a positive impact on areas such as product portfolio rotation and time to market which will translate into improved market share.”
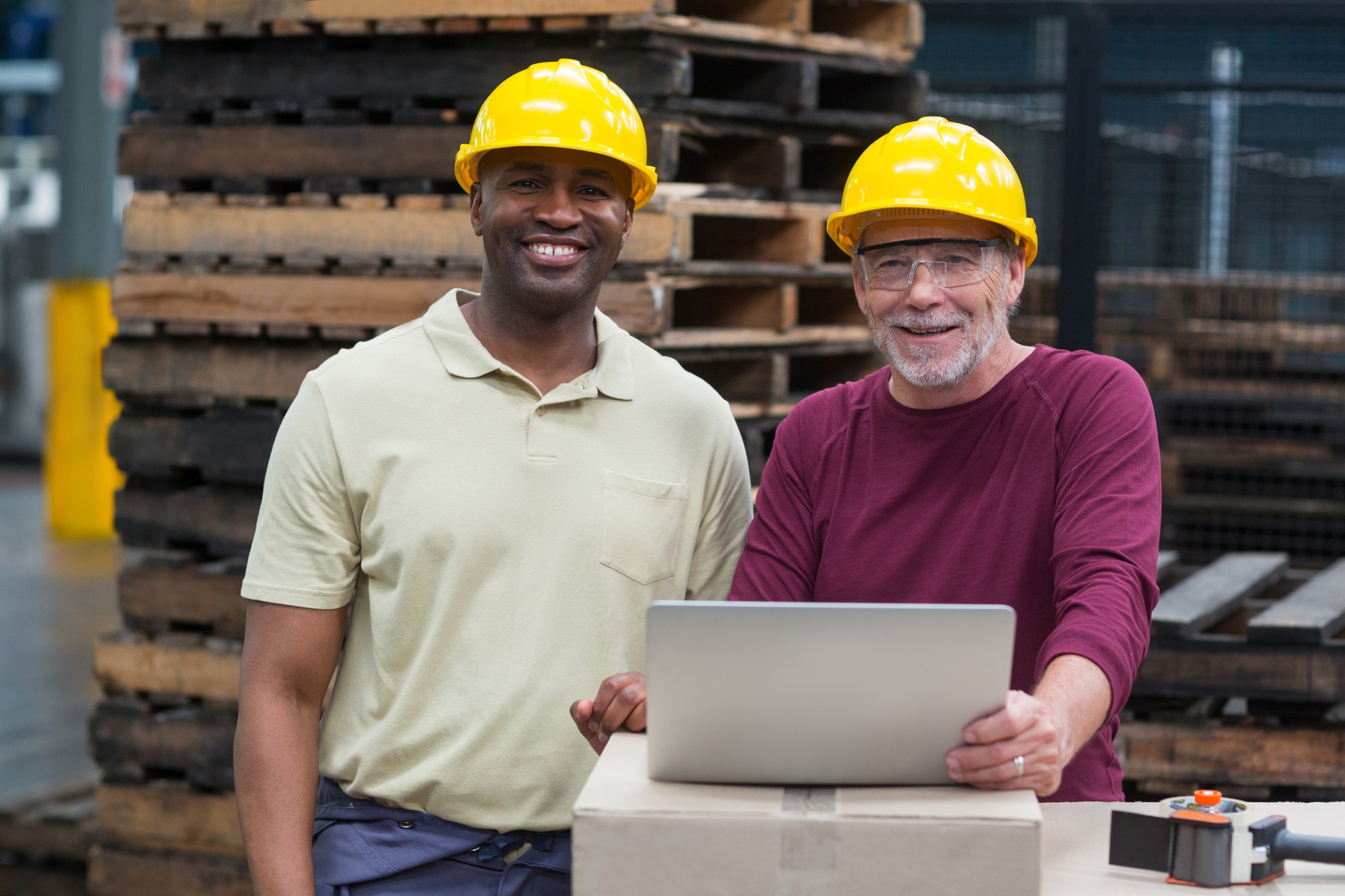
What Is the Purpose of DFMEA?
DFMEA is an indispensable product engineering tool for ensuring companies produce reliable products and services that satisfy customers in today’s competitive business landscape.
As previously mentioned, companies run DFMEA to reduce the number of design defects. Ideally, the process helps companies prevent any design-related problems from occurring at all. Anything that hinders a product from operating correctly is considered to be a “defect.”
The result? The consistent production, manufacturing, and output of high-quality deliverables. Companies involved in manufacturing, high-end technology, service delivery, and construction industries are the most likely to use DFMEA.
But organizations responsible for producing a variety of products and services also use the method for risk management. For these reasons, DFMEA is a vital part of total quality management processes.
