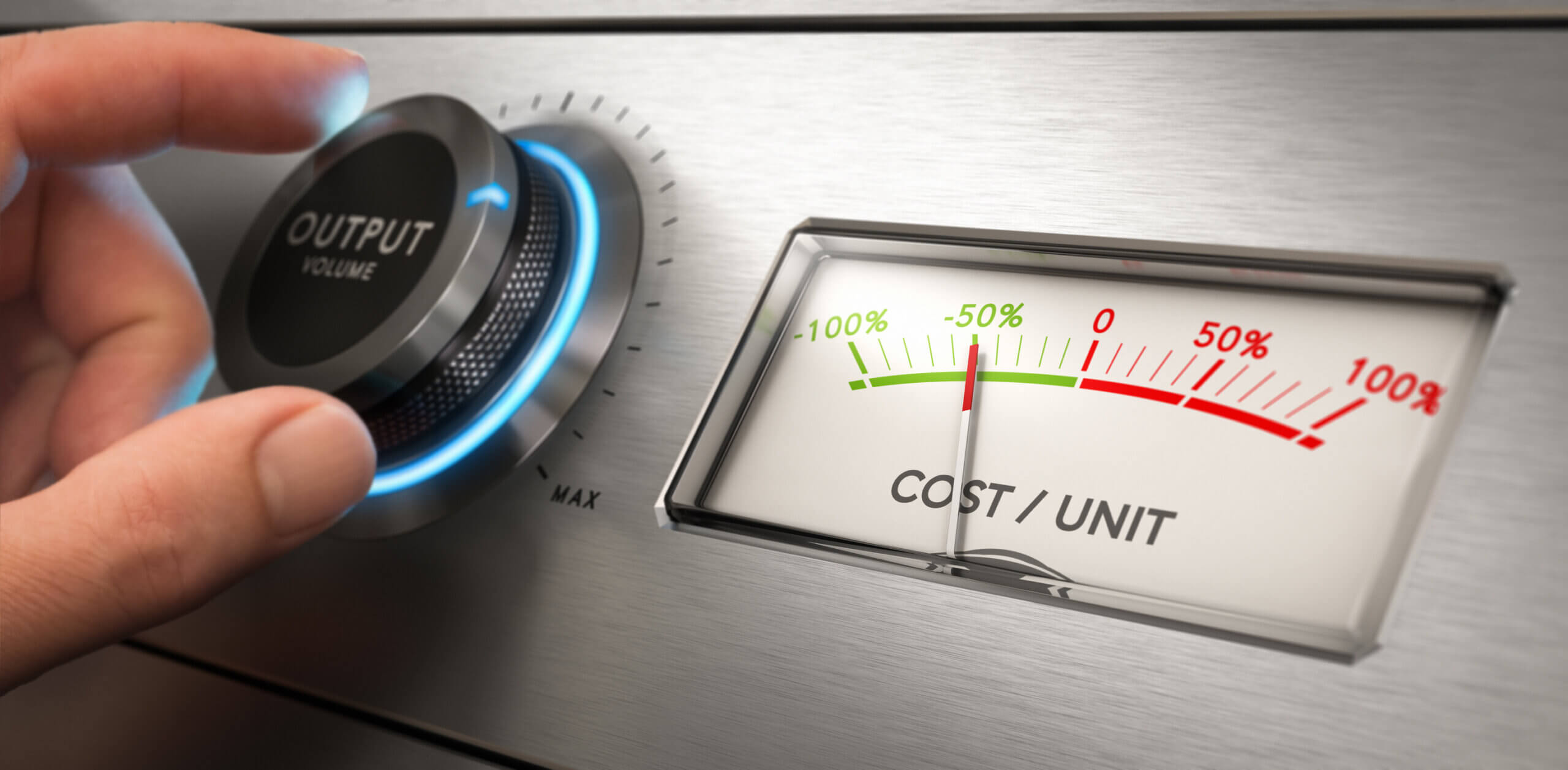
Total Manufacturing Cost (TMC) measures how much companies spend on their manufacturing operations. This goes beyond simply looking at balance sheets and income statements. Manufacturing companies often use many concepts to gain insight into their financial circumstances.
