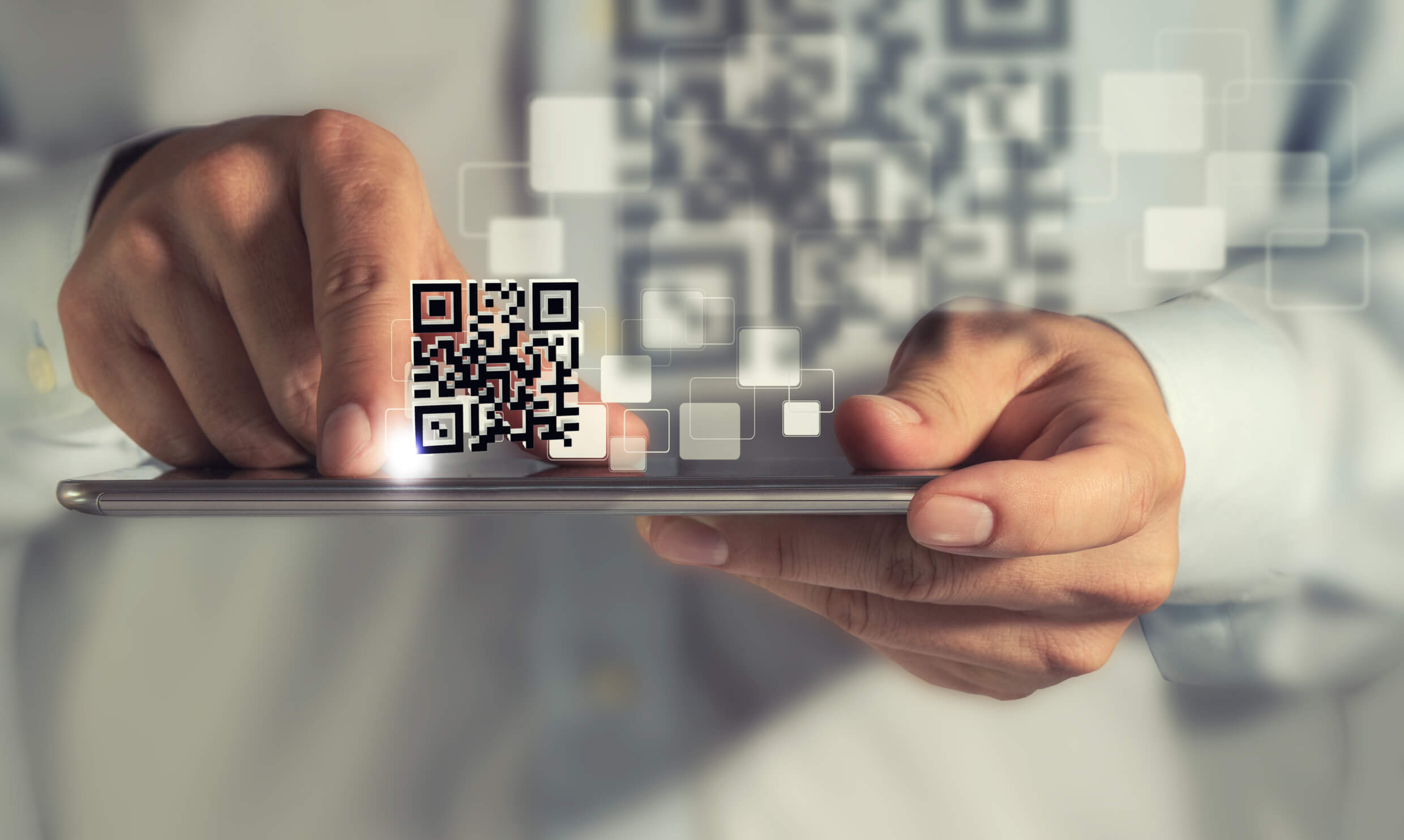
Gone are the days of matching QR codes to equipment via spreadsheets. These days, QR codes with a CMMS helps you save money, keep track of assets seamlessly, and significantly reduce time on task.
