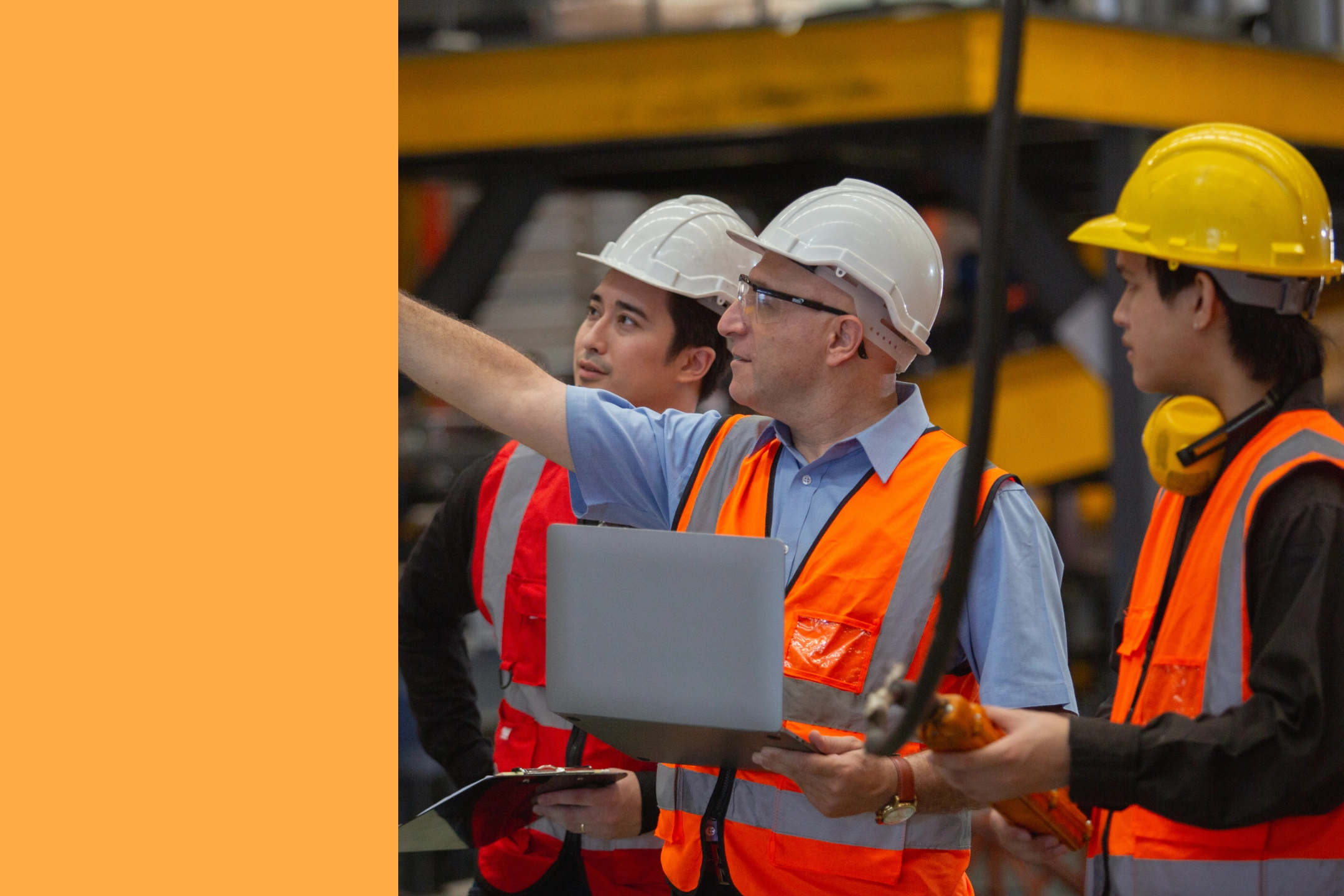
Looking to level up your maintenance strategy or implement one from scratch? Choosing the right maintenance strategy can mean the difference between an optimized system of operations and one wrought with disruptions and downtime.
While certain principles can help anyone improve their maintenance, a one-size-fits-all approach is not the most efficient or cost-effective solution, as not every asset needs the same type or level of maintenance.
In this guide, we’ll walk you through five different types of maintenance strategies, how to choose the best maintenance strategy for your assets, and how to implement each strategy in your business.
What are the 5 different types of maintenance strategies?
The five different types of maintenance strategies include:
- Reactive maintenance
- Preventive maintenance
- Condition-based maintenance
- Reliability-centered maintenance
- Predictive maintenance
Reactive maintenance (breakdown maintenance)
What is reactive maintenance?
A reactive maintenance strategy—also known as run-to-failure maintenance—involves delaying all maintenance work until assets malfunction or break down.
This maintenance management program requires little in the form of proactive work on the team’s part and, in many ways, seems like the most obvious approach. After all, why fix what isn’t broken?
Say you have a limited maintenance budget and a small staff dedicated to maintenance and reliability work. Taking several hours out of the production schedule to tune up equipment and machines that appear to be working fine may not be a viable or intuitive approach.
However, you need to be careful, as a purely reactive maintenance strategy can lead to chaos. Like a glacier submerged in water, looks can be deceiving—it isn’t unheard of for machines and equipment that are working perfectly fine to break down without warning. And, if you’re running a facility with limited maintenance staff, unplanned downtime can cause serious losses in revenue and productivity.
