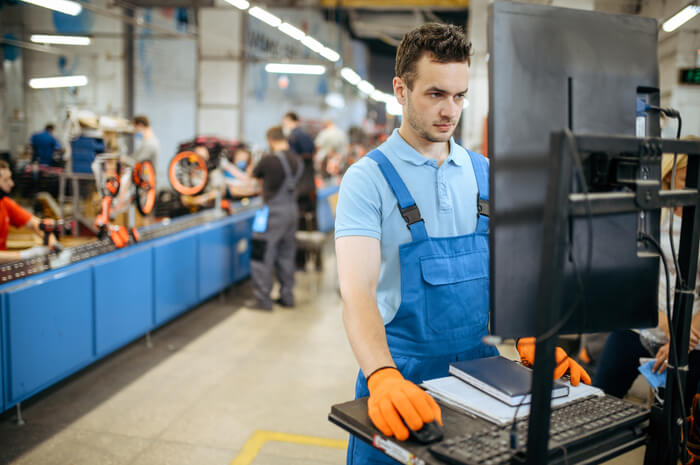
Are equipment failures driving up maintenance costs and unplanned downtime?
Let's face it: when your equipment fails, it's not just an inconvenience—it's a hit to your bottom line. Imagine a world where you could predict and prevent these disruptions and breakdowns. That's the power of a preventive maintenance program.
In this comprehensive guide, we'll explain the eight essential steps to building a robust PM plan that will save you money and transform your approach to proactive maintenance. We'll dive into the nitty-gritty of asset inventory, prioritization, scheduling, and the pivotal role of CMMS software in building a preventive maintenance plan.
Whether you're a seasoned maintenance pro or just dipping your toes into proactive strategies, this guide is your roadmap to a smoother, more efficient, and ultimately more profitable operation.
What is a Preventive Maintenance Plan?
A Preventive Maintenance Plan is a systematic approach to proactively maintaining and servicing equipment, machinery, or assets to prevent breakdowns, reduce downtime, and extend their operational lifespan. This type of maintenance is performed on a scheduled basis, often according to the manufacturer's recommendations or industry best practices.
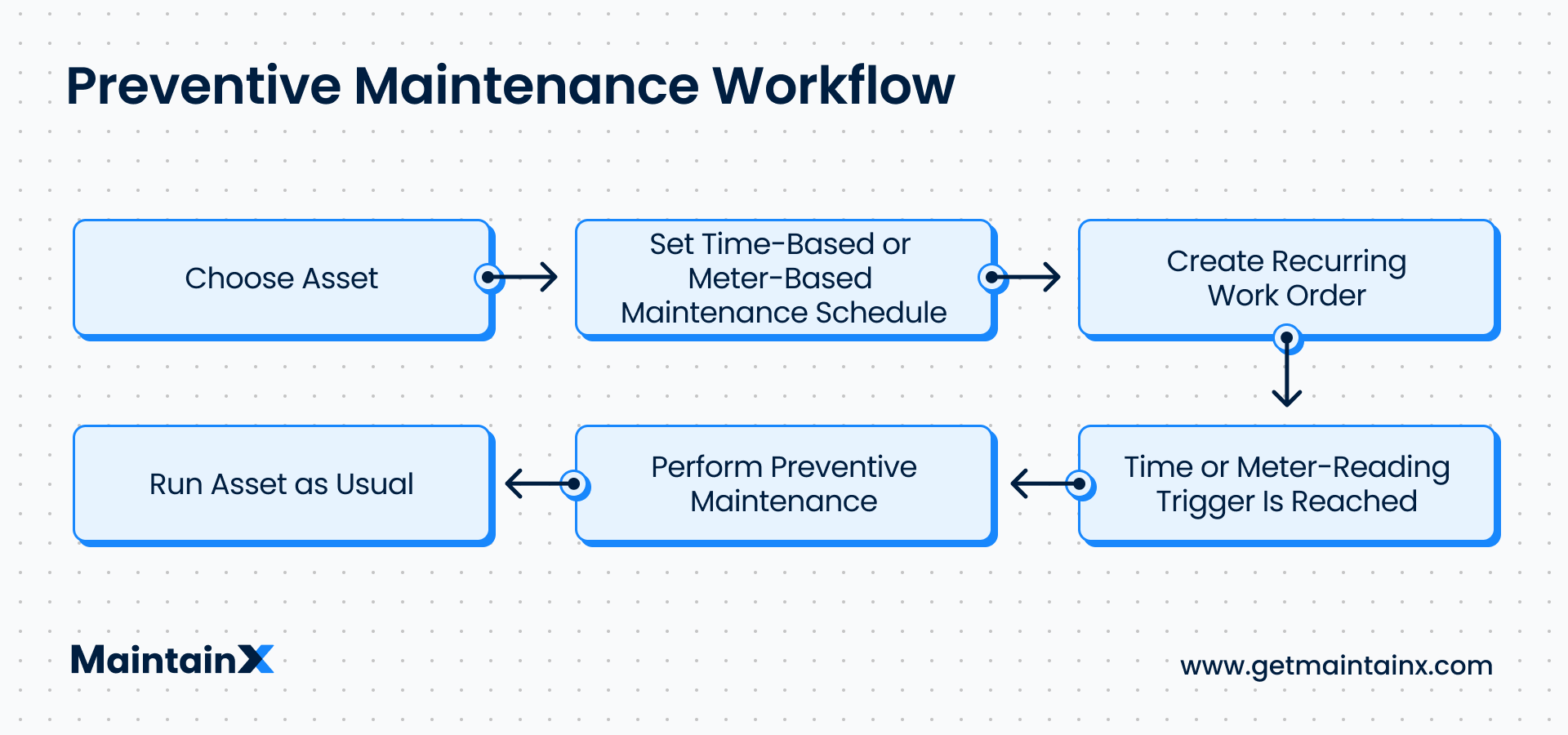
Essential Elements of Effective Preventive Maintenance Plans
Preventive maintenance plans look different for everyone, but here are some essential elements that form the foundation of effective ones. Let's explore these building blocks that make your PM program a true powerhouse for efficiency and cost savings.
1. Asset inventory
Preventive maintenance is an excellent maintenance strategy for keeping critical assets in good working condition. However, the real cost savings in PM come from fine-tuning your organization’s preventive maintenance schedule over time.
Workplace environments, machine usage patterns, and other factors can uniquely impact equipment behavior over time. Translation: Manufacturer’s recommendations won’t always provide foolproof guidelines for maintaining asset reliability.
Beyond the importance of maintaining detailed asset inventories for accounting records, consistent record-keeping can reveal opportunities to optimize spending patterns.
Each asset entry should include:
- Make, model, and serial number
- Specifications/Capabilities
- Unit number
- Category
- Location
- QR/Barcode
As you perform routine maintenance, keep track of service dates, labor costs, spare parts used, and current conditions. Also, note the asset’s criticality to production and safety.