Instead, using QR codes in maintenance on a user-friendly CMMS (Computerized Maintenance Management System) has several benefits, including:
- Time-saving: QR codes enable teams to quickly and easily access asset information, such as maintenance history, repair instructions, and safety protocols, without having to search for this information manually.
- Improved accuracy: With the codes, teams can be confident that they are accessing the correct information for a specific asset, reducing the risk of errors and accidents from using outdated or wrong information.
- Enhanced asset tracking: The codes allow for improved tracking of assets by helping teams to quickly scan the code to access information about the asset, including its location, status, and maintenance history.
- Improved safety: The codes can provide access to safety procedures and protocols, reducing the risk of accidents and injuries during maintenance and repair activities.
- Reduced costs: By enabling maintenance teams to access asset information quickly and accurately, the codes can help reduce costs and downtime while increasing the life of assets by ensuring they receive proper maintenance and repairs on schedule.
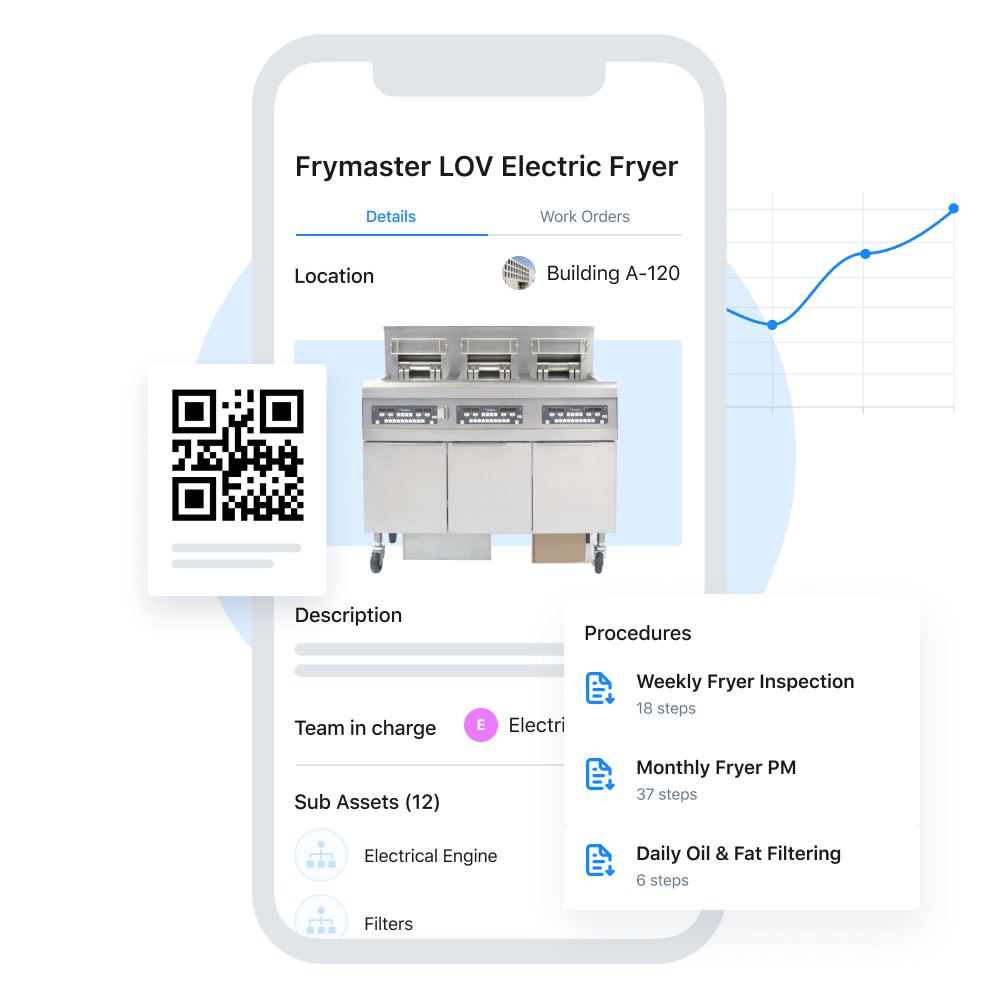
Consider QR-Driven Maintenance Plans
QR-driven maintenance offers preventive maintenance scheduling, which can trigger customizable alerts with the ability to assign them to specific workers.