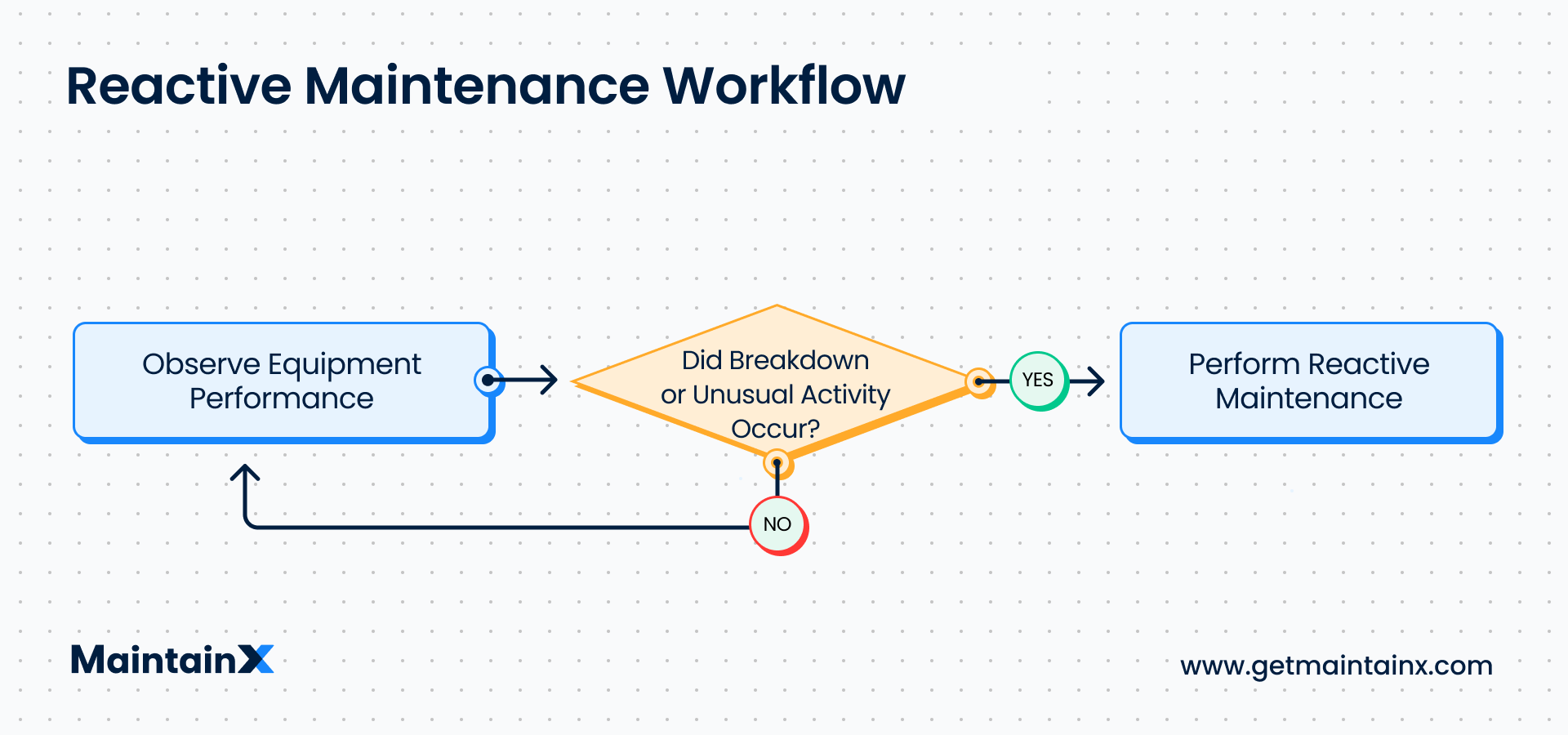
What’s the perfect amount of reactive maintenance?
How often should you plan to let equipment run to failure? While there’s no “perfect” amount of reactive maintenance, experts recommend adopting an 80/20 approach (based loosely on the Pareto Principle), where 80% of maintenance activities focus on proactive work and the remaining 20% on reactive work.
Why bother with reactive maintenance?
If proactive maintenance should take 80% of your time, it probably sounds like a more beneficial approach than reactive. And while it’s advisable to aim to prevent malfunctions in most cases (more on this shortly), you shouldn’t abandon reactive work completely. Reactive maintenance is inevitable; despite your best efforts, breakdowns and malfunctions will happen.
While you want to limit the amount of reactive maintenance that you perform, you should have a robust corrective maintenance plan in place for when things do break down. Corrective maintenance refers to actions taken to correct a malfunction or restore a piece of equipment to functionality. Having a corrective action plan in place means that when equipment goes down, you are not precious time figuring out how to restore functionality. Without a plan in place, you will face hurdles, including assembling the right maintenance team, understanding the problem, and determining how to solve it. As a result, you may struggle to get operations back up and running as soon as possible.