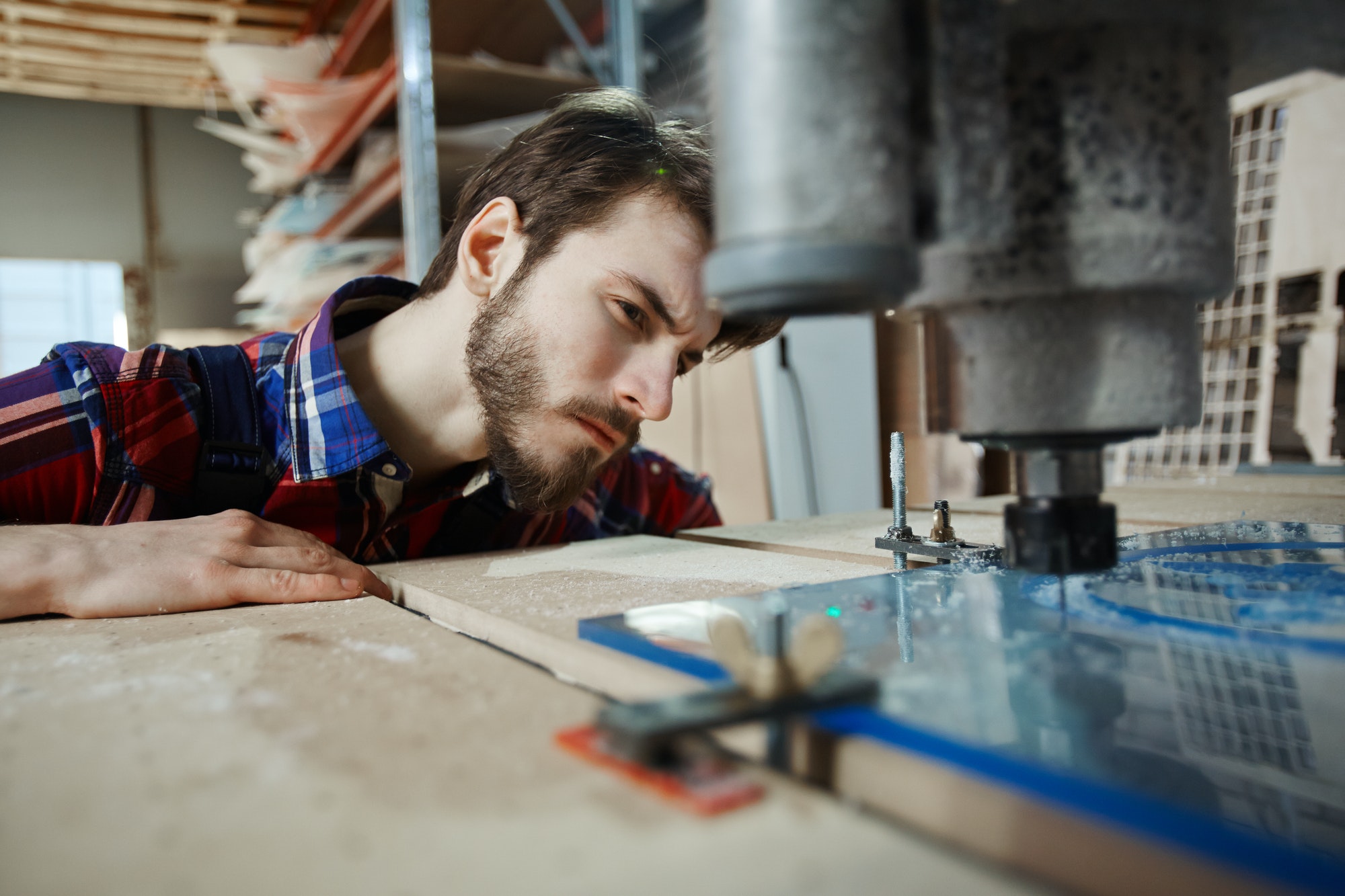
How Does DFMEA Work?
DFMEA looks at potential design failures from all angles to determine what could hinder an intended product function from happening. It focuses on four areas of analysis:
- Failure Mode: The ways that a design-related failure could occur. For example, the laptop interface freezes when X number of programs are open for X number of hours.
- Failure Cause: The root cause of the failure mode could be a defect in a device’s design, system, quality, or part application.
- Failure Effect: The immediate consequences of the failure. For example, the frozen interface leads to a frustrating user experience.
- Severity of Failure: The severity of failure impacts productivity, quality, and safety. Quality engineers usually think in terms of worst-case outcomes.
In essence, DFMEA helps determine what might go wrong, how harmful the consequences would be and how to mitigate the failure modes before they occur.
DFMEA has helped many industries such as manufacturing, software development, healthcare, and food production take a proactive risk prevention and reduction approach.
Difference between DFMEA and FMEA
Failure Mode and Effects Analysis (FMEA) is simply a broad form of DFMEA. Essentially, it’s the same risk assessment tool applied to a broader scope of operations.
Cross-functional teams use FMEA to identify potential failures in product design, production processes, and equipment downtime. They apply the analytical method to a myriad of applications, not only design-related failure modes. As a result, companies spend less time, money, and resources on DFMEA compared to FMEA.