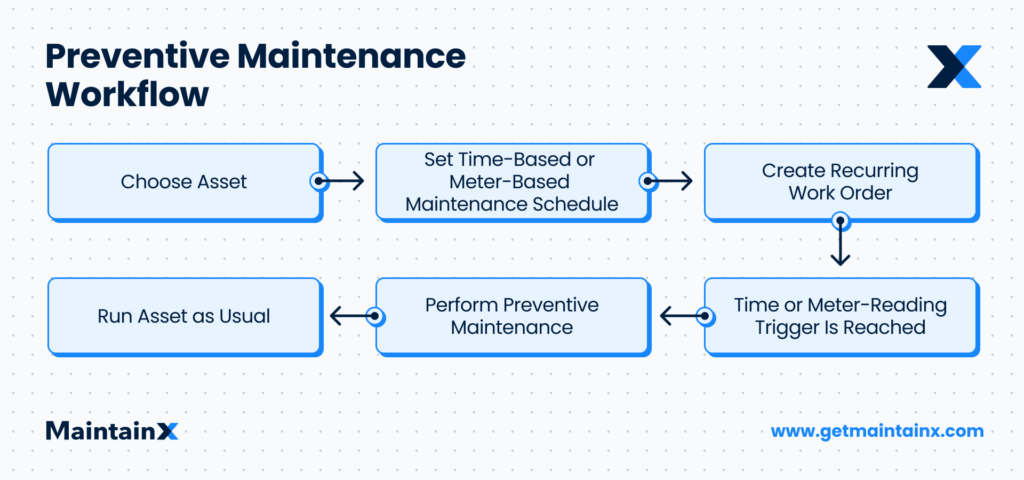
Also, users can attach forms, templates, documents, and images to asset profiles to search for equipment in the field. For example, in MaintainX, once you scan a QR code, you can see the location, images, and maintenance procedures.
For example, in MaintainX, QR and barcode scanning makes it easier to look up an Asset directly from the field or factory floor. Scanning allows you to:
- Scan codes on paired assets to view an asset’s details or create a new Work Order for that asset.
- Scan codes on unpaired assets to attach the code to an asset or create a new one with that code.
- Create and print codes for assets that don’t already have codes in place.
In fact, any barcode or QR code format will work with MaintainX.
Implementing QR Codes in Maintenance
The implementation of QR codes in manufacturing maintenance on a CMMS involves several steps, including:
- Creation of QR codes: The first step is to create codes for each asset or equipment needing maintenance. You can do this with a QR-code generator, which often means entering the asset information, such as its name, location, and maintenance schedule. In MaintainX, you can add a new asset by scanning a code with your mobile device.
- Attachment of QR codes to equipment: Once you’ve created the codes, attach them to the appropriate equipment or assets. Make sure to attach the codes in easily visible locations.
- Scanning of QR codes using a mobile device: Maintenance teams can use a mobile device, such as a mobile phone or tablet, to scan the codes on the equipment. This will provide instant access to the asset information stored in the CMMS.
- Uploading data to CMMS: After scanning the code, teams can update the asset information in the CMMS. This may include adding notes about maintenance activities, updating the maintenance schedule, or marking the asset as needing repair.
- Integration with CMMS: Finally, integrate the codes with the CMMS software so that teams can access the asset information. You can use it to schedule maintenance activities and track the asset’s history.
With the right CMMS, QR codes can significantly improve the efficiency and effectiveness of maintenance activities, reducing costs and improving asset reliability.
Best Practices for Using QR Codes
To ensure that QR codes are used effectively in maintenance on a CMMS, you can follow best practices, including the following:
- Proper placement of QR codes: Place codes in locations that are visible to teams. Be sure to protect the location from damage or wear that could make the code unreadable.