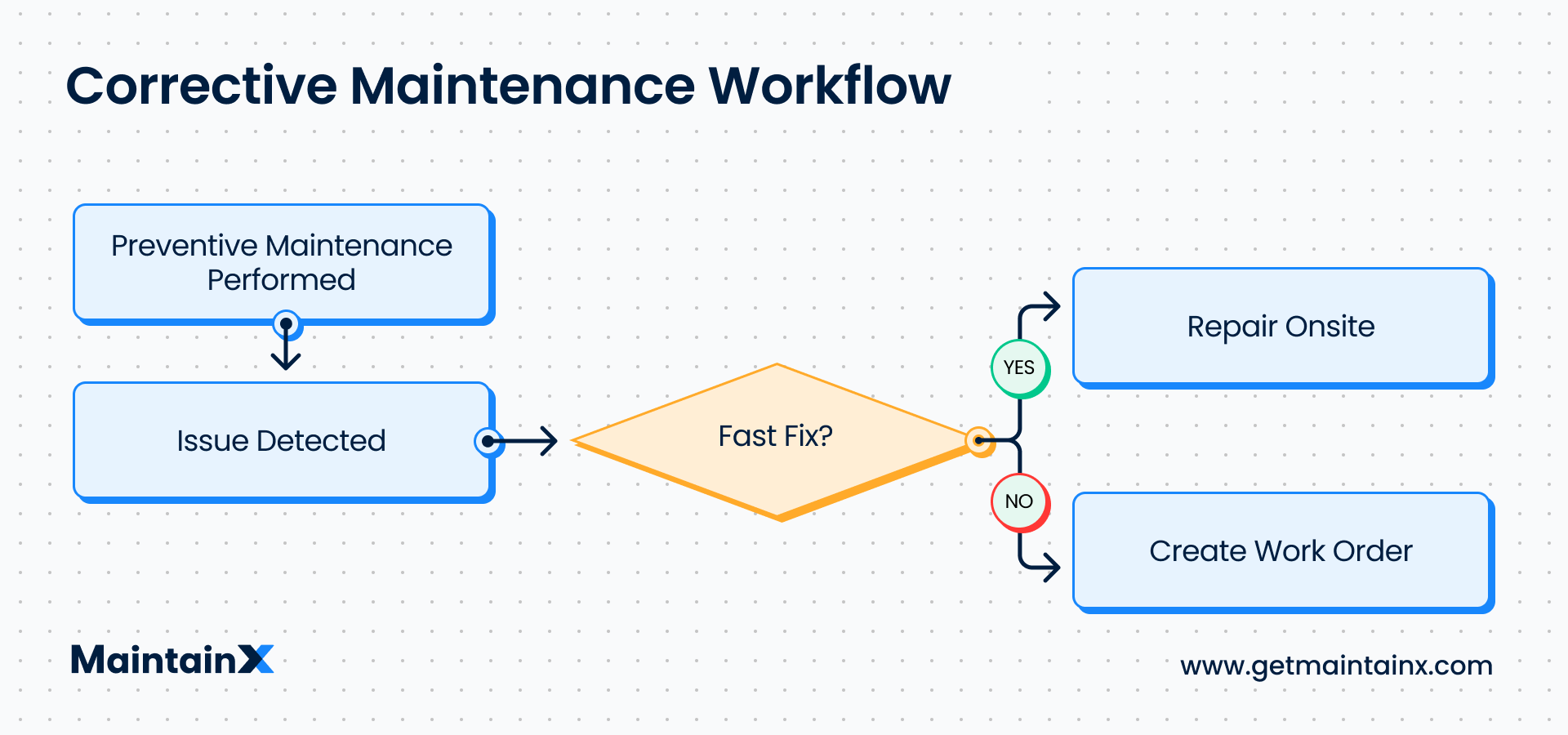
When to choose reactive maintenance
When considering implementing a reactive maintenance strategy, weigh the cost of performing regular maintenance against the cost of asset failure. If the cost of ongoing proactive maintenance outweighs the cost of downtime, repair, and replacement, reactive maintenance is the right maintenance program for that asset. Maintenance costs should never exceed those incurred from a breakdown.
Limitations of reactive maintenance
Although one major appeal of reactive maintenance is its cheapness, the short-term gains from limiting activities to only the assets that break down can often be offset by significant losses in the long term from increased downtime and production disruptions.
And in some instances, fixing assets after they break down can be costlier than preventing them from breaking down in the first place. Emergency repairs and replacement parts can be more expensive than regular maintenance work as they tend to require time and resources to restore availability.
Mostly, though, with reactive maintenance, you just don’t know. You don’t know the kind of day you’re going to have, what kind of schedule to realistically expect, what production output to anticipate, and how to make any serious plans. You go in each day knowing there’s a possibility someone grabs you in the hallway and stops you from eating lunch because something needs fixing right away.
As a maintenance manager, you want to be able to plan out your day knowing that, for the most part, things will follow a set schedule. You can take breaks at certain times, check in with workers at other times, and schedule meetings when convenient. Leaning entirely on a reactive strategy means everything is up in the air, which puts a lot of pressure on leaders.
As Sara Ghali, MaintainX Product Manager, puts it, “Imagine you’re driving a car, and it breaks down in the middle of the road. Your passengers are agitated and confused about what’s happening. You’re supposed to know what to do, and everyone is looking to you for a solution. What you’re feeling in that moment is stress, which is not at all the clear-headed approach you need when deciding how to fix equipment.”
Relying solely on a reactive maintenance program also introduces unnecessary risk to your operations. Unexpected equipment breakdowns pose a safety risk to operators and the employees on the shop floor. Lack of regular maintenance and inspection may lead to regulatory and compliance violations and fines. And the unpredictability of asset breakdowns makes it challenging to budget and allocate resources accordingly, posing a strain on company resources.
Preventive maintenance (planned or scheduled maintenance)
What is preventive maintenance?
Unlike reactive maintenance, preventive maintenance (PM) aims to prevent breakdowns from occurring in the first place. It is a proactive maintenance strategy built on regular and recurring activities that protect assets, keep equipment in good working condition, and prevent unplanned downtime.