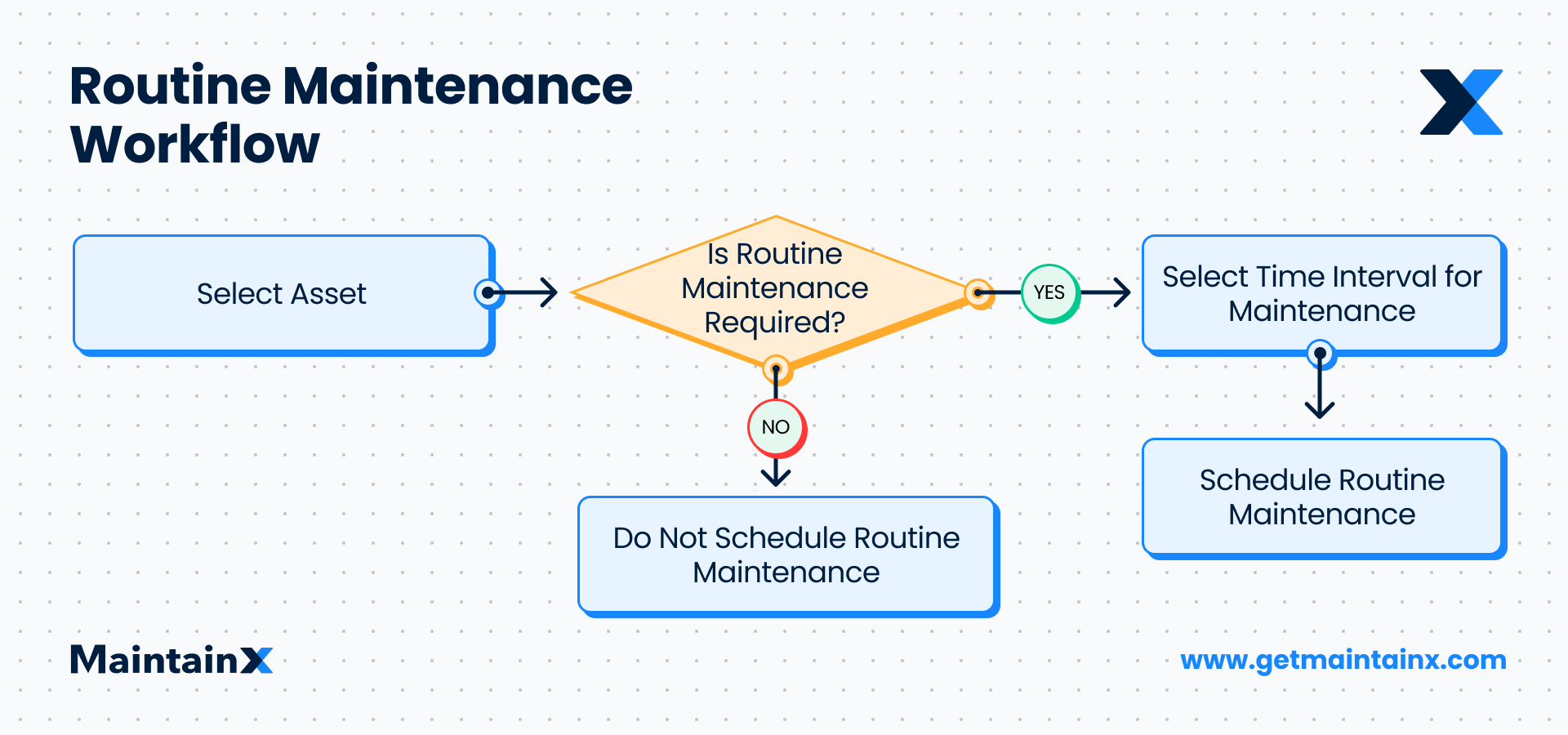
2. Asset prioritization
It’s impossible to include all essential assets in initial PM programs. To stay realistic, create an asset hierarchy and identify your organization’s most critical assets.
An asset hierarchy is a logical index of every critical machine and component that illustrates how the action of one machine affects another. Maintenance team members can use the tool to track machines more easily, schedule maintenance efficiently, and identify the root cause of failures.
Prioritize assets that significantly impact production, have high maintenance costs, require regular maintenance, or pose safety hazards. Once you start to see the increased value and return on investment (ROI) from the maintained assets, you can gradually add more assets to the PM program.
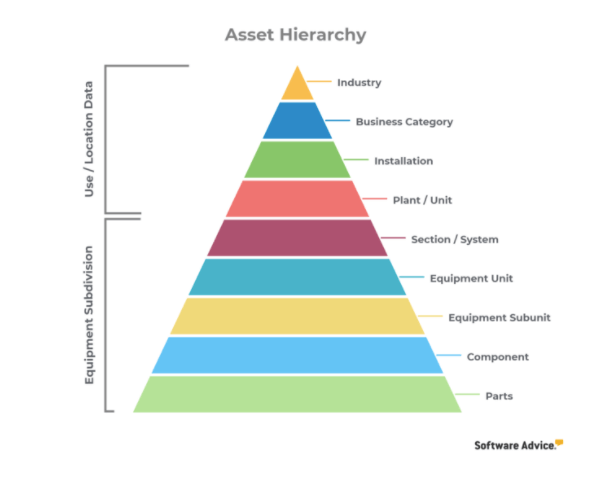
Some organizations may choose to perform a criticality analysis during the preventive maintenance planning stage to help them determine precisely how specific asset failures impact production and the bottom line.