- Regular maintenance of QR codes: To ensure that codes remain readable, inspect and clean the codes regularly. Repair or replace any damage or wear to the codes quickly.
- Integration of QR codes with preventive maintenance plans: You can integrate codes into a preventive maintenance program to ensure that maintenance activities are scheduled and completed on time. Furthermore, this can help to prevent breakdowns and extend the life of the equipment.
- Maintenance team training: Teams should be trained on the proper use of the codes and how to access asset information and schedule maintenance activities.
- Standard QR codes: To ensure consistency and avoid confusion, use standard codes throughout the organization. This can include standardizing the information encoded in the QR code and the code’s physical size and design.
- Regular auditing of QR codes: Periodic auditing of the codes can help you identify any issues, such as unreadable codes or outdated information. Furthermore, this helps to identify any equipment that may not have a code or has a wrong code attached.
With this, you can streamline spare parts and inventory management, reduce downtime, and extend the life of the equipment.
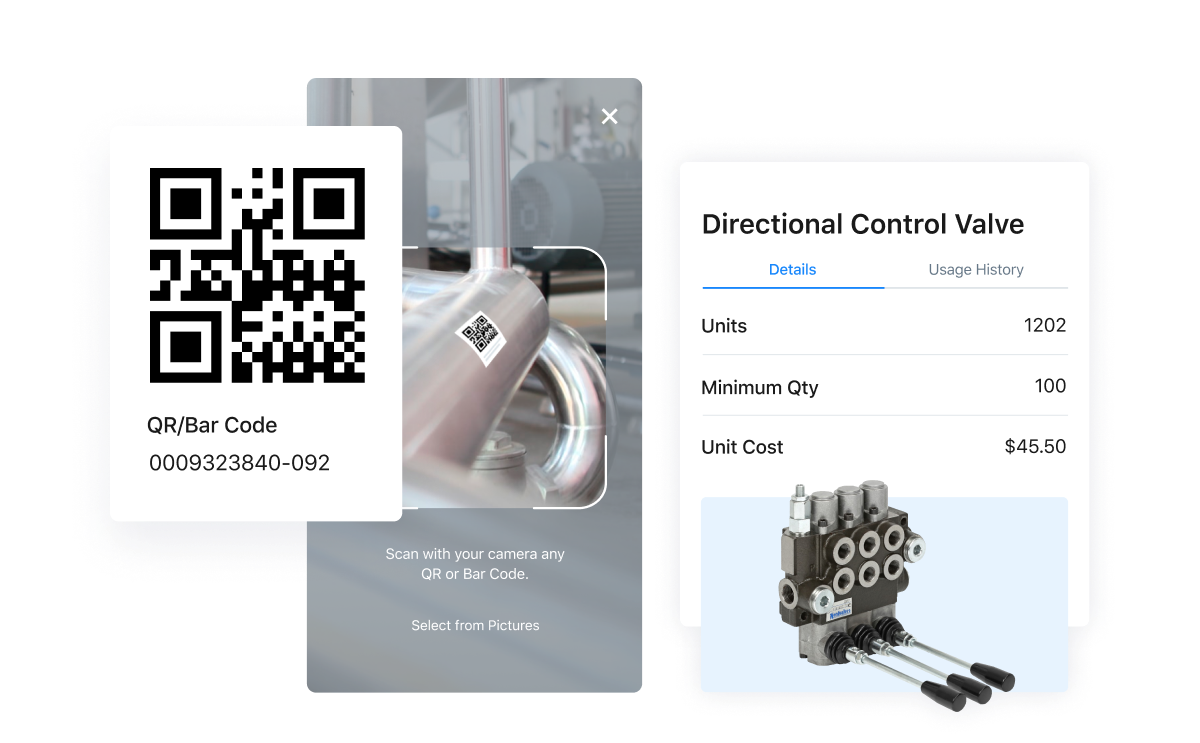
Challenges of Using QR Codes
Using QR codes on a CMMS can provide significant benefits. However, there are also some challenges that your company may run into. These challenges can include:
Adoption
Adopting QR codes on a CMMS may require a significant investment of time and resources. You may need to train teams, establish processes, and integrate the codes with the CMMS.