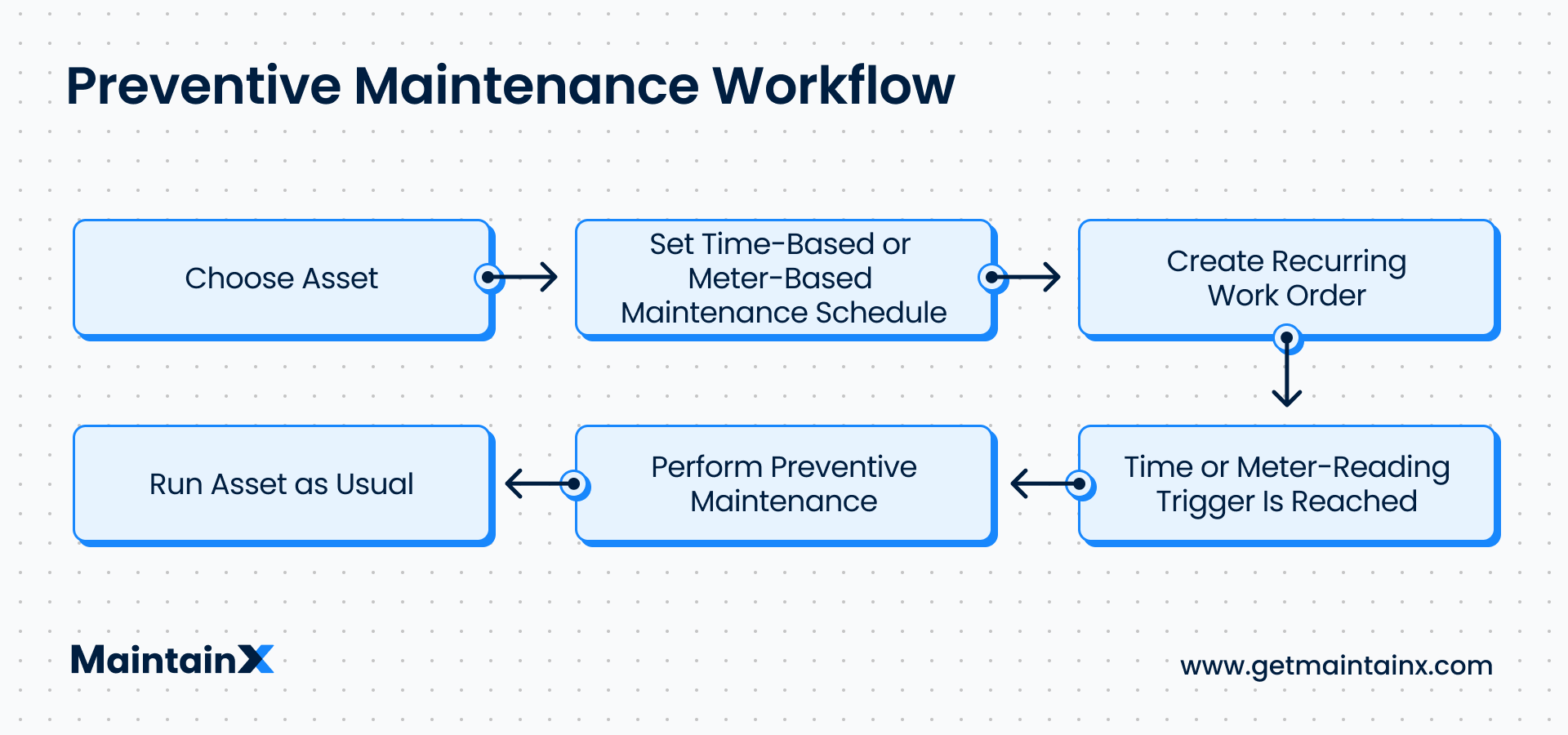
Preventive maintenance can follow a schedule based on usage, calendar, and time period. These types of scheduled maintenance fall under periodic maintenance.
When to choose preventive maintenance
PM is most effective when equipment and parts wear follow a predictable pattern, allowing you to schedule maintenance based on time intervals or usage. In addition, following manufacturer guidelines for maintenance ensures compliance with warranty conditions and aligns with established best practices based on extensive testing.
Preventive maintenance does much more than just keeping assets available for production. By keeping equipment in good working condition, you can ensure that you eliminate any potential issues with quality due to equipment malfunction. Optimal equipment will deliver optimal products.
Ultimately, maintenance is collaborative, and while reducing unplanned downtime is a key benefit of preventive maintenance, this maintenance strategy works hand-in-hand with quality and safety management.
Also, with a reactive strategy, you not only have no idea when your assets will fail but also how. It’s always a coin toss between small failures and breakdowns bearing serious health and safety consequences. Taking control with preventive maintenance means you can significantly reduce the risk of catastrophic failures that compromise the safety of your staff and facility.
To create an effective PM implementation strategy, begin with a thorough inventory of assets. Then, determine priorities by defining the pieces of equipment that require regular maintenance and are critical for production and safety.
Determine your ideal PM intervals based on your workforce capacity, individual asset requirements, and regulator requirements. After scheduling and implementing recurring work orders, be sure to constantly assess your progress to identify areas to improve and adjust your maintenance plans where necessary.
Examples of PM include:
- Conducting routine lubrication and alignment checks on electric motors to prevent overheating and ensure efficient operation, following a schedule based on operational hours.
- Replacing filters and inspecting ducts at regular intervals to maintain air quality and system efficiency, preventing unexpected breakdowns and prolonging equipment life.
Consider how long an asset will last without maintenance and how much it will cost to replace it, then weigh that against the potential cost of running regular PMs for that duration. Also, determine if these assets have failure modes that regular maintenance can prevent. If an asset only experiences failures due to random errors that preventive maintenance can’t address, preventive maintenance wastes time and money and becomes redundant.
