Overall Equipment Effectiveness (OEE) is a manufacturing standard used to measure the productivity of facilities, processes, and equipment. OEE indicates how efficiently companies manage the production process by calculating asset availability, asset performance, and product quality.
Successful manufacturing plants consistently monitor several critical equipment parameters that contribute to operational performance. Overall Equipment Effectiveness (OEE) is one such metric that helps companies identify the percentage of productive manufacturing time.
OEE helps operational managers identify underlying losses, eliminate waste, benchmark progress, and improve manufacturing processes. Notably, Seiichi Nakajima, the pioneer of Total Productive Maintenance (TPM), established the metric in the 1980s.
Factors of Overall Equipment Effectiveness
Three primary factors drive manufacturing plant performance: product quality, availability, and performance efficiency. Organizations striving to achieve world-class OEE ratings should aim to score the following percentages within each category:
- Product Quality: Rating of at least 99 percent. Quality takes into account defects and includes parts that need reworking. A rating of 100 percent means that the facility never produces defects.
- Availability: Rating of at least 90 percent. Availability factors in both planned and unplanned downtime during production. A 100 percent score means a facility experiences no downtime during production.
- Performance Efficiency: Rating of at least 95 percent. For performance, small stops and slow cycles should be taken into account. Processes that run without any stops or slow cycles have a 100 percent score.
For example, a facility with a 100 percent OEE score always produces high-quality products with zero downtime. Alternatively, a facility with a 60 percent OEE score fails to meet quality standards 40 percent of the time.
“Lean process redesign helps companies streamline processes, eliminate waste, and foster a culture of continuous improvement. This versatile methodology applies well to short-cycle as well as long-cycle processes, transactional as well as judgment-based processes, client-facing as well as internal processes.”
McKinsey
Benchmarks for Overall Equipment Effectiveness
Besides being used as a baseline to track progress and eliminate production waste, OEE is also a benchmark for comparing the performance of given assets to other similar company assets, industry standards, and/or the results of different shifts for the same asset.
The benchmarks for OEE are:
- 100 Percent: Production is perfect, and the facility is only producing quality goods as fast as possible without any downtime.
- 85 Percent: A world-class rating for discrete manufacturers that produce itemized products such as automobiles, furniture, toys, and smartphones. Most organizations aim to achieve an 85 percent OEE rating in the long run.
- 60 Percent: A fair rating for discrete manufacturers with opportunity for improvement.
- 40 Percent: A low rating, but fairly common for manufacturers just beginning to track performance and take initiative to decrease downtime.
Ideally, maintenance experts recommend that organizations maintain a minimum OEE rating of 77 percent.
Benefits of OEE
Implementing an OEE strategy can help organizations to achieve their production targets. It gives them the flexibility to proactively tweak their processes in real time and reduce downtimes and costs while improving production capacity, quality, and efficiency. The benefits of OEE include:
- Better return on investment (ROI) for assets
- Increases competitiveness with minimized production losses
- Reduces maintenance costs with minimized unplanned downtime
- Maximizes employee productivity by allocating resources appropriately
- Enables organizations to visualize their performance and note areas to improve based on production data
When correctly implemented, OEE provides organizations with a deep understanding of their production processes. This information helps companies improve productivity and stay competitive within their industries. They also can maximize their ROI from assets critical to production.
How to Calculate Overall Equipment Effectiveness (OEE)
To calculate OEE:
OEE = Availability * Performance * Quality, where:
Availability = Run Time / Planned Production Time
Performance = Planned Production Time – Stop Time
Quality = Good Count / Total Count
The Three Primary Metrics of OEE
Availability
Availability is calculated by dividing the actual hours of operation by the full working shift. For instance, an asset that has an hour of planned downtime operates for a total of 7 hours in an 8-hour working shift. To calculate the asset’s availability, the organization divides 7 hours by 8 hours. Availability equals 87.5 percent.
Performance Efficiency
Performance efficiency is calculated by multiplying the number of processed units by the ideal cycle time for each unit and then dividing by the actual operation time. For instance, a facility that produces 440 units with a 0.5 minutes ideal cycle time for each unit in 420 minutes (actual operation time) has a performance efficiency rating of 52.38 percent.
Rate of Quality Products
This quantifies how many of the units produced meet the required quality standards. For example, if only 435 products out of 440 units produced are of acceptable quality, then the rate of quality products is 97.73 percent.
In the example above, the organization would have an OEE rating of 44.79 % — that is, 87.5 % x 52.38 % x 97.73 %.
How to Improve OEE
Organizations should always strive to improve their OEE rating. They can do this by reducing inefficiencies and losses in their processes. These six big losses affect the effectiveness of an asset:
- Equipment failures
- Equipment setups and adjustments
- Minor production interruptions (small stops)
- Reduced production speeds
- Defective products
- Rejects on startup
The first two losses affect availability, while the next two impact performance. The last two affect quality. Identifying and minimizing these losses will improve an organization’s overall OEE.
In the example above, the organization would have an OEE rating of 44.79 % — that is, 87.5 % x 52.38 % x 97.73 %.
Conclusion
Overall Equipment Effectiveness (OEE) is a key metric for organizations to measure production effectiveness and efficiency. The metric identifies underperforming assets and connects poor performance to availability, performance, and/or quality issues. This information provides useful insights for planning, scheduling, and conducting maintenance activities. In the long run, OEE helps optimize maintenance strategies and reduce costs. A robust CMMS will help you streamline your maintenance operations and oversee everything from work orders to quality management directly from both your mobile device and desktop.
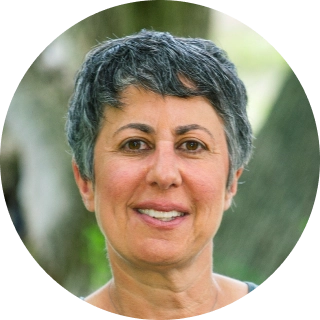
Caroline Eisner
Caroline Eisner is a writer and editor with experience across the profit and nonprofit sectors, government, education, and financial organizations. She has held leadership positions in K16 institutions and has led large-scale digital projects, interactive websites, and a business writing consultancy.
See MaintainX in action