Both run-to-failure maintenance and breakdown maintenance are forms of corrective maintenance that occur after a piece of equipment has malfunctioned. Corrective maintenance is the opposite of preventive maintenance (PM). Preventive maintenance is the practice of performing equipment inspections, parts replacements, and upkeep regularly to reduce the likelihood of failure.
Run-to-Failure vs. Breakdown Maintenance
Run-to-failure maintenance is the world’s simplest maintenance strategy.

The practice involves deliberately allowing assets to operate until they fail, and only then performing necessary maintenance tasks to restore functionality.
Run-to-failure maintenance should not be confused with neglecting a piece of equipment until it fails; it involves a deliberate plan for remedial actions to be taken post-breakdown. Organizations of all sizes intentionally practice run-to-failure maintenance on non-critical assets that don’t impact productivity because it’s more cost-effective in the long run.
When Is Run-to-Failure Maintenance Used?
Run-to-failure maintenance is often used on:
- Redundant assets
- Non-critical machinery
- Assets with short lifespans
- Assets with low financial value
- Assets that are unlikely to fail
- Assets in which repairs aren’t feasible
- Single-use and inexpensive assets or parts
- Assets with random failure patterns that are difficult to anticipate
- Assets that aren’t subjected to statutory maintenance requirements
In these instances, run-to-failure maintenance saves capital by eliminating the associated expenses of regular maintenance activities.
Examples of Run-to-Failure Maintenance
Run-to-failure maintenance is commonly used in the space industry. Because satellites in the night sky are beyond human reach, performing preventive maintenance isn’t cost effective. Consequently, satellites are built to “run to failure.”
However, companies sometimes allow run-to-failure maintenance on pieces of equipment critical to continuous production rather than disrupting production now and then. In such cases, the company realizes that letting the machine break down—which might happen once in its lifetime—makes more financial sense than bringing the machine down for routine maintenance.
What Is Breakdown Maintenance?
Breakdown maintenance refers to maintenance tasks performed on faulty, broken-down, or inoperable equipment. However, unlike run-to-failure maintenance, breakdown maintenance is sometimes seen as unavoidable, undesirable, and inconvenient.
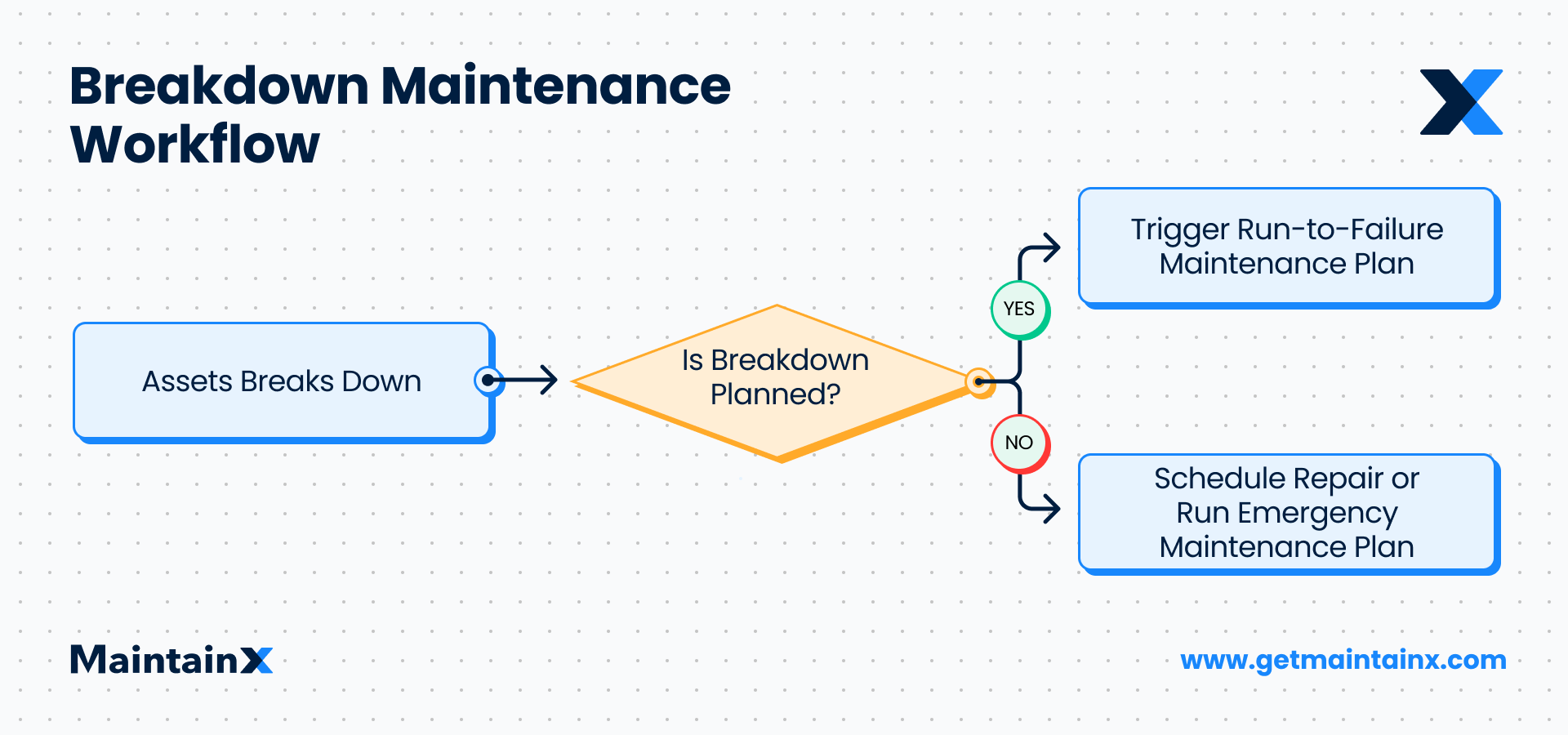
There are two types of breakdown maintenance:
- Planned Breakdown Maintenance: Here the organization expects an asset breakdown to happen and prepares for the eventuality. Once the breakdown occurs, the technician operates from a controlled, well-documented procedure. In other words, there are no surprises or questions about what to do.