3. PM schedule
A PM schedule dictates when maintenance activities should be performed on a given piece of equipment. When developing your PM schedule, select a day and time for maintenance that doesn’t disrupt production. Base PM schedules on one of two metrics:
- Time: You can base your PM schedule on time and perform maintenance after a set period. For example, your fleet of vehicles can undergo maintenance every three months.
- Usage: Track usage metrics such as operating hours and production cycles for usage-based PM schedules. Maintenance activities are then performed when certain milestones are met. For example, schedule your fleet of vehicles for maintenance every 1,000 miles instead of every three months.
PM schedules usually depend on a work order system. A work order is a document that provides details about a maintenance task and outlines the preventive maintenance process for completing it.
It details the scope of the work, what’s expected, the expected timeline for completing the job, who authorized the work orders, and an assigned maintenance technician. Work orders help you organize, assign, prioritize, track, and complete maintenance tasks besides capturing asset maintenance history.
4. CMMS software
Most effective PM programs have one thing in common: a computerized maintenance management system (CMMS) that the entire team feels comfortable using. Maintenance planners can create, implement, and track recurring work orders via user-friendly dashboards.
Additionally, a CMMS helps to simplify, automate, organize, and optimize your operations. According to Plant Engineering, 58 percent of facilities rely on CMMS to manage their maintenance operations.
However, up to 80 percent of CMMS implementations fail. Reasons for CMMS failure include:
- Users excluded from the selection process
- Complex CMMS software
- Resistance to technology adoption
- Poor implementation of CMMS
Using modern, cloud-based CMMS like MaintainX can help overcome these implementation challenges. Unlike traditional on-premise systems, cloud CMMS is available over the Internet and, therefore, is easier to set up, access from anywhere, and manage the database. A modern CMMS also offers regular updates and better database security.
Get The Ultimate Guide to a Seamless CMMS Implementation.
5. Team communication
Clear and fast communication is essential for an effective PM program. Your team should always be able to communicate with each other efficiently and effectively. Poor communication can lead to:
- Delayed maintenance timelines
- Overlapping work orders and activities
- Inappropriate prioritization of maintenance tasks
- Under- or over-maintenance
- Poor maintenance inventory management
- Prolonged downtimes
Approximately 96 percent of office executives claim poor communication is to blame for workplace failures. Maintenance departments are no exception to everyday communication woes.
According to McKinsey Global Institute, a connected workforce is more likely to perform better. Using a mobile CMMS with team chat will prevent important project details from falling through the cracks. MaintainX reduces time spent clarifying details, improves access to maintenance records, and speeds up troubleshooting between technicians and managers.
6. Goals and KPIs
Next, set SMART goals and key performance indicators (KPIs) to measure progress. SMART is an acronym for Specific, Measurable, Achievable, Relevant, and Time Bound.
This means your maintenance goals should clearly outline what you’re looking to accomplish, when you’re looking to achieve them, and the metrics you’ll use to measure success. Your goals should be relevant to your company’s broader business goals.
Common KPIs for measuring preventive maintenance plan effectiveness include:
- Planned maintenance percentage (PMP): This metric measures the time you spend on planned maintenance compared to unplanned maintenance within a given period.
- Preventive maintenance compliance (PMC): This metric tracks how many scheduled PM tasks you complete within a specific timeframe.
- Scheduled maintenance critical percentage (SMCP): This KPI measures the impact of delayed planned maintenance activities.
- Mean time to repair (MTTR): This measure looks at the average time it takes to repair and restore an asset to full functionality.
