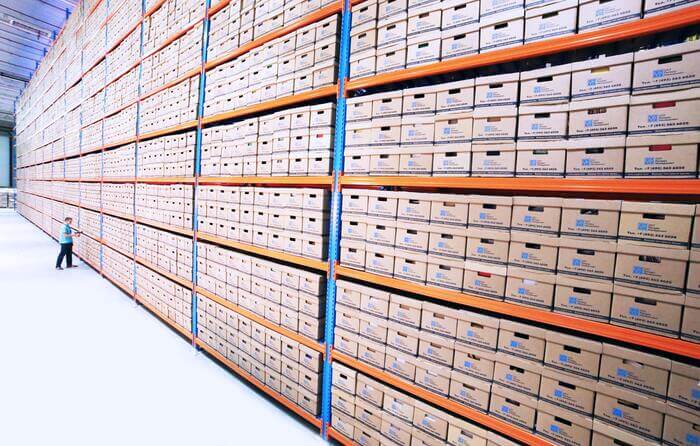
Customers are complaining because their orders sometimes arrive broken. One technician changes a filter in 30 minutes, while another takes an hour. Operational expenses are more expensive this month than last due to production errors.
Though these issues may seem unrelated, they likely have a similar cause. If your team struggles to produce consistent outcomes and maintain high-quality standards, you probably could benefit from writing Standard Operating Procedures (SOPs).
Standard operating procedures are documented instructions that detail routine, work-related tasks. Businesses of all types use written SOPs for many reasons, including maintaining stakeholder satisfaction, increasing efficiency, and decreasing costs. For example, eCommerce businesses often enforce SOPs to maintain quality-control standards while packing shipments. Fast-food restaurants routinely use them to provide consistent dining experiences across multiple locations. And large warehouses use standardization to achieve equipment reliability, maintain smooth production lines, and train new hires.
Regardless, the process for documenting work instructions is relatively the same. Before you even begin thinking about writing standard operating procedures, mapping flow charts, and evaluating SOP formats, it’s helpful first to strategize your approach. In this article, we’ll share eight quick tips that will change the way you think about creating SOP documents. These tips come from Taiichi Ohno, the father of Toyota Production System and the Lean Manufacturing framework’s creator.
No matter what type of business you run, the following tips can help structure business processes that produce more value with less work—something we can all appreciate. Use them as a starting point when planning new SOPs:
Writing Standard Operating Procedures to Reduce Downtime
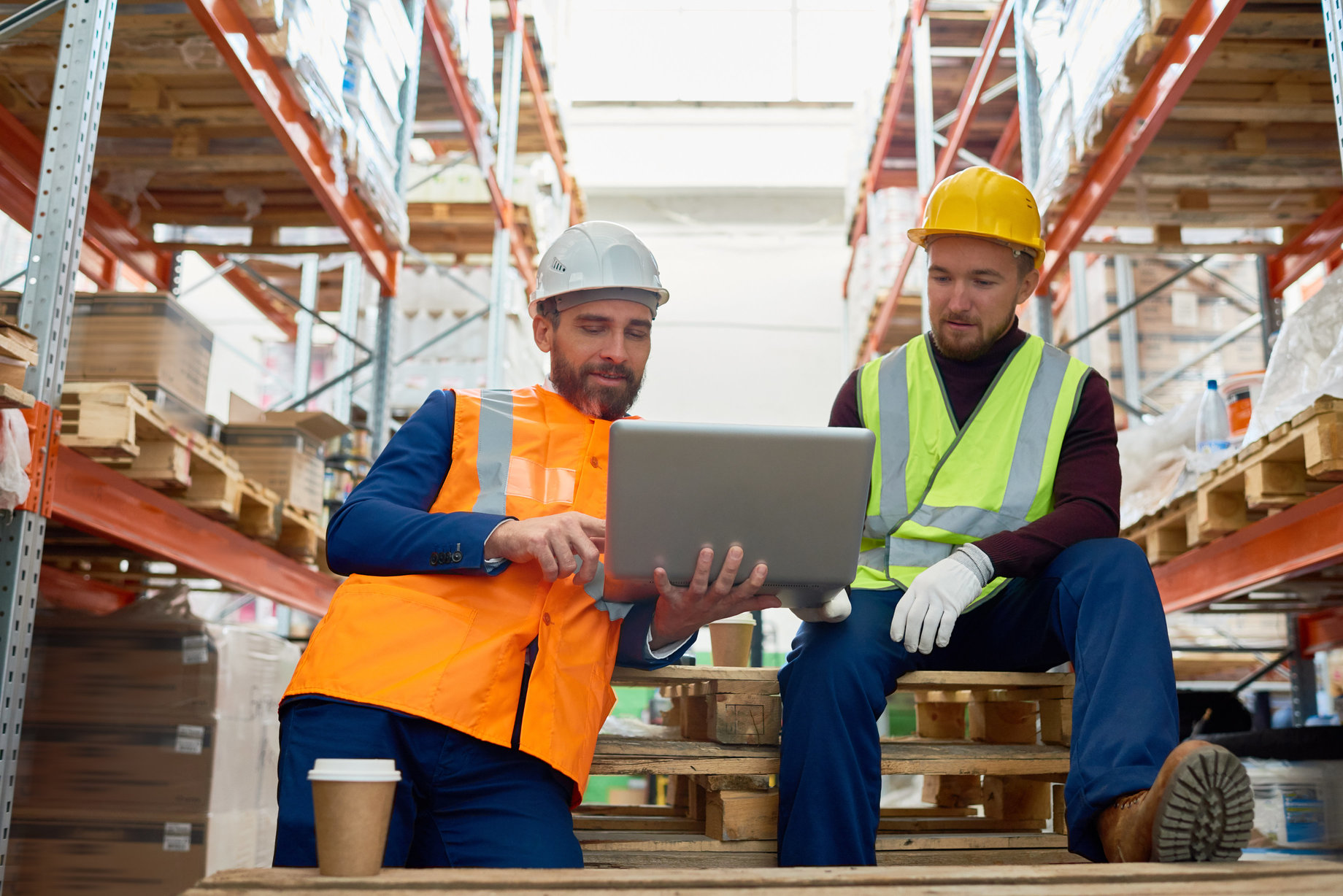
The Internet is full of tips, tools, and instructions for writing standard operating procedures. A quick Google search reveals no shortage of SOP templates, formatting instructions, and detailed steps for writing SOPs. Click here to read our Ultimate Guide to Streamlining O&M with SOPs.
