Over the last few years of supply chain disruptions and soaring costs, maintenance and operations (M&O) teams have been looking for new ways to increase efficiency and improve asset performance and longevity. Teams tasked with protecting physical assets are continually shifting away from reactive maintenance—or fixing problems as they arise—and towards planned maintenance.
Planned maintenance, on the other hand, allows teams to be proactive by scheduling maintenance tasks that can prolong asset life and reduce costs. Implementing a planned maintenance strategy has tremendous benefits but can be difficult to execute without help. A top-rated computerized maintenance management system (CMMS) like MaintainX makes planned maintenance easy, saving time, money, and assets.
In this article, we’ll dive into what planned maintenance is, its advantages and disadvantages, and how to implement it in your organization.
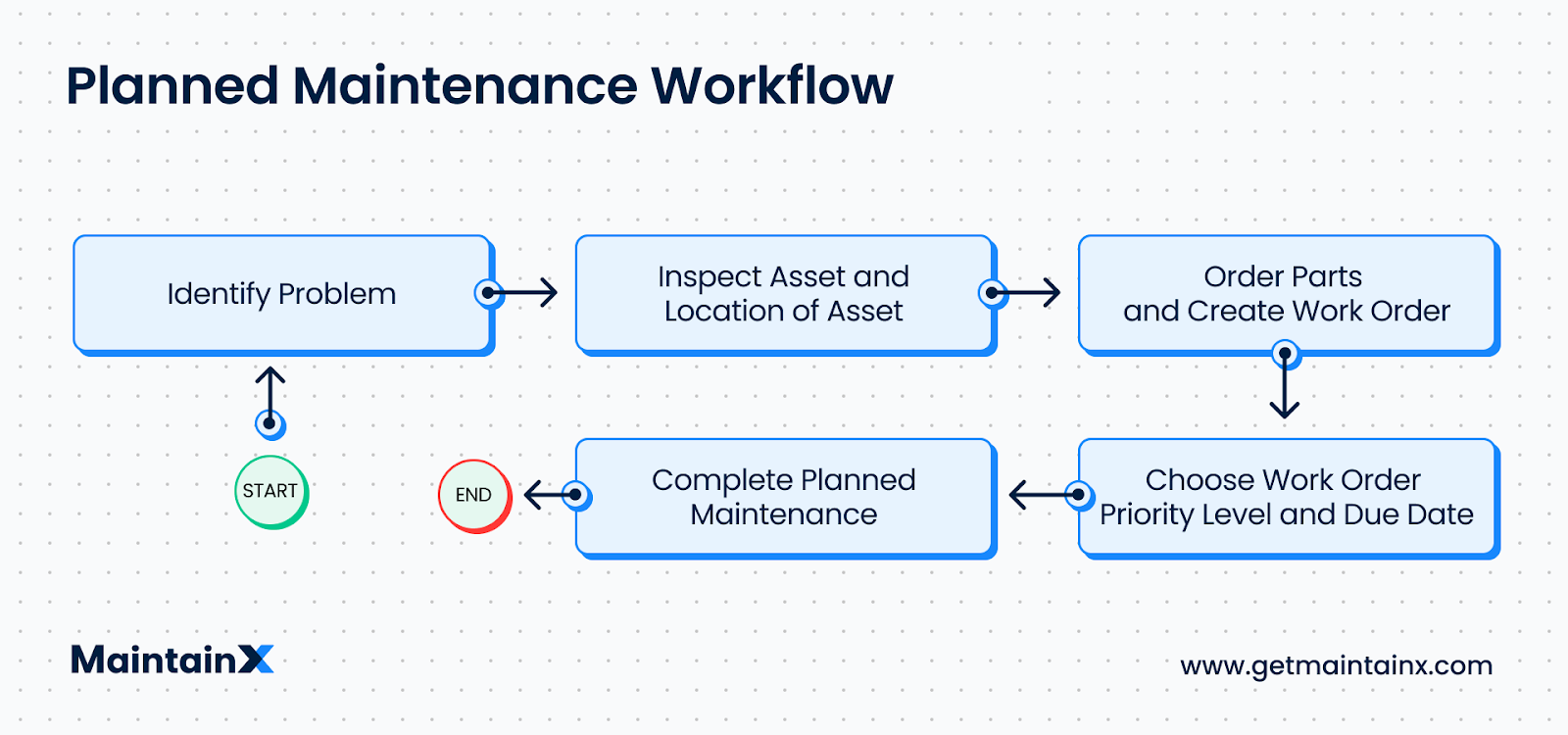
What is planned maintenance?
