Predictive maintenance (PdM) is an advanced form of planned maintenance that monitors asset conditions in real-time. The proactive strategy relies on sensors that alert maintenance teams when preventive maintenance is needed to maintain optimal performance levels.
What Is Predictive Maintenance?
Predictive maintenance (PdM) utilizes equipment data to inform routine maintenance decisions. Also called condition monitoring, PdM technology is the most advanced form of maintenance in the marketplace. PdM includes machine learning technologies that are capable of establishing baseline patterns of “normal equipment operations.” These key performance indicators (KPIs) are then combined with complex algorithms to predict future performance issues.
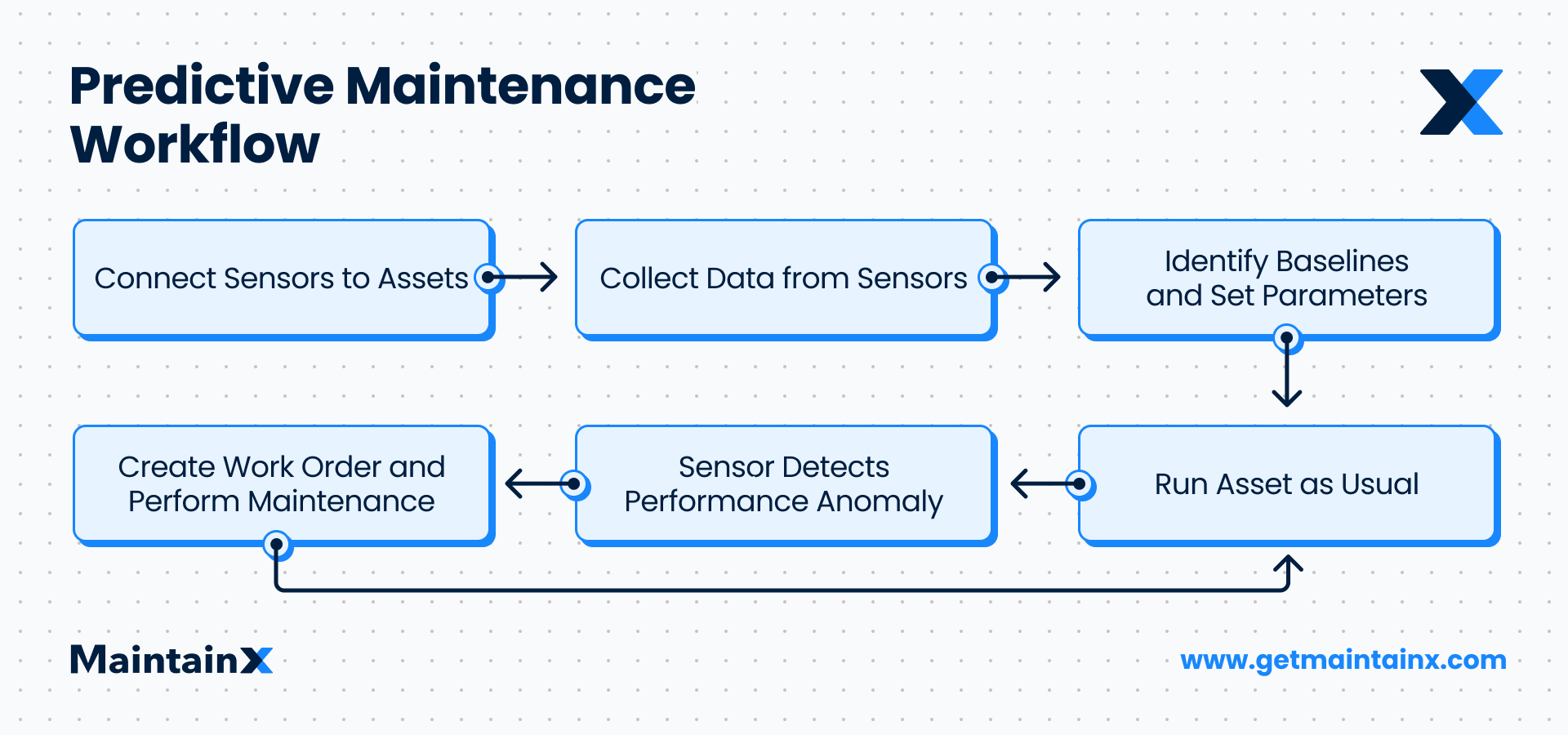
The goal of predictive maintenance is three-fold:
- Maximize uptime, improve reliability, and enhance productivity by reducing the number of unplanned breakdowns.