Quality of QR Codes
Various factors can impact the quality of the codes, including the material on which they are printed, the size of the code, and the quality of the printing. Poor-quality codes can be difficult or impossible to read, reducing their effectiveness.
Maintenance of QR Codes
QR codes require regular maintenance to ensure that they remain readable and current. This can include cleaning, inspecting, and replacing damaged codes.
Data Management
QR codes generate large amounts of data, which you must manage to avoid confusing teams. A robust CMMS like MaintainX stores your data in the cloud, making it viewable from anywhere, anytime. In addition, you can then use this data with MaintainX’s Reporting module to track key performance indicators.
Security
To be sure, QR codes may pose a security risk if they are not adequately protected. Proper security measures must ensure that only authorized teams can access QR code data. MaintainX takes the security of your data seriously. We received our first SOC 2 Type 2 Compliance notification in 2020 and have been earning it since.
The SOC 2 Type 2 compliance designation is an external audit of MaintainX’s internal controls that protect customer information. Specifically, the audit focuses on MaintainX’s description of our system. Furthermore, the audit designates that the company’s internal controls are designed and operating effectively.
As the compliance renewal reinforces, MaintainX fulfills the crucial industry standards that SOC 2 criteria require. We accept our risk-management responsibilities to protect clients’ privacy and data from cyber-attacks.
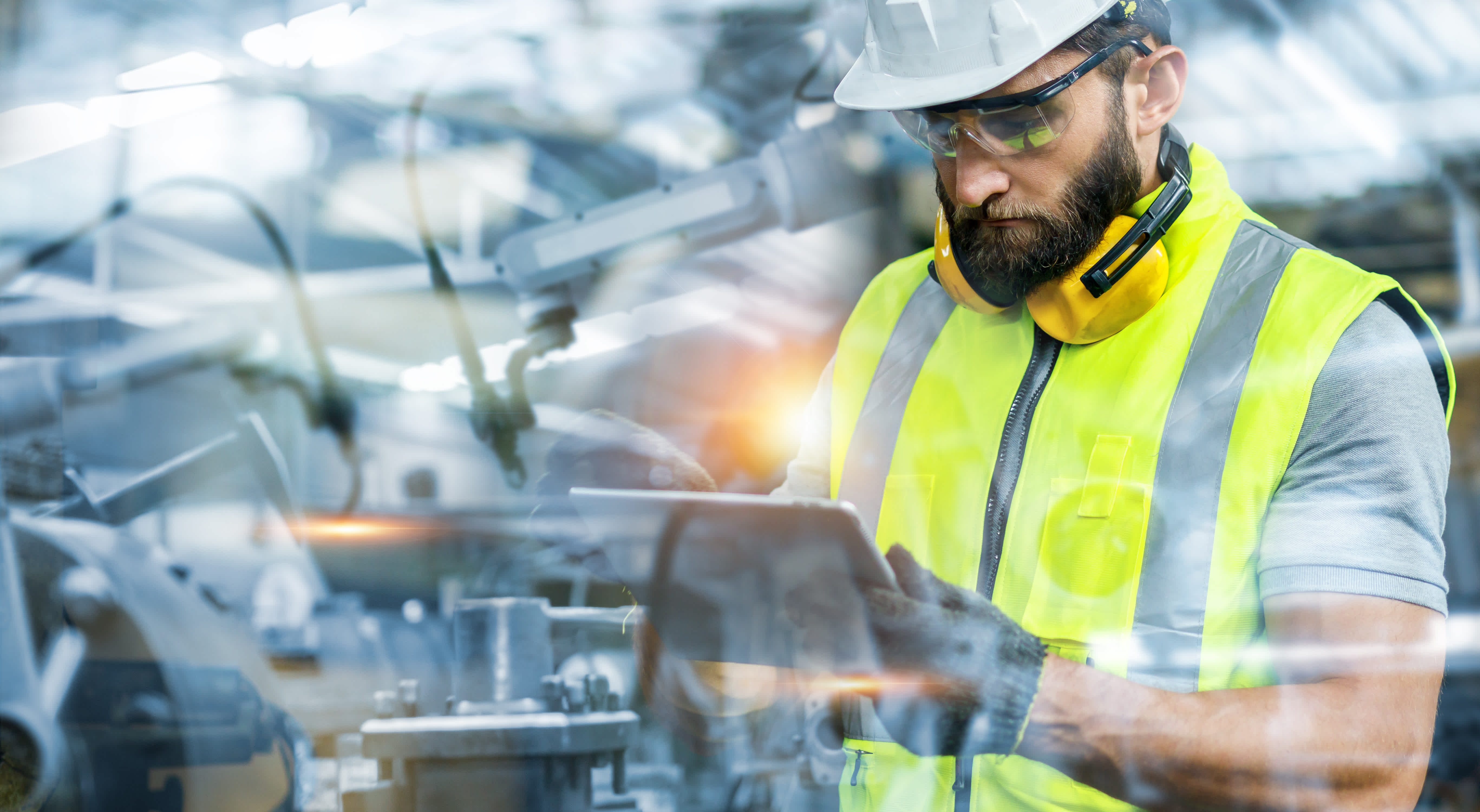
Human Error
