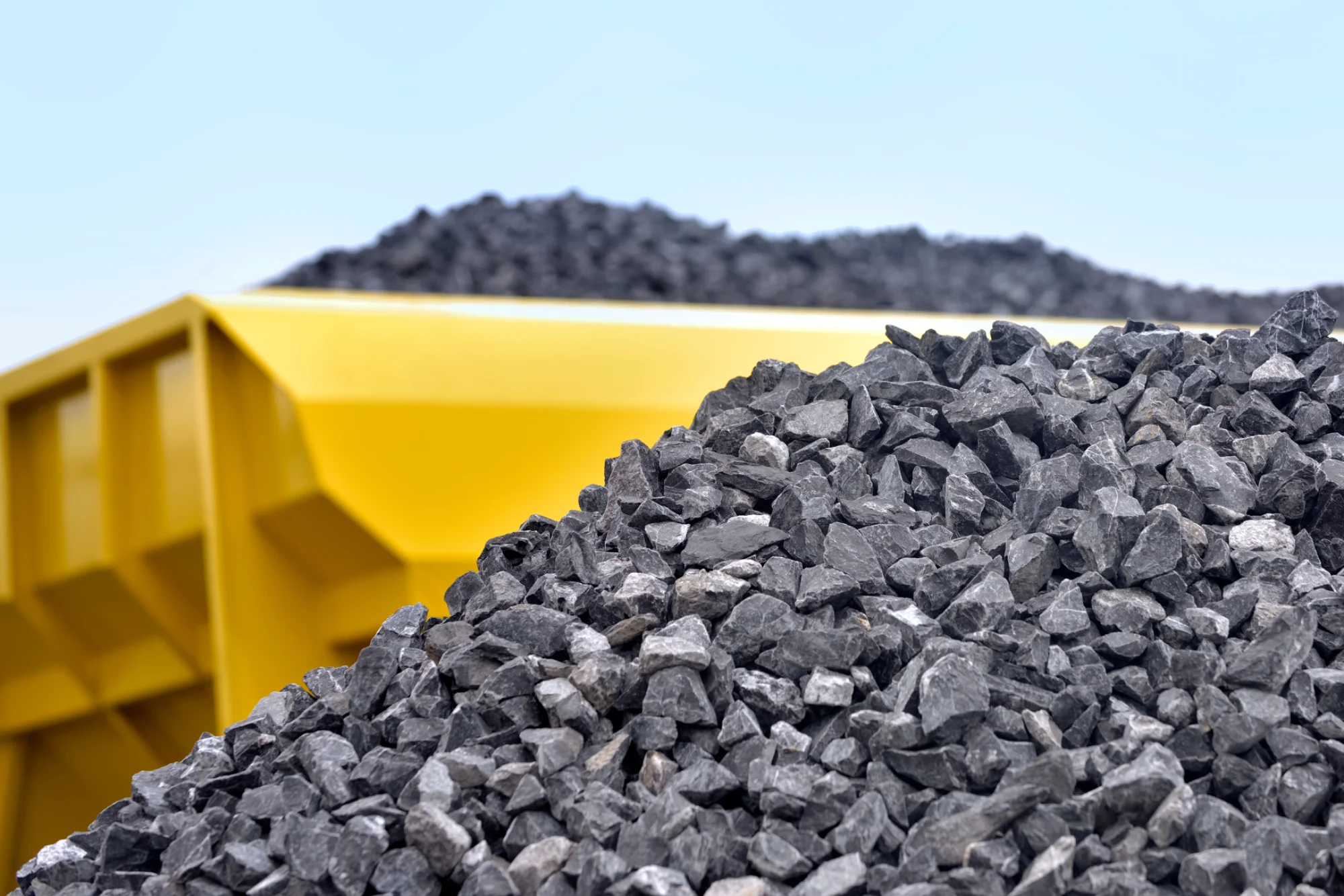
Leaders in the aggregate building materials industry know well that consistent production is crucial to maintaining profitability and market competitiveness. However, it's easy to overlook the significant role that an effective preventive maintenance strategy plays in sustaining this consistency and minimizing your cost.
While wheel loaders and mobile crushers are built to withstand rugged terrain and weather conditions, regular maintenance is critical to keeping equipment safe and operational in mines and quarries. And, with these workhorses often moving from site to site, it is even more challenging to track, monitor, and maintain them.
Operating aggregate equipment until it fails can cause costly downtime. In addition to needing to order out-of-stock parts, run-to-failure and emergency maintenance increases costs. Furthermore, failures increase the possibility of accidents. Just think about, for example, a large haul truck coming down a steep incline with, say, close to 400 short tons payload with faulty brake discs or a hydraulic mining shovel leaking hydraulic oil.