Planned maintenance refers to all proactive maintenance activities that are scheduled and completed according to a specific plan. Also referred to as scheduled maintenance, planned maintenance is typically carried out in order to reduce downtime and costs associated with breakages and equipment failure.
Planned is a basic form of preventive maintenance and involves knowing ahead of time the spare parts, tools, services, and maintenance tasks needed to solve a problem.
Dealing with unplanned breakdowns that cause operations to grind to a halt is stressful, expensive, and time-consuming. For this reason, facilities often plan, document, and schedule their maintenance strategy.
Every asset wears out at some point. However, leaders can keep equipment running efficiently for as long as possible with planned maintenance. The easiest way to execute effective scheduled maintenance is by moving your facility management to a Computerized Maintenance Management System (CMMS).
However, 44 percent of organizations still rely on paper records to plan maintenance activities. Until recently, CMMS platforms were expensive, complicated, and risky investments. The good news is that modern, cloud-based solutions have removed these barriers to entry.
Organizations of all sizes—with workers with varying technical skill levels—can now execute planned maintenance programs via downloadable mobile apps that support importing asset lists, creating work orders, and using team instant messaging.
Why is planned maintenance important?
Planned maintenance is a necessity for most businesses. Machinery, HVAC units, data networks, and other important assets must remain in reliable condition to meet production and service goals. Organizations that primarily operate in reactive-maintenance mode—i.e. fixing equipment as it breaks—risk the severe cost of downtime.
According to a Ponemon Institute report, the average cost of downtime is nearly $9,000 per minute for large businesses and $137 to $427 per minute for SMBs. Of course, downtime expenses vary based on industry vertical, organization size, and business model. However, one thing remains the same across the board: strategically planned maintenance programs increase bottom lines.
Two types of planned maintenance
Planned maintenance activities fall into one of two categories: Preventive Maintenance or Planned Unscheduled Maintenance.
Preventive maintenance
As the term suggests, preventive maintenance (PM) involves taking preventive actions to ensure pieces of equipment never come to an inconvenient and expensive halt. Planned preventive maintenance aims to put in place a maintenance schedule that takes care of problems before they occur. For instance, manufacturers often recommend servicing vehicles every 5,000 miles. This scheduled maintenance task helps vehicles run smoothly. Procrastinate car upkeep for too long, and your car may stall at a dangerous or inconvenient time.