Limitations of preventive maintenance
Preventive maintenance is a cost-effective approach that saves money by preventing breakdowns and any consequent production losses. The guiding principle is that the hours and resources spent on routine activities will add up to less than those that would otherwise go into restoring asset functionality during downtime.
However, finding that balance can be challenging. Poorly planned preventive maintenance can lead to redundant or unnecessary maintenance work, taking up assets and human resources that could be useful elsewhere. And managing multiple PM schedules for a range of assets can become increasingly complicated.
In addition, a preventive maintenance strategy is redundant for non-repairable or single-use assets. It’s usually best to replace assets that are either nearing the end of their life cycles or beyond repair rather than putting in the time and effort to prolong their already limited lives.
Condition-based maintenance (CBM)
What is condition-based maintenance?
Condition-Based Maintenance (CBM) is a proactive maintenance strategy focused on monitoring and evaluating the actual condition of equipment and assets to determine when you should perform maintenance. CBM relies on continuous or periodic monitoring of equipment condition using various diagnostic tools and techniques. Common methods include vibration analysis, thermography, oil analysis, and ultrasonic testing.
CBM can minimize downtime and reduce overall maintenance costs. With this strategy, you initiate maintenance tasks when certain indicators suggest a decrease in performance or impending failure. CBM is a reactive approach that can be less complex and expensive compared to predictive maintenance, which we discuss below.
For example, a common application of condition-based maintenance involves using pressure readings on piping systems. Maintenance staff constantly monitor pressure levels, allowing them to identify when potential leaks may occur. Organizations that rely on pipe or liquid systems, like food and beverage producers, use CBM to track pressure and diagnose problems.
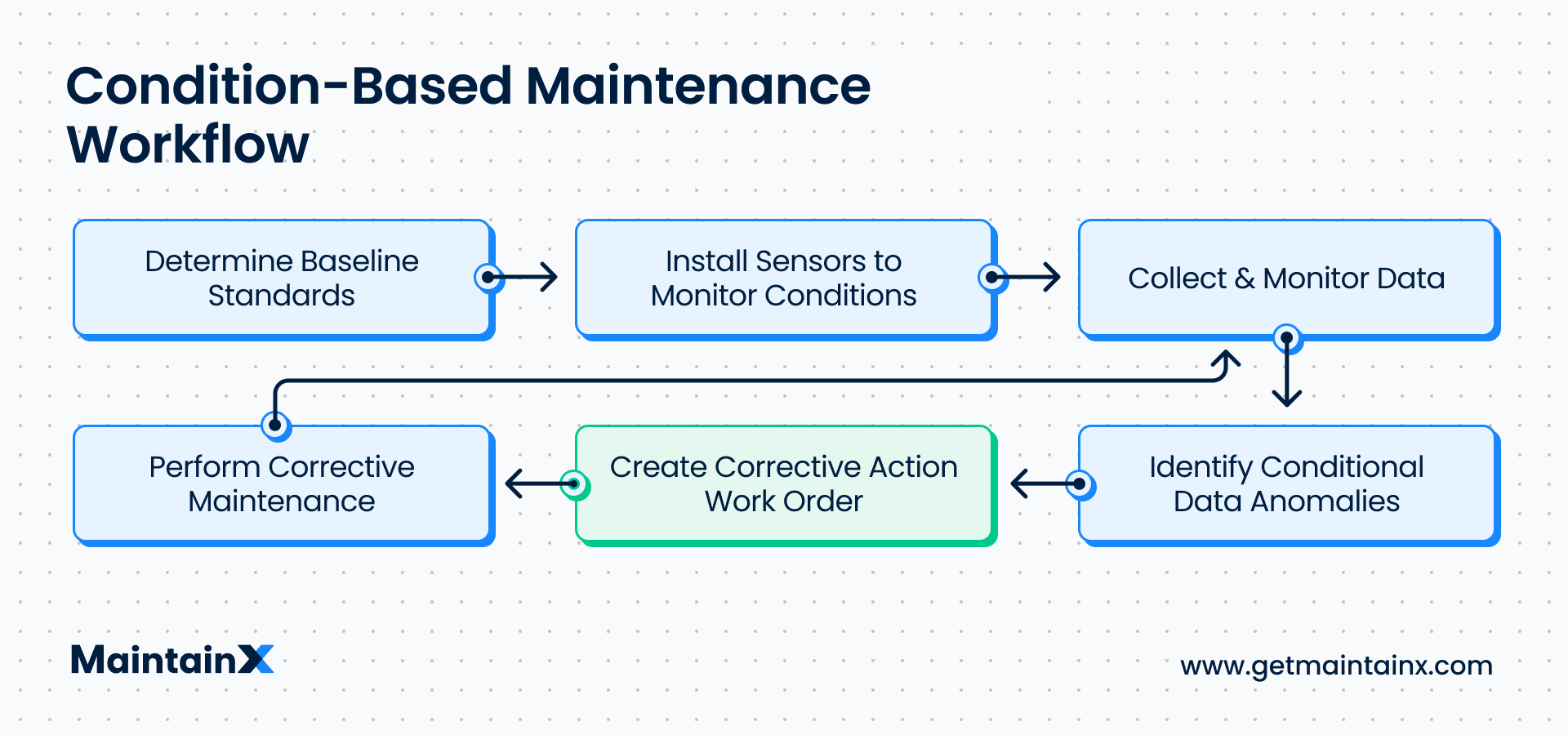
6 primary condition-based monitoring techniques
CBM technologies continuously collect data while equipment operates. These devices record numbers at given intervals or continuously through visual inspections, sensors, and scheduled tests. The six primary condition-based monitoring techniques include the following:
Vibration Analysis: This type of condition-based monitoring system measures the vibration frequencies and levels of machinery. Maintenance teams then use this information to analyze the health of equipment and its components to detect problems, such as bent shafts, resonance, looseness, bearing failure, and imbalance. For example, a damaged fan will produce more vibration signals.