Organizations perform DFMEA in the following scenarios:
- Before launching a new product, process, or service
- Before deploying existing strategies or products in new capacities
- Before developing system control plans for both existing and new processes
- While making improvements to existing processes, products, and services
- When customers routinely complain about a deliverable
As previously mentioned, the goal of FMEA is to minimize major failures in products, processes, and services. Both FMEA and DFMEA look to identify possible failures, determine the severity of the consequences of failure, and recommend improvements to mitigate that risk.
And, both DFMEA and FMEA focus on reducing operational costs, whereas FMEA aims to lower equipment maintenance-related expenses.
Benefits of DFMEA
DFMEA is a powerful quality-control tool that provides several benefits, including:
- Effective Risk Management: It’s nearly impossible to design a product or service without some type of oversight. The more mechanically complex the deliverable, the more likely its production processes will contain inefficiencies. DFMEA makes it easier to identify potential problems that would otherwise go undetected until trial production phases.
- High Customer Satisfaction Ratings: Design problems, no matter how small, can seriously inconvenience customers. Identifying potential failure modes during the design stage with DFMEA provides a safety net to catch the kind of flaws that upset patrons. Companies that provide seamless customer experiences build more loyal followings than those that don’t. This leads to increased brand recognition, longevity, and profitability.
- Lower Production Costs: Problematic products often end up being recalled. Not only does this increase production costs, but it results in delayed product launches. DFMEA helps prevent such issues by supporting the creation of realistic solutions.
- Prioritize Action Items: DFMEA isn’t only effective in identifying potential design failures, but it’s also effective in prioritizing mitigation actions. DFMEA ranks different failure modes based on severity, occurrence, and ability to detect the failures.
Now that you understand why design teams practice DFMEA and what the process entails let’s dive deeper into how they do it.
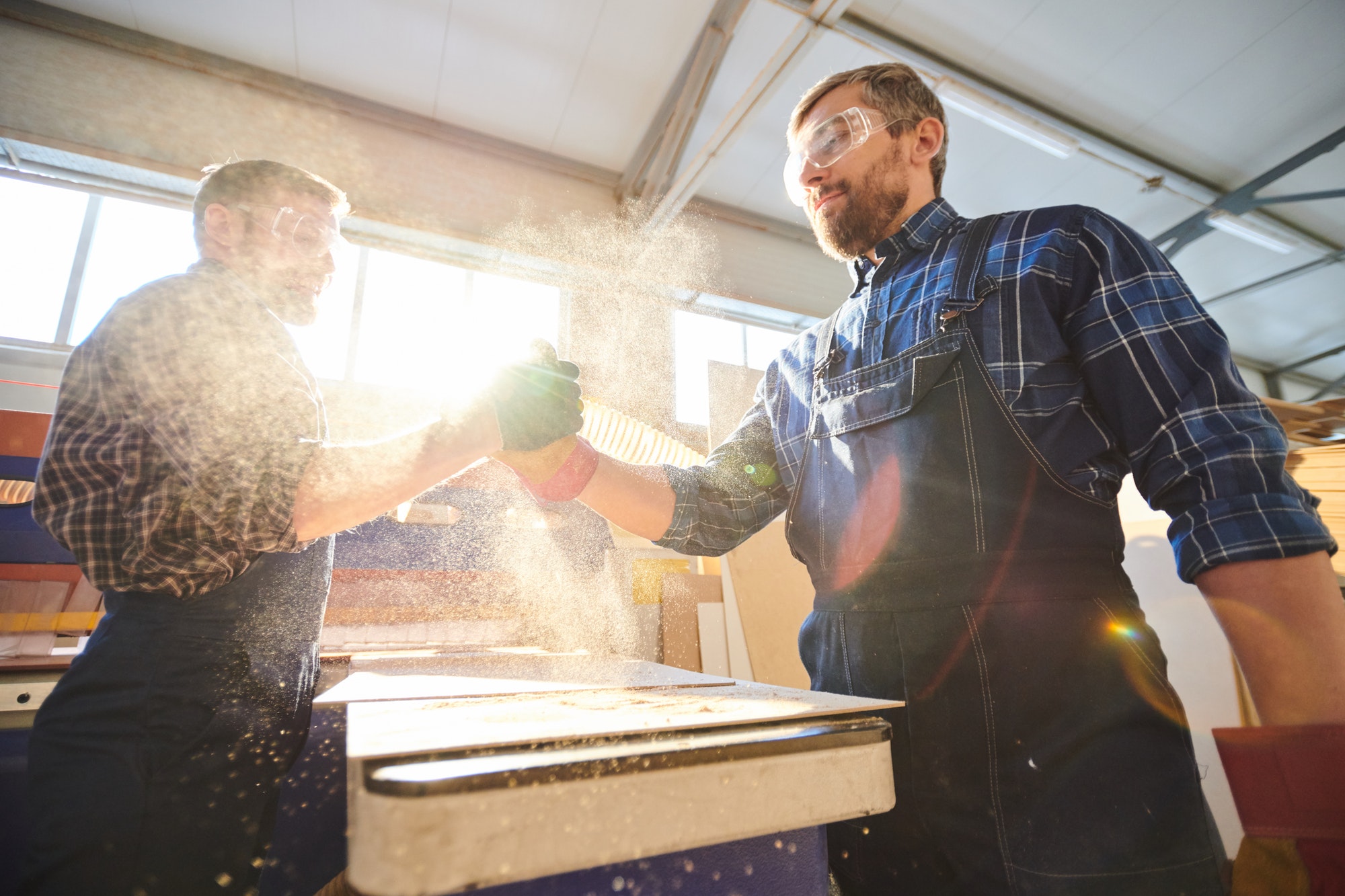
How to Perform DFMEA?
