P-F Curve Definition
A P-F curve is an X-Y-axis graph used to visualize equipment health over time. Maintenance managers use P-F curves to identify potential causes of equipment failure.
During the 1970s, engineers Stanley Nowlan and Howard Heap developed the P-F curve to help United Airlines and the U.S. Defense Department cut O&M losses and reduce aircraft downtime. Since then, manufacturing teams have applied the tool to a variety of equipment situations when determining effective approaches to maintenance.
The P-F curve is an important component of reliability-centered maintenance (RCM), a framework used to determine the most cost-effective times to perform maintenance work. RCM emphasizes matching individual assets with the maintenance techniques most likely to enhance reliability, uptime, and savings. Advanced maintenance teams use P-F curves to visualize the deterioration processes of highly critical pieces of equipment. This allows them to predict the ideal frequency of necessary repairs.
How P-F Curves Work
Equipment failure is sometimes random, unpredictable, and caused by several factors. The longer the P-F interval, the more time maintenance personnel have to detect failure before it occurs. Maintenance technicians can prolong the P-F interval by conducting PM inspections at ideal intervals.
The P-F curve includes three primary elements:
- Point P = Potential Failure: An identifiable physical condition that indicates a functional failure is imminent.
- Point F = Functional Failure: The inability of an item (or the equipment containing it) to meet a specified performance standard.
- The P-F Interval: The time difference between an asset’s potential failure and predicted functional failure.
It’s worth mentioning Point P has mistakenly become the primary focus for many organizations over the years. This is problematic because the failure mode that caused Point P has already happened. Thus, maintenance teams wishing to maximize the value of the P-F curve must ask themselves: why did Point P occur to begin with? With that said, it’s important to remember that Point F does not represent absolute failure, but functional equipment that is no longer performing optimally.
Maintenance Techniques Used to Maximize the P-F Interval
Maintenance personnel use different techniques to determine the condition of an asset. The choice of technique depends on the type of asset and its identified failure modes. The most common techniques used to maximize the P-F interval include:
- Visual inspections
- Process control instrumentation (measurements and trending)
- Process parameter trending, such as temperatures, pressures, rates, and flows
- IR thermography
- Vibration measurement and analysis
- Acoustic emissions detection, such as ultrasound
- Motor current analysis
- Corrosion monitoring
- Lubricant sampling and analysis
These techniques are complex and require extensive training and expertise. While reliability-centered maintenance is complicated, organizations that employ reliability engineers to implement RCM greatly minimize maintenance costs and optimize asset functionality. RCM is achievable as long as the information from the P-F curve is correctly deployed.
According to the Plant Engineering Maintenance Study, up to 24 percent of facilities use RCM as their primary maintenance strategy. But the biggest challenges organizations face when trying to improve maintenance are a lack of resources and staff, limited understanding of new maintenance technologies, and insufficient training.
Uses of P-F Curves
Maintenance teams rely on the P-F curve to monitor the deterioration of an asset. But for the P-F curve to be effective, organizations need historical data on the asset’s failure modes. The following maintenance processes use the P-F curve:
- Scheduling Efficient Maintenance: The P-F curve allows maintenance professionals to schedule maintenance tasks just before failure occurs. It helps avoid over-maintenance on a given piece of equipment and reduces maintenance costs while increasing asset uptime and extending its lifespan. Historical data informs maintenance decisions.
- Understanding Risk Severity over the Asset Lifecycle: Historical data and knowledge about an asset reveal levels of risk as an asset moves through its lifecycle. Maintenance teams can tell how severe a risk is if they know when a potential failure and a functional failure occur. Identifying the risk severity of an asset on the P-F curve helps teams prioritize maintenance tasks depending on the severity of a risk.
- Maximizing an Asset Lifecycle: The P-F curve enables maintenance teams to determine when it’s best to replace an asset. Therefore, organizations can maximize and extend an asset’s functional life and then replace it just before it reaches functional failure. Indicators alert maintenance personnel when failure is about to occur or has already occurred. These indicators inform the decision on asset replacement. The indicators can precede failure, stem from failure that has already occurred, or even occur simultaneously with failure. The indicators depend on the type of asset in question. Organizations need to perform a criticality assessment to determine which assets should be placed under watch depending on business goals.
- Planning Effective Maintenance: By identifying failure modes and knowing when an asset is likely to fail, maintenance professionals can organize the necessary maintenance resources early. They can determine which maintenance tasks will need specialized expertise and negotiate agreements with third-party contractors in advance. They also have the time to source high-quality replacement parts as compared to shopping last minute.
The P-F curve enables organizations to find a balance between different maintenance strategies. They can determine when predictive and condition-based maintenance approaches are required and when to rely on corrective maintenance. For instance, only 10 percent of assets can be run to failure. In fact, 60 percent need preventive maintenance, while 30 percent may need predictive maintenance.
Variability Factors of the P-F Interval
The P-F curve is integral to reliability-centered maintenance. But factors can cause identified failure modes to vary. They include:
- Equipment Design: Different types of equipment are designed with different levels of safety. Some pieces of equipment are designed to be able to cope with overloads, while others are not. The design margins can cause variations in the failure modes.
- Equipment Use: It’s also important to consider the context in which a piece of equipment is operated. Is the piece of equipment being operated in line with the product’s initial design purpose? Other factors, such as high start/stop cycles and periodic impact loading, also can affect the PF Interval.
- Random External Events: Random external events, such as errors during installation, operation, or maintenance, can affect the functionality and lifespan of a component or an entire asset. Operator error accounts for up to 12 percent of unexpected downtimes. Organizations can take steps to protect assets against such events. This includes ensuring that operators and maintenance personnel are adequately trained.
- Process Variability: It’s also important to consider how large and frequent load variations occur on a piece of equipment.
- Equipment and Component Variability: When organizations source for cheaper replacement parts, they risk causing a variation in the asset’s quality or components. This can shorten the P-F interval and leave little time to respond to potential failure. There’s also the risk of recurring failures.
It’s important to watch out for these factors. They can have a significant effect on the warning time provided by a particular alarm level.
Conclusion
The P-F curve is useful to determine when and how to address asset failure. But it requires organizations first to identify the various failure modes associated with an asset and know how the assets operate. When properly implemented, it can help organizations perform maintenance only when necessary and reduce the time to repair.
Use MaintainX to help address asset failure. Robust reporting features on our CMMS system help reduce maintenance costs, minimize unplanned downtime, and prolong the lifespan of an asset. With this, maintenance workers can plan, prioritize, and execute maintenance tasks efficiently and effectively. If that sounds interesting, try MaintainX today. Our goal is to make work smarter, not harder.
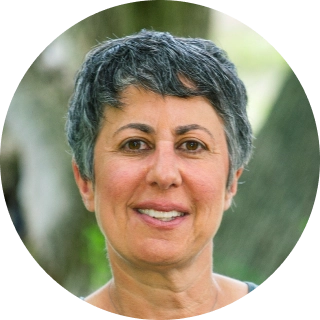
Caroline Eisner
Caroline Eisner is a writer and editor with experience across the profit and nonprofit sectors, government, education, and financial organizations. She has held leadership positions in K16 institutions and has led large-scale digital projects, interactive websites, and a business writing consultancy.
See MaintainX in action