A maintenance planner organizes the resources needed by maintenance technicians to complete work orders.
These workers are mostly found in manufacturing plants, planning preventive maintenance (PM) activities based on their priority levels. They also manage inventories to ensure tools and replacement parts are available when needed. Assets involved in maintenance and work orders are then documented within the computerized maintenance management system (CMMS).
Additionally, maintenance planners coordinate plant-wide shutdowns, consult with third-party contractors, and ensure everything runs smoothly when critical maintenance is performed. They also schedule tasks to minimize production downtimes.
What Do Maintenance Planners Do?
The most important aspect of this role is to increase asset reliability and identify improvements to eliminate maintenance roadblocks, improve efficiency, and reduce downtime.
Thus, the best maintenance planners usually have years of first-hand experience performing maintenance tasks themselves. This gives them insight into how to plan and prioritize maintenance tasks. Important skills for them to have include:
- Ability to work under minimal supervision.
- Leadership skills.
- Computer literacy.
- Organizational skills.
- Knowledge of various CMMS software.
- Proactive and able to prioritize tasks.
- Project planning and execution skills.
Additionally, maintenance planners must form close working relationships with everyone within their department—from the technicians who execute the assigned work orders to the plant managers responsible for meeting production targets—to succeed.
Social skills are as important as technical skills because conflicts about the criticality of maintenance tasks arise.
Organizations That Use Maintenance Planners
As previously mentioned, most maintenance planners work in manufacturing plants. Large organizations with a wide range of assets are most likely to benefit from a maintenance planner’s strategic input. Without a specific task planner, complex organizations run the risk of delaying maintenance tasks, which can lead to increased equipment failures and a backlog of repairs.
Organizations that already have a backlog need maintenance planners to prioritize work orders to move from reactive to proactive maintenance. Prioritization is usually based on how critical the asset is, the availability of resources, and the maintenance costs for each asset.
In large organizations, it’s impossible for the maintenance planner to also schedule maintenance tasks. Such organizations need to hire a maintenance scheduler. However, smaller organizations with limited assets can have the maintenance planner also schedule maintenance activities. They can perform both maintenance planning and scheduling without affecting work order prioritization.
Maintenance Planner Job Outlook
The U.S. Bureau of Labor Statistics categorizes maintenance planners under the broader category of administrative services managers. The category is projected to grow by 7 percent by 2028. However, with an expected annual compound growth rate of 2.1 percent in the manufacturing sector, demand for maintenance planners specifically could even be higher.
Maintenance planners earn an average of $69,734 per year, according to ZipRecruiter. However, depending on several factors, such as experience and location, the salary can be as low as $25,500 and as high as $102,500.
Certifications and Training
Maintenance planners require at least a high school diploma or GED certificate for employment. Some planners also have associate’s, bachelor’s, and master’s degrees. However, most job descriptions require at least five years of experience in maintenance and repairs.
Additionally, applicants are asked to have a working knowledge of common facility equipment like pumps, air handlers, air compressors, and HVAC systems. Filling out detailed reports on the aforementioned equipment is part of the job.
Additionally, it’s recommended that maintenance planners understand basic financial concepts such as estimating and budgeting repair costs. Training and certification programs are available to aspiring maintenance planners who want to advance their careers. The most common certification programs for the role include:
- Certified Maintenance Planner: Offered by Milford University, for example, this program covers maintenance planning areas such as maintenance work processes, project management, performance management, financial evaluation, planning, logistics theory and practice, and influencing and communicating.
- Certification Maintenance: Offered by the American Institute of Certified Planners (AICP), this program aims to help maintenance planners upgrade their knowledge and skills to current industry best practices.
Institutions, such as TPC Training, offer training programs and seminars for maintenance planners.
Other FAQ
How Much Money Does a Maintenance Planner Make?
In 2020, maintenance planners earned an average of $30 per hour, according to ZipRecruiter. However, maintenance planners in cities such as San Francisco, Fremont, and San Jose earn higher than the national average.
What Tools Does a Maintenance Planner Need?
Maintenance planners plan and, in some cases, schedule maintenance tasks. They must be comfortable using CMMS software and adapting to new technologies. They also must have report-writing skills, as they periodically present reports to maintenance supervisors and managers.
What Challenges Do Most Maintenance Planners Face?
According to Reliable Plant, up to 80 percent of CMMS implementations fail. This makes it difficult for maintenance planners to plan maintenance and track inventories as they rely on manual means that are exhausting, error-prone, and time-consuming.
Maintenance planners also work with people from different departments. Working with a diverse group of people is likely to result in challenges such as a lack of accountability, technical language barriers, technology knowledge, and disagreements on work prioritization.
What Is a Work Order Backlog and How Do You Manage It?
A work order backlog is a list of maintenance activities yet to be completed. A backlog can force an organization to resort to reactive maintenance as problems worsen, and issues become more urgent. This increases the risk of unplanned downtimes.
To clear a backlog, the maintenance planner should prioritize work depending on how much the tasks affect production and safety and then organize resources for their completion. It requires everyone within an organization to work as a team to clear the backlog.
What Reports Do Maintenance Planners Use?
Maintenance planners report to maintenance supervisors or managers. They present performance reports that include planned maintenance activities, backlogs, completed work orders, and inventory levels of tools and replacement parts. They also recommend how the organization can improve its asset maintenance.
Get a CMMS for Your Maintenance Workflows
The best way to streamline maintenance tasks and optimize maintenance O&M budgets is through the use of CMMS platforms. Check us out. No credit card required.
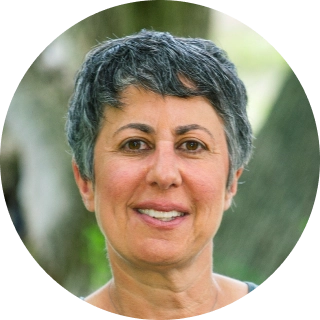
Caroline Eisner
Caroline Eisner is a writer and editor with experience across the profit and nonprofit sectors, government, education, and financial organizations. She has held leadership positions in K16 institutions and has led large-scale digital projects, interactive websites, and a business writing consultancy.
See MaintainX in action