Because DFMEA involves many variables and several team members, things can get a bit complicated without proper systems in place. For this reason, abide by standard guidelines throughout your planning and execution process.
Below is a step-by-step summary to perform DFMEA:
Step 1: Review the Design
The first step involves assembling a multidisciplinary team to participate in the analysis. DFMEA teams typically consist of a product quality engineer, testing analysis engineer, material engineer, and production, service, and logistics teams.
Your cross-functional team will evaluate all the systems, subsystems, interfaces, and components to identify your product’s potential failure modes. Ideally, you should include representatives from each production process touch point to assess possible failure modes from all angles.
The goal at this stage is to determine how good the product design is and see improvements that can make it better. Each item is isolated and investigated so that quality engineers can identify failure modes for each one.
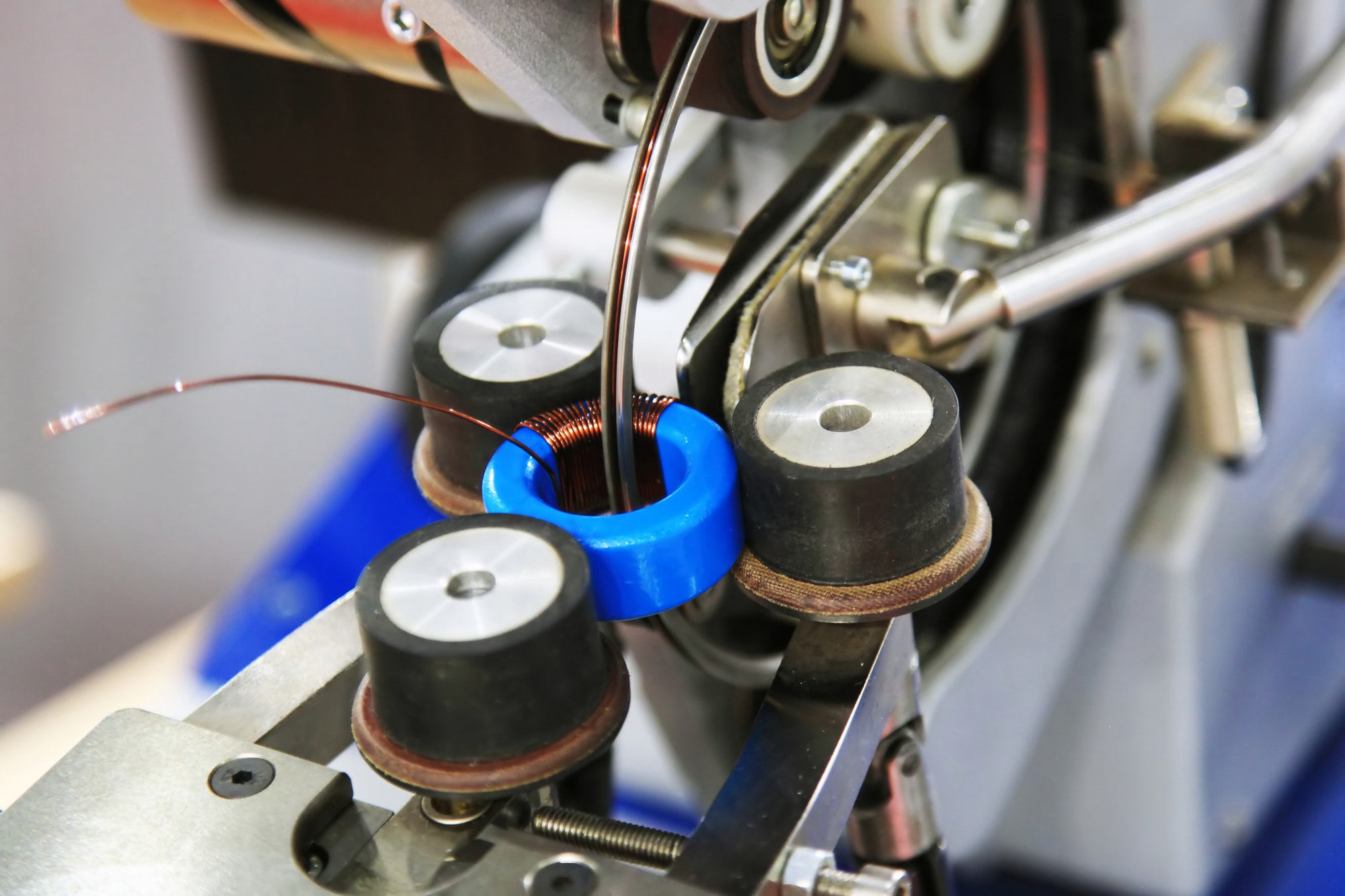
Step 2: Identify All Failure Modes
Thoroughly assess each item and identify all potential failure modes, including:
- Full Failures: This type of failure mode cripples the system or its components. The system cannot function until the faulty part is entirely replaced.