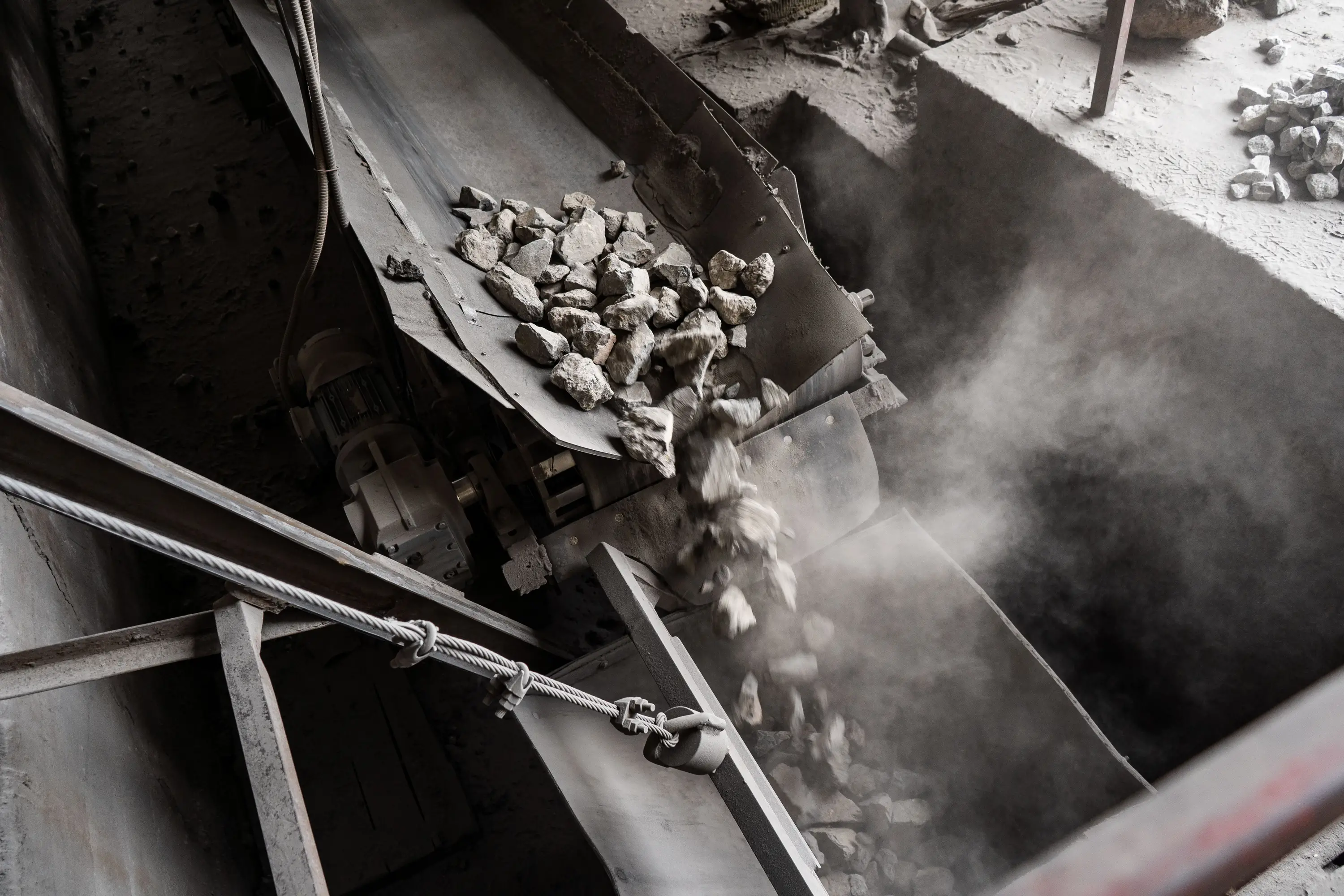
Preventive Maintenance and the Aggregate Industry
Preventive maintenance strategies are critical in the aggregate materials industry due to their profound impact on equipment longevity, operational continuity, safety, cost efficiency, regulatory compliance, and productivity. In addition, well-maintained equipment promotes sustainable practices by identifying excessive energy consumption.
For example, check out our Global Procedure Library for aggregate industry-specific procedures like this one:
MSHA: CRUSHER/SCREENING PLANT DAILY INSPECTION
Implementing a PM can have significant benefits for an aggregate materials company. Cost-saving results you can expect include:
1. Equipment Longevity
With a Computerized Maintenance Management System (CMMS), you can create scheduled maintenance tasks, resulting in better overall equipment health and longer lifespans to avoid costly upgrades of expensive machinery.
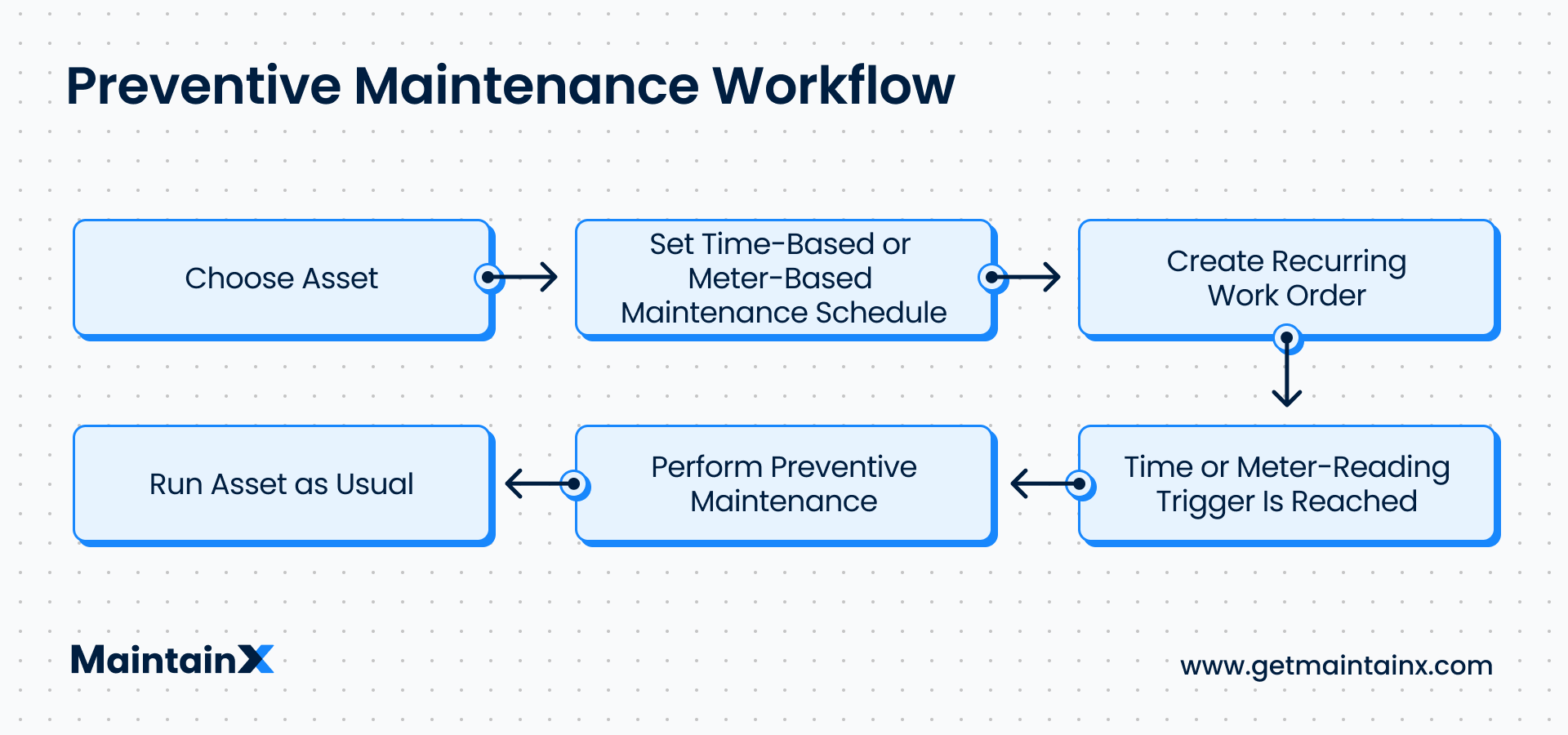
Heavy-haul trailers journey thousands of miles over their life cycle and, with frequent bumps and jolts as they pass over large rocks, no trailer goes unscathed. Traveling with underinflated tires or dry wheel ends can significantly increase wear. As a result, regular checks can add years to a trailer’s life.