Total Manufacturing Cost is one of these concepts. It specifically measures how much you spend to produce your finished goods inventory during a set period. It focuses on production costs, raw materials, direct labor, and manufacturing overhead.
What about the Cost of Goods Manufactured?
If you’ve heard about the Cost of Goods Manufactured (COGM), you might assume it’s the same as Total Manufacturing Cost. And while they are similar, there are crucial differences between both concepts.
Like TMC, COGM considers a company’s total expenses while producing a finished product. However, COGM specifically looks at the cost of producing inventory and putting it up for sale. Therefore, total Manufacturing Cost includes all costs a company incurs in the manufacturing process, whether the goods are prepared for sale or not.
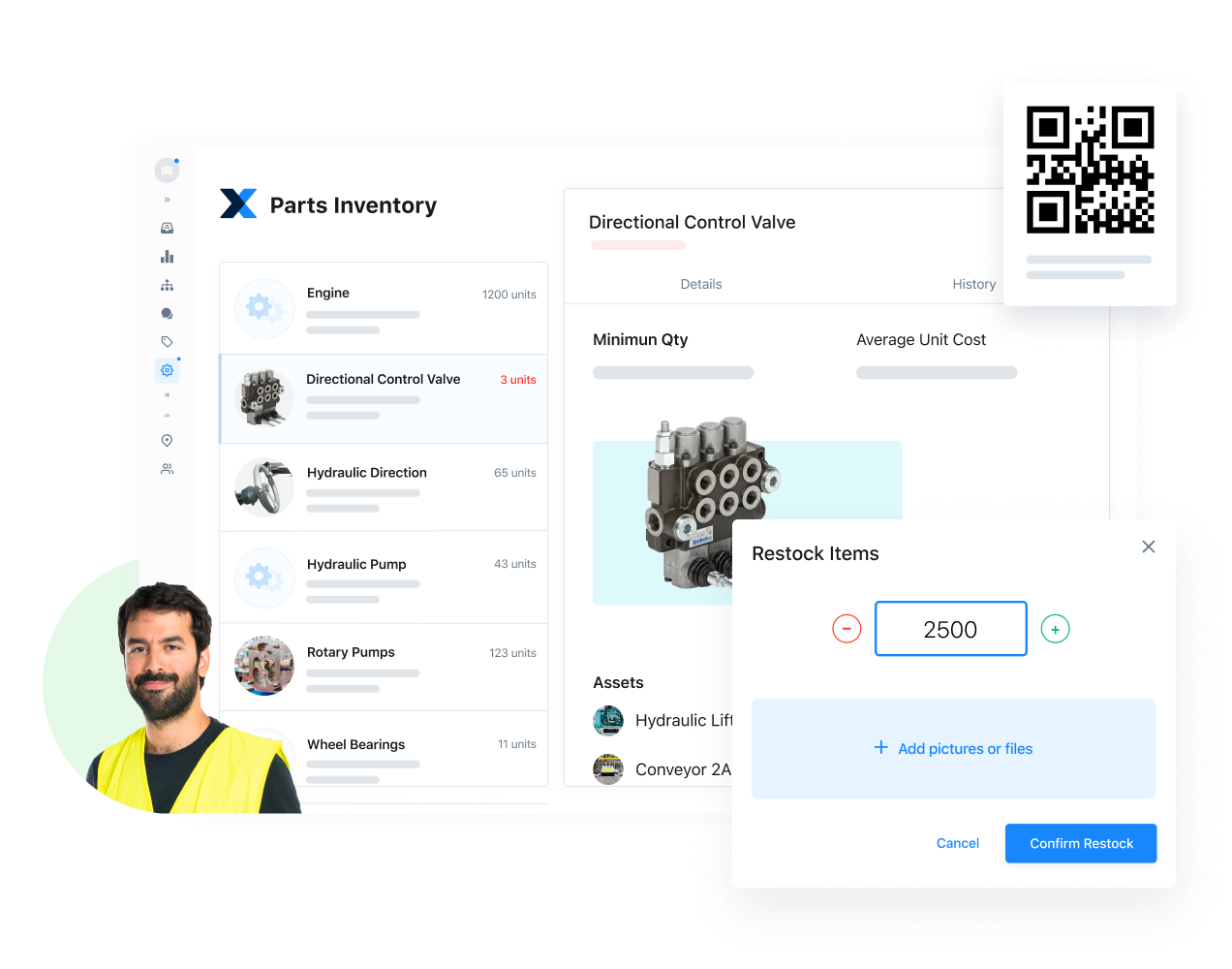
TMC vs. COGS
Furthermore, Total Manufacturing Cost differs from the costs of goods (COGS). Where the total manufacturing cost is the total expense related to all labor and supplies used to create a finished product, COGS sold are simply the cost of finished inventory sold within the reporting period.