Beyond basic car maintenance, preventive maintenance is ideal for the following types of assets:
- Assets with a critical operational function
- Assets with high financial value
- Assets with preventable failure modes
- Assets with an increased likelihood of failure
- Assets with statutory requirements
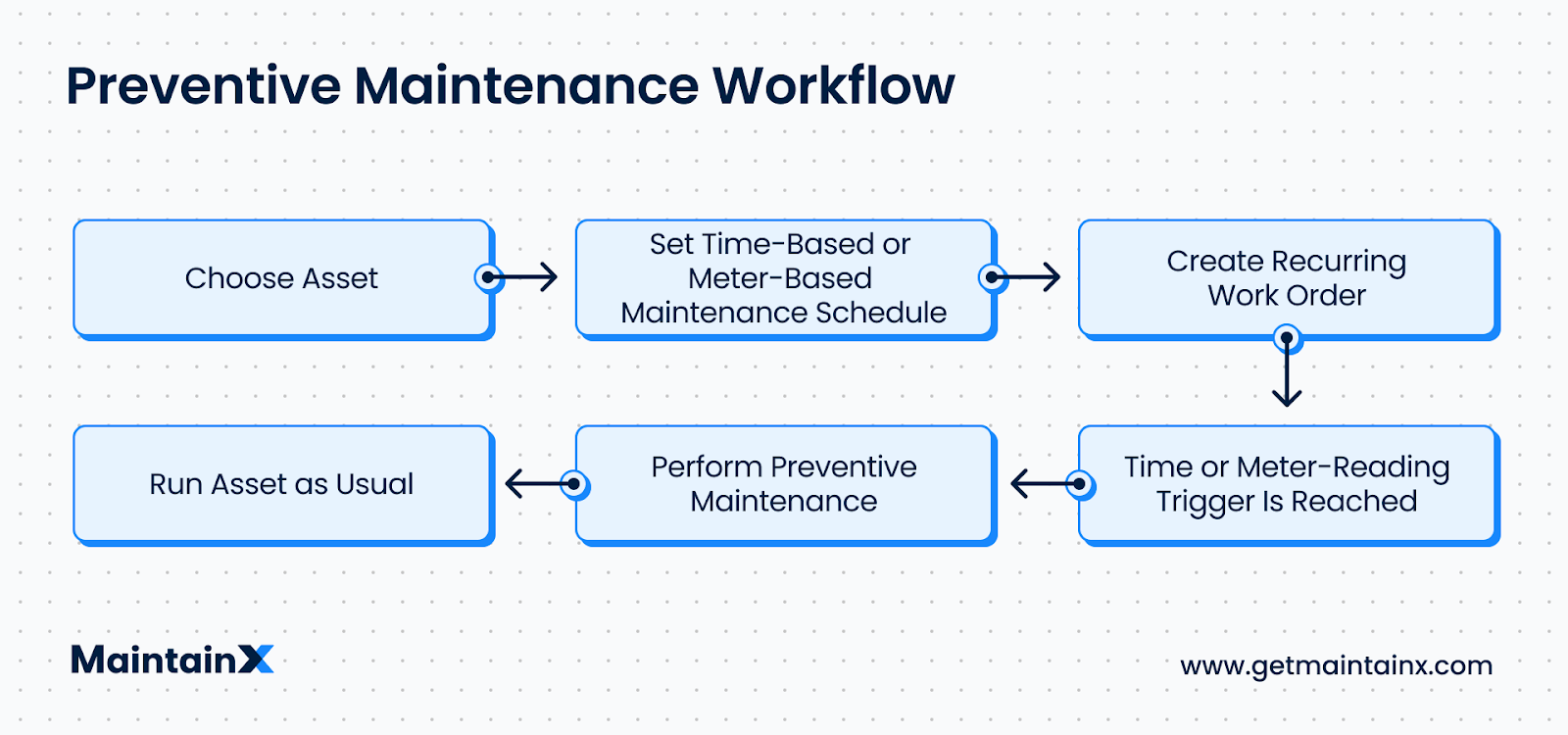
Planned unscheduled maintenance
This approach entails undertaking maintenance activities after a failure has occurred, although a recovery plan is in place to deal with these eventualities. Once again, the goal is to return the equipment to operation as soon as possible without jeopardizing safety. Planned unscheduled maintenance helps minimize maintenance costs by avoiding last-minute rush orders for replacement parts. For example, a vehicle owner may purchase a spare battery in case the current one dies.
Perhaps the most important part of planned maintenance is having well-structured workflows in place, like SOPs, to reduce your reactive maintenance and unplanned downtime and increase your KPIs (key performance indicators).