Improving your recordkeeping by using CMMS maintenance software can help your team stay on top of this, and you can avoid expensive surprises.
2. Reduced Downtime
These days, with inflation and razor-thin margins, the aggregate industry needs to focus on decreasing unplanned downtime costs to stay profitable. An efficient PM program helps predict and prevent failures and breakdowns. Preventive maintenance schedules, facilitated by a CMMS, can reduce the time your equipment is out of service to increase overall productivity.
For example, if your most-used crusher goes down:
Direct costs may include:
- Repairs or replacement of the crusher: $50,000 - $100,000
- Lost production: $10,000 - $20,000 per day
- Overtime for employees: $5,000 - $10,000 per day
- Shipping and handling of replacement parts: $1,000 - $2,000
Indirect costs may include:
- Loss of customer goodwill: $5,000 - $10,000
- Damage to the company's reputation: $10,000 - $20,000
- Increased costs for other departments relying on the crushed aggregate: $5,000 - $10,000
- Opportunity costs (e.g., the company could have used the downtime to make other improvements): $5,000 - $10,000
These are just estimates. The actual costs will depend on assorted factors, such as the crusher's size and complexity, the damage's severity, and the availability of replacement parts.
This Titan America case study reveals more about the impact of downtime on an aggregate production process and how Titan reduced downtime by 30% using preventive maintenance.
3. Enhanced Safety and Compliance
The heavy machinery used in the aggregate materials industry can pose significant safety risks if improperly maintained. However, preventive maintenance checks can identify potential safety issues before they become serious, protecting employees and reducing liability.
Furthermore, dredging operations can be particularly hazardous. MSHA requires thorough workplace examinations, as well as the reporting and correction of all hazards encountered by workers.
Pre-shift examination of mobile equipment and documentation of defects is also required.
Consistent recordkeeping with a CMMS can help keep your team safe from hazards and move a step closer to the Three Zeroes. And it allows you to quickly satisfy MSHA requirements, reducing stress for your entire team.
4. Reduced Capital Expenditures
According to Pit and Quarry, components on crushers and other aggregate equipment wear out frequently. This equipment is expensive to replace, and with supply chain disruptions, investing in preventive maintenance strategies is crucial to increase the life cycle of your machines.
Running your PM strategy on a robust CMMS like MaintainX can help you save on parts based on real-time inventory and asset management, focus technician time on maintaining your critical assets first, and make actionable insights based on in-the-moment KPI data like MTBF and time and cost analyses.
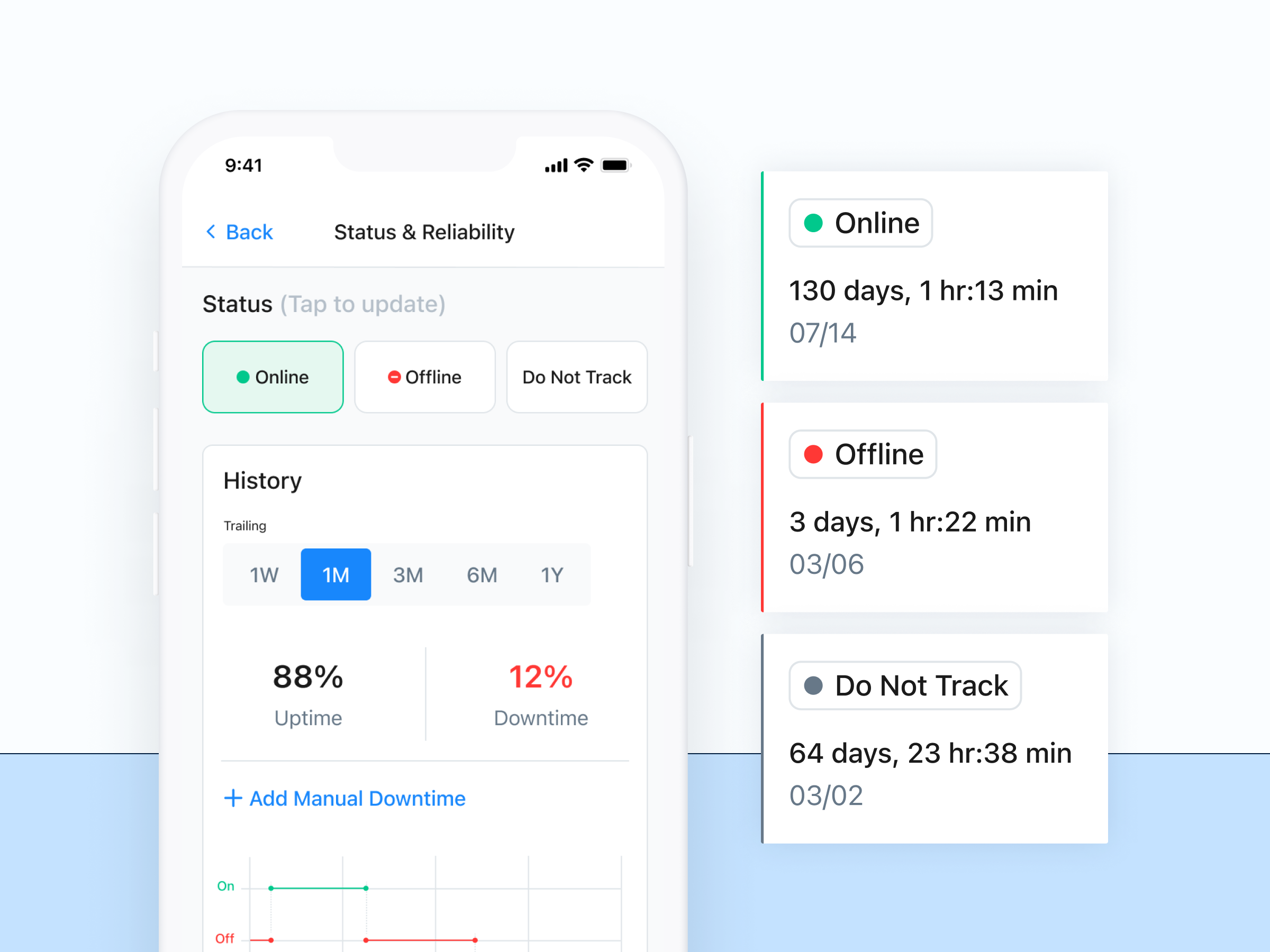
5. Increased Efficiency
Across industries, and especially in aggregates, well-maintained equipment operates more efficiently, producing more output in less time. Every ton of material moves through at least one vibrating screen, and regular inspections help reduce damaging vibrations that can diminish productivity.