Infrared Thermography: Infrared thermography is a condition-based monitoring system that uses thermal imagers to detect radiation from an object. The imagers convert the radiation to temperature and display its distribution in real time. This process helps detect when a piece of equipment is overheating. Examples of infrared tools include infrared thermal imaging cameras, infrared scanning systems, and infrared thermographers. Maintenance teams mostly use them to check the levels of gas, liquids, and sludge; inspect bearings; examine refractory insulation; and monitor mechanical and electrical conditions of motors.
Ultrasonic Analysis: Ultrasonic analysis detects and converts high-frequency sounds into audio and digital data to help identify potentially failing assets. This condition-based monitoring system uses contact and non-contact data collection methods to determine different types of detectable failure. Contact (structure-borne) methods generally detect faults that generate high-frequency noise, such as lubrication problems, bearing faults, broken rotor bars, and gear damage. Non-contact (airborne) methods, on the other hand, help detect pressure and vacuum leaks on compressed gas systems in addition to various electrical applications.
Oil Analysis: Maintenance teams analyze oil health, contamination, and machine wear. They can determine whether the additives are active or depleted and whether the viscosity is correct, among other oil fluid properties. An oil analysis program will help to confirm if a piece of equipment is operating as it should.
Electrical Analysis: Here, the focus is on the incoming power quality of assets. Circuit current is measured using motor current readings from clamp-on ammeters. Electrical analysis helps determine if an asset has an abnormal electricity supply.
Pressure Analysis: It’s important for equipment carrying air, gas, or fluid to maintain the correct pressure. Maintenance teams use pressure analysis to continuously monitor real-time pressure levels. They get alerts to sudden drops or spikes and can respond before it becomes more serious.
When to choose condition-based maintenance
Condition-based maintenance is most effective when applied to critical equipment and assets that would significantly impact production, safety, or operations upon failure or have high maintenance and repair costs. CBM works best with assets that have well-defined failure modes and experience gradual and predictable wear and tear over time. Before choosing CBM, ensure that you have ready access to monitoring technologies, such as sensors, that are compatible with your equipment.
Limitations of condition-based maintenance
CBM offers several advantages, but it's important to recognize its limitations as well. First off, the initial costs of implementing condition-based monitoring systems can be high due to the need to invest in sensors, meters, and other monitoring instruments.
Condition-based maintenance may also be less effective in harsh working conditions, where sensors are vulnerable to damage or exposed to noise. Additionally, CBM is most effective for critical assets that have well-documented failure modes where early detection of issues can prevent cost breakdowns. For less critical or simpler equipment, the cost and effort of implementing CBM may be difficult to justify.
Reliability-centered maintenance (RCM)
What is reliability-centered maintenance?
Reliability-centered maintenance (RCM) focuses on creating systematic and structured approaches for maintaining individual assets. Its primary goal is to ensure that maintenance efforts focus on activities that maximize the reliability and performance of assets while minimizing costs and operational risks. RCM involves first conducting a detailed analysis of possible failure modes and their potential impact and then creating custom plans to prevent them.
RCM aims to answer four critical questions about the maintenance of individual assets:
- What are the functions of the asset? How has it performed in the past?
- What are the potential failure modes and causes for each asset?
- What are the consequences of these failures in terms of safety, environmental impact, and financial losses?
- Which maintenance tasks, whether proactive (preventive) or corrective, should teams apply to mitigate these consequences?
You want to assess the potential consequences of the failures to figure out how to prevent them. Repeat this for all assets, creating a tailored maintenance approach for each piece of equipment, improving reliability, and ensuring assets remain available at all times.