However, what you won’t as easily find? Advice on how to think about SOPs. The key to writing effective SOPs involves answering a simple question: how can our team further reduce DOWNTIME?
According to Ohno, operational managers should write standard operating procedures with the primary goal of eliminating waste (i.e., Muda in Japanese). The executive divided organizational waste into eight categories conveniently represented by the acronym:
DOWNTIME
- Defects
- Overproduction
- Waiting
- Not utilizing talent
- Transportation
- Inventory excess
- Motion waste
- Excess processing
In the manufacturing world, the term, downtime, refers to the amount of time production stalls because of non-functioning equipment. However, downtime can also represent any time wasted in an organization’s production cycle. Use this methodology to identify opportunities to eliminate these eight types of waste with new processes:
1. Eliminate Defects
As expected, the nature of defects varies by industry and task. For McDonald’s, a defect could be a squished hamburger bun or a malfunctioning fryer. For a manufacturing facility, a fault may involve a malfunctioning conveyor belt part. Think about the specific types of defects your team could avoid by eliminating poor quality assurance, insufficient documentation, lousy repair jobs, and missing processes.
Once you’ve identified common sources of troubleshooting, consult with the involved employees to determine where exactly things are falling apart in the production or service process. While eliminating all forms of waste is impossible, you can minimize defects by writing more precise standard operating procedures.
2. Stop Overproduction
No matter the type of goods your company sells, overproduction is bad business. Managers who assign workers routine tasks with no instructions for stopping overproduction are at risk of wasting resources on unnecessary products. Such oversights may prevent the organization from spending capital on more essential projects.