If you’re running a quarry with multiple sites and needs, the right CMMS can streamline the site maintenance process by automating scheduling and assigning work orders to different teams. Using MaintainX, for example, can help you free up your maintenance team to focus on the most critical equipment first to increase overall efficiency. In addition, MaintainX’s built-in chat and messaging features reduce miscommunication and ensure that timely and essential communication never gets lost or delayed. We know staying in contact with those in the field or the factory is crucial.
A recent survey noted that “Three in four business leaders (75 percent) say they spend too much time and energy resolving miscommunications, and those that grew revenue in the last year were more likely to say their team communicates effectively (92 percent, vs. 81 percent whose revenue declined or did not change).”
"Ensuring that critical assets consistently operate at peak efficiency calls for the implementation of a maintenance management plan that is not only efficient but also highly reliable. A thorough maintenance management plan forms an indispensable part of a business’s success strategy.”
Facility Executive
Build an Efficient PM Program Using a CMMS
An efficient Preventive Maintenance (PM) program is crucial for the aggregate materials industry, where high-capacity production equipment like crushers, conveyors, and screeners are integral. CMMS software can effectively manage maintenance tasks, minimize equipment downtime, and prolong machinery life.
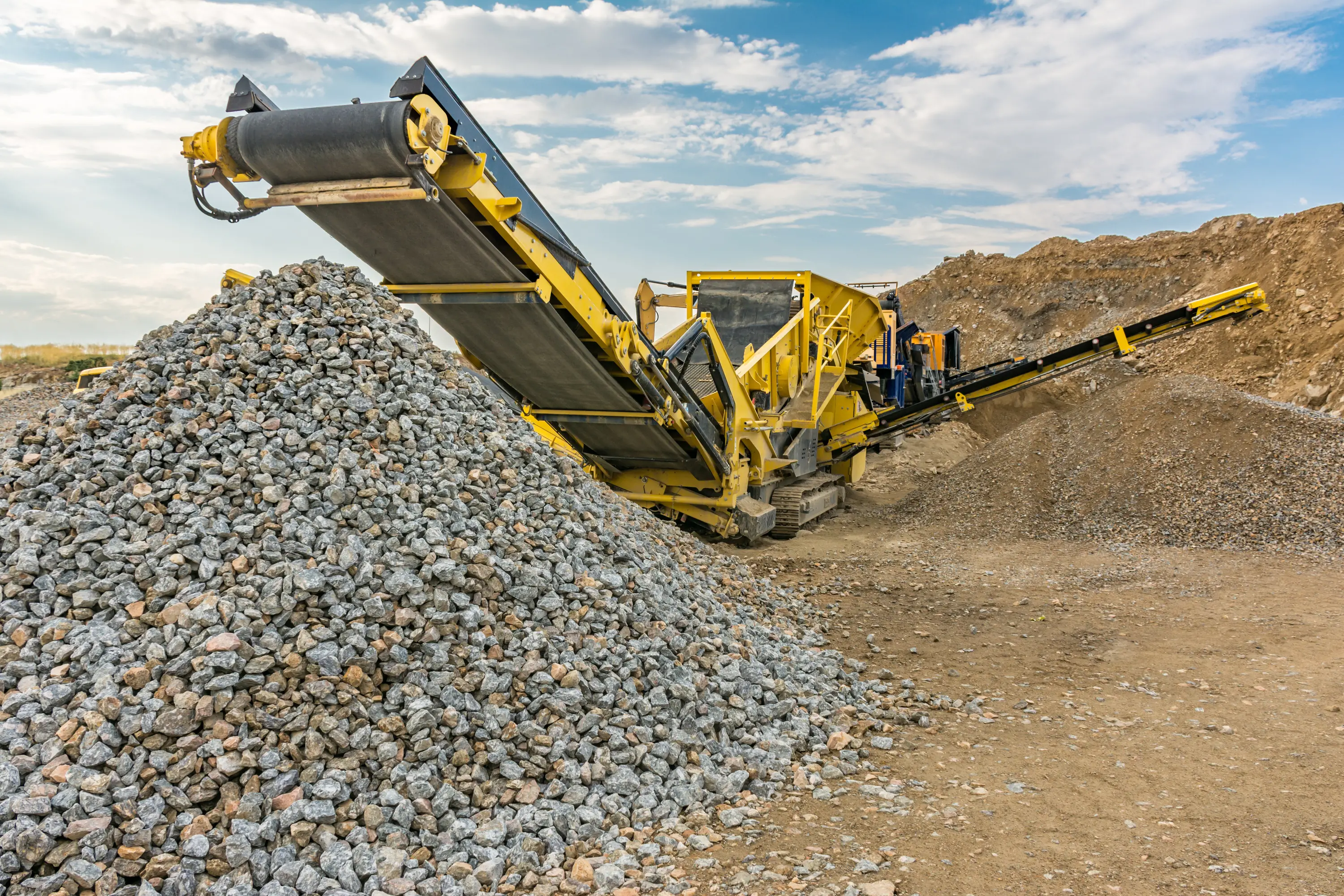
We’ve outlined four steps to help you build your planned maintenance strategy:
1. Identify All Your Assets
What equipment do you use to keep your business running? Include crushers, screens, conveyors, and other machinery in your list.