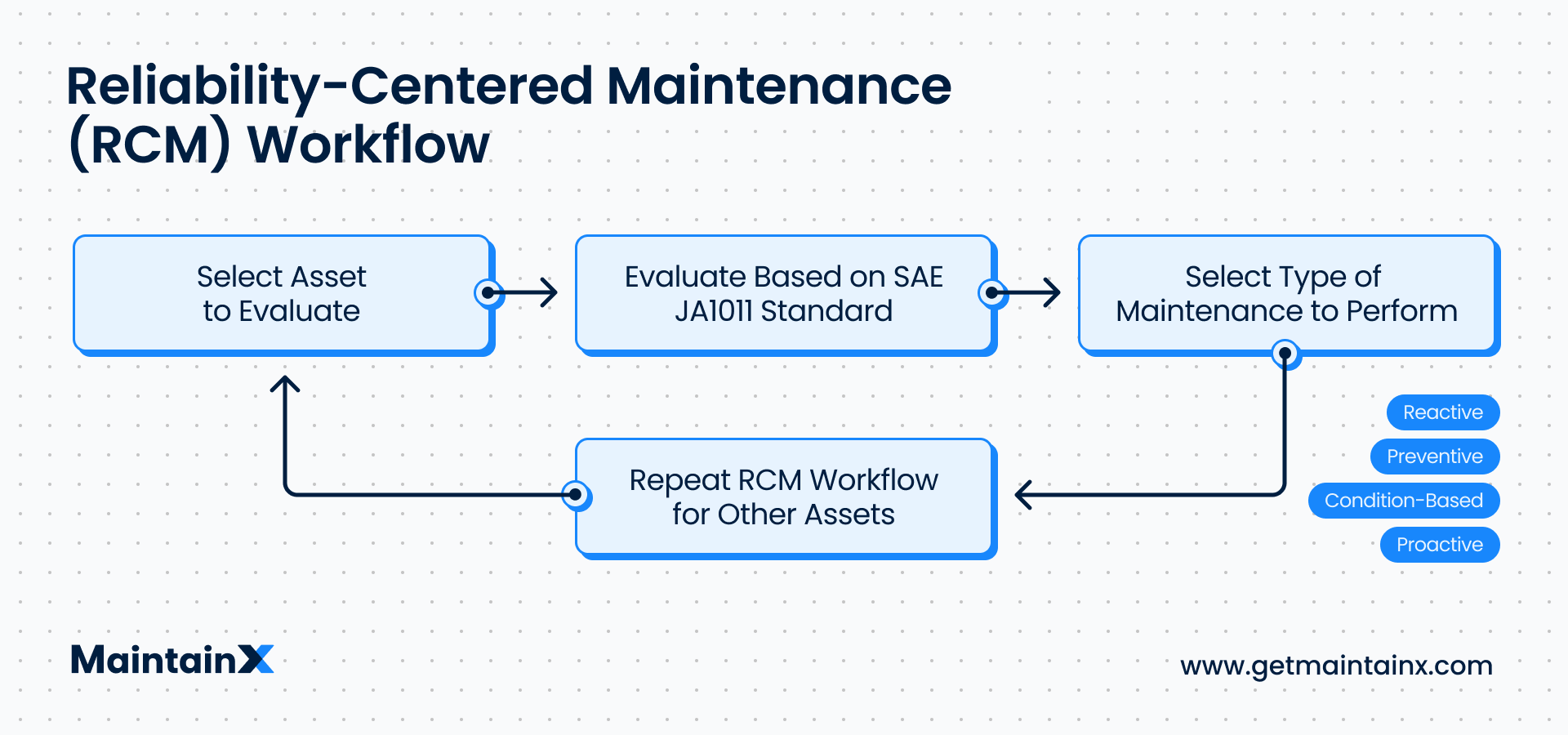
When to choose reliability-centered maintenance
If you need to assign maintenance strategies based on specific equipment needs, RCM is a great idea. Instead of applying one maintenance strategy (preventive, reactive, or predictive) across the entire facility, RCM optimizes data to customize solutions by ranking assets according to criticality. As such, RCM is a good fit for facilities with assets that vary significantly in criticality and helps teams optimize resources based on priority.
Limitations of reliability-centered maintenance
By providing custom solutions for different assets, RCM can be incredibly powerful when dealing with equipment whose malfunctions could have disastrous impacts on revenue, production, and safety. However, creating these solutions requires detailed maintenance data, an elaborate integration process, and a lot of time and resources.
If you have the resources to dedicate staff to integrate RCM across your assets or are willing to work with a partner experienced in this field, then this might be for you.
Similarly, if you have detailed and clear maintenance logs, you’ll have an easier time implementing RCM. Without the proper data, RCM can be more challenging than it’s worth.
Predictive maintenance (PdM)
What is predictive maintenance?
As opposed to reactive condition-based maintenance, predictive maintenance (PdM) is a form of proactive maintenance that functions by using equipment condition information (like temperature, pressure, and other asset health factors) to predict imminent failure.
Unlike condition-based maintenance, the condition-based data collected incorporates advanced analytics, data mining, and machine learning algorithms, which look for patterns and trends to predict the future state of the asset. Maintenance teams can use the equipment downtime predictions to isolate maintenance tasks to only the most necessary assets to reduce any redundant maintenance work.
The key distinction between CBM and PdM is that PdM focuses on forecasting future conditions to optimize maintenance planning, whereas CBM primarily reacts to current equipment conditions.
IIoT and predictive maintenance
PdM uses condition-monitoring sensors to track equipment conditions in real time. These sensors function by means of the IIoT (Industrial Internet of Things), which are devices and interconnected instruments networked with computer applications to enhance manufacturing, maintenance, and other industrial activities.
Examples of PdM sensor devices are vibration analysis equipment, ultrasonic acoustic technology, and other equipment that monitor factors related to equipment health.
PdM feeds the data collected through the sensors into machine learning algorithms to predict potential failures by comparing an asset’s present behavior with its expected behavior. In this case, anomaly (abnormal behavior) detection triggers PdM.