What Do Total Manufacturing Costs Include?
To calculate your Total Manufacturing Cost, you’ll need to understand three main categories of expenses: direct material costs, direct labor costs, and manufacturing overhead costs. So let’s consider each of these a bit more closely.
Direct Material Costs
As the name implies, direct materials go directly into making a product. Other indirect materials might go into other production areas, but this area focuses on the cost of raw materials that go into making a final product.
To calculate your total direct material costs, you need to figure out your direct materials and calculate how much you spent on them. To do this, figure out how much of the direct materials you already have, then add the total cost of the new direct materials. Finally, when you reach the end of the period, subtract whatever ending inventory you still have. This way, you’re left with the costs of only the materials you used during this period.
Direct Labor Costs
Direct labor includes all the work that goes into making the final product. Costs here include workers’ compensation such as salaries, pensions, holiday pay, payroll taxes, etc. Like direct material costs, this focuses on the labor involved in making the product.
As such, you should be concerned with how much you spend paying machine operators, assembly line supervisors, quality assurance staff, and other shop floor workers. Janitorial staff, Human Resources, and other staff not directly involved in the production process will fall into the indirect labor category. As a result of this, they do not count here.
“With manufacturers hit on multiple fronts, they’re looking well beyond the traditional cost-containment playbook to preserve margins. Pricing that perfectly aligns with cost of goods or just-in-time inventory management approaches seem like quaint and distant memories.”
PWC
Manufacturing Overhead Costs
Manufacturing overhead includes indirect manufacturing costs you incur to keep your production running smoothly. Manufacturing costs can be fixed, variable, or semi-variable.