- Partial Failures: While the system or product is still functional, the failure mode prevents it from functioning fully. This results in reduced productivity.
- Intermittent Failures: The malfunction is irregular and unpredictable for this type of failure mode.
- Degraded Failures: This type of failure mode is a result of fatigue from frequent usage. The system eventually becomes weaker.
- Unintentional Failures: For unintentional failure, failure is usually a result of failure from another item.
It’s crucial to recognize that a single system or component can experience more than one type of failure mode. Document each failure mode—no detail is too small. There are also certain operating conditions, usage, and service operations that can affect failure modes.
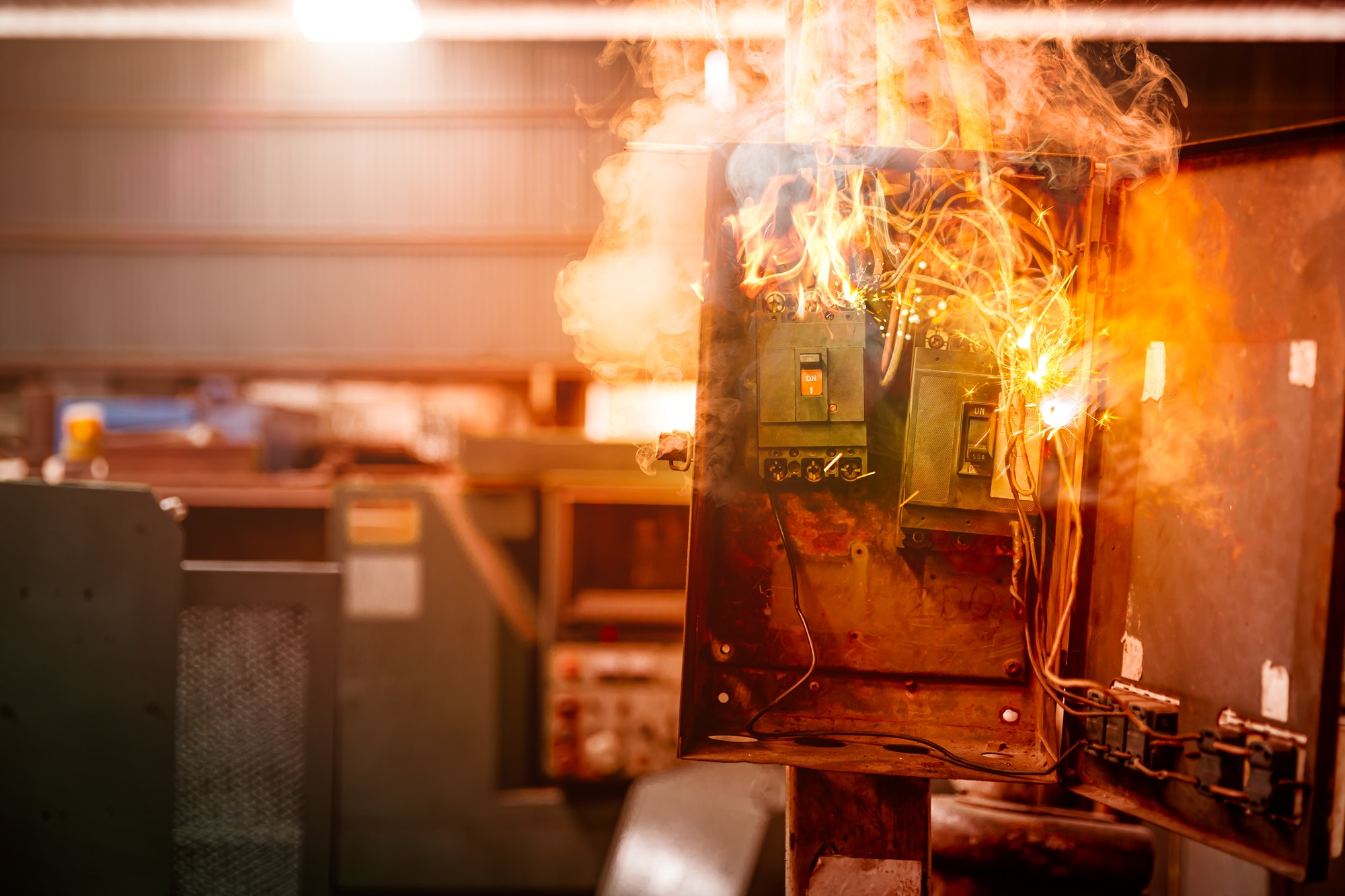
Step 3: Outline the Consequences of Each Failure Mode
After identifying all the potential failure modes, the next step is to identify the consequences of each failure mode. The effects can either be minor or severe.