2. Use a Criticality Analysis to Identify Crucial Machinery
Criticality analysis helps determine the prioritization of each piece of equipment based on various factors. A maintenance criticality analysis can inform your maintenance strategy and how you assign maintenance teams.
Determine which machines are integral to your production process. These should include any machinery whose failure would significantly hamper production or pose safety risks.
3. Establish Preventive Maintenance Tasks and Frequency
Based on your criticality analysis and manufacturer's guidelines, identify the necessary PM strategy for each piece of machinery. Details should include the tasks and procedures, their frequency, necessary tools, and safety precautions.
Create a maintenance schedule based on these planned proactive maintenance activities. You can schedule tasks for teams to perform daily, weekly, monthly, or annually. Types of preventive maintenance also include routine maintenance (RM). RM typically includes regular inspections and machine servicing. The goal is to identify problems before they result in equipment failure.
Consider integrating IIoT devices into predictive maintenance planning. With machine learning, you can apply metrics, meters, and sensors to decrease costly reactive maintenance. This approach can be a game-changer in the aggregate materials industry, with its heavy reliance on large, complex, and costly machinery.
4. Regularly Review Your PM Strategy
With a robust CMMS, you can use critical performance data and reports to review your strategy and identify trends, recurring issues, and improvement areas. The data lets you make action-based decisions about your PM strategy and scheduling.
Remember, though, the success of a PM program relies on the accuracy of the data entered into the CMMS and the commitment of the team to adhere to established maintenance procedures. Once you have completed these steps, you will have a preventative maintenance plan to help keep your aggregate production running smoothly and prevent costly breakdowns.
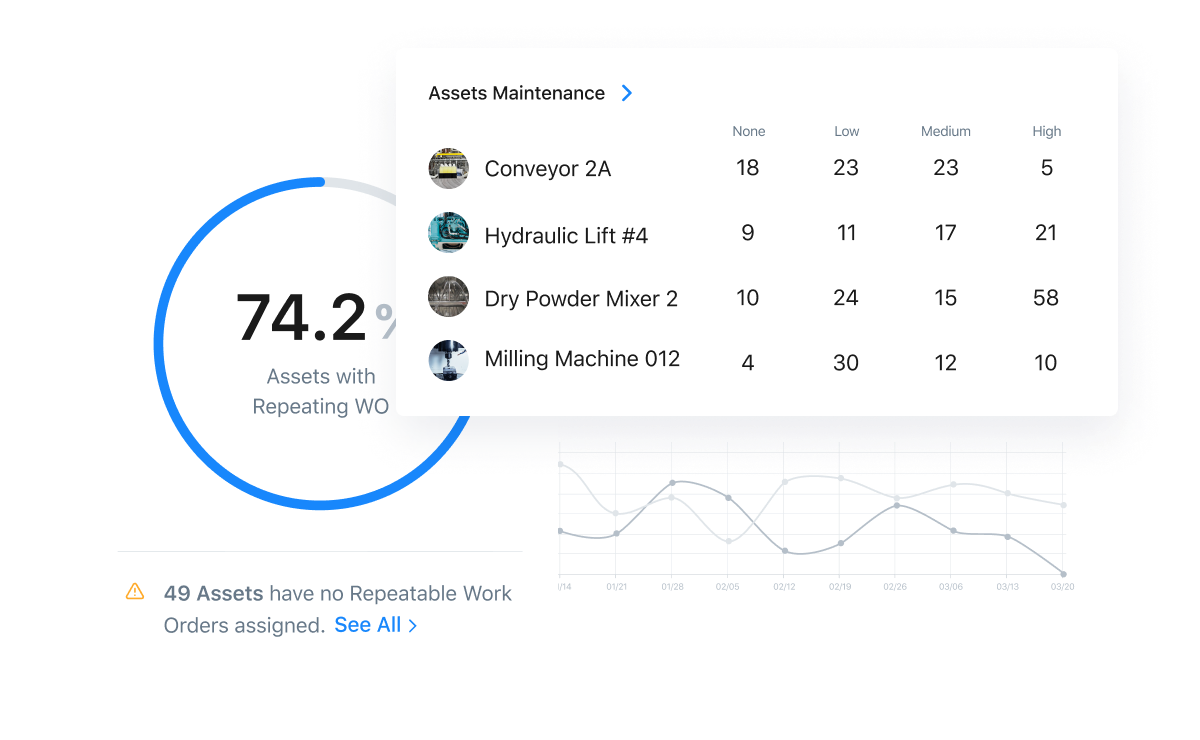
Key CMMS Features for the Aggregate Materials Industry
Choosing a CMMS for the aggregate materials industry requires careful consideration. You'll want a CMMS that can effectively handle the unique demands of heavy machinery and high-capacity production equipment.
Here are key CMMS features to look for:
Preventive Maintenance Workflows
A good CMMS should allow you to schedule and track preventive maintenance tasks to minimize downtime and extend the life of your equipment. In addition, your digital PM plan should be able to generate automatic alerts and work orders when maintenance is due. In MaintainX, you can trigger PM tasks based on meter readings to inspect or service equipment after time used, mileage, or anything else you choose. For example, you can add triggers based on the number of uptime hours of a shaker screen to lubricate roller bearings or mileage on a cement mixer to perform oil changes and tire checks.