Unfortunately, human error can be an issue when using QR codes in maintenance on a CMMS. Not surprisingly, this is because the effectiveness of the codes depends on the accuracy and completeness of the information encoded in the code and the actions taken by teams who use the code.
Examples of human error that can occur include:
Incorrect Data Entry
When creating QR codes, maintenance teams may make errors when entering information such as the asset name, location, or maintenance schedule. These errors can result in wrong or incomplete information stored in your CMMS system.
Misplaced or Damaged Codes
Maintenance teams may accidentally lose or damage codes, making them unreadable and reducing their effectiveness.
Failure to Scan QR Codes
Unfortunately, teams may forget or neglect to scan the during maintenance activities. This may result in incomplete or wrong data in the CMMS.
To address these issues, you can take steps to reduce the potential for human error, such as providing regular training on the use of the codes and CMMS, implementing quality control measures to ensure data accuracy, and developing processes for managing lost or damaged codes.
The Potential of Using QR Codes with a CMMS
The future potential of using QR codes with a CMMS is significant as technology advances and we think of new applications for QR codes. Some of the potential future applications of QR codes in maintenance on a CMMS include:
Augmented Reality (AR) Integration
You can integrate QR codes with AR technology to provide teams with real-time data and visualizations of equipment and assets, making it easier to identify potential issues and perform maintenance tasks.
Predictive Maintenance