For example, an electric surge (failure mode) could result in blown light bulbs (minor consequences) or a fire incident (severe impact).
Step 4: Assign Severity Ranking to Each Failure Mode
Next, determine the severity of each failure mode on the system, subsystems, components, users, and other relevant stakeholders. The degree of severity will vary for each failure mode, system, and component. The higher the severity ranking, the more serious the failure mode.
Rank failure modes based on the following criteria:
- 9-10: Anything that impacts safety and regulatory compliance.
- 7-8: The failure mode results in the system or component losing or experiencing a degradation of its primary function.
- 5-6: The system/component only loses or degrades its secondary function. The failure mode doesn’t affect the primary function.
- 2-4: The failure mode only results in annoyance but doesn’t affect system/component functionality at all.
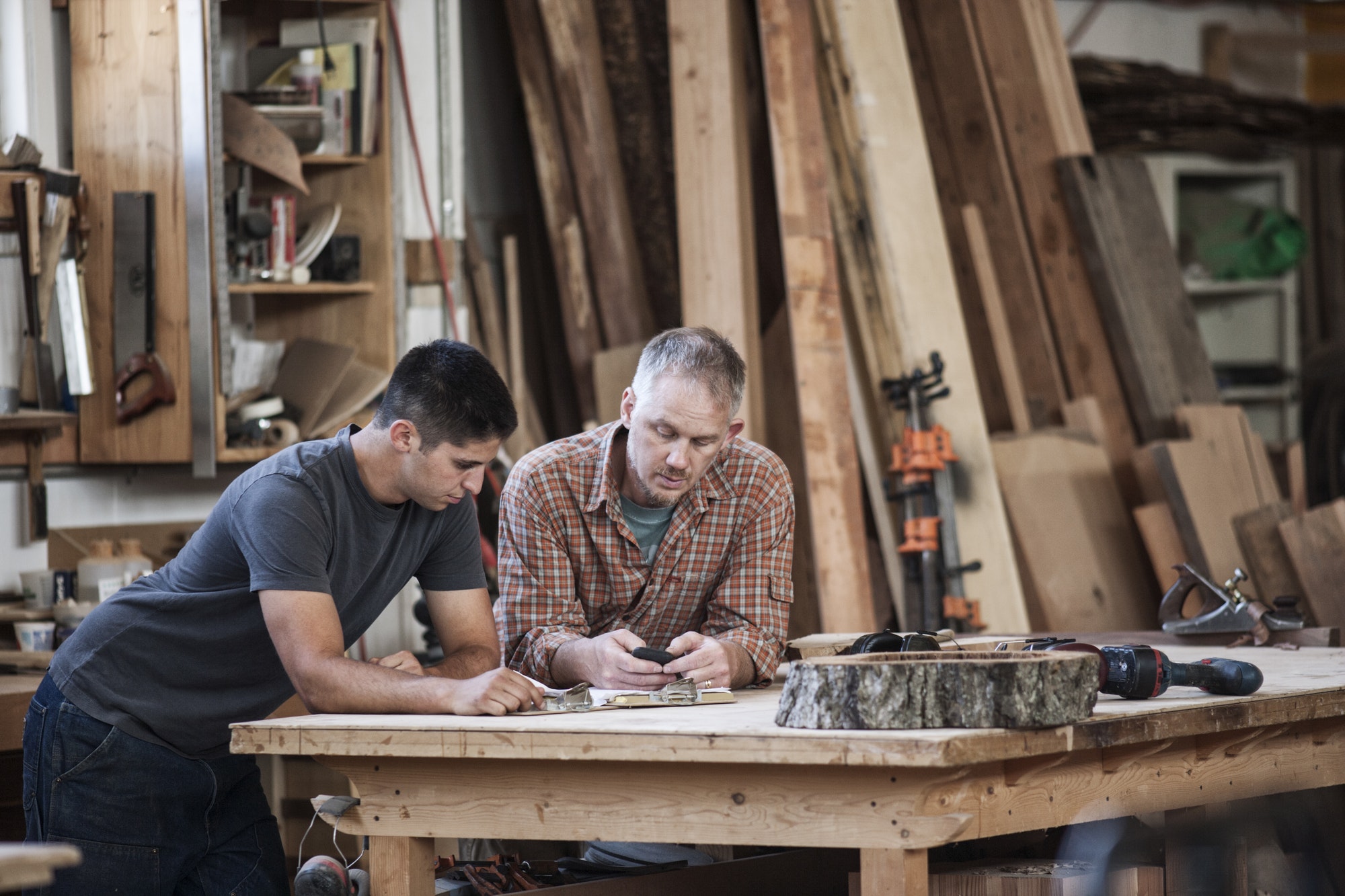
Step 5: Identify Root Causes of Failure
At some point, every organization—no matter how conscientious— experiences a design failure. It’s inevitable! But comprehensive DFMEA processes can facilitate fewer issues post-launch.