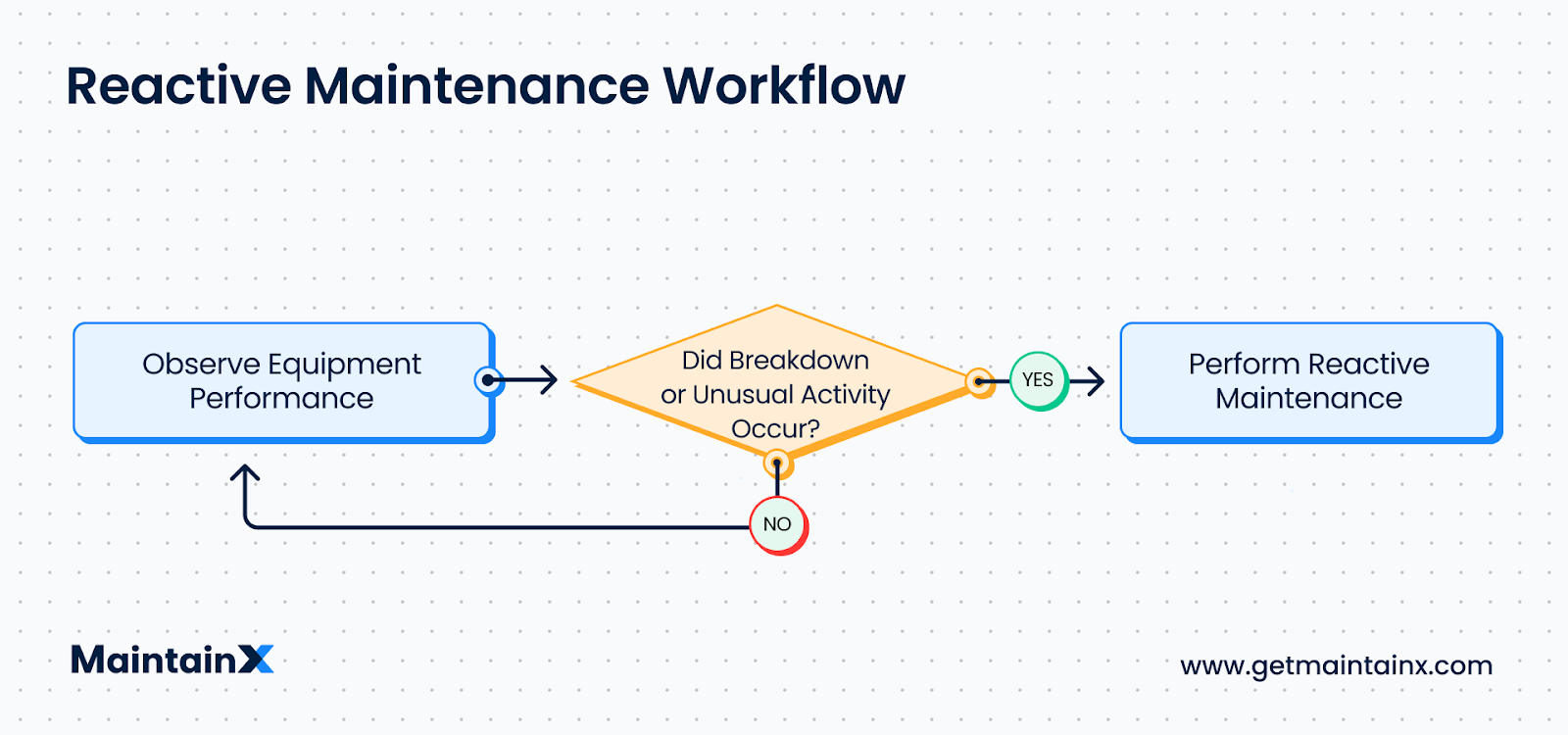
As the graphic above indicates, reactive maintenance always starts with a breakdown or an anomaly, resulting in breakdown and downtime. The benefits of planned unscheduled maintenance—even work orders requiring weekly lubrication of a piece of equipment—are that they prolong asset lifespan.