As we’ve said, you can use the codes to capture data about equipment performance, which you can then analyze to predict when maintenance before a breakdown occurs. This can reduce downtime and extend the life of equipment.
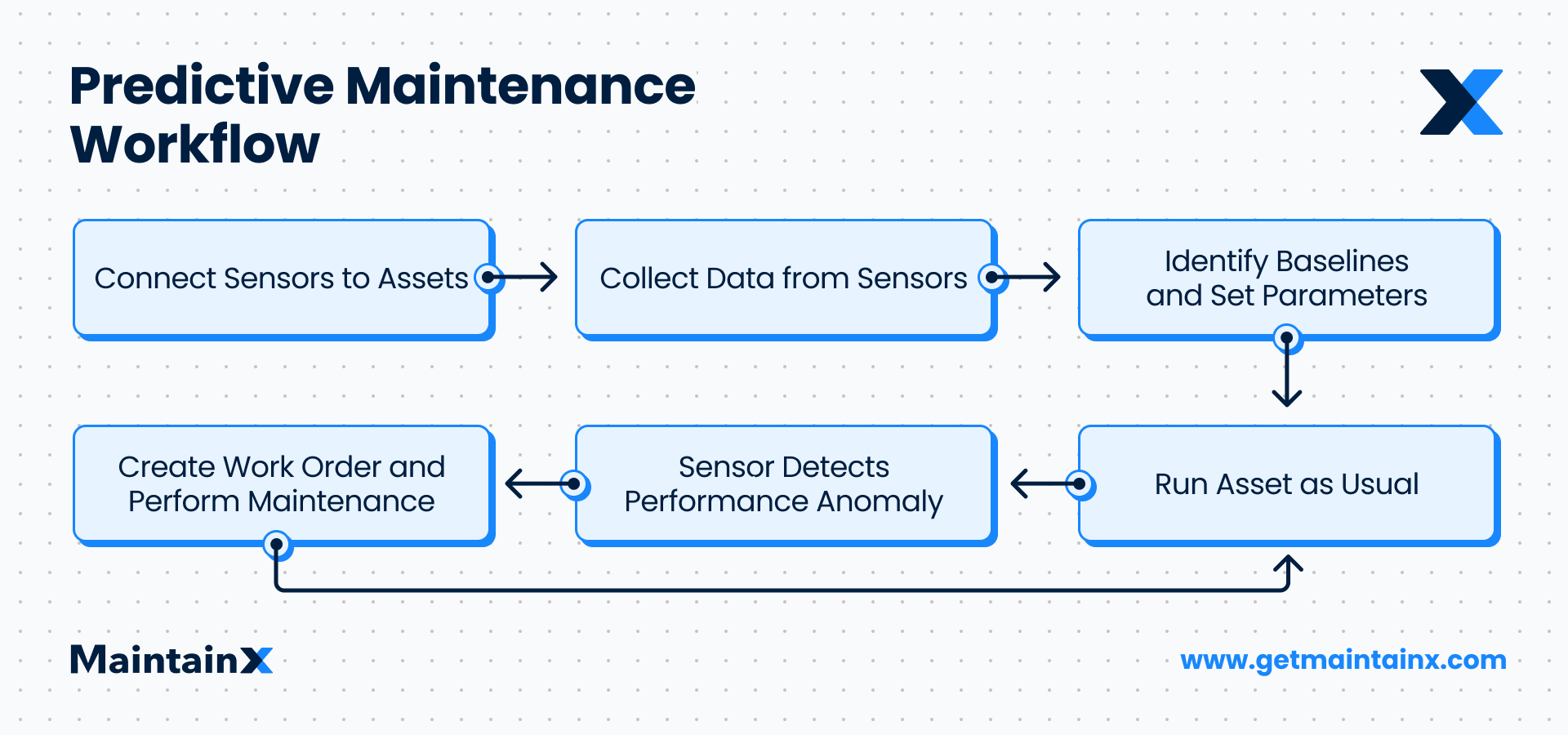
Industrial Internet of Things (IIoT) Integration
You can integrate QR codes with IIoT sensors to provide real-time data about equipment and asset performance, enabling maintenance teams to monitor and manage equipment remotely.
Mobile Device Integration
The codes can be scanned using mobile devices such as smartphones or tablets, enabling maintenance teams to access real-time data and update maintenance records from anywhere in the facility.
By leveraging these technologies, organizations can improve maintenance efficiency, reduce downtime, and extend the lifespan of equipment and assets.
MaintainX and QR Codes
Barcodes and QR Codes will help you organize and find your assets. In addition, MaintainX can integrate with your EAMs (enterprise asset management software) via seamless integrations.
Cloud-based work order and asset management have never been easier. Using MaintainX on your mobile device means real-time notifications based on the codes attached to Work Orders, assets, locations, and inventory. As a result, easy access to your company’s facility management KPIs is available at your fingertips.
FAQs
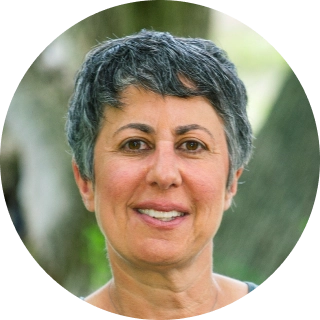
Caroline Eisner is a writer and editor with experience across the profit and nonprofit sectors, government, education, and financial organizations. She has held leadership positions in K16 institutions and has led large-scale digital projects, interactive websites, and a business writing consultancy.