- Reduce operational costs by performing maintenance tasks before they become cost, labor, and time-excessive.
- Extend the lifespan of assets by performing maintenance before equipment failures occur.
Put simply, PdM uses advanced technology to remedy minor equipment problems before they become expensive, big ones.
What Is the Difference between Predictive and Preventive Maintenance?
It’s not uncommon for people to confuse predictive maintenance with preventive maintenance for a simple reason: they are both proactive forms of maintenance that share the goal of reducing downtime. Numerous studies have proven that both predictive and preventive maintenance substantially increase equipment lifespans. Take HVAC units, for example. The cooling systems are designed to last 20 years given routine maintenance that includes changing air filters, lubricating moving parts, cleaning coils, and refilling coolant. However, without periodic care, an HVAC could break down years sooner than necessary.
Likewise, predictive maintenance and preventive maintenance operate under the same proactive philosophy but use different methods to achieve results. Furthermore, PdM is more efficient but costlier. According to McKinsey & Company, PdM technologies can reduce manufacturer downtime by as much as 50 percent, while increasing asset lifespans by 40 percent. Here are the key differences between the two:
Predictive Maintenance
Preventive Maintenance
Assigns maintenance tasks based on information obtained by sensors and machine-learning technology that predicts when a piece of equipment may fail.
Schedules maintenance tasks at set intervals based on past experience and manufacturer’s guidelines. For example, the standard scheduled maintenance for a car is every 5,000 miles.
Requires costly sensor devices and advanced analytics software.
Accomplished via spreadsheets or CMMS (free to expensive).
Generates up to 40% ROI.
Generates up to 30% ROI.
Requires learning a new skill called condition monitoring.
Does not require learning any new skills besides CMMS navigation.
While there are other differences between predictive and preventive maintenance programs, these are the primary factors. As you can see, both strategies have unique advantages and disadvantages.
Why Is Predictive Maintenance Important?
Predictive maintenance is the future, and the future is here. And it isn’t just a theory being discussed in university classrooms; some of the world’s largest companies in manufacturing, aviation, and healthcare are experiencing incredible gains in efficiency, productivity, and savings as a result of their predictive maintenance programs.
A report by Market Research Future predicts that the global predictive maintenance market will reach $6.3 billion in the next two years. Predictive maintenance is, essentially, the gold star of the maintenance world—it ensures that tasks are performed at just the right time. Unlike preventive maintenance, there is no risk of performing too much or too little maintenance work with PdM. According to the U.S. Department of Energy, a functional predictive maintenance program can increase ROI up to ten times. It may also reduce asset breakdowns by 75 percent. This translates to a 45 percent reduction in downtime and a 30 percent reduction in maintenance costs.
What Are Common Predictive Maintenance Tools and Technologies?
Now that you understand the basics of predictive maintenance, let’s look closer at the tools and technologies that make PdM possible:
- Condition-Monitoring Equipment: These are sensors that capture asset data and communicate with software to evaluate wear and tear in real time. Sensors can measure equipment temperature, pressure, vibration, noise, oil, corrosion, electrical current levels, and more. Advanced options include infrared thermography cameras, ultrasonic technology, and vibration analysis equipment.
- The Internet of Things (IoT): IoT helps analyze and make sense of equipment data. The different sensors collect and share the data using IoT technology with a central information system.
- Predictive Formulas: Predictive formulas identify trends to detect when a piece of equipment needs servicing, repairs, or replacement. The formulas rely on predetermined algorithms that compare a machine’s current behavior against its expected behavior. Deviations are indicators of gradual deterioration, and your maintenance team can make timely interventions to avoid equipment failure.