- Fixed Overhead Costs: These costs remain the same regardless of the company’s production scale. Whatever quantity of goods the company produces, these overhead costs do not change. Examples include rent and property taxes. In other words, if you rent a production facility, the rent doesn’t increase or reduce based on how much production you carry out inside.
- Variable Overhead Costs: Unlike fixed overhead costs, variable overhead costs depend on the scale of production. Higher production volumes lead to increased variable overhead costs. Utility costs fall in this category. A higher production volume means you will use more electric power, gas, or other forms of fuel.
- Semi-variable Overhead Costs: These costs remain the same at certain stages but increase based on production output. For example, insurance rates typically include a base rate and then increase based on performance.
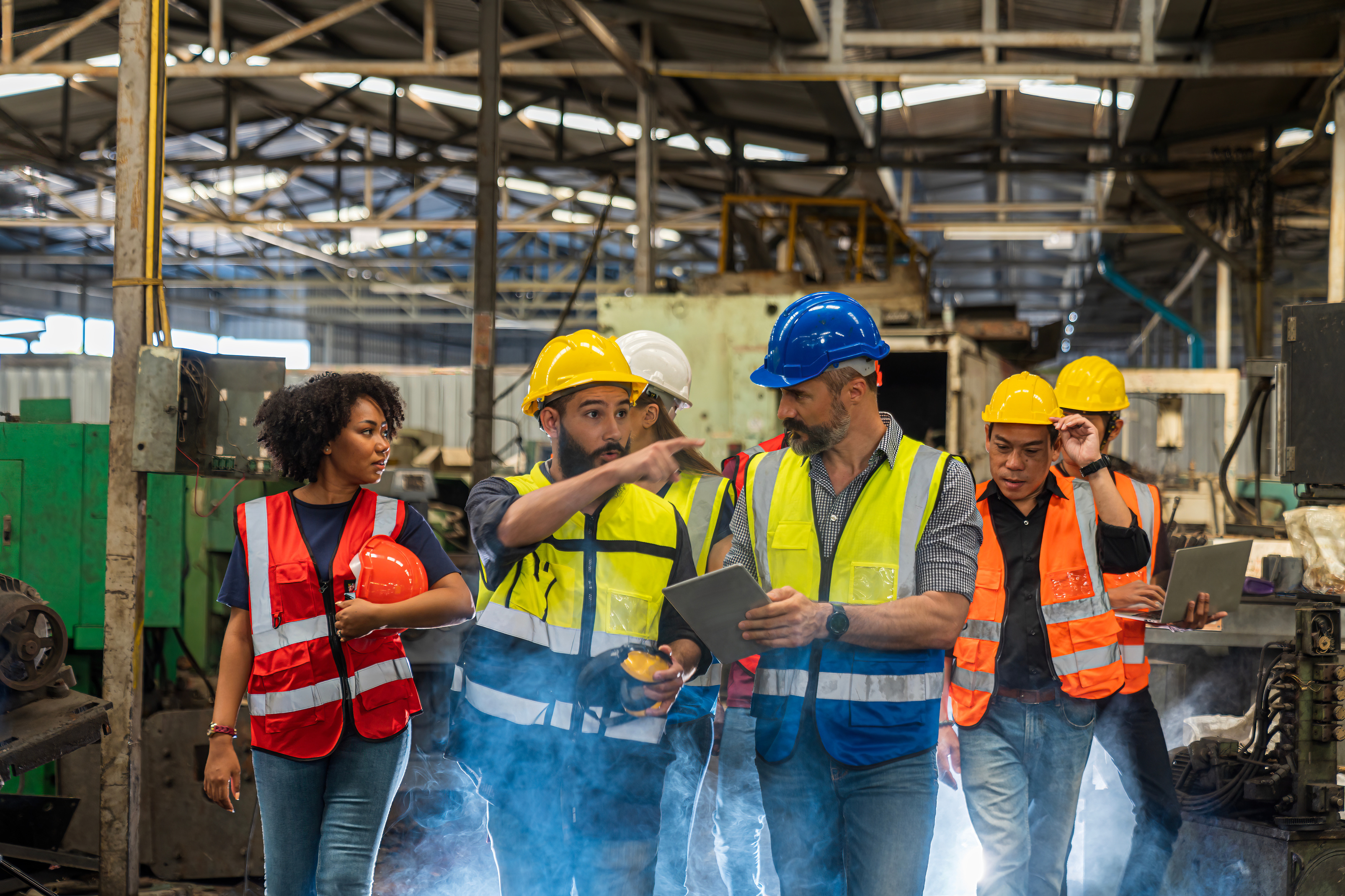
How to Calculate Total Manufacturing Costs
The total manufacturing cost is the sum of all the direct and indirect costs of producing a product. TMC includes raw material costs, labor costs, and any overhead (including any other expenses from the process).
To calculate TPM:
- Raw materials: Include costs of all materials needed to produce the product. Also include the cost of any other materials used in the manufacturing (i.e., shipping costs).
- Direct labor: Includes employee wages and benefits directly involved in producing the product. Multiply the number of hours worked by the hourly wage/benefit rate.
- Manufacturing overhead: Includes indirect costs of the manufacturing process (i.e., maintenance costs, rent, utilities, insurance, and depreciation of manufacturing equipment).
- Add up all the costs: Add the cost of raw materials, direct labor, and manufacturing overhead to get the total manufacturing cost.
Total Manufacturing Cost Formula
Total Manufacturing Cost = Raw Materials Cost = Direct Labor Costs + Manufacturing Overhead
Why Calculate Your Total Manufacturing Costs?