Inventory Management
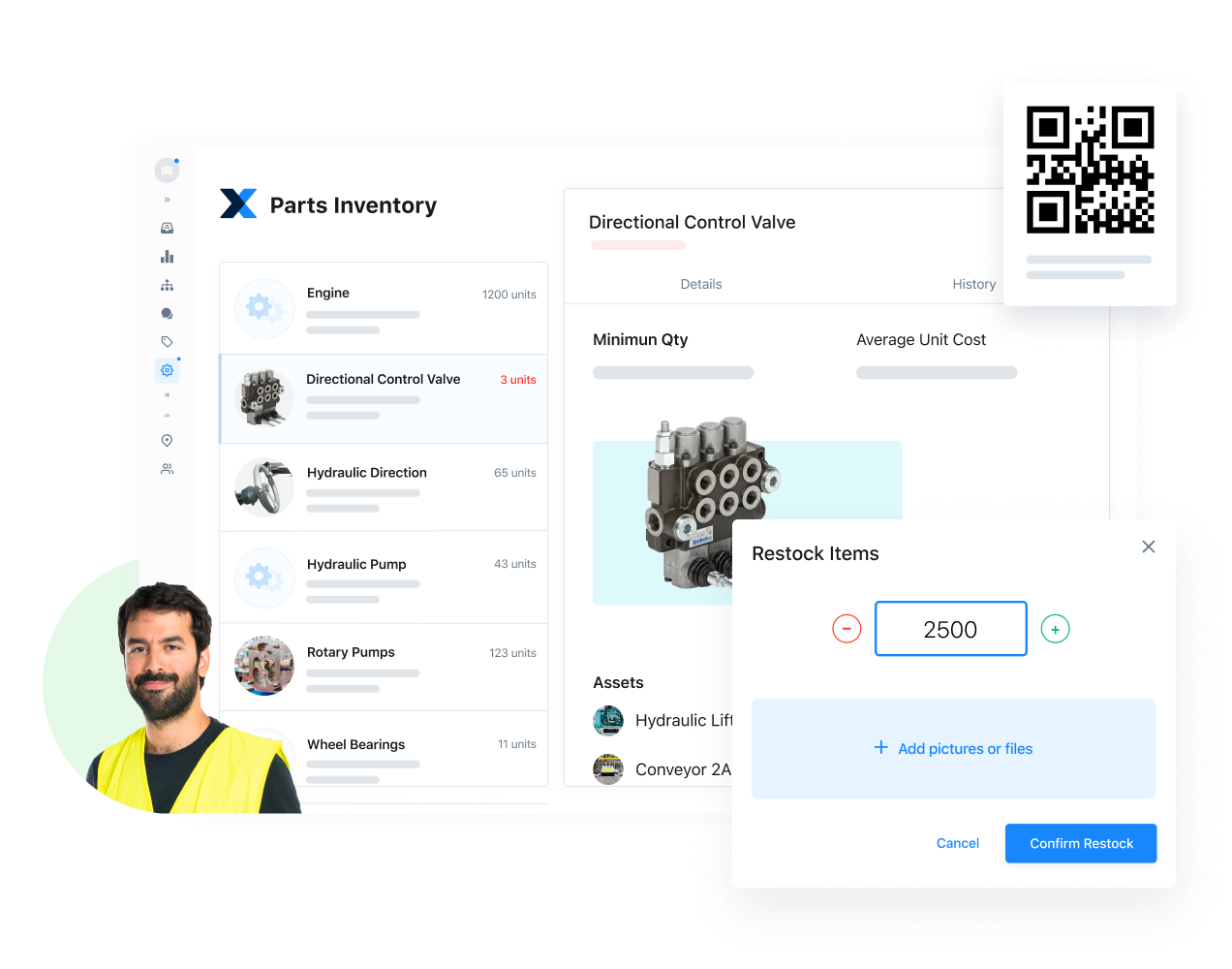
A robust CMMS should help you track all your parts and materials, including automatically reordering parts when stock levels are low. This can help prevent unexpected downtime due to a lack of spare parts.
Using QR codes and bar codes for inventory management helps you save money, keep track of assets seamlessly, and significantly reduce time on task.
The system should allow you to track all your assets, including machinery, tools, and equipment. For example, with MaintainX’s robust assets and parts features, you can simply scan affixed codes to track each piece of equipment's location, condition, maintenance history, and performance in real time.
Work Order Management
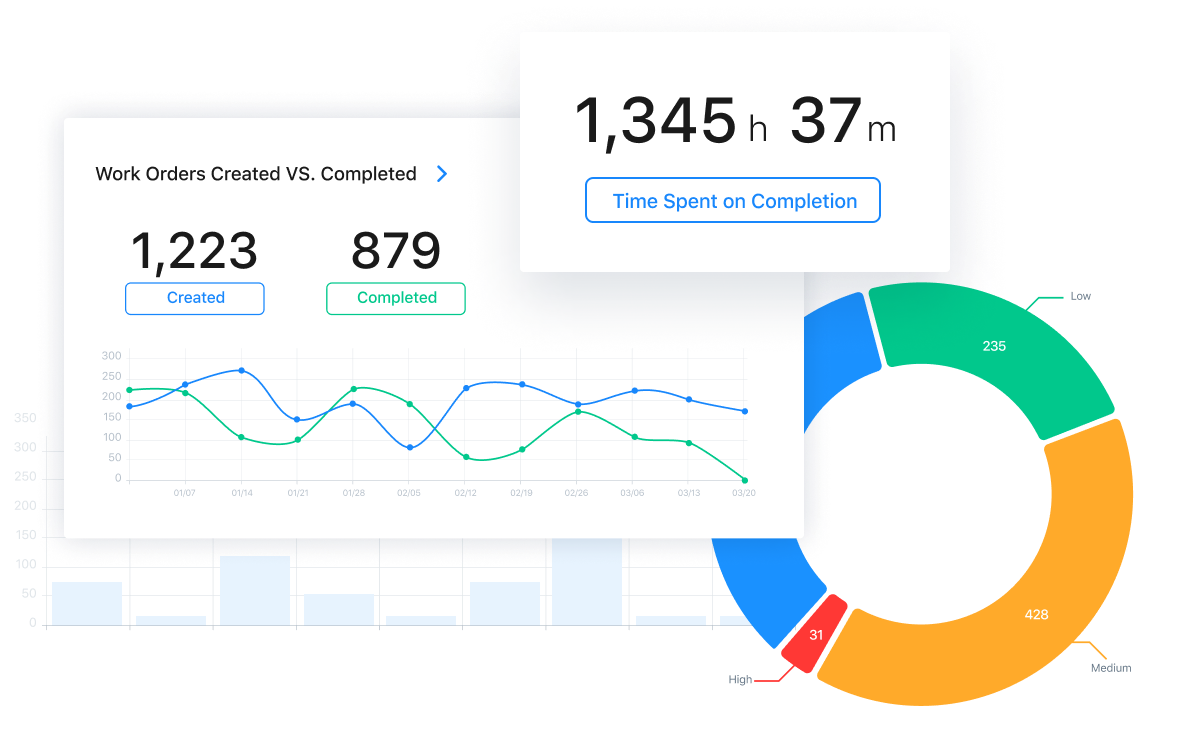
Look for a system that simplifies creating, assigning, and tracking maintenance work orders. In addition, the CMMS should offer real-time updates on the status of each work order and allow technicians to input information, ask questions, and upload images about work orders directly from their mobile devices, anywhere, at any time.