Overproduction most commonly happens in response to unclear customer demands, inaccurate forecasts, engineering changes, and poorly applied automation. When writing standard operating procedures, consider implementing workflows designed to eliminate the potential for overproducing.
3. Minimize Waiting
Most of us don’t enjoy waiting around for something to happen, and it’s incredibly frustrating when facing deadlines. Work can halt for several reasons. To some degree, waiting is inevitable. Outsourced repair technicians sometimes get stuck in traffic, vendors don’t always return phone calls, and Internet connections can go down.
Common causes of waiting include insufficient staffing, poor communication, work absenteeism, unbalanced workloads, and unplanned downtime. With that said, you can put systems in place to minimize wait times. Think about what actions you can build into your SOPs to mitigate common delays in your unique organization.
4. Stop Under-Utilizing Talent
Another common cause of productivity waste is under-utilizing workers’ talents, skills, and knowledge. Common catalysts of under-utilizing talent include assigning wasteful administrative duties, insufficient new employee onboarding, and poor communication.
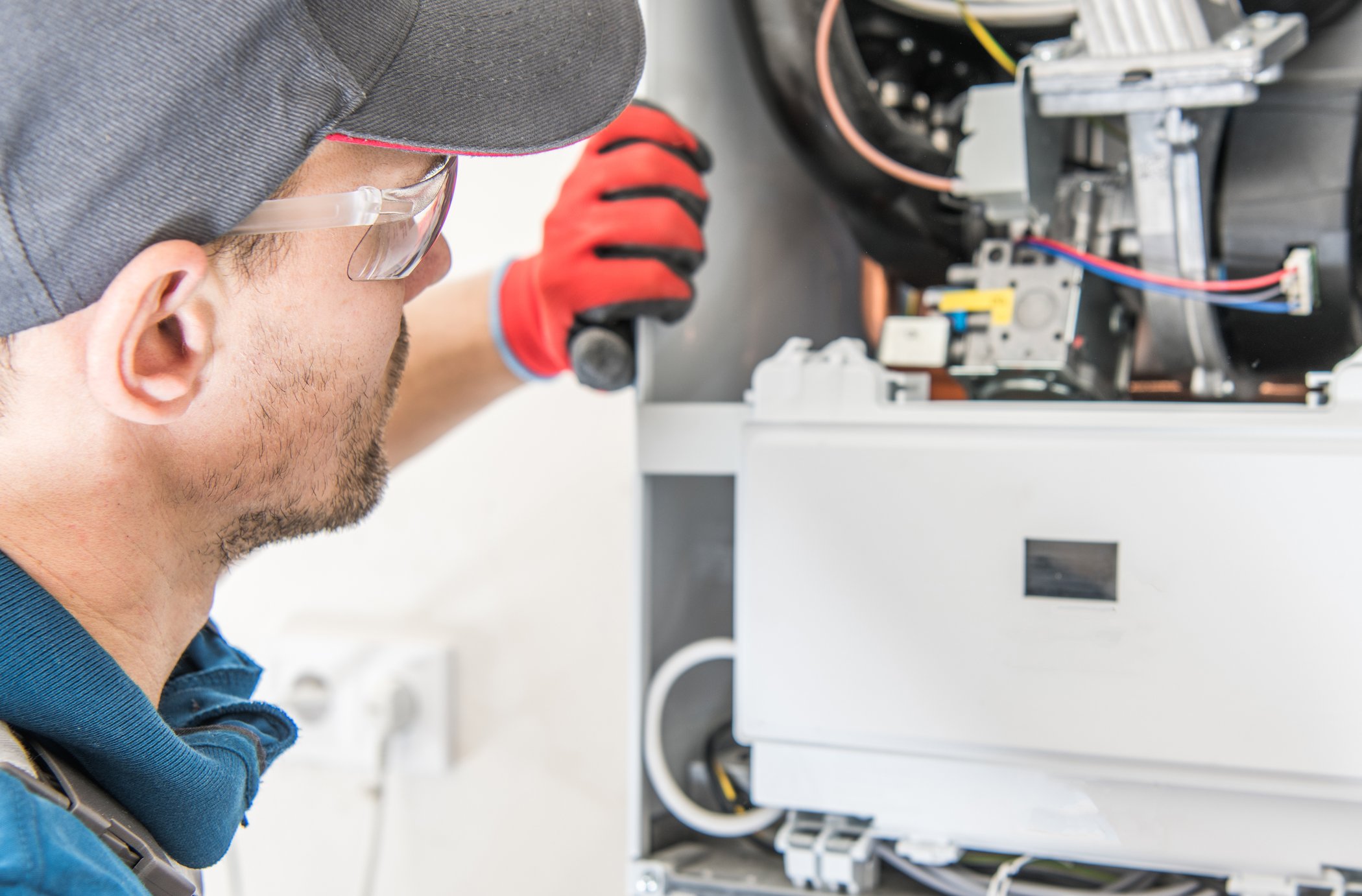
Sadly, the underutilization of talent can also foster employee disengagement. According to a Udemy study, 43 percent of workers admitted to being bored at work. The same survey found that bored workers were twice as likely to quit their jobs over the next six months. Consider implementing standard operating procedures to periodically assess employee skill levels, job satisfaction, and other talent-related benchmarks.