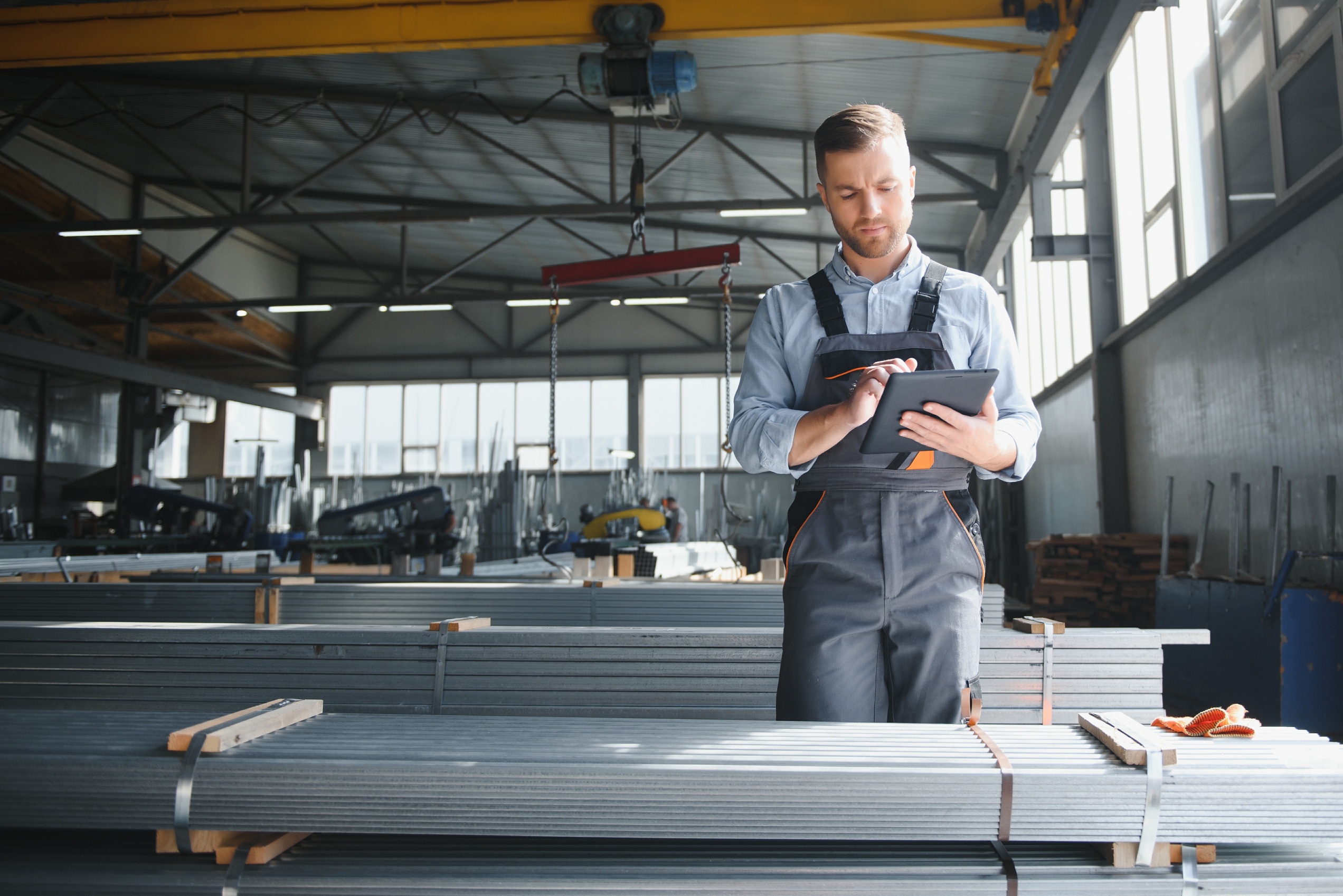
Knowing your manufacturing costs is fundamental when working towards profitability. Instead of setting arbitrary unit prices for your finished goods, you have a cost baseline to work with. Of course, you’ll want to consider market conditions, but knowing your manufacturing cost will allow you to take a multi-pronged approach for a more robust pricing plan.
A clear picture of your manufacturing costs can also help you to optimize your supply chain handling and manage your spending. Calculating this metric requires paying close attention to your direct costs. As a result, you can points of waste in the supply chain that you might otherwise have overlooked.
Get a CMMS to Help Calculate Your TMC
Helps You Collect Accurate Data
The first step in calculating your manufacturing costs is identifying and calculating all your direct costs. A CMMS can help you get a more accurate picture of these costs by tracking data.
For example, using a CMMS to track work orders can help you assess the labor hours involved in making a specific product. Similarly, a good CMMS will come with inventory management functionalities to help you track your direct materials.
Helps You Store Your Documents
Store documents: Many CMMS solutions have functionality for storing your documents. MaintainX, for example, offers cloud-based document storage. This means you can keep all the necessary documents relating to your direct costs in one place. Anyone who needs access to, say, a bill of materials knows where to find it.