It’s worth mentioning that Computerized Maintenance Management Software (CMMS) also plays an important role in predictive maintenance. CMMS platforms facilitate easy access to historical asset information, which provides the starting point for predictive maintenance benchmarks. CMMS also generates alerts and work orders in addition to serving as a central organizational tool and facilitating data interpretation.
Are There Any Drawbacks or Concerns with Predictive Maintenance?
As previously mentioned, predictive maintenance isn’t an ideal maintenance strategy for every organization. Even if you suspect PdM is right for your company, management should understand its inherent drawbacks. The most commonly raised concerns about predictive maintenance are:
It’s Time Consuming
One of the major drawbacks of PdM is the amount of time needed to assess and implement a maintenance schedule. It is a complex process that needs a thoroughly trained team to use the equipment and correctly interpret the data and analytics.
It’s Expensive
You will need to invest in maintenance tools and systems. This can be quite expensive, especially if the business is still growing. You will also incur training costs. While cloud-based technology has helped to reduce costs, training is still quite high for most businesses.
Baselines Must Be Established
Before installing sensors, management must establish conditional baselines for equipment. This provides initial “controls” for the technology to compare with future irregularities. Identifying functioning baselines is a delicate process—one wrong step can compromise all future data.
However, don’t let these drawbacks scare you away from investing in PdM. Overcome these hurdles with proper planning, and your organization will enjoy substantial ROI.
Is PdM Right for You?
Predictive maintenance takes the cake when it comes to reducing downtime. Though preventive maintenance is proven to deliver substantial benefits, it can’t predict equipment issues with the same level of accuracy as machine learning technology. However, despite the fact that PdM promises the highest long-term financial savings—and the most dependable route for avoiding downtime—because of the cost it isn’t the ideal choice for most teams YET.
Launching a successful predictive maintenance program requires significant capital, training, and time investment right now. No matter the industry, new technologies are always expensive. For this reason, only a small number of organizations are ideal candidates for PdM programs. However, it’s worth the effort for companies with enough capital, manpower, and management skills. Here’s an article with more information on how to identify the ideal maintenance strategies for your unique organization, assets, and teams.
How Do You Implement a PdM Program?
To implement predictive maintenance, you must first lay the groundwork for a sustainable PdM system. Prioritize your most important assets for tracking, start small, and scale up as your team adjusts. Here’s how to implement a predictive maintenance program:
1: Identify Critical Assets: The first step is to identify the critical assets and systems that should be included in the program. Prioritize assets with the highest repair and replacement costs.
2: Establish Your Asset Database and Install IoT Devices. Information is highly critical to your success. It offers actionable insights into machine behavior. Establish your database from CMMS, departmental records, and hardcopy files.
3: Establish Failure Modes. Perform an analysis of critical assets and establish failure modes. Connect IoT devices to a CMMS or remote dashboard for data collection and analysis.
4: Make Failure Predictions. Design a modeling approach for failure predictions to monitor operating conditions, predict and understand patterns, and create alerts on a fully automated system.
5: Deploy the System on Pilot Equipment. Before doing a massive rollout, conduct a pilot test for a select group of equipment. This will enable you to identify any system areas that need improvement.
Depending on the size and complexity of your company, it may take a while to see the impact of the new system on your operations. However, successfully implementing a PdM program will immensely improve business operations.
Types of Predictive Maintenance
There are four types of predictive maintenance:
Vibrational Analysis
Used for high-rotating machinery in manufacturing plants; helps detect loose parts of equipment, misalignment, imbalance, and wear and tear on bearings.
Sonic Acoustical Analysis
Used for both low- and high-rotating machinery; similar to vibrational analysis but focuses on proactive lubrication measures.
Ultrasonic Acoustical Analysis
Identifies stress and friction sounds in an ultrasonic range; used for mechanical and electrical equipment. This type of predictive maintenance, in particular, is excellent at anticipating imminent breakdowns.