To resolve the failure modes, you need to identify their root causes first. That’s what you’ll be doing at this stage.
Step 6: Assess Existing Design Controls
Next, assess your existing design controls to determine how effectively they can detect and prevent your previously brainstormed failures. Robust design controls should be able to prevent, or at least foresee, failure modes. There are two types of design controls:
- Prevention Controls: These controls help eliminate failures from occurring. They include design, material, and engineering requirements as well as documentation. Prevention controls usually serve as standard operating procedures (SOPs) when undertaking projects.
- Detection Controls: Rely on detection controls to identify causes of failure and failure before they occur. You can use detection controls during prototyping, reliability testing, functional testing, and simulations.
Remember: the main purpose of design controls is to enable you to avoid incidents before your final product launch.
Step 7: Assign Occurrence Rankings to Each Failure Mode
Use occurrence rankings to determine the likelihood of each failure mode occurring. DFMEA teams usually rely on a 1 to 10 ranking scale. Failure modes with lower occurrence rankings have minimal chances of occurring, while those with higher numbers are almost certain to occur.
Step 8: Assign Detection Rankings to Each Failure Mode
As with severity and occurrence rankings, evaluate detection rankings on a scale of 1 to 10. Only this time, ask yourself: how likely are we to detect each of the identified failure modes before they occur?
The goal is to determine the effectiveness of your existing design controls in detecting problems before occurring. Lower detection rankings mean it’s highly likely your team will uncover issues. Alternatively, the higher the detection ranking the less plausible it is to foresee the failure mode occurring.
Step 9: Calculate Risk Priority Numbers (RPN)
Unfortunately, there are only so many hours in a day to devote to product development! Knowing your RPNs is key to determining which design problems team members should resolve first.
Give the failure modes with the highest RPNs top priority. After the ratings have been assigned, the RPN for each issue is calculated by multiplying Severity x Occurrence x Detection
Risk Priority Number Formula:
RPN = Occurrence × Severity × Detection
Step 10: Establish Corrective Actions
At this stage, you may have uncovered information that suggests the need for modifications to existing design processes. Establish an acceptable RPN for the failure modes and document your corrective actions. In addition, identify any tools you will need to lower your RPN.
Step 11: Implement Corrective Action Plan (Recalculate RPNs)
Once you’ve developed your action plan(s), it’s time to get to work! Get everyone on board and implement your product design action plan. At the end of your implementation period, recalculate the RPN to evaluate measurable progress.
Did your team manage to lower its occurrence and severity rankings? Did the detection ranking increase? When it comes to maintenance, asset management, and equipment inventory management, we recommend using a CMMS (computerized maintenance management system) like MaintainX to track your progress.
A user-friendly CMMS will streamline data management, save time with digital procedural checklists, and provide meaningful metrics that support effective O&M decision-making.
DFMEA Practice Example