Planned unscheduled maintenance is ideal for the following assets:
- Redundant assets
- Non-critical machinery
- Assets with short lifespans
- Assets with low financial value
- Assets unlikely to fail
- Assets in which repairs aren’t feasible
- Single-use and inexpensive assets or parts
- Assets with random failure patterns difficult to anticipate
- Assets not subject to statutory maintenance requirements
Planned maintenance advantages versus disadvantages
Before talking about how to create and implement a maintenance plan, let's look at the pros and cons of creating one.
Advantages
- Decreases downtime: Planned maintenance enables teams to resolve issues before they result in failure. Even when a failure occurs, technicians can “follow the plan” to get equipment up and running quickly.
- Increases asset useful life span: Regularly serviced equipment lasts longer.
- Reduces maintenance costs: Not surprisingly, planned maintenance programs allow teams to handle breakdowns efficiently without spending extra capital on the expedited delivery of replacement parts or outsourced maintenance services. For example, look for a CMMS that connects directly with vendors: knowing lead times for parts from the maintenance work site is a game changer.
- Improves workplace safety: Assets operating in optimal conditions are safer to work around. Planned maintenance minimizes the risk of disaster.
- Enhances company culture: Frequent unexpected downtime hurts employee morale, increases stress, and leads to dissatisfaction. Facilities that minimize downtime foster greater contentment for all.
Disadvantages
However, planned maintenance does have some disadvantages. Its biggest drawback is that unnecessary tasks may sometimes be completed. For example, if the equipment being inspected doesn’t need upkeep, the servicing technician will have wasted time that could have been spent on a more urgent work order. To eliminate this issue, teams must prioritize work orders based on organizational needs. A powerful solution like MaintainX is highly customizable, allowing you to prioritize tasks based on a range of criteria, ensuring the most impactful work is at the top of the list.
Another disadvantage is that inefficient preventive maintenance programs can increase maintenance costs over the long run due to unnecessary work. Understanding what KPIs to measure and having a sound strategy can ensure preventive maintenance is profitable. With MaintainX’s advanced reporting, it’s easy to identify wasted efforts, bottlenecks, or areas for improvement, protecting your investment in planned maintenance.
What is a maintenance plan & what does it include?
Maintenance plans outline all maintenance tasks necessary to maintain facility assets. Effective maintenance plans document company maintenance policies, trace exhaustive asset inventories, and map workflows.
A maintenance plan may be simple or exceedingly intricate, depending on a company’s preventive maintenance program experience. Different sizes and types of businesses require different levels of organizational systems. Depending on the size of your organization, you may want to consider using computerized maintenance management software (CMMS) to streamline asset management, PM schedules, parts inventory, and standard operating procedures (SOPs).
If you decide to ditch the paper stacks, consider choosing a CMMS that can be used on both desktop and mobile. This way, technicians can use their smartphones to fill work orders and communicate with management while on the job.
Regardless of whether or not you choose to use a CMMS, general maintenance plans should include the following elements:
Maintenance mission statement
Base your maintenance strategies on a maintenance mission statement that both supports and is supported by your organization’s overall business plan. The best maintenance plans reflect the needs of customers, employees, and shareholders. Consult with executive leadership to discuss the role maintenance plays in meeting production and service goals.
Maintenance tasks
List all of your facility’s preventive maintenance tasks and scheduled unplanned maintenance tasks in a central place. Ideally, every piece of equipment, from small to large, should be included on your list. The more information you catalog with each asset, the better (e.g. serial numbers, locations, service history dates, vendors). Again, a CMMS makes creating and keeping a list like this a lot easier.
Work instructions
Once you have documented your facility’s maintenance tasks, outline work instructions for completing each task. You may want to develop standard operating procedures (SOPs) to make sure everyone knows exactly how to perform each task.
Maintenance schedule
Schedules help ensure technicians complete PMs as needed, no more and no less. Maintenance schedules also give workers time to plan and source necessary resources. Set a “maintenance window” to begin your program year. While it would be great to begin at the start of the calendar year, waiting to do so may not be an option. Communicate the timeframe to the entire production team so there is no confusion.