5. Eliminate Unnecessary Travel
The most apparent form of wasteful travel includes unnecessary vehicle trips taken to transport or pick up items. This category also includes inefficient routes and travel times that cause employees to sit in traffic.
Managers should adjust SOPs to include simplified processes, handling unnecessary products less often, and taking shorter trips. For large warehouses, changing physical facility layouts can positively impact productivity.
6. Streamline Inventory Systems
Similar to overproduction, overstocked inventory closets tie up capital gains if they are disorganized. Additionally, overly abundant supplies create a facade that customer demand is more significant than it is. If your organization has struggled with inventory management, you may need a better system for monitoring inventory levels.
Consider creating step-by-step instructions to address mismatched production speeds, long set-up times, misunderstood customer needs, and unreliable suppliers.
7. Reduce “Motion Waste”
Unnecessary travel doesn’t only happen by vehicle. It also occurs by foot and hand. Extra process steps, poorly designed systems, and misaligned workflows contribute to wasted motion within a place of business.
Managers should strive to eliminate excess movement, whether by employees or machines. Common culprits of motion waste include crowded workstations, poor workstation layouts, poor process designs/controls, and siloed operations. Rearranging layouts and workflows to decrease distance can pay huge dividends.
8. Remove Excess Processing
Finally, look for opportunities to eliminate extraneous procedures that don’t add value. Examples of excess processing include requiring workers to get multiple signatures on reports, entering the same data into more than one database, and engaging in extraneous steps that aren’t needed to deliver high-quality output.
Excess processing increases costs, wastes time, and can weaken employee morale. Remove extra processing by mapping your organization’s procedures and talking with those involved about how they can be more efficient.
Reduce DOWNTIME with SOPs
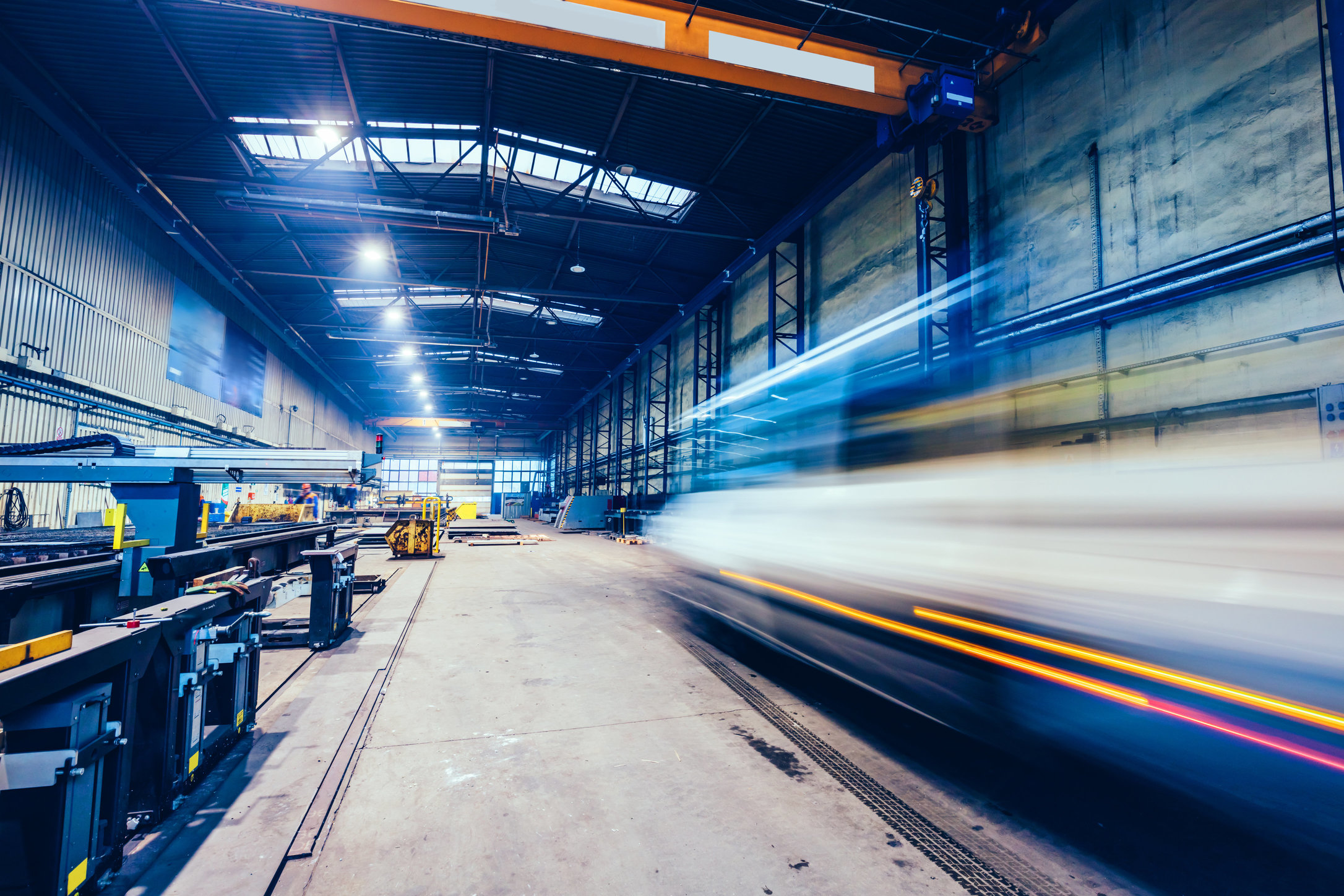
Writing standard operating procedures isn’t a one-time thing. Managers need to revisit them consistently as workplaces evolve. SOPs for quality control, regulatory requirements, and health and safety require routine updates to stay relevant.
We hope you’ll refer to the acronym DOWNTIME when writing your next round of SOPs. Eliminate the eight types of waste in your processes to maximize efficiency, increase productivity, and enhance job satisfaction.
Want to streamline process management even further? MaintainX allows teams to create, fulfill, and monitor digitized SOP checklists from their smartphones in real time. Our Computerized Maintenance Management System (CMMS) also users to:
- Create reusable SOP templates with hierarchical checklists
- Create, assign, and track recurring work orders
- Organize assets, parts, and inventory data
- Instant message team members
Click here to download MaintainX’s Basic Plan for free.
FAQs
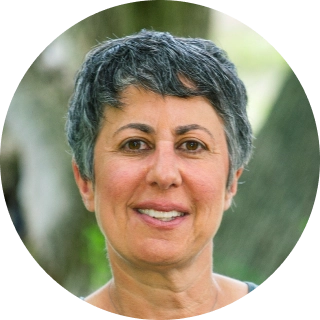
Caroline Eisner is a writer and editor with experience across the profit and nonprofit sectors, government, education, and financial organizations. She has held leadership positions in K16 institutions and has led large-scale digital projects, interactive websites, and a business writing consultancy.