7. Upper-management support
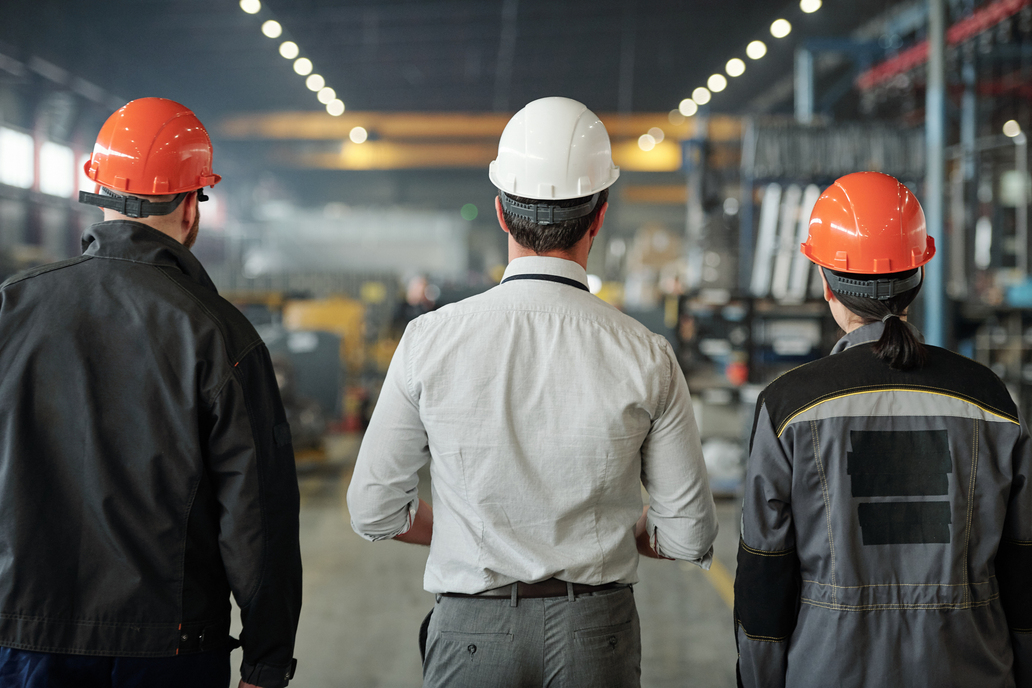
Finally, you’ll need the support of your company’s upper management to implement a PM plan successfully. Convincing leadership to get on board and increase budgets can be daunting. Here are some tips to help you to make the case for implementing a PM plan:
- Estimate return on investment: You must prove to the team that the PM program will improve the company’s bottom line. Select a few critical assets and demonstrate how shifting from corrective to preventive maintenance will reduce maintenance costs and improve profits. For example, if you experience three unplanned downtimes a year and the cost of restoring full functionality each time is $500, a PM program could reduce the downtimes from three to one and save $1000 in maintenance costs.
- Lay out maintenance goals: You can also make a presentation on your long-term maintenance goals and how they align with the overall organizational goals. Remember to cover the challenges faced with the current (reactive) system and how a PM program would overcome them.
How to start a preventive maintenance program in 8 steps
Ready to roll up your sleeves and put your preventive maintenance strategy into action? Let's break down the process into eight actionable steps, making it easy for you to create and implement a program that delivers real results.
1. Establish clear goals
Are you looking to reduce downtime? Cut spending on rush orders for parts? Increase equipment availability? Step one is to define what you aim to get out of the overall preventive maintenance program. Work with relevant stakeholders—from frontline workers to senior management—to develop a clear sense of where you want to go with a structured PM approach.
2. Inventory your assets
Before creating a preventive maintenance plan, you need comprehensive data about your assets. Carry out an audit of your equipment, taking note of relevant information like the age of each asset, its usage, and maintenance history. Also, consider the asset's current condition and priority level in relation to productivity and workplace safety.
3. Conduct a criticality analysis
Limited resources often mean that teams cannot pay the same amount of attention to all assets. As such, you need to establish priorities regarding your equipment. Conduct a criticality analysis to determine which assets are most crucial for production and safety. A criticality analysis refers to rating the importance of assets based on their potential risks. In this instance, we define risk as any possible ways failure can occur and how such failures might impact organizational productivity, expenses, and safety.