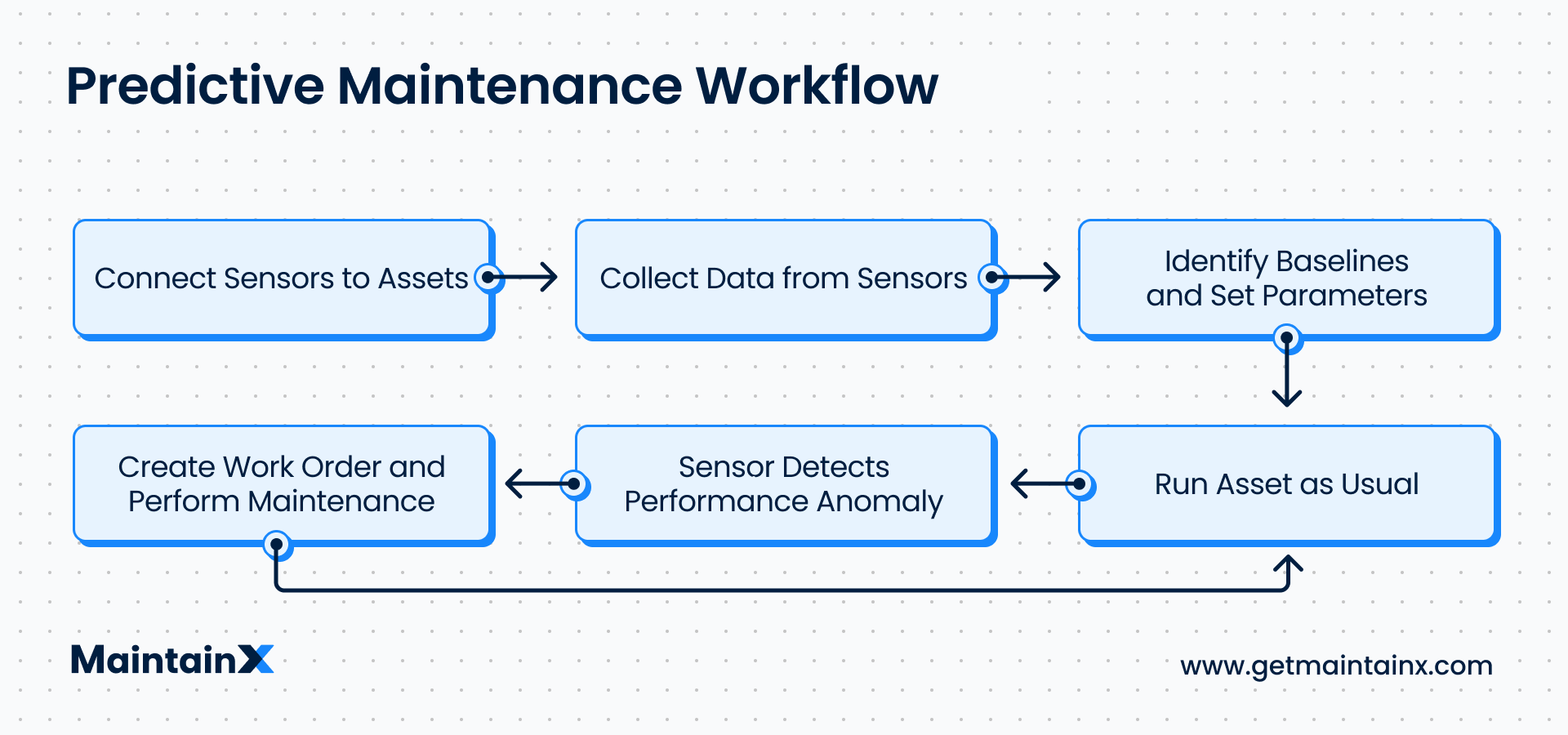
When to choose predictive maintenance
Implementing predictive maintenance only makes sense when you have the necessary data collection and analysis capabilities in place, as it relies heavily on real-time monitoring and analysis of equipment conditions through complex predictive algorithms. Without the necessary infrastructure in place or the willingness to invest in the required infrastructure, implementing a predictive maintenance strategy successfully is difficult. However, for maintenance teams ready or willing to invest in predictive maintenance, you can increase the reliability of assets, decrease maintenance costs, and reduce unplanned downtime.
Maintenance strategies summary chart
Choosing the right maintenance strategy for your facility
In practice, you’ll be hard-pressed to find a facility that depends exclusively on one strategy. As much as a preventive maintenance program helps to reduce costs, maintain uptime, and prevent emergency shutdowns, a reactive maintenance plan is necessary to handle emergencies when they occur. Consider these factors as you build your maintenance program:
- The assets in question: Thoroughly examine your asset register to determine which type of maintenance each asset requires. What do manufacturer guidelines say regarding how and when to approach maintenance? Do any compliance regulations apply to particular pieces of equipment? What do you and your maintenance team notice about these assets, and how do they perform when used? Consider the potential costs of equipment failure for each asset and the cost of equipment monitoring to prioritize maintenance on specific assets.
- Internal capabilities and resources: No matter how robust your resources are, you don’t want to waste any of them. Think about ways to optimize your maintenance staff and spare parts when creating a maintenance strategy. Do you have enough staff to implement each of your maintenance strategies? And what would it cost you to rely strictly on reactive maintenance?
- Data, data, data: When implementing any strategy, be sure to collect, record, and analyze data constantly. Use this data to identify which actions produce your desired results and which do not. “Robust data saves you the trouble and energy of remembering things,” Sara Ghali says. “Even in the absence of an expert, the knowledge is within the system. Not only will you have access to knowledge about how you handled problems in the past, but you’ll be able to identify trends, institute incremental improvements, and optimize your time management.” With this in mind, continue to reiterate and fine-tune your maintenance approach for constant improvement.
Take your maintenance to the next level
Choosing the right type of maintenance is specific to your company and to each asset. While specific strategies may seem perfect on paper, the right strategy for you will always be the one you can successfully implement.
As you set about implementing your chosen strategy, remember you don’t have to do it alone. Book a tour with MaintainX to find out how our computerized maintenance management system (CMMS) can help you build or improve your maintenance strategy.
FAQs
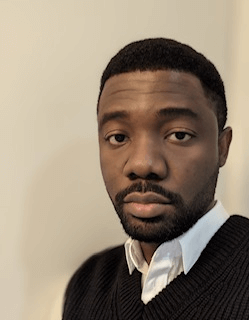
Lekan Olanrewaju is a content writer with years of experience in media and content creation. He has held positions at various media organizations, working with and leading teams at print magazines, digital publications, and television productions.