Maintenance technicians
Indicate the specific skills needed for each maintenance activity, then group tasks by required skill sets before matching them with technician specialties. Doing so saves significant time when evaluating new hires and assigning current ones.
Third-party contractors
Facilities outsource an average of 19 percent of maintenance operations to third-party contractors. Delineate the tasks for outsourced specialists in your maintenance plan. Doing so will help streamline the hiring process when sourcing quotes.
Replacement parts
Nothing is worse than not fixing a machine because you’re waiting on a part! Accurately predicting spare parts usage is crucial to maximizing profitability, reducing downtime, and reducing stress. Make a comprehensive list of all spare parts the department should stock.
Again, a robust CMMS can help with this. The more service history data you put into your CMMS, the more efficient your team will become. Software analytics often reveal surprising time and spending patterns of organizational waste. Managers who fine-tune maintenance strategies based on evolving O&M data can make smarter and more confident budgeting decisions throughout the year.
How to implement a planned maintenance strategy in 7 steps
Proactive maintenance is an essential part of maximizing equipment usefulness, reliability, and value. However, organizations are often unsure of how to create a sustainable planned maintenance program. Take the following steps to build a functional planned maintenance plan for each asset, starting with the most important.
1. Identify equipment failure modes
Conduct a criticality analysis to outline the scope of work to be completed. Gather information on the asset in question, its failure modes, and any other related data that might be useful during maintenance. Failure modes describe specific ways that assets and their components can fail. For instance, the failure modes for a centrifugal pump can be mechanical failure, hydraulic failure, corrosion, or human error. Implementing a predictive maintenance workflow into your planned maintenance system may be essential here.
2. Inspect assets
Outline the details of the maintenance tasks to be performed in the event of failure. Ask yourself questions like: What tools will I need? Which replacement parts must be available? Are there any work environment factors that could affect maintenance?
3. Define work processes
Document the maintenance process for the asset step-by-step, including additional standard operating procedures, outlining safety precautions, shutdown procedures, and other important information.
4. Create Priority Levels
Once you have several recurring work orders scheduled, prioritization becomes essential. Always handle tasks that return facilities to optimal operations levels ASAP.
5. Schedule & assign work orders
When starting, schedule PM intervals according to your manufacturer’s recommended maintenance guidelines. Asset maintenance can also be scheduled by date, meter readings, alarm monitoring, or based on the completion of other work.
Assign your recurring work orders for times that will cause the least disruption to in-house operations, procedures, and your customers. If you run a 24/7 operation, scheduling around production and/or service lines may seem intimidating. However, you don’t need to shut down all production lines to briefly service particular components.
Once again, a user-friendly CMMS can simplify the process tenfold.
6. Implement an asset management system
A well-organized asset management system is imperative to optimized scheduling. Make important information, such as asset QR codes, recommended maintenance procedures, and troubleshooting procedures easily accessible to technicians. Knowing an asset’s model and serial code is essential for replacing parts. A mobile CMMS can help streamline this process.
7. Track KPIs
Key Performance Indicators (KPIs) can help you keep track of how assets are maintained, ensuring a safe environment. They also help you track the performance of your equipment and any hidden costs associated with keeping it up and running. The decision to finally retire machinery or equipment may depend on various factors that negatively affect your KPIs, including the total number of breakdowns, cost of replacement parts, and time spent fixing equipment. You may phase out an asset due to changes in your operational requirements or because the cost of maintaining it has become too high, and you are running the risk of total equipment failure.
The bottom line: the more information you collect about your individual equipment service history over time, the more you can optimize scheduling intervals. The easiest way to automate the maintenance scheduling process is via a user-friendly CMMS.