Tasks critical to production/safety AND have high repair/replacement costs fall into the high-priority category. Alternatively, you should give less priority to maintenance work on equipment that is not critical to production/safety AND has low repair/replacement costs. Non-critical, inexpensive, and worn-out assets are often better candidates for reactive maintenance.
4. Choose your preventive maintenance program KPIs
To ensure you can adequately track the progress of your PM plan, transform your goals into concrete targets in the form of KPIs. Common KPIs include Mean Time to Repair (MTTR), Mean Time Between Failure (MTBF), and Overall Equipment Effectiveness (OEE), among others. With KPIs, you have numbers against which to benchmark your progress, ensuring you can measure your performance and fine-tune your plan. The right CMMS can make all the difference here. MaintainX, for example, contains a robust reporting module that analyses your data to generate actionable insights.
5. Determine ideal PM ratios
How frequently should you carry out maintenance work on assets? The correct answer will depend on a combination of factors, including your resources, equipment manufacturer guidelines, regulatory requirements, staff capacity, historical equipment performance, and inventory. You also need to strike the right balance, ensuring you don’t leave assets undermaintained but do not waste resources by over-maintaining assets.
6. Schedule your PMs
At this stage, you’re finally ready to schedule your preventive maintenance activities. Word to the wise: don’t try to tackle everything at once. We recommend creating a long-term (yearly) maintenance schedule before breaking high-priority tasks down into a short-term schedule (quarterly, monthly, weekly, and daily).
A user-friendly computerized maintenance management system (CMMS) like MaintainX will make assigning, overseeing, and adjusting your PM program infinitely easier. AI-powered work scheduling based on labor insights and smart estimates.
MaintainX allows maintenance managers to create, assign, and monitor recurring work orders. MaintainX also optimizes work management through AI-powered work scheduling based on labor insights and smart estimates.
7. Train your team
Proper adoption is essential to get the best out of a preventive maintenance. As a result, you need to be proactive with your change management. Ensure you carry your staff along, providing any support and guidance for them to properly understand the software. Better yet, seek out solutions that are intuitive, user-friendly, and require little training. MaintainX, for example, is rated the most usable CMMS according to third-party reviews, for its intuitive processes that encourage easy adoption.
8. Monitor preventive maintenance program success
Monitor your chosen KPIs, ask for team member feedback, and make small adjustments accordingly. Focus on progress by determining how many PMs have been performed on critical equipment and how many times those assets have failed since the program began. You should be able to determine whether you should reduce or increase your PM activities based on this data. If your team isn’t meeting its goals, conduct a root cause analysis to identify where inefficiencies are occurring and correct course. Reporting tools like MaintainX’s asset health insights will also help you to double down on what works and eliminate initiatives that don’t.
Why preventive maintenance plans sometimes fail
While preventive maintenance provides several benefits, successful execution is not without its challenges. Here are a few to take note of.
Lack of data
Properly executing a preventive maintenance plan requires accurate data about your equipment to enable you to track your progress. Without this data, you’ll have no idea what kind of maintenance work your assets actually need, how well your maintenance efforts are actually performing, and what changes you might need to make as you proceed. Manual data management systems worsen this problem, limiting your ability to analyze your data and extract relevant insights for taking action.
Poor inventory management
Speed is crucial to effective preventive maintenance work, and technicians finding themselves without the necessary parts only serves to increase downtime. Without accurate and reliable inventory management, it’s impossible to ensure your team members have the parts they need when they need them. As a result, maintenance work will suffer delays, and you might end up having to pay more for rush orders.
Limited resources
While preventive maintenance helps teams save money, it can also be cost-intensive at the start. Without enough resources, teams face the challenge of finding the right balance when allocating staff and funds to preventive maintenance work, especially when those resources could be useful elsewhere.
Simplify preventive maintenance planning with Maintainx
Preventive maintenance helps organizations reduce unplanned equipment downtimes, increase asset reliability, minimize maintenance costs, and improve operations. While initially launching a preventive maintenance program may seem complicated, it’s simple if you effectively plan for it.
