Reliability engineers identify and manage risks that can affect asset reliability and business operations. They focus on risk management, loss elimination, and lifecycle asset management. Reliability engineers aim to reduce the cost of failure by minimizing system downtimes. They ensure that plant operations run effectively and efficiently.
What Do Reliability Engineers Do?
These professionals assess the reliability of organizational assets and identify areas that need improvements, such as equipment operation and maintenance. While it’s impossible for organizations to completely eliminate equipment failure, reliability engineers seek to identify and reduce the probability of failures and their effects.
Reliability Engineer Responsibilities
The responsibilities of a reliability engineer include:
- Developing Failure Mode and Effects Analysis (FMEA) processes for new and existing assets
- Performing data analysis to predict and curb failures before they occur
- Planning performance evaluation tests to determine potential production and safety risks
- Performing Root Cause Analysis (RCA) for recurring failures and recommending corrective action
- Collaborating with maintenance teams to develop proactive maintenance strategies that enhance asset reliability
- Working with project engineers to ensure the maintainability and reliability of newly installed and modified equipment
- Ensuring adherence to the Life Cycle Asset Management (LCAM) process
- Participating in the development process for the design and installation of custom machine specifications
- Providing technical support to other teams, such as production and maintenance
- Working with the production team to ensure asset utilization and overall equipment effectiveness (OEE)
"To capture everything digital can offer in increasing reliability and reducing costs, companies should boost their digital-maintenance ambitions."
McKinsey
Reliability Engineer Skills
Reliability engineers do more than work through technical mechanical problems. The profession encompasses everything from the conceptual stage of asset design to the inevitable replacement of machinery. Additionally, these workers are responsible for addressing potential risks and failure modes to optimize asset utilization.
For these reasons, they should possess a number of skills, including organizational, communication, leadership, problem-solving, critical thinking, and analytic abilities.
Some of the most important skills include:
- Demonstrated knowledge of statistical, mathematical, and engineering concepts
- Experience using statistical and probability methods and tools
- Critical and problem-solving skills
- Logical thinking
- Exceptional organizational and communication skills
- Proven leadership skills
- Ability to multitask and prioritize workloads
- Knowledge of engineering concepts such as lifecycle asset management, risk management, configuration management, and loss elimination
Reliability engineers can use CMMS maintenance software to solve maintenance challenges and reduce downtime. Robust CMMS like MaintainX provides work order and asset histories, as well as real-time inventory counts.
Types of Reliability Engineers
There are three primary types of reliability engineers.
Manufacturing Plant Reliability Engineer
Identifies and manages risks associated with assets and systems that can impact business operations. Their goal is to maximize asset uptime while reducing maintenance costs and production losses. Manufacturing plant engineers use RCA, FMEA, criticality analysis, and critical spares analysis to improve asset dependability.
Reliability Design Engineer
Evaluates product designs to ensure predictable performance. Their responsibilities include planning and implementing life tests, drafting test reports, performing design FMEA, and ensuring reliability risk mitigation.
Site Reliability Engineer
Oversees system automation and integration to improve the reliability of large systems, often relying on software development skills.
Organizations That Rely on Reliability Engineers
As businesses grow and the scope of production increases, there’s an increased risk of encountering equipment failure. Large production facilities need a reliability engineer to ensure that critical assets for production and safety perform at peak levels. For such organizations, asset breakdowns can have adverse effects on operations, productivity, and safety.
An in-house engineer enables organizations to proactively identify and manage various asset risks. They’re able to ensure that each asset contributes as it should to the organization’s overall performance. Industries that need reliability engineers include manufacturing, aerospace, scientific research, military, mining, utility systems, and transportation, among others.
Reliability engineers promote a culture in organizations of informed and data-driven decision-making. They work with various departments and maintenance teams to get an accurate view of the state of operations and how to improve it.
What Is the Difference between Reliability Engineers and Maintenance Engineers?
Both reliability engineers and maintenance engineers look to optimize the performance of organizational assets. They both ensure that pieces of equipment operate according to the planned schedule over their lifecycle, and unexpected downtimes are taken care of effectively and quickly. However, there are fundamental differences between the two roles.
Reliability Engineers
Reliability engineers develop FMEA processes to identify potential risks and recommend how to take care of them before they occur. This helps to improve asset reliability and production. Maintenance engineers are only involved when asset maintenance is required. Reliability engineers are concerned with the long-term operation of an asset. They’re involved in the entire asset lifecycle from installation through replacement. The primary goal of reliability engineers is to proactively enhance asset performance.
Maintenance Engineers
Maintenance engineers’ primary goal is to minimize asset downtimes by restoring them to operating conditions after a breakdown. They also ensure proactive maintenance strategies are in place to prevent unexpected breakdowns.
But it’s important to note that both groups work together to improve asset availability and overall production. They aim to increase the organization’s bottom line by ensuring that assets are in excellent working order.
Job Outlook
How much does a reliability engineer make? As expected, salary varies depending on factors like location, education, experience, and performance. According to ZipRecruiter, the average salary in the US is $117,820 /year, which is about $57/hour.
The U.S. Bureau of Labor Statistics doesn’t provide specific job outlook projections for professionals. However, it predicts network architects, which includes reliability engineers, to grow 5 percent by 2029.
Certifications and Training
Reliability engineers pursue specialized training to work with complex pieces of equipment. Most companies require a bachelor’s degree in engineering and entry-level experience for employment.
However, some technical institutes also provide apprenticeship programs that give candidates adequate training. Depending on the industry and organization, the specific maintenance and operational knowledge required varies. Also, licensing requirements vary from state to state.
The most popular training and certification programs for the positions include:
- Certified Reliability Engineer (CRE): Offered by the American Society for Quality (ASQ), CRE certification is awarded to reliability engineers who have demonstrated technical knowledge in the discipline. CRE is an exam-based program that tests one’s knowledge of numerical and analytical concepts of reliability engineering.
- Certified Maintenance & Reliability Professional (CMRP): The Society for Maintenance and Reliability Professionals (SMRP) offers this certification to test management and leadership skills along with practical knowledge.
- Certified Reliability Leader (CRL): Offered by the Association of Asset Management Professionals (AMP), the CRL focuses on the added components of social responsibility, economic prosperity, and environmental sustainability. The exam-based certification also tests the candidate’s knowledge of asset condition management, reliability leadership, maintenance, work execution management, and asset management.
The Mobius Insitute’s Asset Reliability Practitioner and certifications from the International Council for Machinery Lubrication may also be appropriate.
Ready to move your new standardized and efficient processes online? Try MaintainX for free.
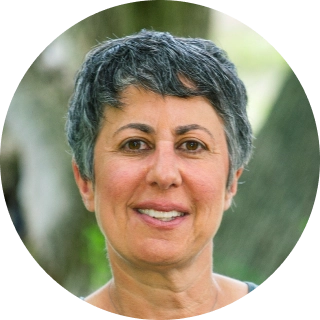
Caroline Eisner
Caroline Eisner is a writer and editor with experience across the profit and nonprofit sectors, government, education, and financial organizations. She has held leadership positions in K16 institutions and has led large-scale digital projects, interactive websites, and a business writing consultancy.
See MaintainX in action