With MaintainX, you can automatically create and assign a work order to an asset, location, or technician, and track the progress of work orders in real time. In addition, you can create work orders that repeat on a calendar or runtime basis in seconds. And, whether you do preventive maintenance, reactive, or both, you can simply create work orders as needed.
Real-Time Communication and Accountability
Given the nature of the aggregate materials industry, your team may be spread out across multiple locations. A CMMS with mobile capabilities allows technicians to access work orders, maintenance history, and other important information from anywhere.
A CMMS with mobile access lets you easily track who performed what tasks and when. This can improve communication, accountability, and overall team performance.
With MaintainX, the only CMMS with in-app chat, you and your teams can comment on work orders and provide clarification instantly.
Data-Driven Analytics and Decision Making
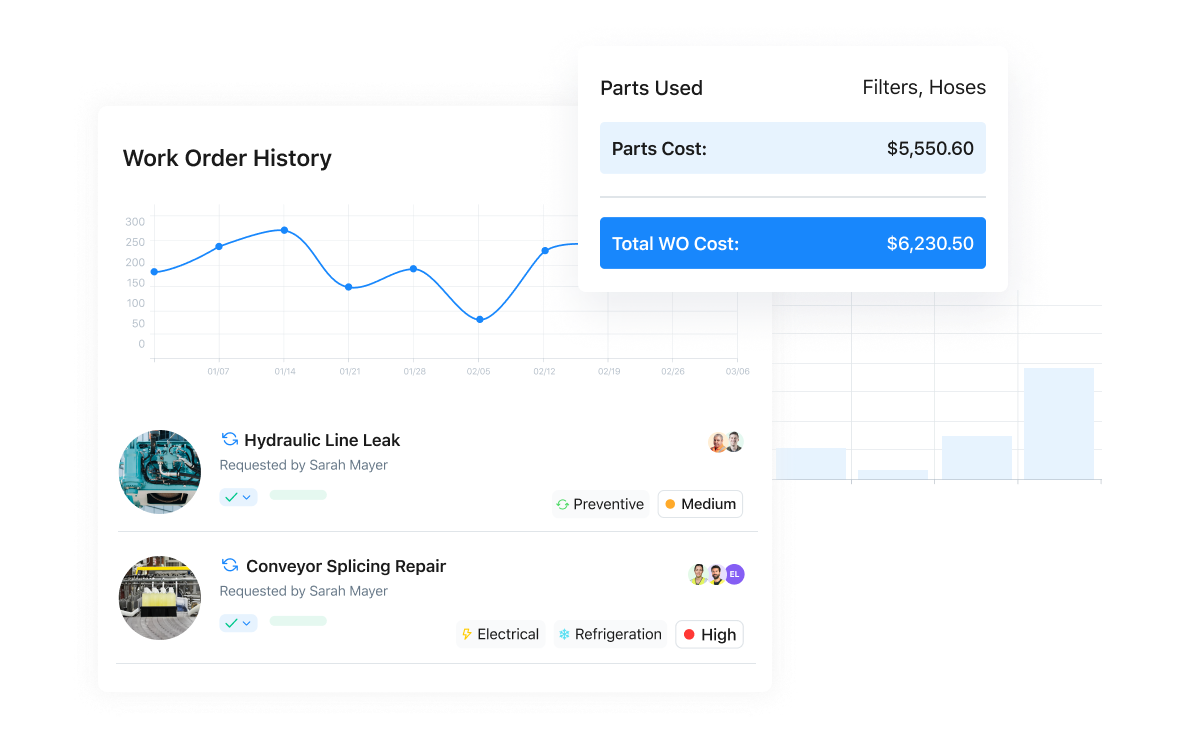
In today’s economic climate, optimizing cost-effective strategies and driving production and maintenance efficiencies are more important than ever. Not to mention that budget squeezes and supply chain delays are making it critical to run leaner. To help solve these challenges, MaintainX provides enhanced Reporting tools to help you make data-driven decisions.
With these tools, you can spot trends, identify recurring problems, and make informed data-driven decisions about, for example, whether to replace or fix a vertical impact crusher based on MTTR, MTBF, downtime, and other KPIs.
Integration Capabilities
The CMMS should integrate with the other software systems you use to manage your aggregate business, such as enterprise resource planning (ERP) systems for accounting, to streamline operations and ensure data consistency. Check out the ease of integrating your software systems with MaintainX.
Ease of Use
The system should be user friendly and easy to navigate, even for those who aren’t tech savvy. Training and technical support from the software provider are always beneficial.