Focus on scheduling PM for your most critical assets to keep your new maintenance program affordable, manageable, and effective. The easiest way to get organized is with the support of a user-friendly CMMS like MaintainX. Here are some key ways MaintainX can support your preventive maintenance planning.
Work order management
MaintainX allows you to manage your work order process by organizing everything in one place. Instead of dealing with pen and paper work requests and instructions, MaintainX allows you to simplify the process by creating, assigning, and monitoring work orders in one place. You can send and track real-time updates, see when a technician starts a task, how far along they are, and provide any necessary instructions. In addition, MaintainX helps optimize your work management with AI-powered work scheduling based on labor insights and smart estimates.
Asset Management
Track downtime, standardize maintenance procedures, and use data-driven insights to improve reliability across sites and regions with MaintainX. With MaintainX, you can instantly see asset and work history, including what work was performed, who did the work, and which parts were used. You can make smarter decisions about your assets with accurate and current data.
Parts inventory management
MaintainX CMMS offers a robust parts management module that helps ensure you always have the necessary parts on hand for maintenance work. Global parts management allows you to standardize and enhance inventory management across all your facilities. Enabling leaner inventory levels will increase parts availability, avoid long lead times on parts orders, and decrease inventory costs.
Reporting and analytics
Built-in reports and dashboards allow you to assess the health of your operations at a glance. Get insights on key KPIs like PM compliance and MTBF so you can reduce downtime, optimize staffing, and ensure the effectiveness of your PM program. Ready access to data gives you the power to identify key areas of improvement and optimize your maintenance program for maximum impact.
Robust integrations
Connect your entire maintenance and asset ecosystem. MaintainX provides out-of-the-box and customizable integrations so you can work with existing infrastructure and workflows. There are three ways to integrate with MaintainX:
- MaintainX integrates with 4,000+ applications via Zapier — a low-code platform that allows you to configure integrations with ease.
- MaintainX can configure your integrations and set you up for success.
- Expert systems integrators can help you achieve your goals, including: Faye, Rovisys, Industry Corps, MachineMetrics, and MAJiK Systems.
Get started with MaintainX today
Anyone with a smartphone can download the MaintainX and get started with our basic plan, which includes unlimited work orders, right away. Want to learn more? Check out case studies to read about how MaintainX helps customers transform their operations, or book a tour today to see for yourself.
FAQs
What are the benefits of a preventive maintenance plan?
The benefits of Preventive Maintenance include:
- Reduced unplanned downtime and associated costs.
- Extended equipment lifecycle, reducing the need for premature replacement.
- Improved safety for employees and reduced risk of accidents.
- Increased operational efficiency and productivity.
- Better compliance with industry regulations and standards.
- Reduced need for costly repairs.
How does preventive maintenance differ from reactive and predictive maintenance?
Predictive Maintenance is a data-driven asset management approach that uses sensors, monitoring equipment, and advanced analytics to predict when maintenance is actually needed. It relies on real-time data and condition monitoring to identify signs of impending failure. Reactive Maintenance involves repairing equipment after it has failed or broken down. Preventive Maintenance, on the other hand, involves scheduled maintenance tasks performed proactively to prevent breakdowns and extend the life of equipment.
Can software be used to manage preventive maintenance?
Yes, Preventive Maintenance software helps businesses automate and streamline the management of preventive maintenance workflows. It can schedule, track, and document maintenance activities, send alerts for upcoming tasks, and generate real-time reports for analysis of asset performance.
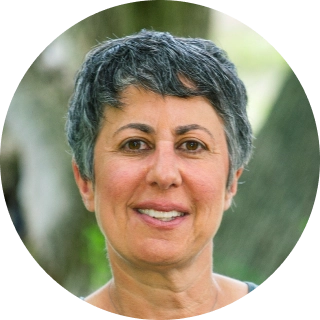
Caroline Eisner is a writer and editor with experience across the profit and nonprofit sectors, government, education, and financial organizations. She has held leadership positions in K16 institutions and has led large-scale digital projects, interactive websites, and a business writing consultancy.