Infrared Analysis
Suitable for a number of assets because it doesn’t depend on the rotational speed or loudness of an asset; can be used to identify airflow, cooling, and motor stress problems.
Examples of Predictive Maintenance
Here are some real-life examples of predictive maintenance in action:
- Utility companies use PdM to prevent outages that could be disruptive and expensive. For instance, some power companies now use drones fitted with sensors to map utility networks and identify trees that are too close to power lines and risk falling on them.
- The transportation industry is also a pioneer when it comes to predictive maintenance. It’s projected that the industry, specifically railway transport, will spend nearly $30 billion on IoT projects within the next 15 years, with the goal of reducing unexpected maintenance costs and improving safety and efficiency.
- Manufacturing plants use infrared imagers to monitor equipment temperatures to avoid unexpected overheating.
These are just a few of the real-life implementations of PdM happening right now. With that said, some industries rely on PdM more heavily than others.
What Are the Main Industries Using Predictive Maintenance Right Now?
Predictive maintenance isn’t some futuristic technology—industry pioneers around the world are already using PdM to increase efficiency. Here’s how those sectors at the forefront of the maintenance revolution are using it:
Predictive Maintenance in Manufacturing
There’s no industry that stands to benefit more from predictive maintenance than the manufacturing industry. According to the McKinsey Global Institute, the global manufacturing industry could save up to $630 billion by 2025, by using predictive maintenance. This is not pocket change. Manufacturers can use predictive maintenance to manage plant floor equipment, boost operations, and improve workplace safety. The move to wireless sensors will only make it easier to implement predictive maintenance.
Predictive Maintenance in the Automotive Industry
The shift to electric cars is picking up. And automakers are now equipping electric cars with sensors to collect data and relay information on performance back to dealerships. Car dealerships can also get in touch with drivers and ask them to act on given alerts. Fleet managers are using the information to plan maintenance service.
Predictive Maintenance in Aviation
The aviation industry is often credited with pioneering predictive maintenance. The industry uses predictive maintenance to not only reduce maintenance-related flight delays and cancellations but also to improve aircraft health. Obviously, such maintenance helps to prevent devastating accidents.
Predictive Maintenance in Oil and Gas
Ever since the 2010 Deepwater Horizon oil spill disaster, the oil and gas industry has taken a more proactive approach to safety. Perhaps no industry needs PdM more than this one because of the high level of risk and exposure. Anticipating failure and taking care of it not only helps prevent disastrous accidents but also optimizes machinery and saves costs. Royal Dutch Shell, BP, and ExxonMobil are the more notable oil companies using predictive maintenance.
Predictive Maintenance in Medicine
Did you know that remote monitoring equipment can anticipate potential failures in CT tubes? Such predictive maintenance measures are slowly being implemented in the medical industry. Additionally, hospitals cannot fully rely on human labor to ensure the optimal functioning of equipment because it requires advanced skills, and there’s insufficient human labor to sustain the entire industry. Signs of impending equipment failure must be detected early enough and maintenance scheduled before the systems break down to save lives and reduce downtime. This is one area that IoT and predictive maintenance have greatly improved and has cut back on warranty claims to equipment manufacturers.
The History of PdM
To fully appreciate the progress we’ve made, it’s helpful to understand where PdM began. The use of predictive maintenance tools began picking up at the start of the 21st century. Organizations used early technologies to monitor the condition of assets via an offline approach. Standard operating procedures were generally performed monthly, comparing new measurements to old ones. The increased operational efficiency generated by this approach eventually inspired inventors, scientists, and engineers to develop remote, real-time technology.
Simplify Predictive Maintenance with MaintainX
Predictive maintenance is the future, and the future is now. As PdM providers continue to improve existing technologies, this maintenance strategy will become more affordable in the years to come.
However, implementing PdM doesn't happen occur overnight. Effective implementation takes time, resources, and user-friendly CMMS software. MaintainX is a cloud-based maintenance management system designed with convenience, affordability, and security in mind.
Ready to move your new standardized and efficient processes online? Try MaintainX for free.
See MaintainX in action