- Unplanned Breakdown Maintenance: Alternatively, when equipment fails unexpectedly, and there are no planned breakdown procedures in place, the event causes unplanned downtime. The facility may lose time, money, and productivity due to extended downtime.
What Are the Disadvantages of Breakdown Maintenance?
Neither type of breakdown maintenance should be practiced in situations where safety is a concern. For example, the aviation industry cannot rely on breakdown maintenance for airplane malfunctions because it puts passengers in danger. Other disadvantages of breakdown maintenance are:
- Faster plant deterioration.
- Hurried maintenance jobs that lead to poor execution.
- Longer repair times compared to other maintenance types.
Breakdown maintenance is unavoidable in most industries, and planned breakdown maintenance is always a useful strategy.
Examples of Breakdown Maintenance
Assets that are inexpensive and easy to replace are the best candidates for breakdown maintenance. Examples include:
- A homeowner replacing light bulbs after they burn out.
- A hotel general manager replacing hand tools after a year’s wear and tear.
- A water company replacing high-flow pumps with short lifespans.
Deploying preventive maintenance on such assets is wasteful because they tend to outlive their usefulness within short periods, are easily replaced, and don’t majorly impact operational functionality.
Differences between Run-to-Failure and Breakdown Maintenance
Run-to-failure maintenance is a more specific and detailed version of breakdown maintenance. What makes breakdown maintenance more versatile than run-to-failure maintenance is that it also includes unplanned downtime events.
Because it’s more general, organizations use breakdown maintenance on all types of assets. Conversely, run-to-failure maintenance is only used on disposable, short-life, and non-critical assets, as it requires careful planning and documentation.
Here are the differences at a glance:
When to Use Run-to-Failure vs. Breakdown vs. Preventive Maintenance
Though preventive maintenance (PM) has been proven to enhance equipment reliability and decrease costs, it’s not an ideal strategy for every asset. In fact, proactive maintenance may be an unnecessary expense for non-critical machinery. Surprisingly, it’s sometimes more cost-effective to wait for an asset to fail than to assign technicians to visit machinery, inspect it, and replace cheap parts before they fail—this is where run-to-failure vs. breakdown maintenance comes into play.
As a rule, when the associated costs of equipment failure are negligible, and the productivity consequences minimal, avoid preventive maintenance. However, you may be wondering: Is run-to-failure maintenance the same as breakdown maintenance?
While both corrective maintenance methods revolve around fixing problems post-failure, they hold slightly different intentions.
Other Frequently Asked Questions
What Are the Four Types of Maintenance?
An organization’s productivity depends on its maintenance strategy; different assets require different strategies to run smoothly. Here are four main types of maintenance strategies used by organizations across industries:
- Corrective Maintenance: Also known as reactive maintenance, this term refers to maintenance tasks performed after problems occur. Both run-to-failure and breakdown maintenance fall into the parent category of corrective maintenance.
- Preventive Maintenance (PM): The main goal of preventive maintenance is to keep assets in good order and reduce unplanned downtime. PM includes common tasks such as lubrication, cleaning, adjustments, and parts repairs or replacements before failure occurs.
- Predictive Maintenance (PdM): Predictive maintenance involves using sensor devices to monitor the condition of assets in real time. The sensor data connects with CMMS software to alert management when to service equipment to avoid breakdowns.
- Condition-based Maintenance (CBM): Here, maintenance tasks are performed based on asset conditions. The goal of CBM is to perform maintenance at the moment before an asset fails.
What Is the Difference Between Corrective and Breakdown Maintenance?
Both breakdown maintenance and run-to-failure maintenance are forms of corrective maintenance. However, as we have discussed in this article, there are some key differences between planned run-to-failure maintenance and unplanned (breakdown) maintenance. With that said, the terms are often used interchangeably.
So Which Is It: Run-to-Failure vs. Breakdown Maintenance?
As you can see, there are several similarities between run-to-failure and breakdown maintenance. Though different in intent, both run-to-failure and breakdown maintenance entail fixing problems after they occur. These strategies can minimize maintenance costs, especially for non-critical assets that don’t require preventive maintenance. However, proper planning and documentation should be used to avoid safety hazards, expenses, and inconveniences associated with unplanned breakdown maintenance.
MaintainX: Reenvisioning How Maintenance Works
MaintainX is a cloud-based CMMS maintenance software designed with convenience, affordability, and security in mind. Users can sign-up, log in, and begin creating worfklows and WOs immediately from their desktop or mobile devices.
See MaintainX in action