Scalability
A good CMMS should grow with you as your business grows. MaintainX easily scales up to handle increasing amounts of data and additional users as your business expands.
Integrate MaintainX into Your Aggregate Business Preventive Maintenance
Implementing a CMMS can revolutionize your aggregate maintenance operations and dramatically improve the reliability and lifespan of your aggregate equipment. MaintainX automates your maintenance scheduling and tracking of maintenance tasks and provides vital data to help you optimize your PM program and make informed, strategic decisions.
Remember, the best CMMS for you will depend on your specific needs and the nature of your aggregate operations. With features like work order management, real-time inventory control, and detailed analytics, a CMMS like MaintainX can increase efficiency, reduce downtime, and significantly save costs. In addition, it's an investment that can pay dividends by increasing your competitive edge in the aggregate building materials industry.
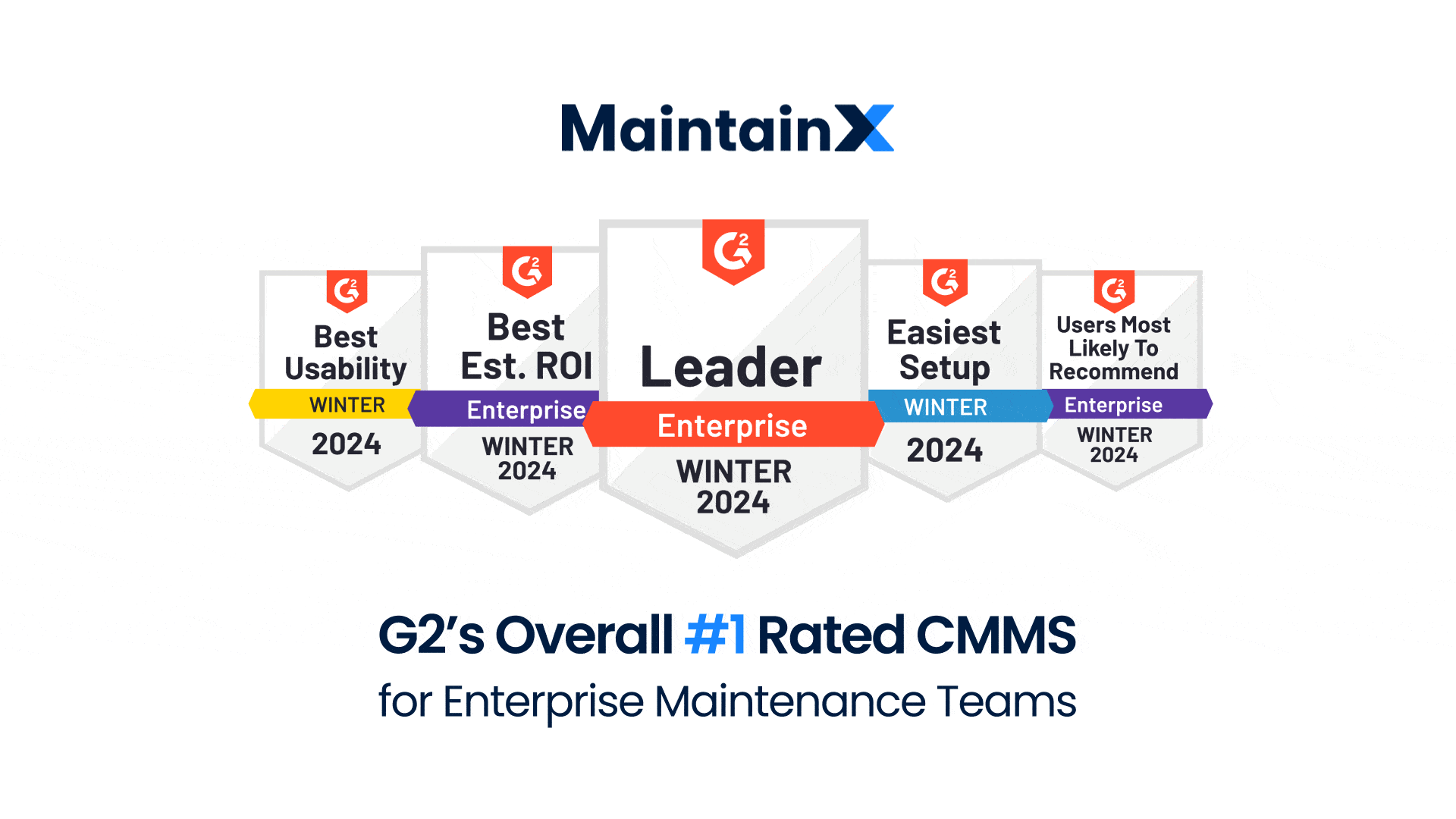
Through G2 and Capterra reviews, MaintainX users continue reinforcing how we’ve redefined the CMMS category by providing the best world-class, mobile-first solution, empowering hundreds of thousands of frontline workers worldwide. We’ve always been committed to providing a world-class customer experience with seamless implementations and a partnership approach to shared success. We’ve been recognized on G2 for the following: features:
- Fastest Implementation
- Most Implementable
- Easiest Setup
- Best Usability
- Easiest Admin
- Best Meets Requirements
- Best Relationship
- Best Results
- Users Most Likely To Recommend
- Highest User Adoption
- Momentum Leader
The aggregate industry is at a critical juncture. Those who decide to embrace digital transformation will be well-positioned for success in the years to come.
Check out MaintainX. We can help you work smarter, not harder.
FAQs
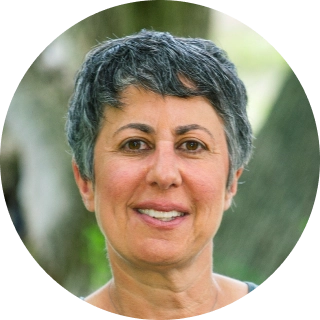
Caroline Eisner is a writer and editor with experience across the profit and nonprofit sectors, government, education, and financial organizations. She has held leadership positions in K16 institutions and has led large-scale digital projects, interactive websites, and a business writing consultancy.