Helps You Establish Standard Operating Procedures (SOPs)
Staying in good financial health means maintaining robust documentation. Whether it’s a bill of materials or a balance sheet, you want any responsible parties to know exactly what process to follow in your team. A good CMMS can help you create and share operating procedures to standardize your documentation processes.
Helps You Analyze Data over Time
With a CMMS like MaintainX, you can access dashboards that can help you analyze data over time. You can create visualizations and take advantage of the app’s reporting feature, which gives you powerful insight into your data.
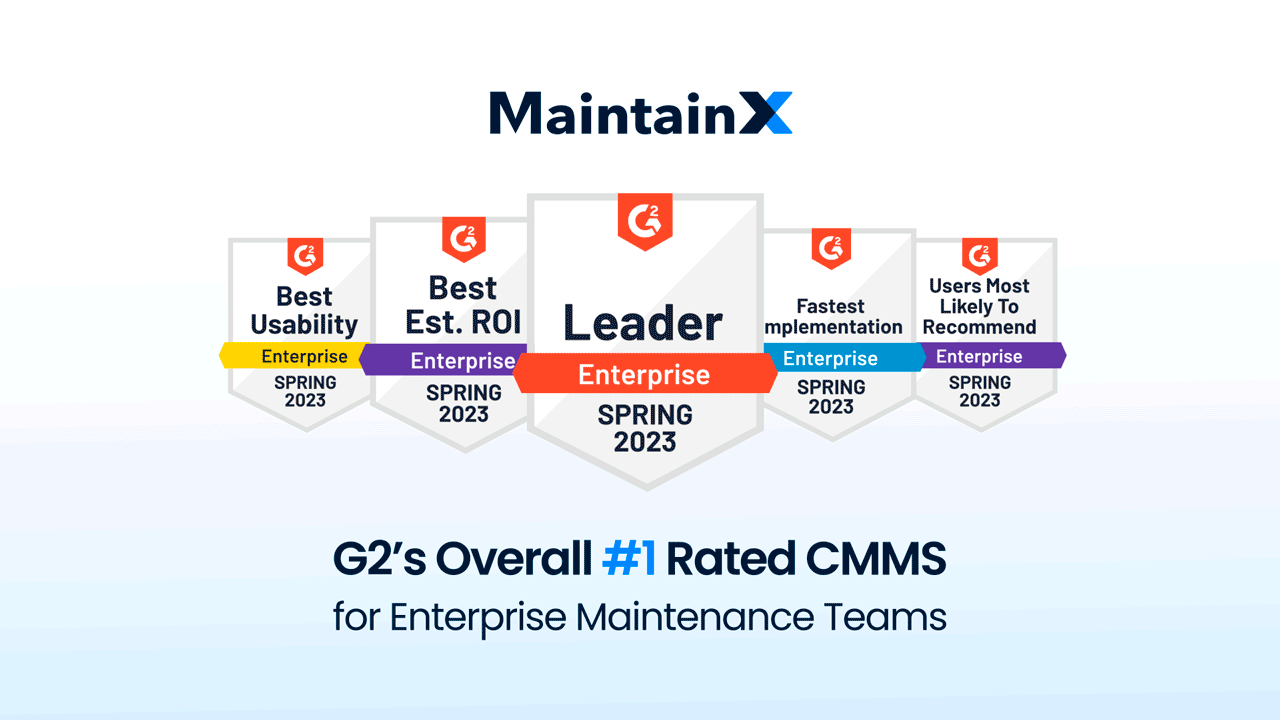
Track Your Operating Costs with MaintainX
Looking to keep track of your operations? MaintainX is a Computerized Maintenance Management Software that helps you automate work processes and get real-time updates from the shop floor. If you’re looking to streamline your workflows, transition from pen-and-paper processes to digital ones, or reduce your downtime with preventive maintenance, try MaintainX today!
FAQs
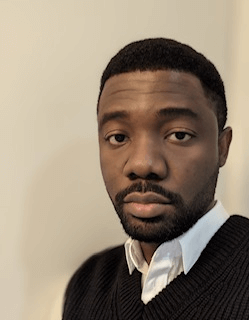
Lekan Olanrewaju is a content writer with years of experience in media and content creation. He has held positions at various media organizations, working with and leading teams at print magazines, digital publications, and television productions.