Examples of equipment that requires planned maintenance
Different companies have different types of assets and maintenance needs, making it difficult to pinpoint everything that should go on a planned maintenance program. However, the most common items in a planned maintenance schedule include:
- HVAC maintenance: HVAC systems should be regularly inspected and cleaned to ensure proper airflow and energy efficiency.
- Light fixtures: Dust can gather on lighting fixtures and reduce the amount of light reaching production areas. They need to be frequently dusted off and burnt-out bulbs replaced.
- Pest control: Pest control services in either a residential area or business can be scheduled for routine maintenance.
- Filters: This includes water filters, filtration parts, grease and baffle hood filters, HVAC filters, and office air filters.
- Belts: Conveyor belts and belts on other equipment should be regularly inspected and changed when they show signs of wear and tear.
- Instruments recalibration: Recalibrate delicate instruments after a given number of uses so they stay accurate.
- Vehicle maintenance: Tire rotation, oil changes, state inspections, and cleaning are some of the maintenance tasks you should carry out regularly if you manage a fleet of vehicles.
- Compressors: Frequently inspect your compressors to ensure they are free of cracks or wear and tear. Faulty compressors can be a safety hazard.
The list of non-critical and critical assets you can add to a proactive maintenance program is endless. These are just a few to get you started. Having a CMMS can help you set up an efficient maintenance schedule.
Let MaintainX run your Planned Maintenance
Don’t start your planned maintenance journey alone — partner with the top-rated CMMS on the market to make maintenance easy and effective. From solo maintenance powerhouses to robust teams full of technicians, our flexible and powerful solution provides full visibility and detailed reporting to save you money and protect your assets.
Streamline your maintenance schedules
Gain a centralized view of all maintenance-related activities with MaintainX. Easily create preventive maintenance schedules by automating tasks and notifying team members when new work is assigned to them. Once work has started, you can view work progress and include SOPs to ensure standards are met.
As you work and use the platform more, MaintainX gains more data, giving you a real-time view of your operations. You can then use the learnings to identify bottlenecks and adjust maintenance priorities proactively.
Optimize asset performance and longevity
Instead of waiting for important assets to fail, a partnership with MaintainX allows you to get ahead of maintenance. Ensuring maintenance tasks are scheduled and proactively completed helps improve asset health and performance.
Detailed reporting and live data, including integrating with IoT sensors, give a clear view of your asset, helping identify where resources should be focused. Accurate data and customized reporting help your team make proactive maintenance decisions.
Enhance team productivity with mobile access
MaintainX’s easy-to-navigate app saves maintenance technicians time by eliminating trips back and forth to the office. All the information they need to complete work can be found in the palm of their hand, including notifications when new work orders are assigned and easy access to procedures or past work orders.
If a technician needs help while working in the field, they can leverage MaintainX’s live messaging to connect to team members. Groups can be created to allow for real-time collaboration, uniting team members across locations and allowing information to flow freely. Teams gain efficiency and help retain tribal knowledge for years to come.
Ensure compliance with automated documentation
Many industries face compliance challenges and must prove they meet the regulatory board’s standards. Hunting down records to remain compliant is time-consuming and cumbersome, and it can lead to the loss of important documents.
Take the hassle out of compliance with MaintainX’s automated documentation. Instantly pull up past work orders and pictures, showing work history with completion dates and more. When you have a powerful solution on your side, you can free yourself up for more important tasks and ensure your organization meets compliance requirements.
Planned maintenance FAQs
Unplanned maintenance is often the result of unanticipated equipment failure. It can result in decreased productivity and impact your company’s bottom line. Unplanned maintenance can be expensive, dangerous, and time-consuming. For this reason, organizations should thoroughly examine the failure modes of each asset.
Planned maintenance tasks can include routine inspections, lubrication, cleaning, adjustments, calibrations, parts replacements, and software updates, among others.
The frequency of planned maintenance depends on factors such as equipment type, usage patterns, manufacturer recommendations, and environmental conditions. It can range from daily to weekly, monthly, quarterly, or annually.
See MaintainX in action