Want to see what DFMEA looks like in action?
Check out this example of a DFMEA conducted for developing an automobile front door at a manufacturing plant compiled by ReliantSoft.
The next section will highlight some of the most common errors companies make when implementing both general and design failure mode and effect analyses.
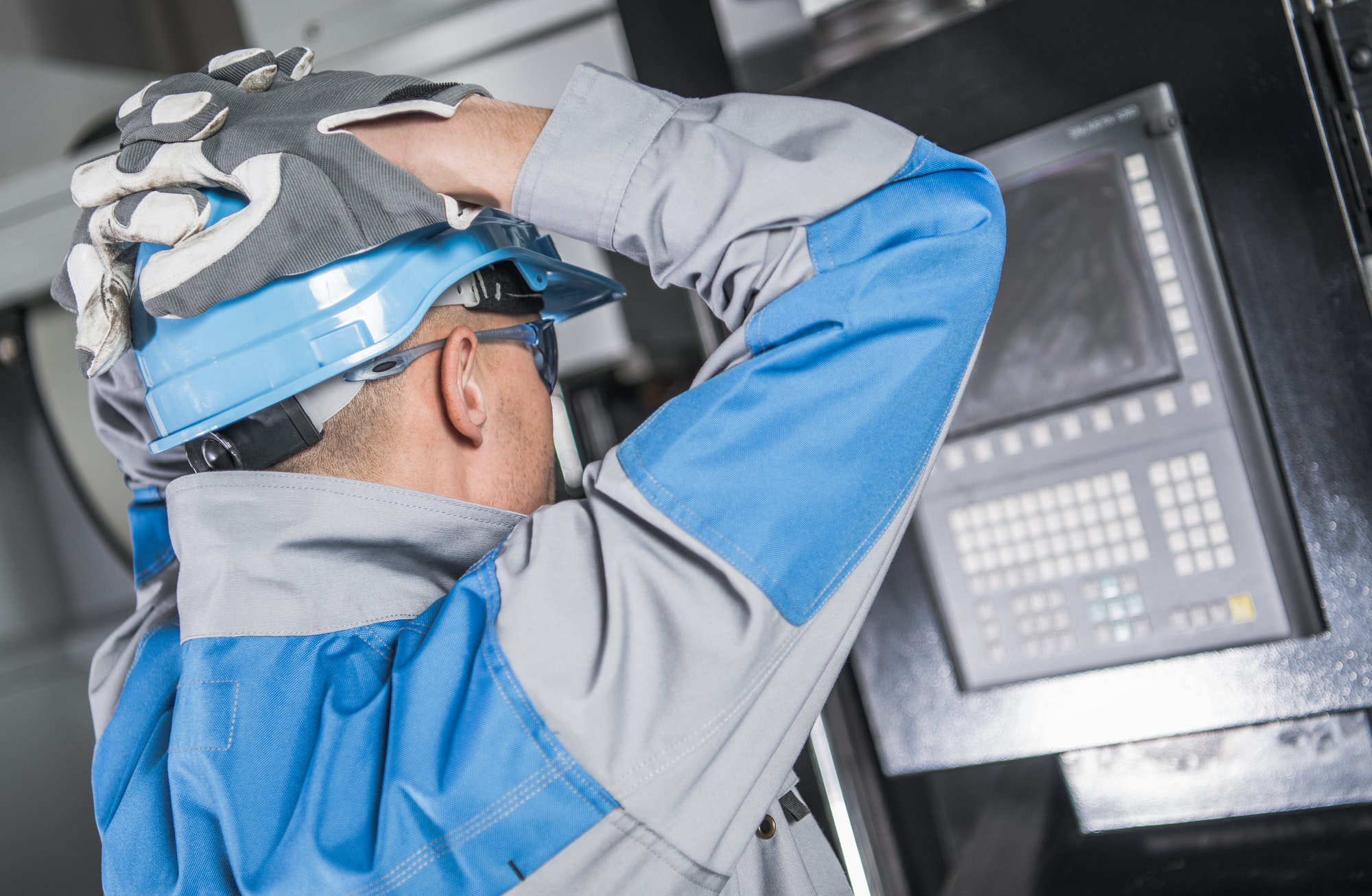
Common Mistakes Made with DFMEA
Below are some of the most common mistakes organizations make when first attempting FMEAs:
1. Don’t Integrate FMEA Types
Lack of FMEA integration is a common occurrence in many organizations. It’s not unusual for leadership to handle various FMEA projects in isolation despite significant overlap between roles and departments.
You can’t effectively perform DFMEA while ignoring process FMEA (PFMEA). PFMEA focuses on evaluating potential setbacks to operational processes that disrupt deliverables. It helps maintenance departments prioritize preventive maintenance (PM) by providing a method to measure varying consequences of asset breakdowns. PFMEA also can serve as a catalyst for decreasing production costs, eliminating production waste, and reducing downtime.
2. Incorrect FMEA Ownership
Another common beginner’s mistake is tasking quality control departments with complete ownership of DFMEA. This oversight is harmful because quality engineers aren’t typically the primary executors of the design and production processes under review.
They may lack first-hand knowledge about system details, design requirements, and how product development changes will ultimately impact end-users. For this reason, it’s wise to task the project to product designers and assign other department members supporting roles.
3. Incomplete Taskforces
Besides FMEA ownership, FMEA team composition is also often a major challenge for organizations. If you select the wrong people to make up the team, you’ll end up with ineffective risk mitigation measures. In fact, you may end up making things worse.
The FMEA team should always be made up of people knowledgeable about design and customer requirements and how to meet them. The primary department of the system should be included in the team.
4. Poor Timing
Unfortunately, it’s sometimes possible to do everything right but at the wrong time. How does one perform FMEA at the wrong time? They don’t think about FMEA until something goes wrong!
This can lead to organizations running FMEA just to complete the paperwork. It becomes another process to be met instead of proactively looking for ways to improve your systems and products.
Instead of making DFMEA an expensive afterthought, aim to complete the analysis during the product design phase. You can’t initiate PFMEA and System FMEA first, then complete DFMEA later. DFMEA comes first, followed by the others.
Streamline Asset Management with MaintainX
One of the easiest ways to organize equipment-related information is with MaintainX.
Our mobile-friendly platform allows operational teams to catalog, analyze, and act on crucial metrics to reduce the occurrence of production bottlenecks. With zero training, most workers feel comfortable creating, assigning, and monitoring work orders within minutes.
FAQs
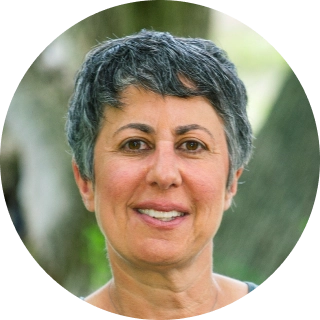
Caroline Eisner is a writer and editor with experience across the profit and nonprofit sectors, government, education, and financial organizations. She has held leadership positions in K16 institutions and has led large-scale digital projects, interactive websites, and a business writing consultancy.